The Scope and Purpose of a Home Inspection
This report is best viewed on a computer opposed to a mobile device or tablet
This report is a snapshot in time
A snapshot in time is a detailed description of a particular moment or instance, providing a portrayal of the inspection at that specific moment in time. Some factors may only be exhibited under certain circumstances given the "day of" circumstances.
Purpose of Inspection
A real estate inspection is a visual survey of a structure and a basic performance evaluation of the systems and components of a building. It provides information regarding the general condition of a residence at the time the inspection was conducted. It is important that you carefully read ALL of this information. Ask the inspector to clarify any items or comments that are unclear.
Purchasing property involves risk
The purpose of a home inspection is to help reduce the risk associated with the purchase of a structure by providing a professional opinion about the overall condition of the structure. A home inspection is a limited visual inspection and it cannot eliminate this risk. Some homes present more risks than others. We cannot control this, but we try to help educate you about what we don’t know during the inspection process. This is more difficult to convey in a report and one of many reasons why we recommend that you attend the inspection.
A home inspection is not an insurance policy
This report does not substitute for or serve as a warranty or guarantee of any kind. Home warranties can be purchased separately from insuring firms that provide this service.
A home inspection is visual and not destructive
The descriptions and observations in this report are based on a visual inspection of the structure. We inspect the aspects of the structure that can be viewed without dismantling, damaging or disfiguring the structure and without moving furniture and interior furnishings. Areas that are concealed, hidden or inaccessible to view are not covered by this inspection. Some systems cannot be tested during this inspection as testing risks damaging the building. For example, overflow drains on bathtubs are generally not tested because if they were found to be leaking they could damage the finishes below. Our procedures involve non-invasive investigation and non-destructive testing which will limit the scope of the inspection.
This is not an inspection for code compliance
This inspection and report are not intended for city / local code compliance. During the construction process structures are inspected for code compliance by municipal inspectors. Framing is open at this time and conditions can be fully viewed. Framing is not open during inspections of finished homes, and this limits the inspection. All houses fall out of code compliance shortly after they are built, as the codes continually change. National codes are augmented at least every three years for all of the varying disciplines. Municipalities can choose to adopt and phase in sections of the codes on their own timetables. There are generally no requirements to bring older homes into compliance unless substantial renovation is being done.
Please note that any codes referenced in this report are sourced from national resources, specifically the ICC or NEC, as a courtesy and may not reflect local code variations specific to your area.
Moisture meters used
Throughout the report, reference may be made to moisture conditions and percentages of moisture content. Generally moisture meters are used "qualitatively" as opposed to "quantitatively." This means that actual percentages shown by meter are meant to be indicative of moisture as compared to likely dryer areas. False positives are not always possible to eliminate entirely, but moisture meters can give good guidance.This is just our opinion
Thermal Imaging
Any thermal images are quantitive and all approximate temperatures. All tempatures can and will vary in range. This is done to show the general functionality of the area or item being tested and is strictly Due Diligence of the inspector to the client
Environmental/Mold Exclusions
The reported or actual health effects of many potentially harmful, toxic or environmentally hazardous elements that may be found in building materials or in the air, soil, water in and/or around any house are varied, and, in some cases controversial. A home inspection does not include the detection, identification or analysis of any such elements or related concerns such as, but not limited to, mold, allergens, legal/illegal drugs and other biological contaminants, radon, , bed bugs, cockroaches, fleas, lice, formaldehyde, asbestos, lead, electromagnetic fields, carbon monoxide, insecticides, Chinese drywall, refrigerants and fuel oils. Furthermore, no evaluations are performed to determine the effectiveness or appropriateness of any method or system (e.g., water filter, radon mitigation, etc.), designed to prevent or remove any hazardous or unwanted materials or elements. An environmental health specialist should be contacted for evaluation of any potential health or environmental concerns. The noting of the presence of materials commonly considered to contain asbestos, formaldehyde, lead, mold etc in the inspection report, should not be construed to mean the inspector is inspecting for these things but instead should be seen as a "heads-up" regarding these materials and further evaluation by qualified professionals may be warranted.Please note that identification of mold, mold testing and indoor air quality are beyond the scope of this inspection. If you are concerned about mold or indoor quality, I recommend additional inspection by a specialist. As a general rule, localized mold problems can often be easily repaired by eliminating the moisture source and removing or sealing the localized area that got wet. Best practices to control mold in buildings are to spend limited resources diagnosing and repairing water problems. Where water problems are chronic, mold problems can be more complex and expensive to correct. Where water problems are seasonal or localized, repairs tend to be more limited in scope and less complex to repair. Mold problems in attics are generally unlikely to affect indoor air quality because homes experience the stack effect where warm air escapes out the top of the house like a chimney. However, at the very least repairs should be made to diagnose and understand attic moisture problems to prevent on-going water damage in this space.
Pest
This is not a pest/termite report. This is a visual observation only of specific areas and if noted in the report is strictly Due Diligence of the inspector to the client
Construction techniques and standards vary. There is no one way to build a house or install a system in a house. The observations in this report are the opinions of the home inspector. Other inspectors and contractors are likely to have some differing opinions. You are welcome to seek opinions from other professionalsResponsibility of the Inspector
The inspector IS required to:
- use this Property Inspection Report form for the inspection;
- inspect only those components and conditions that are present, visible, and accessible at the time of the inspection;
- indicate whether each item was inspected, not inspected, or not present;
- indicate an item as Deficient (D) if a condition exists that adversely and materially affects the performance of a system or component OR constitutes a hazard to life, limb or property as specified by the Ohio SOPs:https://com.ohio.gov/static/documents/1301.17.1.17-StandardsofPractice.pdf ;and
- explain the inspector's findings in the corresponding section in the body of the report form.
The inspector IS NOT required to:
- identify all potential hazards;
- turn on decommissioned equipment, systems, utilities, or apply an open flame or light a pilot to operate any appliance;
- climb over obstacles, move furnishings or stored items;
- prioritize or emphasize the importance of one deficiency over another;
- provide follow-up services to verify that proper repairs have been made; or
- inspect system or component listed under the optional section of the SOPs (22 TAC 535.233).
Responsibility of the Client
While items identified as defective in an inspection report DO NOT obligate any party to make repairs or take other actions, in the event that any further evaluations are needed, it is the responsibility of the client to obtain further evaluations and/or cost estimates from qualified service professionals regarding any items reported as Deficient (D). It is recommended that any further evaluations and/or cost estimates take place prior to the expiration of any contractual time limitations, such as option periods.
Please Note: Evaluations performed by service professionals in response to items reported as Deficient (D) on the report may lead to the discovery of additional deficiencies that were not present, visible, or accessible at the time of the inspection. Any repairs made after the date of the inspection may render information contained in this report obsolete or invalid.
Report Limitations
This report is provided for the benefit of the named client and is based on observations made by the named inspector on the date the inspection was performed (indicated above).
ONLY those items specifically noted as being inspected on the report were inspected.
This inspection IS NOT:
- a technically exhaustive inspection of the structure, its systems, or its components and may not reveal all deficiencies;
- an inspection to verify compliance with any building codes;
- an inspection to verify compliance with manufacturer's installation instructions for any system or component and DOES NOT imply insurability or warrantability of the structure or its components.
- Ohio Inspector Law & Administrative Rules
https://codes.ohio.gov/ohio-administrative-code/rule-1301:17-1-17
NOTICE CONCERNING HAZARDOUS CONDITIONS, DEFICIENCIES, AND CONTRACTUAL AGREEMENTS
Conditions may be present in your home that did not violate building codes or common practices in effect when the home was constructed but are considered hazardous by today's standards. Such conditions that were part of the home prior to the adoption of any current codes prohibiting them may not be required to be updated to meet current code requirements. However, if it can be reasonably determined that they are present at the time of the inspection, the potential for injury or property loss from these conditions is significant enough to require inspectors to report them as Deficient (D). Examples of such hazardous conditions include:
- malfunctioning, improperly installed, or missing ground fault circuit protection (GFCI) devices and arc-fault (AFCI) devices;
- ordinary glass in locations where modern construction techniques call for safety glass;
- malfunctioning or lack of fire safety features such as smoke alarms, fire-rated doors in certain locations, and functional emergency escape and rescue openings in bedrooms;
- malfunctioning carbon monoxide alarms;
- excessive spacing between balusters on stairways and porches;
- improperly installed appliances;
- improperly installed or defective safety devices;
- lack of electrical bonding and grounding; and
- lack of bonding on gas piping, including corrugated stainless steel tubing (CSST).
Home inspectors are typically hired to inspect a home's major systems and components, including the roof, foundation, electrical, plumbing, HVAC (heating, ventilation, and air conditioning), and more. However, there may be areas of a home that are not inspected due to limitations of the home inspector. These limitations can be due to a variety of factors, including safety concerns, accessibility issues, and the scope of the inspection. Here are some areas that may not be inspected due to limitations of a home inspector:
- Hidden areas: A home inspector may not be able to inspect areas that are concealed, such as inside walls, beneath flooring or insulation, or behind fixtures.
- Outbuildings: If a property has additional structures such as garages, sheds, or guesthouses, a home inspector may not inspect these structures as part of their standard inspection.
- Environmental hazards: Home inspectors typically do not inspect for environmental hazards such as lead, asbestos, mold, or radon. A separate specialist would need to be hired to perform these types of inspections.
- Cosmetic issues: A home inspector may not inspect for cosmetic issues such as chipped paint or worn carpeting.
It is important to note that home inspections are not meant to be comprehensive, and there may be areas of a home that are not inspected due to limitations of the inspector. If a buyer has concerns about a particular aspect of a home, they may need to hire a specialist to perform a more detailed inspection.
Please Note: items identified as such in an inspection report DO NOT obligate any party to make repairs or take other actions. The decision to correct a hazard or any deficiency identified in an inspection report is left up to the parties to the contract for the sale or purchase of the home.
As I don't know the qualifications of the seller or the buyer to conduct repairs, I always recommend that you consult a qualified licensed professional in the appropriate trade to determine all needed repairs and best repair method, to estimate costs, and to perform all repairs deemed necessary. That's what I mean when I write "Repair as necessary", "Fix it" or ANY other terms implying the need for repair / replacement. You need to decide for yourself if you or the seller's qualifications, experience and knowledge would allow the repair to be made without using a qualified licensed trade professional.
Remember, you, the buyer, should consult with a qualified contractor in the appropriate trade to determine all needed repairs, recommendations and best repair methods, to estimate costs, and to perform all repairs deemed necessary. Consider having servicing or maintenance discussed in this report or verbally at the time of the inspection completed prior to any final date as indicated in any Real Estate sales agreement. This property inspection report may include an inspection agreement (contract), addenda, and other information related to property conditions.
Since Olonzo Inspections does not dismantle equipment or perform invasive inspections or destructive testing, the contractor's subsequent examination may reveal additional required repairs.
How to Read This Report
Getting the Information to You
This report is designed to deliver important and technical information in a way that is easy for anyone to access and understand. If you are in a hurry, you can take a quick look at our "Summary Page” and quickly get critical information for important decision making. However, we strongly recommend that you take the time to read the full Report, which includes digital photographs, captions, diagrams, descriptions, videos and hot links to additional information.
The best way to get the layers of information that are presented in this report is to read your report online, which will allow you to expand your learning about your house. You will notice some words or series of words highlighted in blue and underlined – clicking on these will provide you with a link to additional information.
This report can also be printed on paper or to a PDF document.
Chapters and Sections
This report is divided into chapters that parcel the home into logical inspection components. Each chapter is broken into sections that relate to a specific system or component of the home. You can navigate between chapters with the click of a button on the left side margin.
Most sections will contain some descriptive information done in black font. Observation narrative, done in colored boxes, will be included if a system or component is found to be significantly deficient in some way or if we wish to provide helpful additional information about the system or the scope of our inspection. If a system or component of the home was deemed to be in satisfactory or serviceable condition, there may be no narrative observation comments in that section and it may simply say “tested,” or “inspected.”
Standards of Practice
Throughout this report, you will see references to 'Standards of Practice,' labeled in blue, which provide important information regarding the Ohio Standards of Practice for home inspections. These references are included to help clients understand the guidelines and limitations that govern the inspection process. However, they do not expand the scope of the inspection beyond what is required by these standards. The inspection is a visual, non-invasive assessment of the property’s condition at the time of inspection and does not guarantee future performance or uncover concealed defects. Clients are encouraged to review these standards for a clearer understanding of the inspection’s scope and limitations
Information and Limitations (Info and LMT's)
Throughout this report, you will see sections labeled 'Info & Limitations' (Info & Lmt's) labeled in orange. These sections provide important informational context for the client regarding the inspection process, scope, and findings. They are intended to enhance understanding but do not constitute a warranty, guarantee, or an exhaustive evaluation of every potential issue. The inspection is conducted in accordance with the Ohio Standards of Practice and reflects the conditions observed at the time of inspection. Clients are encouraged to review these details carefully and consult with relevant professionals for further evaluation if needed.
Observation Labels
All narrative observations are colored, numbered and labeled to help you find, refer to, and understand the severity of the observation. Observation colors and labels used in this report are:
- Recommended Repair/Marginal Defects:
Items identified with safety hazards or functional/installation deficiencies may have been operational at the time of inspection, but their functionality could be compromised. These defects often lead to further issues. Repairs or replacements are recommended for optimal performance and to prevent future problems before the end of your contingency period. Such items typically require attention from a qualified contractor or handyman and are not suitable for routine maintenance or DIY repairs. - Minor Defects/Maintenance Items:
This category encompasses items or components requiring minor repairs to enhance functionality, as well as those needing regular or basic maintenance. It also includes observations and recommendations for upgrades to specific items, areas, or components. - Safety :The item, system, area, or component poses a safety concern that should be addressed promptly by a qualified professional. Identifying potential hazards is a key aspect of home inspection, as the inspector evaluates the property’s safety and highlights any risks affecting occupant well-being.
- Conditions Be Evaluated And Corrected If Deemed Necessary:
During a home inspection, a home inspector may encounter issues or areas of concern that require further evaluation. In such cases, the home inspector may recommend that the buyer or homeowner seek further evaluation by a specialist. A specialist is an expert in a specific area related to home construction, repair, or maintenance. - Inquire With Seller:When buying a home, "inquire with seller" refers to the process of asking the seller (or their agent) specific questions about the property. This can help you gather important information before making a purchase decision.
- Note:Refers to aside information and /or any comments elaborating on descriptions of systems in the home or limitations to the home inspection.
Summary Page
The Summary Page is designed as a bulleted overview of all the observations noted during inspection. This helpful overview is not a substitution for reading the entire inspection report. The entire report must be read to get a complete understanding of this inspection report.
Summary
Recommended Repair Marginal Defects
- C1P-2 Ch. 12 Plumbing - 12.10 General Plumbing Observations and Recommendations:
PEX plumbing was observed installed too close to the gas water heater. According to most manufacturer’s guidelines and UPC Code 604.11.2, PEX should be kept at least 18 inches away from the water heater’s exhaust vent to prevent heat-related damage.
Recommendations:
It is recommended to have a licensed plumber evaluate and properly reposition the PEX piping to meet safety standards.
Minor Defects Maintenance Items
- CESDW-1 Ch.4 Exterior Siding, Doors and Windows - 4.8 General Exterior Siding, Doors and Windows Observations and Recommendations:
The backdraft damper for the exterior fan vent cover is not closing properly on the right side of the property. The damper is important to prevent air from entering the house and fan vent when the fan is not in use.
Recommendations:
Have this further evaluated and repaired as recommended by a qualified contractor.
- C7G-1 Ch. 7 Garage - 7.6 General Garage Observations and Recommendations:
Typical cracks were noted in the concrete garage slab. No control joints were used in the pour here so the concrete will crack.
Recommendations:
Monitor or fill the cracks with a masonry rated caulking
Note:
If the cracks widen significantly or show signs of structural stress, consult a structural engineer for evaluation.
- C1HCFV-5 Ch. 11 Heating, Cooling, Fireplaces and Ventilation - 11.12 General Heating and Cooling Observations and Recommendations:
There was an older and soon-to-be outdated refrigerant used in this unit.
Recommendations:
It is recommended to replace the current system, with a system that uses modern A2L refrigerant, due to changes coming in the law.
Follow this link for updates: R-410 Phase Out
- C1HCFV-6 Ch. 11 Heating, Cooling, Fireplaces and Ventilation - 11.12 General Heating and Cooling Observations and Recommendations:
The pad supporting the outdoor condensing unit is not level. Mechanical system requirements state that equipment and appliances supported from the ground shall be level and firmly supported on a concrete slab or other approved material extending not less than 3 inches (76 mm) above the adjoining ground. Such support shall be in accordance with the manufacturer's installation instructions.
Recommendations:
I recommend a licensed HVAC contractor or other qualified workman review the condition and make corrections.~ IRC - Mechanical Code: M1305.1.4.1
- C1HCFV-7 Ch. 11 Heating, Cooling, Fireplaces and Ventilation - 11.12 General Heating and Cooling Observations and Recommendations:
Minor damage was noted on the ductwork. While it does not appear to significantly impact functionality at this time, repairs are recommended to prevent potential energy loss or further deterioration.
Recommendations:
A qualified HVAC professional should be consulted for evaluation and repairs as needed.
- C1HCFV-8 Ch. 11 Heating, Cooling, Fireplaces and Ventilation - 11.12 General Heating and Cooling Observations and Recommendations:
During the inspection, a buildup of dust, debris, and potential contaminants was observed in the ductwork, which may impact indoor air quality and HVAC system efficiency.
Recommendations:
It is recommended that a professional duct cleaning service or HVAC specialist be consulted to thoroughly clean the ductwork and ensure optimal air circulation and system performance.
- Drywall dust was noted inside the air handler - this should be cleaned as part of a new construction servicing.
- C1AP-1 Ch. 13 Additional Plumbing - 13.5 Additional Plumbing Observations and Recommendations:
The floor drain in the basement is missing a cover.
Recommendations:
Install the missing cover and check with a plumber to verify that this drain trap will stay primed top prevent sewer gas from entering the home.
- C1AP-2 Ch. 13 Additional Plumbing - 13.5 Additional Plumbing Observations and Recommendations:
Construction bricks were observed placed on the sump pump, which may interfere with its operation.
Recommendations:
It is recommended that the builder remove the bricks and inspect the pump to ensure proper functionality.
- C1ILAB-1 Ch 14. Interior Living Area(s) and Bedrooms - 14.11 General Interior Living Observations and Recommendations:
The door stop system for the home is incomplete.
Recommendations:
I recommend systematically installing door stops to protect doors and wall finishes.
- C1ILAB-2 Ch 14. Interior Living Area(s) and Bedrooms - 14.11 General Interior Living Observations and Recommendations:
The top edge of interior doors were found to be unfinished. Per most manufacturers' specifications, all surfaces of the door, including the top and bottom, should be properly sealed to prevent moisture absorption, which can lead to warping or swelling.
Recommendations:
It is recommended to have a qualified painter or contractor finish these areas to ensure the longevity of the doors.
Note:
Most doors are shipped without the top edge finishes and finishes are required to be completed on site.
Heres a link to help explain:
https://pdf.lowes.com
- C1ILAB-3 Ch 14. Interior Living Area(s) and Bedrooms - 14.11 General Interior Living Observations and Recommendations:
Caulking the inside of a window is crucial for maintaining a well-insulated, weatherproof, and aesthetically pleasing living or working environment. It contributes to the overall comfort, energy efficiency, and longevity of the building.
Recommendations:
Have areas around windows re-caulked by a qualified contractor.
- C1LF-1 Ch. 16 Laundry Facilities - 16.8 General Laundry Observations and Recommendations:
No drain pan was observed beneath the second-floor washing machine. A drain pan with a discharge line is typically required when installed above a finished space to help prevent water damage.
Recommendations:
It is recommended to have a licensed plumber evaluate and install a proper drain pan as needed.
- C1B-1 Ch. 17 Bathroom(s) - 17.8 General Bath Observations and Recommendations:
The backsplash behind the master and upstairs bathroom sink is not adequately sealed to the countertop and could allow water to get behind the countertop.
Recommendations:
Have a qualified professional seal with caulking.
- C1B-2 Ch. 17 Bathroom(s) - 17.8 General Bath Observations and Recommendations:
All the toilet(s) have not been caulked to the floor. Caulking the toilet to the floor is recommended and even required though opinions on this can vary. The biggest risk of not caulking the toilet to the floor is that the toilet can become loose.
Recommendations:
Repair as recommended by a licensed plumber.
- C1B-3 Ch. 17 Bathroom(s) - 17.8 General Bath Observations and Recommendations:
Missing caulking for the shower fixtures in the family, master and upstairs bathroom. Caulking should be applied to prevent any unnecessary water intrusion.
Recommendations:
Repair as recommended by a licensed plumber.
- C1FSB-1 Ch. 19 Foundation, Structure and Basement - 19.7 General Structure and Basement Observations and Recommendations:
Small vertical cracks were observed in the foundation wall. While these are often considered normal settling cracks, it is recommended to monitor them for any signs of widening or moisture infiltration.
Recommendations:
If further concerns arise, a foundation specialist should be consulted for evaluation.
This more than likely occurred when the concrete was poured
- C1FSB-2 Ch. 19 Foundation, Structure and Basement - 19.7 General Structure and Basement Observations and Recommendations:
Minor cracks were observed in the basement slab. While these do not appear to pose an immediate structural concern, it is recommended to monitor the cracks for any significant widening or moisture intrusion.
Recommendations:
If further concerns arise, a foundation specialist should be consulted for evaluation.
Safety
- C7G-2 Ch. 7 Garage - 7.6 General Garage Observations and Recommendations:
The laser eye safety mechanism for the overhead garage door has been set too high - this sensor should be 5-6 inches off of the floor to perform as intended and prevent entrapment.
Recommendations:
Have this further evaluated and repaired by a garage door specialist.
- C7G-3 Ch. 7 Garage - 7.6 General Garage Observations and Recommendations:
The self-closing hinges on the garage occupant-door are missing. This safety device is recommend to ensure the door to the garage is closed to keep pollutants and even fire from spreading into the house. This is a requirement that has been enforced and then removed from building standards over the years.
Recommendations:
It is currently recommended considered best-practices for improved safety.
- C7G-4 Ch. 7 Garage - 7.6 General Garage Observations and Recommendations:
Although not required by code, due to height and profile, it is still recommended to install a guardrail for the garage stairs for additional safety measures, as the stair height are close to the threshold where a guardrail would be mandated.
Recommendations:
Adding a guardrail enhances safety by reducing the risk of falls.
- C1P-3 Ch. 12 Plumbing - 12.10 General Plumbing Observations and Recommendations:
The discharge tube for the water heater temperature and pressure relief valve (TPRV) is plumbed using a PEX tubing. Though this is very common, this restricts the diameter of the opening and is unsafe and not recommended - see attached link. Ideally, the discharge tube for a relief valve:
- Terminates to an exterior location or above a drain, though this is not always possible
- Terminates between 6 and 24-inches off the ground (UPC)
- Slopes to drain to prevent water pooling inside the discharge tube
- Is not made from pipe with an inside diameter less than 3/4 on an inch
- Terminates to a visible location that can be monitored for leaks and discharges
- Does not have a threaded termination point which would prevent accidental capping of this important discharge
- Does not terminate into a drain pan
Recommendations:
I recommend having this relief valve discharge tube further investigated and repaired as recommended by a licensed plumber.
- C1P-4 Ch. 12 Plumbing - 12.10 General Plumbing Observations and Recommendations:
Testing of the plumbing system today, the water tested as too hot 125 degrees F. This is a scald hazard. To prevent scalding, standards recommend indoor hot water temperatures do not exceed 120 degrees. There is some evidence that hot water temperatures should be greater than 130 degrees to prevent Legionnaires' disease from developing in the water heater. If this is a concern, you can heat the water in the tank to 140 degrees F and have a tempering valve installed at the hot water tank. Please note that during inspection it is difficult to accurately test the water temperature as it can vary between fixtures. Testing is done in multiple locations during inspection and a median temperature is taken.
Recommendations:
Have this further evaluated and repaired by a licensed plumber or simply turn down the temperature as desired to eliminate a scald hazard.
- C1B-4 Ch. 17 Bathroom(s) - 17.8 General Bath Observations and Recommendations:
The glass door to the bathroom shower opens into the shower. This is non-standard and unsafe - all doors to showers should open out or swing in both directions so they can be escaped in an emergency.
Recommendations:
Monitor for safety or have this door updated for improved safety.
Further Evaluation Recommended
- C1ARSV-1 Ch. 18 Attic, Roof Structure and Ventilation - 18.9 General Attic, Roof Structure and Ventilation Observations and Recommendations:
The attic and roof cavity ventilation look to be non-standard. Proper attic ventilation is important for the roofing materials to perform as intended and to reduce chances for condensation problems and heat build-up in the attic. The problem here is the use of ridge vents and gable vents. Most ridge vent manufacturers recommend ridge and soffit vents only to get convective ventilation across the roof decking; the gable wall vents can disrupt this convective air flow. No evidence of problems from this configuration was noted to date and depending on occupant behavior this may not ever cause a problem.
Recommendations:
If you wish to correct, consult with a qualified general contractor about blocking off existing gable vents.
Note:
No red flags were observed on the day of inspection.
Inquire With Sellers
- CGC-2 Ch.1 General Comments - 1.1 Building Characteristics, Conditions and Limitations:
In accordance with the State of Ohio regulations, home inspectors are not required to obtain or research work permits. It is strongly recommended that clients inquire with the builder regarding any work permits, warranties, or guarantees associated with modifications or improvements made to the property. This includes all systems and components, such as structural elements, roofing and siding, electrical systems, HVAC, plumbing, and decking etc.
Other areas of this report may make reference to permits found or not found during the inspection.
- C9ES-1 Ch. 9 Electric Service - 9.3 Electric Service Permits Found:
No permit stickers or paper work related to electrical work were found on the electric panel. Inquire with builder for any additional information about this installation.
Notes
- CGC-1 Ch.1 General Comments - 1.1 Building Characteristics, Conditions and Limitations:
As this is a new construction building, the building plans, permits, drainage plans, construction records, a list of sub-contractors and warranty information is available. I recommend trying to obtain and keep this information for your records and for future re-sale.
- C1EDFW-1 Ch. 10 Electric Distribution and Finish Wiring - 10.2 Receptacles and Fixtures:
Several GFCI protected breakers were noted to be wired in series - see the kitchen, bathrooms, exterior, garage and basement.
A ground-fault circuit interrupter (GFCI) can be wired in series to protect other standard receptacles that are downstream of it. This method is called the multiple-location method.
Here are some things to know about wiring GFCIs in series:
How it works: The load terminals on a GFCI receptacle can be used to extend wiring to other receptacles. This gives the other receptacles GFCI protection, even though they aren't GFCI receptacles.
When to use it: This method is used when a single GFCI is needed to protect other standard receptacles.
What happens if the GFCI fails: If the GFCI fails, all of the downstream outlets will stop working.
Label Note:
These circuits seem to be GFCI protected, which is an acceptable repair. However, these receptacles should be labeled to indicate they are both ungrounded and GFCI protected. No labeling was found during inspection.
- C1HCFV-1 Ch. 11 Heating, Cooling, Fireplaces and Ventilation - 11. 8 Mechanical Ventilation Systems:
This building has a house ventilation fan timer. You typically want this set for at least two hours / day though this does depend on occupant behavior. The goal is to keep indoor relative humidity below 50% during cold weather.
- C1HCFV-2 Ch. 11 Heating, Cooling, Fireplaces and Ventilation - 11.9 Gas Fireplaces:
This gas log fireplace does not have a fan system installed. This is pretty normal, but if you wish to install a fan this will need to be added.
- C1HCFV-3 Ch. 11 Heating, Cooling, Fireplaces and Ventilation - 11.9 Gas Fireplaces:
A mantle has been installed above the gas fireplace. Direct vent gas fireplaces are designed principally for their aesthetic value, but they also produce as much heat output as possible, within ANSI and UL standards for combustible temperatures. The allowable standard for combustibles is 117°F above room temperature. Since the average room temperature is 70-75°F, a 187-192°F surface temperature can be expected. On a solid surface, such as a mantel, 150°F is very hot to the touch. Monitor this gas log during use and be sure combustible materials do not exceed this temperature standard. This installation may need to be replaced or reconfigured for improved safety.
Note: Also note that each manufacturer may have different clearance requirements for mantles. We try and look this stuff up where feasible, but often specific installation requirements are not accessible and in general, verification of manufactories installation requirements is not possible as part of a visual and limited home inspection. If you have concerns the best is to consult with the installation instructions from the manufacturer. If these can be located will will always assist with looking this up.
- C1HCFV-4 Ch. 11 Heating, Cooling, Fireplaces and Ventilation - 11.9 Gas Fireplaces:
The gas fireplace does not appear to be correctly labeled. Have this fireplace serviced and repaired to ensure it has the proper LP rated burner and it is correctly labeled.
- C1P-1 Ch. 12 Plumbing - 12.5 Waste Pipe and Discharge:
A video camera sewer scope is recommended. An evaluation of the sewer line below the ground is beyond the scope of this inspection. Due to the age and location of the building, a sewer scope is recommended to further evaluate the sewer line and the below ground connections between the house and the municipal sewer line. Sewer scopes are done using video cameras and can reveal the materials, condition and reliability of the sewer line. If that has been done recently, I recommend having a sewer scope performed.
📃 The Complete Inspection Report
Ch.3 Grounds
3.1
3.2 General Grounds Pictures
3.3 Driveways/Walkways/Patios
3.4 Grounds, Trees and Vegetation
3.5 Drainage and Site
3.6 Window and Stairwells
3.7 Retaining Walls
3.8 Fences
3.9 Outbuildings, Trellises, Storage Sheds, Barns
Ch.4 Exterior Siding, Doors and Windows
4.1
4.2 General Exterior Siding, Doors and Windows Pictures
4.3 Siding and Trim
4.4 Eaves
4.5 Exterior Doors
4.6 Exterior Window Frames
4.7 Exterior Vent and Exhaust Terminations
4.8 General Exterior Siding, Doors and Windows Observations and Recommendations
Ch. 5 Decks, Porches and Balconies
5.1 Wood Decks Porches and Balconies
5.2 Concrete Decks, Stoops, Landings and Porches
5.3 Exterior Stairs
5.4 Water-Resistant Decks and Balconies
5.5 Metal Decks and Balconies
Ch. 6 Roof, Chimney and Gutters
6.1
6.2 General Roof Views
6.3 Exterior Elevations and Roof Pitch
6.4 Roof Materials
6.5 Flashings, Valley’s and Penetrations
6.6 Gutters and Downspouts
6.7 Chimneys
6.8 Skylights
Ch. 7 Garage
7.1 General Garage Pictures
7.2 Garage General
7.3 Garage Doors and Automatic Openers
7.4 Garage Slab
7.5 Garage Stairs
7.6 General Garage Observations and Recommendations
Ch. 8 Fuel Storage and Distribution
8.1 General Comments
8.2 Gas Meter
8.3 Gas, Propane and Oil Piping
8.4 Oil Storage
8.5 Propane Storage
Ch. 9 Electric Service
9.1
9.2 Electrical System Safety Overview
9.3 Electric Service Permits Found
9.4 Electric Service Voltage Tested
9.5 Electric Service
9.6 Electric Service Equipment
9. 7 Sub Panel
9.9 Electrical Grounding System
9.10 Electrical Bonding System
Ch. 10 Electric Distribution and Finish Wiring
10.1 Branch Wiring
10.2 Receptacles and Fixtures
10.3 Ceiling Fans and Lighting
10.4 Smoke and Carbon Monoxide Alarm Systems
Ch. 11 Heating, Cooling, Fireplaces and Ventilation
11.1
11.2 Thermostat
11.3.1 Cooling Systems and Heat Pumps
11.3.2 Cooling Systems and Heat Pumps
11.4.1 Heating System
11.4.2 Heating System
11.5 Vents and Flues
11.6 Air Filters
11. 7 Heating and Cooling Distribution Systems
11. 8 Mechanical Ventilation Systems
11.9 Gas Fireplaces
11.10 Wood Burning/Solid Fuel Fireplaces
11. 11 Additional Heat Sources
11.12 General Heating and Cooling Observations and Recommendations
Ch. 12 Plumbing
12.1
12.2 Water Meter
12.3 Water Service Supply
12.4 Distribution Pipe
12.5 Waste Pipe and Discharge
12.6 Additional Sinks
12.7 Water Heater
12.8 Water Temperature
12.9 Exterior Hose Bibs
12.10 General Plumbing Observations and Recommendations
Ch. 13 Additional Plumbing
13.1 Sump Pumps and Drains
13.2 Radon Equipment
13.4.1 Sewage Ejector Pumps
13.4.4 Irrigation
13.5 Additional Plumbing Observations and Recommendations
Ch 14. Interior Living Area(s) and Bedrooms
14.1
14.2 General Interior Pictures
14.3 General Bedroom Pictures
14.4 Walls, Ceilings, Trim, Hallways and Closets
14.5 Floors and Floor Materials
14.6 Interior Doors and Doorstops
14.7 Windows
14.8 Wall Insulation, Air Bypass and Register Vents
14.9 Stairs and Railings
14.10 Indoor Air Quality
14.11 General Interior Living Observations and Recommendations
Ch. 15 Kitchen
15.1
15.2 General Kitchen Pictures
15.3 Sinks and Faucets
15.4 Cabinets and Countertops
15.5 Disposers
15.6 Dishwasher
15.7 Ranges, Ovens and Cooktops
15.8 Refrigerators
15.9 Ventilation Method
15.10 General Appliances
Ch. 16 Laundry Facilities
16.1
16.2 Laundry Pictures
16.3 Washer
16.4 Dryer
16. 5 Laundry Ventilation
16.6 Laundry Cabinets
16.7 Laundry Chute
16.8 General Laundry Observations and Recommendations
Ch. 17 Bathroom(s)
17.1
17.2 General Bathroom Pictures
17.3 Sinks and Cabinets
17.4 Toilet
17.5 Bathtub / Shower / Bathtub Walls and Enclosures
17.6 Bathroom Ventilation
17.7 General Bath Condition
17.8 General Bath Observations and Recommendations
Ch. 18 Attic, Roof Structure and Ventilation
18.1
18.2 General Attic Pictures
18.3 Attic Access
18.4 Roof Framing and Sheathing
18.6 Attic Insulation
18.7 Attic Fan Exhaust Vents
18.8 Attic and Roof Cavity Ventilation
18.9 General Attic, Roof Structure and Ventilation Observations and Recommendations
Ch. 19 Foundation, Structure and Basement
19.1
19.2 Foundation
19.3 Floor, Wall and Ceiling Framing
19.4 Basement
19.5 Basement Slab
19.6 Basement Moisture
19.7 General Structure and Basement Observations and Recommendations
Ch.1 General Comments
1.1 Building Characteristics, Conditions and Limitations
Style of Home: Traditional
Type of Building : Single Family (2-story)
Approximate Square Footage: More than 5000, 3125
Approximate Year of Original Construction: New Construction, 2024, 1985
Attending the Inspection: Buyer, Construction crew
Occupancy: Unoccupied
Animals Present: No
Weather during the inspection: Clear, Ice
Approximate temperature during the inspection: Below 32[F]
Ground/Soil surface conditions: Frozen, Snow-covered
For the Purposes of This Report, the Front Door Faces: West
This link provides access to the National Association of Home Builders: Residential Construction Performance Guide.
New Construction Note: New construction presents a more difficult inspection challenge due to the lack of any history at the structure. Items such as foundation settling, materials aging and other conditions that would be evident due to the natural aging and usage of the building have not yet become evident. Often there will be adjustments and minor repairs at most new structures over the first few years of occupation that will become evident only during usage and should be expected with any new structure.
This inspection consists predominantly of an interior viewing of the inspected unit and a partial visual inspection of other areas of the perimeter of the structure, [the roof, the grounds and the common areas] that are available and open for observation. Only this unit was open to viewing, though, so there was no attention given to any adjacent units or other units in the structure. Regarding zero lot line townhouse construction, responsibilities for maintenance and repairs falls substantially on the individual owner, although there are sections of the structure that will need cooperative efforts for repair, such as roofs, common exterior walls, common exterior grounds etc. For specific responsibilities though, gaining information from the condominium association's agreement is recommended to determine the actual responsibilities of the new occupant and how it may be shared with the group. It is highly recommended that the association’s building records and minutes be examined to determine whether there have been issues in the past at other units that might indicate a more substantial issue than what might be observed at the inspected unit, or that might require a general assessment.
For new homes, I would recommend that they receive substantial ventilation, which could consist of activation of the whole house fan system for longer than normal periods of time during initial occupation, as well as opening windows and allowing for cross ventilation to occur in a more significant manner than what might be usually considered adequate. Even though new materials are more eco-friendly, new structures have a significant amount of toxins that off-gas from newer engineered materials that are used in new construction, such as the chemicals used for carpet construction, particleboard adhesion and different types of resins and chemicals used in different paint and construction materials. More ventilation will help the initial period of off-gassing clear rather than letting this remain in the structure to build up at the interior.
I would recommend for new construction that the new owner gain copies of either "as built" or original building plans so that future changes, repairs or references can be made to this information. At least the association should have these on hand. Warranties for all the appliances and interior systems equipment should also be saved.
For new structures, accumulating some spare materials such as floor tile, specialty trims or tile work, roofing and other materials for minor repairs and replacements in the future is recommended. Generally as the years go by, model numbers and glazing types for materials change and it is sometimes difficult to get matching material. Keeping a small stockpile on hand can be very helpful in repairing the structure in the future
Info and LMT's. This house was vacant / unoccupied at the time of inspection. Vacant and unoccupied houses present unique challenges for home inspection, especially the piping and wiring systems which have not be subject to regular use prior to the inspection. While these systems can be tested during inspection, this one-time test is different than regular use and it is difficult to know how these systems will respond to regular use after the inspection. For example, septic systems may initially function and then fail under regular daily use. Plumbing traps may operate with no signs of leaks and then let go when being actively used for a few days. Shower pans may only leak when someone is standing in the shower and taking a shower. Seals for plumbing fixtures can dry up and leak when not is use. Sewer lines with roots may allow water flow, but then fail when waste and tissue are flushed; it can take a few days for that to backup. Please understand we are trying our best to look for clues of past or existing problems to paint a realistic best-guess as to the reliability of these systems during inspection.
At the time of the inspection, snow coverage was present, which limited the ability to fully evaluate certain exterior components such as the roof, walkways, driveway, deck, and grading around the foundation. Any hidden defects or concerns may only become apparent once the snow has melted.
For the sake of this inspection, the front of the structure will be considered as the portion pictured in the above cover photo. References to the left or right of the structure should be construed as standing in the front yard, viewing the front of the structure.
Info and LMT's. The approximate square footage listed here is listed as a courtesy and is based off of public records and disclosure. An evaluation of square footage of the buildings and property lines is beyond the scope of this inspection.
Info and LMT's. Unless the wiring in the building has been fully updated, this building likely has wiring that predates the late 1980's. Branch circuit wiring installed in buildings built prior to the late 1980s is typically rated for a maximum temperature of only 60 degrees Celsius. This includes non-metallic sheathed (Romex) wiring, and both BX and AC metal-clad flexible wiring. Knob and tube wiring, typically installed in homes built prior to 1950, may be rated for even lower maximum temperatures. Newer electric fixtures including lighting and fans typically require wiring rated for 90 degrees Celsius. Connecting newer fixtures to older, 60-degree-rated wiring is a potential fire hazard. Repairs for such conditions may involve replacing the last few feet of wiring to newer fixtures with new 90-degree-rated wire, and installing a junction box to join the old and new wiring. It is beyond the scope of this inspection to determine if any such incompatible components are installed. Based on the age of this building, be aware that such components may be present.
Info and LMT's. In 1978, federal laws were passed to prohibit use of lead and asbestos in building materials. Manufacturers of building materials were allowed to sell existing stocks of materials that were manufactured with lead and asbestos, so even buildings constructed as late as the mid-1980's could possibly contain lead or asbestos. Identification and testing for lead and asbestos and other environmental testing is beyond the scope of this home inspection. If you wish to seek additional information, I recommend contacting an environmental lab or industrial hygienist.
In accordance with the State of Ohio regulations, home inspectors are not required to obtain or research work permits. It is strongly recommended that clients inquire with the builder regarding any work permits, warranties, or guarantees associated with modifications or improvements made to the property. This includes all systems and components, such as structural elements, roofing and siding, electrical systems, HVAC, plumbing, and decking etc.
Other areas of this report may make reference to permits found or not found during the inspection.
As this is a new construction building, the building plans, permits, drainage plans, construction records, a list of sub-contractors and warranty information is available. I recommend trying to obtain and keep this information for your records and for future re-sale.
1.2 Ancillary
Pest/Termite: Waived by Client
Radon: Completed
Well/Septic: N/A
This home inspection does not include a termite inspection. Clients are advised to consult a licensed pest control professional for a thorough evaluation of potential termite activity or damage.
Info and LMT's. If additional inspections, such as termite, radon, or well/septic evaluations, are requested, the findings will not be included in this report. Instead, separate reports will be provided by the respective specialized entities conducting those inspections. Any additional inspections requested will not be conducted by members of Olonzo Inspections. These inspections are scheduled solely as a courtesy to the client(s).
Ch. 2 Appliance Disconnects and Utility Shutoffs
2.1 Shutoffs and Disconnects Noted
Picture Showing Additional Gas Line Shutoffs Fireplace and Additional Shutoff(s)
Picture Showing Main Electric Panel Disconnect at the Electric Meter.
The service disconnect or main OCPD (over current protection device) was inspected looking for any deficiencies and reporting on its location. This disconnect can be a breaker, fuse block, or kill switch. This is the means of shutting off all electricity entering the home
Ch.3 Grounds
3.1
Per the Standards of Practice, the home inspector shall observe Exterior electrical receptacles and the presence of GFCI protection (GFCI protection was not required prior to 1975, but upgrading is recommended for safety). Decks, balconies, stoops, steps, areaways, porches, and applicable railings that are directly attached to the structure. Vegetation, grading, and drainage of grounds, driveways, patios, walkways, and retaining walls will be inspected with respect to their effect on the condition of the structure.
The home inspector is not required to observe: Fences and gates, Geological conditions, Soil conditions, Recreational facilities (including spas, saunas, steam baths, swimming pools, tennis courts, playground equipment, and other exercise, entertainment, or athletic facilities), Detached buildings or structures, or the Presence or condition of buried fuel or waste storage tanks. The home inspector is not required to: Move personal items, panels, furniture, equipment, plant life, soil, snow, ice, or debris that obstruct access or visibility.
3.2 General Grounds Pictures
3.3 Driveways/Walkways/Patios
Driveway: Concrete
Walkways: Concrete
Patios: Concrete, Pavers
Info and LMT's. All flatwork was not fully visible for inspection today due to snow and ice cover. I recommend having additional inspections completed at a later time when the snow has cleared off.
3.4 Grounds, Trees and Vegetation
Trees/Vegetation too near building: Well Pruned-Monitor
The vegetation here has been nicely pruned back off the house. Be sure to keep this up; this is require regular maintenance.
3.5 Drainage and Site
Site Description: Moderate slope
Downspout Discharge: Below grade
Info and LMT's. Regular monitoring your homes drainage allows timely identification of clogs, blockages, or inadequate slope that could hinder effective drainage. Addressing drainage issues promptly can help maintain the integrity of the home, prevent costly repairs, and safeguard its long-term value.
As a general rule, the soil, or grading is recommended to slope away from the structure, with a 6-inch drop in elevation, in the first 10 feet away (5% grade).
Info and LMT's. The grounds in contact with the structure were inspected to determine that they were sloped to allow rainwater to drain away from the structure adequately. The soil is recommended to slope away from the foundation, with a 6-inch drop in elevation, in the first 10 feet away from the structure (5% grade). When the 5% grade can not be achieved, swales or drains should be used as needed to properly divert and/or manage rainwater runoff. Any flat or low areas around the structure should be backfilled and sloped away from the foundation to prevent potential moisture infiltration into areas below grade (as applicable). No significant grading deficiencies were present at the time of inspection unless otherwise noted in this report.
Info and LMT's. The home inspection performed does not extend to the examination of subterranean drainage systems. Consequently, it does not include the inspection of underground pipes, drains, or similar components situated beneath the surface, which are tasked with diverting water from the premises. Any possible concerns relating to these underground drainage structures fall outside the purview of the inspection and would necessitate evaluation by appropriate specialists should the need arise.
Info and LMT's. The evaluation of grading and lot drainage effectiveness is based solely on the conditions observed during the inspection and is not guaranteed due to the dynamic nature of environmental factors. Changes in weather, particularly heavy rainfall, can expose issues that were not apparent during the inspection. Additionally, issues like leaks in downspouts and gutter systems may remain undetected in dry weather, potentially contributing moisture to the soil near the foundation.
Assessment of grading and drainage performance concerning moisture infiltration through foundation walls or under slabs is limited to visible conditions and evidence of previous problems at the time of inspection. It is advisable to communicate with the sellers regarding any history of moisture intrusion into the structure and review the Seller's Disclosure for potential disclosure of such issues.
3.6 Window and Stairwells
Present
3.7 Retaining Walls
Block
Retaining walls are inspected in respect to their effect on the structure of the home. The structural integrity or load bearing capacities of retaining walls are beyond the scope of a home inspection.No significant deficiencies were observed in the walls relation to the structure unless otherwise noted in this report.
3.8 Fences
None noted
3.9 Outbuildings, Trellises, Storage Sheds, Barns
None Noted
Ch.4 Exterior Siding, Doors and Windows
4.1
Per the Standards of Practice, the home inspector shall observe from ground level: - Wall cladding, flashings, and trim; entryway doors and a representative number of windows; eaves, soffits, and fascias. The home inspector shall: Describe wall cladding materials, Operate all entryway doors and a representative number of windows, and probe exterior wood components where deterioration or damage is suspected.
The home inspector is not required to observe: Storm windows, storm doors, screening/screens, shutters, awnings, and similar seasonal accessories; the Presence of safety glazing in doors and windows; Detached buildings or structures; or the Presence or condition of buried fuel storage tanks, water tanks, or septic tanks. The home inspector is not required to: Move personal items, panels, furniture, equipment, plant life, soil, snow, ice, or debris that obstruct access or visibility.
4.2 General Exterior Siding, Doors and Windows Pictures
Info and LMT's. A home inspection entails a visual inspection of the accessible exterior components of the property that are readily accessible able and available. It does not encompass a thorough evaluation of concealed elements, nor does it consider weather-related influences, concealed damages, or inaccessible areas.
4.3 Siding and Trim
Trim Material: Wood, Fiber cement
Siding Material: Brick, HardiePlank
The wall, wall cladding and trim were inspected, looking for significant damage, proper flashings, potential water entry points, etc. No reportable deficiencies were visibly present at the time of inspection unless otherwise noted in this report.
Info and LMT's. All visible sections of the flashings were examined for any notable deficiencies, including Z-flashings, drip caps, etc., where relevant. Given that flashings are often concealed by wall claddings, their functionality is assessed by checking for signs of moisture intrusion or damage in areas where they are expected to be present.
HardiePlank Siding
HardiePlank siding is a fiber-cement type siding that consists of fibrous materials with a cement component and silica sand/fibers that are compressed together with interior resins that have an embossed outside textured or smooth appearance. HardiePlank contains no asbestos, fiberglass or formaldehyde. This material is a relatively newly engineered product. It has no long term track record to match the 30 year warranty that comes with it, but it has received good reviews in the trades regarding it's stability and durability if properly applied and maintained. It has also become a very popular siding alternative to wood siding due to its durability, price and low maintenance characteristics.
There are some specific requirements for installation and protection. HardiePlank can be blind-nailed or face nailed at the builders discretion but is recommended to be face nailed in high wind areas. HardiePlank cannot be blind nailed with 24" oc framing. Nails should be corrosion resistant and caulked, and double nailed if a penetration of the siding skin occurs while nailing. Butt ends of material should be in moderate contact with minimal gapping and are currently not recommended to be caulked. Previously, up until Oct 2008, the butt joints were recommended to be either butted together or gapped a maximum of 1/8” and caulked. Currently the joints should have “joint flashing” behind, which can consist of a number of different materials such as Mylar, felt, metal or strip/gap backing. At this time Hardie does not specify what the joint backing material requirements are. All window, door and trim connections should be caulked as with standard building practice. It can be hand nailed or compressor nailed, but staples should not be used. Full installation instructions are noted with a link below.
Penetrations such as hose bibs and holes 1 1⁄2” or larger, such as dryer vents, furnace vents, electrical and light fixture boxes should have a flashed block of trim around point of penetration. Smaller piping does not require blocking but should be well caulked.
HardiePlank and HardiePanel need to be kept painted. This is a fiber cement material that is porous and will absorb moisture if not kept sealed, which can cause flaking, mold and deterioration. Any caulking, primer or paint used is required to be 100% latex acrylic material. HardiePlank should not be stained.
There have been numerous difficulties with different types of applied products that are engineered, such as Louisiana-Pacific siding, Masonite Omni-Board, pressboard panel type siding as opposed to natural materials such as cedar siding. HardiePlank siding, having limited long term history, is difficult to comment on in regard to its expected life span and aging characteristics, but has been faring very well in comparison.
HardiePlank siding does have a “30-Year Limited Transferable Warranty”, but "transferable", as stated in the fine print of this materials contract, includes transference only from the original material buyer, meaning the builder, to the first purchaser and then to the second purchaser. Subsequent buyers/owners are not covered by this warranty. Calling this a 30-year transferable warranty seems optimistic since upon sale of the structure to a third buyer and beyond, there is no warranty protection. Few structures are owned for 30 years by just two individuals.
Further information:
James Hardie Building Products at 1-800-426-4051 - www.jameshardie.com
HardiePlank installation instructions http://www.jameshardie.com/d2w/installation/hardieplank-hz10-us-en.pdf
Hardie Best Practices https://www.jameshardiepros.com/Install-and-Tech-Docs/BrowseTechDocs?doctype=Best%20Practice%20Guide
4.4 Eaves
Vinyl, Wood
The roof overhangs were inspected at visible portions looking for any water damage or other significant defects. No reportable conditions were visibly present at the time of inspection unless otherwise noted in this report. The possibility of hidden damage exists on any structures with fascia and/or soffit that is clad with vinyl/aluminum.
4.5 Exterior Doors
Exterior Door Styles: Solid core, Sliding glass
Info and LMT's. Handlesets, including deadbolts and door handles, are not assessed for functionality with keys during the inspection. It is advisable to consider replacing or re-keying any deadbolts and handles due to uncertainty regarding who may have access to keys for the residence. Consequently, deadbolts and handles will be evaluated solely based on their alignment with the door, focusing on any issues preventing proper latching or locking.
4.6 Exterior Window Frames
Window Frames: Vinyl
The exterior components of the windows (trim, flashing, etc.) were inspected looking for damage, lack of proper flashing, clearance from grade, etc.No reportable deficiencies were visibly present at the time of inspection unless otherwise noted in this report.
It is always my recommendation to monitor and maintain this area to prevent future problems such as water or pest intrusion.
4.7 Exterior Vent and Exhaust Terminations
Present, Bathroom Vent(s), Dryer Exhaust, HVAC, Fireplace
4.8 General Exterior Siding, Doors and Windows Observations and Recommendations
The backdraft damper for the exterior fan vent cover is not closing properly on the right side of the property. The damper is important to prevent air from entering the house and fan vent when the fan is not in use.
Recommendations:
Have this further evaluated and repaired as recommended by a qualified contractor.
Ch. 5 Decks, Porches and Balconies
5.1 Wood Decks Porches and Balconies
None noted
5.2 Concrete Decks, Stoops, Landings and Porches
Concrete entry
The concrete decks, stoops landings and porches were inspected, looking for significant damage, proper flashings, potential water entry points, cracks, slopes and structural integrity. etc. No reportable deficiencies were visibly present at the time of inspection unless otherwise noted in this report.
5.3 Exterior Stairs
Present
5.4 Water-Resistant Decks and Balconies
None Noted
5.5 Metal Decks and Balconies
None Noted
Ch. 6 Roof, Chimney and Gutters
6.1
Per the Standards of Practice, the home inspector shall observe: The roof covering, roof drainage systems, visible flashings, skylights, chimneys, and roof penetrations and report signs of leaks or abnormal condensation on building components. The home inspector shall: Describe the type of roof covering materials and Report the method used to observe the roofing.
The home inspector is not required to: Walk on the roofing (although every safe attempt to do so will be taken), report on the age or remaining life of the roof covering, or move leaves, snow, or other items on the surface that may block visual accessibility, or observe attached accessories including but not limited to solar systems, antennae, satellite dishes, and lightning arrestors. No claims will be made as to the remaining roof material life expectancy, and no guarantee or warranty should be expected from comments or observations. The sellers or the occupants of a residence will generally have the most relevant knowledge of the roof and of its history. Therefore, I recommend that you consult with the sellers about the age of the roof covering and that you either include comprehensive roof coverage in your home insurance policy or obtain a roof certification from an established local roofing company.
6.2 General Roof Views
Info and LMT's. The examination of the roof and its covering material is confined to the conditions observed on the day of inspection exclusively. The assessment includes inspecting the roof covering material, visible sections of the roof structure within the attic (if accessible), and interior ceilings to identify any signs of existing or previous leaks. It's important to note that leaks may become apparent in the future or during adverse weather conditions that were not evident during the inspection.
Any deficiencies documented in this report regarding the roof covering or signs of past or present leaks should be addressed promptly by a licensed roofing contractor. They should be evaluated and remedied as necessary to ensure the integrity of the roof and prevent potential damage.
6.4 Roof Materials
Roof Covering Materials: Asphalt shingle, Architectural grade composition shingle
Method of Roof Inspection: Viewed with a camera stick, Snow
Roof Style: Gable
Overlay Roof: No
Shingle Fastening Accessible For Inspection : No
Percentage of Roof that could be Safely Traversed: 0%
Approximate Age of Roof Covering: New
The visual components of the roofing materials were inspected for proper roofing material, structure, flashing, gutters and downspouts, ventilation and penetrations and debris. No reportable deficiencies were present at the time of inspection unless otherwise noted in this report.
Info and LMT's. This home inspection does not provide a thorough examination of the roof's structural integrity or concealed components. The assessment is restricted to visually inspecting the accessible areas of the roof without utilizing invasive methods. Weather-related influences, concealed damages, or inaccessible sections are not taken into account during the inspection. For a more comprehensive analysis, it is advised to seek assistance from a qualified roofing professional. Only the readily visible and accessible sections of the roof were inspected on the day of assessment.The purpose of the inspection is to determine general condition, NOT to determine life expectancy.
Info and LMT's. This roof was not fully visible for inspection today due to snow and ice cover. I recommend having the roof inspected at a later time when the snow has cleared off.
Info and LMT's. Please note that when inspecting composition roof installations, I try and look under shingles to see how the shingles have been fastened. Proper fastening is critical for successful roof performance. Often the shingles are bonding so well, they cannot be lifted to inspect the fastening. In this case, I was unable to lift the shingles and see the fastening pattern - they are bonded well and I do not use a flat bar to pry them apart as part of a visual inspection unless there is a reason to start chasing visible leaks. While this limits my visual inspection, this is a good sign, as loose, un-bonded shingles can lead to wind damage and would be written up as a defect.
Info and LMT's. The information provided below is based on general observations and industry standards and should be treated as a rough estimate. Determining the exact age of a roof without official records or professional inspection is challenging and may not always be accurate. Factors such as maintenance history, climate conditions, and quality of materials can significantly affect the lifespan of a roof. It is strongly recommended to consult with a qualified roofing professional for a thorough inspection and assessment of your specific roof. The information provided in this disclaimer is not intended as a substitute for professional advice, and any actions taken based on this information are solely at the discretion and responsibility of the individual. The accuracy or completeness of the estimation cannot be guaranteed, and no liability is assumed for any damages, losses, or inconvenience arising from the use of this information.
6.5 Flashings, Valley’s and Penetrations
Present and Visually Standard, Plumbing Stack Vent
Roof flashings are used to keep a roofing system waterproof where the roofing material starts, stops, changes direction or is penetrated. During inspection, we look for standard flashing techniques that could be considered normal or standard in our region. Damaged, incomplete or non-standard flashings can be a sign of an older or less reliable roofing system and may require repair. Any non-standard flashings noted during inspection will be reported on below if found.
Visible portions of the flashings were inspected, looking for significant deficiencies (drip edge, sidewall, headwall, counter, step, etc. - as applicable). Typically most areas of flashings are not visible as they are covered by the roof covering material and/or the wall cladding (as applicable), and these areas are excluded from this inspection. Therefore functionality has to be determined by looking for moisture intrusion on ceilings where the flashing was presumed to be in place or on the roof decking from within the attic (as accessible). No reportable conditions were observed at visible portions at the time of inspection unless otherwise noted in this report.
6.6 Gutters and Downspouts
Gutter and Downspout Materials: Aluminum
The gutters and downspouts were inspected looking for proper securement, debris in the channel, standing water, damage, etc. Leaking gutters can not be diagnosed if an active rain was not occurring at the time of inspection, and if leaks are noticed after taking ownership of the property, sealing or repairs may be needed at seams or endcaps. No deficiencies were visibly present at the time of inspection unless otherwise noted in this report.
It is always my recommendation to monitor and maintain this area to insure the home has a proper drainage system.
6.7 Chimneys
None noted
6.8 Skylights
None Noted
Ch. 7 Garage
7.1 General Garage Pictures
7.2 Garage General
Garage Type: Attached
Fire Seperation: Not Visible
7.3 Garage Doors and Automatic Openers
Overhead Garage Door Type: Vinyl
Automatic Garage Opener: Present
Garage Occupant Door: Hinges Missing
The garage door, rollers, brackets, door panels, springs, and tracks were inspected looking for damage or loose components. No reportable conditions were present at the time of inspection unless otherwise noted in this report.
The garage door(s) were tested by operating the wall-mounted transmitter and checking for proper operation. The door(s) were examined for significant damage or installation-related deficiencies. No reportable conditions were present at the time of inspection unless otherwise noted in this report.
7.4 Garage Slab
Garage Floor: Concrete
Completed Visible portions of the concrete slab was inspected looking for significant deficiencies and/or significant cracking. No reportable conditions were present at the time of inspection unless otherwise noted in this report.
Any references to cracks on basement or garage concrete slabs will need to be sealed with an appropriate material by a qualified person at a minimum, regardless of the cracks size. This will prevent the possibility of moisture/water infiltration rising through the crack(s) during periods of heavy rainfall.
7.5 Garage Stairs
Standard
The garage stairs were inspected by evaluating the risers and treads, applicable railings, etc. No significant deficiencies were present at the time of inspection unless otherwise noted in this report.
7.6 General Garage Observations and Recommendations
Typical cracks were noted in the concrete garage slab. No control joints were used in the pour here so the concrete will crack.
Recommendations:
Monitor or fill the cracks with a masonry rated caulking
Note:
If the cracks widen significantly or show signs of structural stress, consult a structural engineer for evaluation.
The self-closing hinges on the garage occupant-door are missing. This safety device is recommend to ensure the door to the garage is closed to keep pollutants and even fire from spreading into the house. This is a requirement that has been enforced and then removed from building standards over the years.
Recommendations:
It is currently recommended considered best-practices for improved safety.
Although not required by code, due to height and profile, it is still recommended to install a guardrail for the garage stairs for additional safety measures, as the stair height are close to the threshold where a guardrail would be mandated.
Recommendations:
Adding a guardrail enhances safety by reducing the risk of falls.
Ch. 8 Fuel Storage and Distribution
8.1 General Comments
Fuel Sources Present
8.2 Gas Meter
Present
Gas Pipe Materials: Steel and flex pipe
8.3 Gas, Propane and Oil Piping
Gas Piping Materials Noted: Steel, CSST
8.4 Oil Storage
None noted
8.5 Propane Storage
None noted
Ch. 9 Electric Service
9.1
Per the Standards of Practice, the home inspector shall observe Service entrance conductors; Service equipment, grounding equipment, the main overcurrent device, main and distribution panels; Amperage and voltage ratings of the service (if the conductors' sizing text is present/legible); Branch circuit conductors, their overcurrent devices, and the compatibility of their ampacities and voltages. The home inspector shall describe Service amperage and voltage (if known), Service entry conductor materials, Service type as being overhead or underground, and the location of main and distribution panels. The home inspector shall report on: the presence of any observed aluminum branch circuit wiring.
The home inspector is not required to: Insert any tool, probe, or testing device inside the panels; Test or operate any over-current device except ground fault circuit interrupters; Dismantle any electrical device or control other than to remove the covers of the main and auxiliary distribution panels; or Observe: Motion or Dusk to Dawn lighting, Low voltage systems; Security system devices, heat detectors, or carbon monoxide detectors; Telephone, security, cable TV, intercoms, or other ancillary wiring that is not a part of the primary electrical distribution system.
9.3 Electric Service Permits Found
Permits Stickers Found: No Permits Found
No permit stickers or paper work related to electrical work were found on the electric panel. Inquire with builder for any additional information about this installation.
9.4 Electric Service Voltage Tested
Service Voltage: 120/240
Info and LMT's. The service amperage is determined by inspecting the service entrance conductors size as well as the service disconnects size. Voltages are not tested for and therefore not confirmed, so 120/240VAC is presumed unless noted in report. In some situations the sizing of the service entrance conductors will not be legible or marked and the stated amperage will be followed by "presumed" as it could not be verified.
9.5 Electric Service
Meter Base Amperage: 200
Service Entrance: Below Ground
9.6 Electric Service Equipment
Main Electric Panel Location: Basement
Main Panel Amperage: 200 amps
Panel Manufacturer: Square D
Service Entrance (SE) conductor Size: Aluminum, 4/0, 200 amps
Electric Service Amperage: 200 amps
An infrared camera was employed to detect any thermal irregularities in the electrical panel(s). During the inspection, no anomalies were detected under the current loading conditions, unless specified otherwise in this report. However, it is important to note that anomalies may emerge under heavier loads, such as those experienced during normal occupancy.
The service amperage is determined by inspecting the service entrance conductors size as well as the service disconnects size. Voltages are not tested for and therefore not confirmed, so 120/240VAC is presumed unless noted in report. If a concern, a licensed electrician could test for proper voltages to see if 120/208VAC is present. In some situations the sizing of the service entrance conductors will not be legible or marked and the stated amperage will be followed by "presumed" as it could not be verified.
9. 7 Sub Panel
Not Present
9.9 Electrical Grounding System
Present - Could Not Confirm, UFER Ground Not Visible
Info and LMT's. During a home or property inspection, every effort is made to inspect the visible components of the electrical system grounding. The grounding system is critical for safely discharging electrical surges, especially in the case of lightning strikes. There is no way in the context of a home inspection to verify the "effectiveness" of the grounding system as much of the system is not visible and there are not practical tests one can perform in the way we can test a furnace or a plumbing fixture. However, there are many things that can lead me to recommend further evaluation of the grounding system by a licensed electrical contractor and they will be documented in the observations below if discovered.
9.10 Electrical Bonding System
Present - Could Not Confirm, Bonding Noted on Water Pipes, Bonding Noted on Gas Pipes
Info and LMT's. During the inspection, I attempt to visually document electrical system bonding. There is no way in the context of a home inspection to verify the "effectiveness" of system bonding. All metallic systems in the building are required to be "bonded" (connected) to the the building's electrical grounding system. Bonding creates a pathway to shunt static charges (that would otherwise build up on the system) to earth, and to provide a pathway to trip a breaker in the event that these bonded metallic components became energized. There are many things that can lead me to recommend further evaluation of this system by a licensed electrical contractor and they will be documented as repair items in the observations below if discovered.
Ch. 10 Electric Distribution and Finish Wiring
10.1 Branch Wiring
Wire Material: Copper, Multi-strand Copper
Wiring Method: Non-metallic sheathed cable
The branch wiring was inspected at visible portions looking for any significant deficiencies or defects that could be a fire and/or safety hazard; including but not limited to: connections made outside of a junction box, wiring terminations, open junction boxes, damage, the wiring material, improper support, etc. The majority of branch feeders are not visible due to being behind wall and ceiling coverings, insulation, etc. No significant deficiencies were visibly present at the time of inspection unless otherwise noted in this report.
10.2 Receptacles and Fixtures
Electric Receptacles: Three wire receptacles
Inspection Method: Representative Testing
A representative number of outlets were inspected by, visual examination and with an outlet tester, ensuring that they functioned properly and safely (I will attempt to test all outlets as long as they are not obstructed by personal belongings). No reportable conditions were present at the time of inspection unless otherwise noted in this report.
Info and LMT's. Receptacles of 220V/240V and 20-amp dedicated circuits are not assessed for functionality or polarity during the inspection, as they cannot be tested using a standard receptacle polarity tester. Any visible deficiencies pertaining to these receptacles will be noted in the report.
Info and LMT's. Fully confirming or locating GFCI protection in certain areas of the home may be challenging as the protection mechanisms are not always visible. When test and reset buttons are not present on each receptacle, tripping them with a polarity tester might inadvertently affect downstream receptacles that are obstructed by personal belongings or otherwise inaccessible. This could result in those receptacles losing power. I suggest verifying GFCI protection in all recommended areas after personal belongings have been removed or upon assuming ownership of the property. If you're unsure about this process, it's advisable to enlist the services of a licensed electrician for assistance.
Several GFCI protected breakers were noted to be wired in series - see the kitchen, bathrooms, exterior, garage and basement.
A ground-fault circuit interrupter (GFCI) can be wired in series to protect other standard receptacles that are downstream of it. This method is called the multiple-location method.
Here are some things to know about wiring GFCIs in series:
How it works: The load terminals on a GFCI receptacle can be used to extend wiring to other receptacles. This gives the other receptacles GFCI protection, even though they aren't GFCI receptacles.
When to use it: This method is used when a single GFCI is needed to protect other standard receptacles.
What happens if the GFCI fails: If the GFCI fails, all of the downstream outlets will stop working.
Label Note:
These circuits seem to be GFCI protected, which is an acceptable repair. However, these receptacles should be labeled to indicate they are both ungrounded and GFCI protected. No labeling was found during inspection.
10.3 Ceiling Fans and Lighting
Lighting: Present and Tested
Lighting was tested looking for functionality and safety. No reportable conditions were visibly present at the time of inspection unless otherwise noted in this report.
Info and LMT's. Exterior dusk-to-dawn lights, motion lights, landscape lighting, or any lighting fixtures not affixed to the structure are not encompassed within a standard home inspection and were not evaluated for functionality. These elements are explicitly excluded from the inspection.
10.4 Smoke and Carbon Monoxide Alarm Systems
CO Alarms Noted: Outside all Sleeping Areas, On Main Floor, On 2nd Floor, In Basement
CO Alarms: Present
Smoke Alarms Noted: On Main Floor, On 2nd Floor, In Basement, In All Bedrooms
Smoke Alarms: Present
The installation of carbon monoxide alarms is recommended for all homes that have fuel burning appliances such as gas or oil furnaces, gas water heaters, gas ovens and cooktops, gas fireplaces and wood stoves. The location should be: at least one alarm outside of all sleeping areas and one on each floor of the house. Best practices are to have these alarms hardwired with a battery back-up - though requirements are for the installation to meet manufacturer's specifications. Carbon monoxide is a colorless, odorless gas that can cause sickness, nausea and even death. Alarms have a useful service life of roughly 6 years, so changing them more frequently than smoke alarms is recommended.
The link below includes important information about smoke alarms that could save lives in the event of a fire. There are two basic types of smoke alarms: ionization, which are better at detecting flaming fires and photoelectric, which are better at detecting smoldering fires. Standards in the building industry are moving toward recommending BOTH types of detectors in the home. It is nearly impossible to accurately test smoke alarms during a home inspection. I recommend learning more about these important life saving devices and consider installing both types of smoke detectors in your home. http://getscribeware.com/blog/wp-content/uploads/2016/04/Ionization-vs-photoelectric.pdf
Smoke detectors, also known as smoke alarms, are designed to detect smoke and alert occupants of a building to the presence of a fire. The frequency with which smoke detectors should be tested and maintained depends on the type of detector and the manufacturer's recommendations.
Most smoke detectors should be tested at least once a month to ensure that they are functioning properly. This can be done by pressing the "test" button on the detector, which will cause it to emit a loud alarm sound. If the alarm does not sound, the detector may need new batteries or may need to be replaced.
In addition to monthly testing, smoke detectors should be cleaned regularly to ensure that they are free from dust and other debris that can interfere with their operation. This can be done by gently vacuuming the detector or wiping it with a clean, dry cloth.
Smoke detectors also have a limited lifespan, typically ranging from 5 to 10 years depending on the type and model. Manufacturers usually recommend replacing smoke detectors after this time to ensure that they continue to function properly.
In summary, smoke detectors should be tested at least once a month, cleaned regularly, and replaced after their recommended lifespan to ensure that they are functioning properly and can alert occupants to the presence of a fire.
As a safety precaution, It would always be my recommendation to update or replace all smoke or carbon detection systems when acquiring a new home.
Info and LMT's. During the home inspection, I try and test a representative sample of the smoke alarms by using the test button on the alarms. This is NOT an accurate test of the sensor just a test to see if the unit is powered. For reliability, fire marshals recommended updating smoke alarms every 10 years and changing batteries bi-annually. The latest data indicate that we should be using photoelectric technology in our smoke alarms for improved fire detection and to reduce problems with false alarms which can lead to disabling of this important safety system. Unfortunately, the alarms have to be removed to determine if they are photo-electric or ionization types. It is surprisingly complex to accurately test a smoke alarm system and determine the reliability, age, and type of sensor technology used, especially as many homes can have half a dozen or more alarms throughout the house. A complete evaluation of smoke alarms is beyond the scope of this inspection. For optimal fire safety, I recommend taking control of these important safety devices and learning about how to service and maintain your smoke alarm system to keep the building occupants safe. For more information, please read this link. For more information, please read this link.
Ch. 11 Heating, Cooling, Fireplaces and Ventilation
11.1
Per the Standards of Practice, the home inspector shall observe the permanently installed heating and cooling systems, including Heating and cooling equipment central to the home; visible ducts and piping, air filters, registers, and the presence of an installed heating and cooling source in each room. The home inspector shall describe the energy source and heating equipment. The home inspector shall operate the systems using normal operating controls. The home inspector shall open readily accessible access panels provided by the manufacturer or installer for routine homeowner maintenance. The home inspector is not required to: Operate heating systems when weather conditions or other circumstances may cause equipment damage; Operate automatic safety controls; Ignite or extinguish solid fuel fires; or Observe Humidifiers, Electronic air filters; or The uniformity or adequacy of heat supply to the various rooms. The efficiency of the units and load testing is not conducted. Air conditioning units can not be tested when temperatures are lower than 60 degrees due to the possibility of damaging the compressor. Clients are advised to have an HVAC company perform maintenance on the system annually.
11.2 Thermostat
Location: Living Room
11.3.1 Cooling Systems and Heat Pumps
Cooling System: Heat Pump Present
Data Plate: Shown here
Manufacturer: Bryant
Listed Nominal Capacity: 3 Tons
Energy Source: Electric
System Type: Air Source
Age: 2023
Info and LMT's. Regular cooling system maintenance is important. Due to the numerous causes of any system malfunction, assessment by a qualified cooling serviceman is advisable. Periodic refrigerant recharging may be needed; such conditions may not be predictable.
Condensate back up or leakage can lead to Mold or what looks like mold.
The outdoor unit base should be maintained in a reasonably level position. The coils will require periodic cleaning; clearance from vegetation/obstructions should also be provided.
Clean air filters not only improve the living environment, they also help maintain the Air Conditioner components by providing proper cooling of the internal parts and reducing dust accumulation in key components.
According to commonly accepted home inspection industry standards, there should be a 15-20 degree F difference in temperature between the return air duct and the supply air ducts, after about 20 minutes of operation. This is supposed to give the inspector a rudimentary indication of whether the unit is functioning or not. Documenting this split is required when feasible by the Home Inspector Standards of Practice and I must emphasize the test is relatively meaningless. Humidity, outdoor air temperature, air flow speed, coolant fluid pressure, leaking ducts, duct location, air filter condition and other considerations impact true efficiency and function. When there is less of a differential or a greater differential further evaluation by a qualified HVAC contractor may be warranted and generally is warranted. Nothing stated in the report should ever be construed to mean the system is "properly functional" or "fully functional" as that is only something that can be determined by complicated and invasive testing by a licensed HVAC contractor which is always recommended in the context of your due diligence.
It's important to be aware of how long air conditioners last, so you don't get the unwelcome surprise of a broken air conditioner in the peak of the summer heat. In general, air conditioners that are properly maintained can last 15 to 20 years.
Info and LMT's. The air conditioning system and condensate control system could not be tested during inspection. Outdoor temperatures should exceed 65 degrees F for at least 24-hours or the air conditioning equipment can be damaged by testing. I recommended having this system serviced and inspected prior to the next cooling season.
11.3.2 Cooling Systems and Heat Pumps
Cooling System: Air Conditioning Present
Data Plate: Shown here
Manufacturer: Bryant
Listed Nominal Capacity: 3 Tons
Energy Source: Electric
System Type: Air Source
Age: 2023
It's important to be aware of how long air conditioners last, so you don't get the unwelcome surprise of a broken air conditioner in the peak of the summer heat. In general, air conditioners that are properly maintained can last 15 to 20 years.
Info and LMT's. The air conditioning system and condensate control system could not be tested during inspection. Outdoor temperatures should exceed 65 degrees F for at least 24-hours or the air conditioning equipment can be damaged by testing. I recommended having this system serviced and inspected prior to the next cooling season.
11.4.1 Heating System
Heating System: Present
Data Plate: Shown Here
Last Service Record: None
Loction: Basement
Energy Source: Natural gas
Manufacturer: Bryant
Listed Max Capacity Per Data Plate: 80,000 btu's
Heating Method: Gas forced air furnace
Age: 2023
Metal Vents and Vent Connectors: Standard
The interior unit(s) were inspected visually and tested by ensuring they responded to normal operating controls (at the thermostat), and that conditioned air was produced. The unit(s) responded to normal operating controls and no indications of deficiencies were observed at the time of inspection, unless otherwise noted in this report.
Info and LMT's. The HVAC system inspection is restricted to assessing the system's response to normal operating controls, including the thermostat, in both heating and cooling modes (subject to weather conditions). It also involves visually observing the exterior and interior equipment non-invasively and removing any access panels designed for easy removal by homeowners without the need for tools. For a more comprehensive inspection, it's advisable to consult an HVAC contractor.
This house has a gas forced air furnace. A critical component to all combustion heating equipment is the heat exchanger. This is the welded metal assembly inside the furnace that contains the products of combustion so that moisture, carbon monoxide and other products of combustion do not mix with interior air and get safely vented to the exterior. Heat exchangers on modern furnaces have an average life expectancy of 15-20 years. Unfortunately, heat exchangers are concealed inside the heating equipment; they are not visible and specifically excluded from a home inspection. Cracks in heat exchangers may be concealed and can pose a potential safety hazard.
Although some furnaces can last more than 40 years (extremely rare), the average life of a furnace is around 15 to 30 years. As long as you have scheduled annual furnace maintenance, it should easily last over 15 years. Just like your car, your older furnace may need some basic repairs.
11.4.2 Heating System
Heating System: Present
Data Plate: Shown Here
Last Service Record: None
Loction: Closet
Energy Source: Natural gas
Manufacturer: Bryant
Listed Max Capacity Per Data Plate: 60,000 btu's
Heating Method: Gas forced air furnace
Age: 2024
Metal Vents and Vent Connectors: Standard
The interior unit(s) were inspected visually and tested by ensuring they responded to normal operating controls (at the thermostat), and that conditioned air was produced. The unit(s) responded to normal operating controls and no indications of deficiencies were observed at the time of inspection, unless otherwise noted in this report.
Info and LMT's. The HVAC system inspection is restricted to assessing the system's response to normal operating controls, including the thermostat, in both heating and cooling modes (subject to weather conditions). It also involves visually observing the exterior and interior equipment non-invasively and removing any access panels designed for easy removal by homeowners without the need for tools. For a more comprehensive inspection, it's advisable to consult an HVAC contractor.
This house has a gas forced air furnace. A critical component to all combustion heating equipment is the heat exchanger. This is the welded metal assembly inside the furnace that contains the products of combustion so that moisture, carbon monoxide and other products of combustion do not mix with interior air and get safely vented to the exterior. Heat exchangers on modern furnaces have an average life expectancy of 15-20 years. Unfortunately, heat exchangers are concealed inside the heating equipment; they are not visible and specifically excluded from a home inspection. Cracks in heat exchangers may be concealed and can pose a potential safety hazard.
Although some furnaces can last more than 40 years (extremely rare), the average life of a furnace is around 15 to 30 years. As long as you have scheduled annual furnace maintenance, it should easily last over 15 years. Just like your car, your older furnace may need some basic repairs.
11.5 Vents and Flues
Common Observations: Standard
Vents and flues were inspected looking for proper clearance, material and condition, slope and direction, support and stability, connection and joints, clearance to combustibles, vent termination and flue liners (if applicable). No reportable conditions were present at the time of inspection unless otherwise noted in this report.
11.6 Air Filters
Air Filter Size: 16 x 25 x 1
Common Notes: Filters Were Clean, Filters Are Located at Cold Air Returns, Be Sure to Change or Clean Quarterly
Filtration Systems: Disposable
11. 7 Heating and Cooling Distribution Systems
Distribution Method: Forced Air / Ducts
Heat Source in Each Room: Present
Info and LMT's. An infrared camera was utilized to demonstrate that the system(s) responded to normal operating controls during the inspection. However, these images are not intended to depict the precise temperature differential, efficiency, or performance of the system, as these aspects fall outside the scope of a home inspection. For accurate readings, HVAC thermometers (wet bulb) are necessary, and an HVAC contractor would conduct measurements at different locations.
In cooling mode, typical temperature differentials between return and supply air can range from 12 to 20 degrees, while in heating mode, they can range from 15 to 25 degrees. Numerous factors, including indoor and exterior ambient air temperatures, humidity levels, and the condition of the air filter and evaporator, among others, can influence these values.
11. 8 Mechanical Ventilation Systems
Whole House Fans, Ventilation and HRVs: Present
Bath Fan Ducting: Ducted to exterior
Kitchen Fan Ducting: Ducted to exterior
This building has a house ventilation fan timer. You typically want this set for at least two hours / day though this does depend on occupant behavior. The goal is to keep indoor relative humidity below 50% during cold weather.
11.9 Gas Fireplaces
Fireplace Types: Direct vent gas log fireplace
Fan Present: No
Mantle Present: Yes
Gas Rating Sticker Noted: No
Gas Shut off Noted: Yes
Screen Covering For Direct Vent: Yes
Battery Cradle: Not Applicable
System Responded to Testing: Yes
This gas log fireplace does not have a fan system installed. This is pretty normal, but if you wish to install a fan this will need to be added.
A mantle has been installed above the gas fireplace. Direct vent gas fireplaces are designed principally for their aesthetic value, but they also produce as much heat output as possible, within ANSI and UL standards for combustible temperatures. The allowable standard for combustibles is 117°F above room temperature. Since the average room temperature is 70-75°F, a 187-192°F surface temperature can be expected. On a solid surface, such as a mantel, 150°F is very hot to the touch. Monitor this gas log during use and be sure combustible materials do not exceed this temperature standard. This installation may need to be replaced or reconfigured for improved safety.
Note: Also note that each manufacturer may have different clearance requirements for mantles. We try and look this stuff up where feasible, but often specific installation requirements are not accessible and in general, verification of manufactories installation requirements is not possible as part of a visual and limited home inspection. If you have concerns the best is to consult with the installation instructions from the manufacturer. If these can be located will will always assist with looking this up.
The gas fireplace does not appear to be correctly labeled. Have this fireplace serviced and repaired to ensure it has the proper LP rated burner and it is correctly labeled.
11.10 Wood Burning/Solid Fuel Fireplaces
Fireplace Types: No wood burning fireplaces or appliances noted
11. 11 Additional Heat Sources
Description: None Noted
11.12 General Heating and Cooling Observations and Recommendations
There was an older and soon-to-be outdated refrigerant used in this unit.
Recommendations:
It is recommended to replace the current system, with a system that uses modern A2L refrigerant, due to changes coming in the law.
Follow this link for updates: R-410 Phase Out
The pad supporting the outdoor condensing unit is not level. Mechanical system requirements state that equipment and appliances supported from the ground shall be level and firmly supported on a concrete slab or other approved material extending not less than 3 inches (76 mm) above the adjoining ground. Such support shall be in accordance with the manufacturer's installation instructions.
Recommendations:
I recommend a licensed HVAC contractor or other qualified workman review the condition and make corrections.~ IRC - Mechanical Code: M1305.1.4.1
Minor damage was noted on the ductwork. While it does not appear to significantly impact functionality at this time, repairs are recommended to prevent potential energy loss or further deterioration.
Recommendations:
A qualified HVAC professional should be consulted for evaluation and repairs as needed.
During the inspection, a buildup of dust, debris, and potential contaminants was observed in the ductwork, which may impact indoor air quality and HVAC system efficiency.
Recommendations:
It is recommended that a professional duct cleaning service or HVAC specialist be consulted to thoroughly clean the ductwork and ensure optimal air circulation and system performance.
- Drywall dust was noted inside the air handler - this should be cleaned as part of a new construction servicing.
Ch. 12 Plumbing
12.1
Per the Standards of Practice, the home inspector shall observe at visible portions: Interior water supply and distribution system, including piping materials and supports; fixtures and faucets; functional flow; leaks; and cross-connections. Interior drain, waste, and vent system, including traps; drain and waste lines; leaks; and functional drainage. The home inspector shall describe Water supply and distribution piping materials; Drain, waste, and vent piping materials; and the Location of the main water supply shutoff device. The home inspector shall operate all plumbing fixtures, including their faucets and all exterior faucets attached to the house, except where the flow end of the faucet is connected to an appliance.
The home inspector is not required to: State the effectiveness of anti-siphon devices; Determine whether water supply and waste disposal systems are public or private; Operate automatic safety controls; Operate any valve except water closet flush valves, fixture faucets and hose faucets; Observe: Water conditioning systems; Fire and lawn sprinkler systems; On-site water supply quantity and quality; On-site waste disposal systems; Foundation irrigation systems; Spas, except as to functional flow and functional drainage; Swimming pools; Solar water heating equipment; or Observe the system for proper sizing, design, or use of proper materials.
12.3 Water Service Supply
Pipe Material: Copper
Water Supply: Public water
Pressure Reducing Valve: None noted
Water Pressure: 75 PSI
This shows the water pressure tested during inspection. Generally, "normal water pressure," should be between 30-80 PSI, though pressures near or below 30 can result in poor functional flow to fixtures. Water pressures in excess of 80 PSI risk damaging supply piping components and should be controlled with a pressure reducing valve.
12.4 Distribution Pipe
Supply Pipe Materials: PEX
Pipe Insulation: Not visible
Functional Flow: Average
Circulation Pump: None Noted
All supply piping components appeared to be in serviceable condition at the time of the inspection. Inspection typically includes evaluation of all visible supply and drain pipes, looking for leaks, improper installation, and other deficiencies. No reportable conditions were observed at the time of inspection unless otherwise noted in this report.
Info and LMT's. This building has PEX tubing used for supply piping. Crimp ring connections on PEX pipe have very specific installation guidelines and most of these connections will not be visible at the time of inspection (just like any other type of pipe fitting). It is beyond the scope of this inspection to evaluate a significant number of these connections.. Any leaking noted at fittings should result in more careful inspection of all of the plumbing system by a licensed plumber that is experienced in the installation of these types of connections
Info and LMT's. The sections of the plumbing system concealed by finishes and/or storage (below sinks, etc.), below the structure, or beneath the ground surface are not inspected. Overflow backup is not tested due to the possibility of damage from water leakage. This is necessary due to the fact that that aged gaskets may fail and leak.
12.5 Waste Pipe and Discharge
Discharge Type: Public Sewer - Buyer
Waste and Vent Pipe Materials: PVC
Location of Sewer Cleanout: Basement, Side Yard
A video camera sewer scope is recommended. An evaluation of the sewer line below the ground is beyond the scope of this inspection. Due to the age and location of the building, a sewer scope is recommended to further evaluate the sewer line and the below ground connections between the house and the municipal sewer line. Sewer scopes are done using video cameras and can reveal the materials, condition and reliability of the sewer line. If that has been done recently, I recommend having a sewer scope performed.
12.6 Additional Sinks
Tested
All sink components appeared to be in serviceable condition at the time of the inspection. Inspection of the sink typically includes evaluation of functional flow, functional drainage, proper operation of shut-off, diverter valves and faucet; and moisture intrusion under the sink. The visible portions of the sink plumbing was inspected by running water through the drain pipe for an extended period of time and looking for leaks from the drain pipe / trap assembly, water supply lines, and areas underneath of the sink area (ceiling below/basement/crawl space). Other significant defects are also looked for with the plumbing. No reportable conditions were observed at the time of inspection unless otherwise noted in this report.
12.7 Water Heater
Manufacturer: A.O.Smith
Data Plate: Shown Here
System Type: Tank
Energy Source: Gas
Size: 50 gal
Drain Pan: Present with drain
Straps : Not Needed
Pad: None Needed
Bollard: None Required
Age: 2024
Relief Valve: Present - Not Tested
Expansion Tank: Present
The water heater was inspected visually and tested by ensuring it responded to normal operating controls in a safe and functional manner. The unit(s) responded to normal operating controls and no indications of deficiencies were observed at the time of inspection, unless otherwise noted in this report.
Per the Standards of Practice, the inspector will examine and report the condition: of the water heater enclosure, plumbing supply, energy source, venting, and TPR valve, if applicable. The inspector is not required to: activate the system if it is powered down or the pilot flame is not lit, Inspect the system for proper sizing, design, or use of proper materials.
A hot water heater's lifespan depends on many factors, including the type of water heater, the energy source, the type of water you have, and how well the unit is maintained. On AVERAGE, most water heaters last between 8 and 12 years but some can last up to 20 years with regular maintenance.
A temperature and pressure relief valve (TPRV) is required on all water heaters to discharge any excessive pressure within the tank. A discharge pipe should be attached to the valve and directed to a safe location away from body contact. Newer installations must be directed to the building exterior or to an approved indoor drain receptor. Most manufacturers suggest that homeowners test these valves at least once a year by lifting the lever to ensure the valve discharges properly and also recommend inspection of these safety devices every three years. The picture here shows a typical TPRV. They may also be found on the side of the heater on some models. I do not test these valves due to the possibility that they may leak after testing. A leaking or inoperative TPRV should be replaced immediately by a licensed plumber.
Due to inconsistencies between both UPC and IPC Plumbing codes, and water heater manufacturer's instructions, and TPRV manufacturer instructions, it is not actually possible to install the drain from the Water Heater TPRV "properly." There are conflicts with distance of termination to the floor/ground, types of pipes approved, and diameters of pipes approved. Additional confusion is added when jurisdictional inspectors approve installations/materials specifically not allowed by both codes and manufacturers. My recommendations will vary depending on the installation and will be included in the applicable narratives below.
Most codes defer to manufacturer instructions and I favor those recommendations. The yellow tag on the valve states clearly the termination should be 6" above the floor which is more consistent with the UPC code requirements.
12.8 Water Temperature
Water Temperature Measured During Inspection: 125 Degrees F
12.9 Exterior Hose Bibs
Winterized - not tested
The exterior hose bibs were winterized at the time of inspection and could not be tested. Inquire with the seller to see if they are generally operable.
12.10 General Plumbing Observations and Recommendations
PEX plumbing was observed installed too close to the gas water heater. According to most manufacturer’s guidelines and UPC Code 604.11.2, PEX should be kept at least 18 inches away from the water heater’s exhaust vent to prevent heat-related damage.
Recommendations:
It is recommended to have a licensed plumber evaluate and properly reposition the PEX piping to meet safety standards.
The discharge tube for the water heater temperature and pressure relief valve (TPRV) is plumbed using a PEX tubing. Though this is very common, this restricts the diameter of the opening and is unsafe and not recommended - see attached link. Ideally, the discharge tube for a relief valve:
- Terminates to an exterior location or above a drain, though this is not always possible
- Terminates between 6 and 24-inches off the ground (UPC)
- Slopes to drain to prevent water pooling inside the discharge tube
- Is not made from pipe with an inside diameter less than 3/4 on an inch
- Terminates to a visible location that can be monitored for leaks and discharges
- Does not have a threaded termination point which would prevent accidental capping of this important discharge
- Does not terminate into a drain pan
Recommendations:
I recommend having this relief valve discharge tube further investigated and repaired as recommended by a licensed plumber.
Testing of the plumbing system today, the water tested as too hot 125 degrees F. This is a scald hazard. To prevent scalding, standards recommend indoor hot water temperatures do not exceed 120 degrees. There is some evidence that hot water temperatures should be greater than 130 degrees to prevent Legionnaires' disease from developing in the water heater. If this is a concern, you can heat the water in the tank to 140 degrees F and have a tempering valve installed at the hot water tank. Please note that during inspection it is difficult to accurately test the water temperature as it can vary between fixtures. Testing is done in multiple locations during inspection and a median temperature is taken.
Recommendations:
Have this further evaluated and repaired by a licensed plumber or simply turn down the temperature as desired to eliminate a scald hazard.
Ch. 13 Additional Plumbing
13.1 Sump Pumps and Drains
Sump Pumps: Present
Floor Drain: Basement Floor Drain Present, Cover /Screen Missing
Info and LMT's. This home inspection focuses on the visible components and operation of the sump pump system. It does not involve dismantling equipment or conducting invasive tests. The inspection covers general functionality, visible signs of wear, and operational testing, but does not account for potential hidden defects, long-term reliability, or future performance
Info and LMT's. A floor drain was noted in the basement. I do not test floor drains but I do recommend they be tested for function by the homeowner or a handy-person by running a hose in them for a prolonged time or having them professionally scoped by a qualified plumber. The traps in these drains sometimes dry-out allowing sewer gases and vermin into the home. As a part of routine maintenance I recommend making sure drain trap has water in it and is properly covered.
13.2 Radon Equipment
Not Present
13.4.1 Sewage Ejector Pumps
Location: Not Present
13.4.4 Irrigation
Not Present
13.5 Additional Plumbing Observations and Recommendations
Ch 14. Interior Living Area(s) and Bedrooms
14.1
Per the Standards of Practice, the home inspector shall observe walls, ceilings, and floors; steps, stairways, balconies, and railings; counters and a representative number of installed cabinets; and a representative number of doors and windows; fireplaces by examining the firebox, operating the damper, and reporting on the presence of a gas shut off valve. The home inspector shall: Operate a representative number of receptacles, switches, windows, and interior doors; and report on signs of abnormal or harmful water penetration into the building or signs of abnormal or harmful condensation on building components.
The home inspector is not required to observe: Paint, wallpaper, and other finish treatments on the interior walls, ceilings, and floors; Carpeting, tile; or Draperies, blinds, or other window treatments. Gas fireplaces are not tested for functionality, and the pilot light will not be lit if it's off at the time of inspection. An evaluation by a gas company is recommended before using any gas appliances in the home.
14.2 General Interior Pictures
Info and LMT's. Assessing the quality and condition of interior finishes involves a significant degree of subjectivity. Factors such as cleanliness, cosmetic imperfections, material quality, architectural aesthetics, and color fall outside the purview of this inspection. Comments provided will be general in nature, unless specific functional concerns are identified. It's important to note that furniture, area rugs, storage items, appliances, and wall hangings are not relocated during the inspection, which may obscure potential defects.
Items such as carpeting, window treatments, central vacuum systems, household appliances, screens, recreational amenities, paint, wallpaper, and other finish treatments are not inspected unless explicitly mentioned in the report. It is recommended to conduct a thorough review of interior areas during the final walk-through inspection before closing. Please note that only areas that were readily visible and accessible were inspected on the day of assessment.
14.4 Walls, Ceilings, Trim, Hallways and Closets
Wall and Ceiling Materials: Drywall, Wood
Visual inspection of the walls and ceilings typically includes examination for functional defects in the wall and ceiling coverings, window and door casings, baseboards and other installed moulding. No reportable conditions were visibly present at the time of inspection unless otherwise noted in this report.
14.5 Floors and Floor Materials
Floor Materials: Luxury Vinyl Plank (LVP), Carpet, Tile
Floor Settlement: None noted
Visible portions of the floors throughout the structure were inspected looking for significant deficiencies. No reportable conditions were visibly present at the time of inspection unless otherwise noted in this report.
Info and LMT's. At the time of the inspection, the majority of the flooring was covered due to ongoing construction and/or painting. As a result, a full evaluation of the flooring condition was not possible.
14.6 Interior Doors and Doorstops
Interior Doors: Hollow Core
A representative number of interior doors were inspected by operating them ensuring that they opened and closed properly, as well as latched properly without binding on jambs or the floor. No reportable conditions were present at the time of inspection unless otherwise noted in this report.
14.7 Windows
Window Glazing: Double pane
Interior Window Frame: Vinyl
Window Styles: Single hung, Casement, Sliding
A representative number of windows were inspected by operating them ensuring that they opened and closed properly, as well as latched properly without binding.No reportable conditions were present at the time of inspection unless otherwise noted in this report.
14.8 Wall Insulation, Air Bypass and Register Vents
Wall Insulation: Not Visible
14.9 Stairs and Railings
Completed
The interior stairs were inspected by evaluating the risers and treads, applicable railings, etc. No significant deficiencies were present at the time of inspection unless otherwise noted in this report.
14.10 Indoor Air Quality
Link to Indoor Air Quality
The following link can provide you with additional information regarding indoor air quality.
https://www.epa.gov/indoor-air-quality-iaq
14.11 General Interior Living Observations and Recommendations
The top edge of interior doors were found to be unfinished. Per most manufacturers' specifications, all surfaces of the door, including the top and bottom, should be properly sealed to prevent moisture absorption, which can lead to warping or swelling.
Recommendations:
It is recommended to have a qualified painter or contractor finish these areas to ensure the longevity of the doors.
Note:
Most doors are shipped without the top edge finishes and finishes are required to be completed on site.
Heres a link to help explain:
https://pdf.lowes.com
Caulking the inside of a window is crucial for maintaining a well-insulated, weatherproof, and aesthetically pleasing living or working environment. It contributes to the overall comfort, energy efficiency, and longevity of the building.
Recommendations:
Have areas around windows re-caulked by a qualified contractor.
Ch. 15 Kitchen
15.1
Per the Standards of Practice, the inspector will examine and report on the condition and operation of the dishwasher by initiating a cycle, the range by testing the heating elements and the oven, the mounted microwave by starting a warm-up cycle, test the hot/cold water supply at the fixture, look for leaks in the plumbing and fixtures/faucet, examine counters, walls, ceilings, floors, a representative number of cabinets, windows, doors, and the presence of GFCI receptacles and their operation, if applicable. Homes built prior to 1987 were not required to have GFCI receptacles in the kitchen, but upgrading is recommended for safety.
The home inspector is not required to report on: Clocks, timers, self-cleaning oven functions, thermostats for calibration or automatic operation; Non-built-in appliances; or Refrigeration units. The home inspector is not required to operate: Appliances in use; or Any appliance that is shut down or otherwise inoperable.
15.2 General Kitchen Pictures
15.3 Sinks and Faucets
Tested
All Kitchen sink components appeared to be in serviceable condition at the time of the inspection. Inspection of the area typically includes evaluation of functional flow, functional drainage, proper operation of shut-off, diverter valves and faucet; and The supply and drain pipes were inspected looking for leaks, improper installation, and other deficiencies. No reportable conditions were observed at the time of inspection unless otherwise noted in this report.
15.4 Cabinets and Countertops
Countertop Material: Granite
Cabinet Material: Wood
This is a great document From the Natural Stone Institute that covers maintenance and installation recommendations for slab surface stone countertops.
The kitchen and bathroom cabinetry and countertops, and any other cabinets and countertops were inspected looking for significant damage and by testing a representative number of doors and drawers evaluating their operation. No reportable conditions were present at the time of inspection unless otherwise noted in this report.
15.5 Disposers
Not operated
Info and LMT's. The disposal switch could not be located and, therefore, was not tested. It is recommended to confirm its presence and functionality during the final walkthrough.
15.6 Dishwasher
Present
The dishwasher was operated by running a rinse cycle and was functional at the time of inspection. No leaks or water was present at the unit's base at the cycle's completion. The unit's efficiency of cleaning dishes is not tested. No deficiencies were observed with the unit unless otherwise noted in this report.
15.7 Ranges, Ovens and Cooktops
Gas and electric
15.8 Refrigerators
Present
The refrigerator was tested during inspection and was operable. Appliances are generally beyond the scope of a home inspection, but are tested for basic function as a courtesy. I use these images just to show the system was generally functioning during inspection. No reportable deficiencies visible on the day of in inspection.These are representative photos.
Info and LMT's. Refrigerators are examined as a courtesy during a Home Inspection, as they are regarded as transient or "unattached" items. However, they are not relocated to inspect the condition of the flooring beneath them or the surrounding cabinetry. Consequently, the visibility of their water line and power receptacle is limited and excluded from this inspection. If any concerns arise regarding the refrigerator, it is advisable to arrange for an evaluation by an appliance repair company or another qualified professional before proceeding with the closing.
15.9 Ventilation Method
Present
15.10 General Appliances
General Testing Note
Info and LMT's. Appliances are checked for general functionality by turning them on for a short period of time using basic operating modes. Thermostats, timers, clocks, self-cleaning features and other specialized functions are not tested during this inspection. Appliances are not inspected for cosmetic flaws, performance or the ability/accuracy of heating, cooling, etc. They are not inspected to ascertain whether the proper racks and/or accessories are present or in working order. Laundry appliances (and other portable appliances) are not moved and are outside the scope of this inspection; any comments are included for information purposes only. Water supply valves are not operated for liability reasons. It is further recommended that appliances be operated once again during the final walk through inspection prior to closing. Finally, product recalls and consumer product safety alerts occur almost daily. To best address your specific concerns, visit www.cpsc.gov or www.recalls.gov. Items, brand names, and model numbers will be required for proper identification.You may also find some general information or listed recalls on appliances by visiting the following link: https://www.building-center.org/
Info and LMT's. Except for the microwave, kitchen appliances were tested during inspection today. The typical design life of appliances can range from 4-20 years. Some appliances such as an older electric range are simple and tend to last longer than more complex appliances such as dishwashers and refrigerators or modern appliances with circuit boards. It is impossible to predict the useful remaining life of an appliance. I ran appliances during inspection. Any defects noted will be listed in this report. There are companies that offer warranties for appliances such as AHS Home Shield. While I do not endorse or recommend any specific warranty. I know that some home owners have been very happy with this insurance. For your convenience, I have attached a link to a web site of one such warranty product. LINK
Ch. 16 Laundry Facilities
16.1
Per the Standards of Practice, the inspector will examine and report on the condition of the exposed plumbing, the presence of a 240-volt receptacle, GFCI receptacles, dryer vent condition, and termination, as well as the walls, floors, ceilings, doors, cabinets, counters, and windows, if applicable.
The inspector is not required to: Inspect or move washers and dryers, operate water valves where the flow end of the faucet is connected to an appliance, or Inspect the plumbing for proper sizing, design, or use of proper materials.
16.2 Laundry Pictures
16.3 Washer
Washer: Not included
The clothes washer is apparently not included with the sale of the house. I recommend verifying this and budget accordingly.
16.4 Dryer
Dryer: Not included
Power Source: Electric
Exhaust Duct: Ducted to Exterior
The clothes dryer is apparently not included with the sale of the house. I recommend verifying this and budget accordingly.
Proper dryer exhaust venting is critical for safe and reliable performance from the dryer. Here are some basic rules of thumb for dryer exhaust duct installation: Unless a vent-free appliance is being used, the dryer exhaust vent must terminate outdoors. It should be no more than 25 feet long and for every 90 degree turn subtract 5 feet and for every 45 degree bend subtract 2.5 feet. Use only smooth-wall metal vent pipe @ 4 inch pipe diameter. Do not use plastic pipe and plastic flex pipe. If a flexible connector is needed behind the dryer use a short amount of corrugated metal pipe. If the exhaust duct is getting pinched behind dryer, consider use of a dryer vent box, pictured here. Flex and corrugated pipes should never be used in concealed spaces such as through walls or in attic or crawl spaces. Insulate dryer exhaust duct where it passes through unconditioned spaces to prevent condensation that could hasten lint build-up inside the pipe. Do not use screws to connect pipe as these can trap lint. Secure duct with foil tape as needed. Be sure duct is sleeved properly so that it will not trap lint and clean the vent regularly, especially if it is a long exhaust run.
16. 5 Laundry Ventilation
Type: None noted
16.6 Laundry Cabinets
Present
16.7 Laundry Chute
None Noted
16.8 General Laundry Observations and Recommendations
No drain pan was observed beneath the second-floor washing machine. A drain pan with a discharge line is typically required when installed above a finished space to help prevent water damage.
Recommendations:
It is recommended to have a licensed plumber evaluate and install a proper drain pan as needed.
Ch. 17 Bathroom(s)
17.1
Per the Standards of Practice, the inspector will examine and report the condition of the: sinks, showers, tubs, enclosures, toilets, exposed plumbing, and the presence of leaks from plumbing, fixtures, and/or faucets. As well as the walls, floors, ceilings, a representative number of windows and doors, heating/cooling source, ventilation, and presence of GFCI protection, if applicable. GFCI protection in bathrooms was not required in homes built prior to 1975, but upgrading is recommended for safety.
The home inspector is not required to: Operate any valve except water closet flush valves, fixture faucets, and hose faucets; or Inspect the system for proper sizing, design, or use of proper materials.
17.2 General Bathroom Pictures
17.3 Sinks and Cabinets
Tested
All sink components appeared to be in serviceable condition at the time of the inspection. Inspection of the sink typically includes evaluation of functional flow, functional drainage, proper operation of shut-off, diverter valves and faucet; and moisture intrusion under the sink. The visible portions of the sink plumbing was inspected by running water through the drain pipe for an extended period of time and looking for leaks from the drain pipe / trap assembly, water supply lines, and areas underneath of the sink area (ceiling below/basement/crawl space). Other significant defects are also looked for with the plumbing. No reportable conditions were observed at the time of inspection unless otherwise noted in this report.
The visible portions of the sink plumbing was inspected by running water through the drain pipe for over one minute and looking for leaks from the drain pipe/trap assembly, water supply lines, and areas underneath the sink area (ceiling below/basement/crawl space). Other significant defects are also looked for with the plumbing. No reportable conditions were observed at the time of inspection unless otherwise noted in this report.
17.4 Toilet
Tested
Info and LMT's. Toilets are not assessed for their attachment to the closet flange or anchor bolts during the inspection. This is because manipulating or pushing on a toilet can compromise the wax seal, potentially leading to leaks. Therefore, the securing of toilets is not included in this inspection.
17.5 Bathtub / Shower / Bathtub Walls and Enclosures
Tested
The shower enclosure and door was inspected by running water in the shower for a few minutes and looking for visible signs of leaks. Lived in conditions can not be replicated during an inspection and if leaks are noticed after taking possession the door tracks will need to be sealed as needed to rectify any leaking. No reportable conditions were present unless otherwise noted in this report.
Info and LMT's. Water was allowed to flow through the drains of tubs and showers for an extended duration, followed by an inspection of the areas beneath these drains (if applicable) using thermal imaging to detect any signs of leaks. No leaks were detected during the inspection unless specifically mentioned in this report.
It's important to note that the effects of weight applied to these drains cannot be replicated during the inspection. When individuals shower or bathe, the weight can exert pressure on gaskets or joints in the drain pipes, potentially leading to leaks. This risk may be heightened in homes that have been unoccupied for an extended period. Therefore, any leaks occurring from these areas after the inspection are not covered.
Info and LMT's. Tub and sink overflows are not assessed for functionality during testing, as there is a high probability that the gaskets may leak. Therefore, it is advisable to be cautious when filling tubs to prevent water from entering the overflow. While these overflows typically help drain away excess water, some degree of leakage should be expected. To address this issue, it is recommended to have a licensed plumber inspect the gaskets and perform any necessary repairs. It should be assumed that these overflows may not be completely watertight.
17.6 Bathroom Ventilation
Type: Bath fan
The lifespan of a bathroom fan, also known as an exhaust fan, can vary depending on several factors, including the quality of the fan, the frequency of use, and the level of maintenance and care. In general, a well-maintained bathroom fan can last anywhere from 10 to 15 years, although some fans may last longer or shorter depending on their specific features and usage.
17.7 General Bath Condition
Testing Procedure Note
Info and LMT's. During inspection today I operated all plumbing fixtures in bathrooms. I ran a moisture meter around toilets and tile shower enclosures to check for concealed leaks and sounded for loose tile and finishes in shower and tub enclosures. I do not test bathtub overflow drains as this risks damaging finishes around the tub. Monitor tubs while filling and avoid pushing water into the overflow. Even well-installed overflow drains can leak as the gaskets that seal the overflow will dry out over time and may no longer provide a watertight seal. Monitor plumbing after moving into a new home as testing during inspection presents less stress on plumbing than daily use. Please note that vacant homes present additional risk as it can be difficult to distinguish how the plumbing system will respond to daily use. Any defects uncovered during inspection are listed in this report.
17.8 General Bath Observations and Recommendations
All the toilet(s) have not been caulked to the floor. Caulking the toilet to the floor is recommended and even required though opinions on this can vary. The biggest risk of not caulking the toilet to the floor is that the toilet can become loose.
Recommendations:
Repair as recommended by a licensed plumber.
Ch. 18 Attic, Roof Structure and Ventilation
18.1
Per the Standards of Practice, the inspector will examine: the attic area and report on the condition of the access opening (including location), insulation type (and current depth), ducts, visible electrical components, exhaust terminations, plumbing components, and ventilation if applicable.
The inspector is not required to: move or disturb insulation, report on the adequacy of current ventilation, or Calculate the strength, adequacy, or efficiency of any system or component, including framing. Enter any attic that may damage the property or its components or be dangerous to or adversely affect the health or safety of the home inspector or other persons. Therefore, I do not attempt to enter attics with less than 36" of headroom, where insulation obscures the ceiling joists, or where ducts block access. In these cases, I will evaluate from the access opening as best I can.
18.2 General Attic Pictures
Info and LMT's. It is recommended to inspect all attic spaces at least twice annually to ensure that ventilation openings remain unobstructed and to prevent the development of mold. While there may be minimal or no visible evidence of organic growth during the inspection, mold can proliferate rapidly under favorable conditions. Organic growth poses potential hazards and can spread when moisture accumulates in the attic and is not properly vented to the exterior. Any areas of concern should be examined by a qualified contractor for analysis and appropriate removal measures.
Info and LMT's. Every effort is made to access and navigate all attics safely and thoroughly. Details regarding the inspection method used, including the approximate percentages of the attic that were both physically and visually accessible, will be provided, along with any safety concerns or obstacles that may have limited the inspection.
The method of inspection is determined solely by the inspector and is influenced by various factors, including accessibility, clearance, insulation levels, stored items, temperature, and more. It's important to note that the inspection is confined to visible areas only, and any sections that were not visually accessible are not included in the assessment.
It's essential to recognize that hidden damage may exist, as no attic can be entirely evaluated due to physical and visible obstructions such as insulation, which is not disturbed during the inspection for visual access to items.
18.3 Attic Access
Hatch Location: Bedroom, Closet
Method Of Inspection: Crawled partial
Percentage of Attic that could be Safely Traversed: 70%
18.4 Roof Framing and Sheathing
Rafters: Truss
Sheathing: Plywood
18.6 Attic Insulation
Attic Insulation Type: Fiberglass
Insulation Depth: 14
Approximate Insulation R-Value on Attic Floor: 38
Approximate Insulation R-Value on Attic Ceiling: Not needed
Approximate Insulation R-Value on Attic Walls: Not visible
The insulation was inspected to determine the approximate depth and type. Current energy star standards recommend between 10-17 inches of insulation (dependent upon type) to achieve an R-38 rating. Depending on when the home was constructed, anywhere from 6 - 14 inches may be present. No reportable deficiencies were observed with the insulation unless otherwise noted in this report.
18.7 Attic Fan Exhaust Vents
18.8 Attic and Roof Cavity Ventilation
Attic Ventilation ethod: Soffit vents, Ridge vents, Gable vents
Attic and roof cavity ventilation is a frequently misunderstood element of residential construction. All roof cavities are required to have ventilation. The general default standard is 1 to 150 of the attic area and ideally, this comes from at least 60% lower roof cavity ventilation and 40% upper, but this is a wild over-simplifications of the subject. As a good guiding principle the most important elements for healthy attic spaces, which are traditionally insulated and ventilated are:
Make sure the ceiling between the living space and the attic is airtight
Ventilate consistently across the whole lower part of the roof cavity with low, intake soffit venting
Upper roof cavity venting is less important and if over-installed can exacerbate air migration into the attic from the living space.
Avoid power ventilators which can depressurize the attic and exacerbate air migration from the house into the attic.
For more information, please see: Link
18.9 General Attic, Roof Structure and Ventilation Observations and Recommendations
The attic and roof cavity ventilation look to be non-standard. Proper attic ventilation is important for the roofing materials to perform as intended and to reduce chances for condensation problems and heat build-up in the attic. The problem here is the use of ridge vents and gable vents. Most ridge vent manufacturers recommend ridge and soffit vents only to get convective ventilation across the roof decking; the gable wall vents can disrupt this convective air flow. No evidence of problems from this configuration was noted to date and depending on occupant behavior this may not ever cause a problem.
Recommendations:
If you wish to correct, consult with a qualified general contractor about blocking off existing gable vents.
Note:
No red flags were observed on the day of inspection.
Ch. 19 Foundation, Structure and Basement
19.1
Per the Standards of practice, the inspector will examine and report on the condition of the foundation walls, the framing (including probing of any framing that looks to have damage/deterioration), columns/piers, and insulation if applicable.
The inspector is not required to: enter any area that could be considered a safety hazard to the inspector; report on the adequacy of structural components; or report on spacing, span, or size of structural components. Ductwork, framing, plumbing, and insulation may block the visual accessibility of some areas. The inspection is limited to the conditions on the inspection day; I inspect several items looking for indications that moisture has infiltrated the foundation area. But, I can not guarantee that water will not infiltrate the area at a future time due to conditions unforeseen at the time of inspection.
19.2 Foundation
Building Configuration: Basement
Foundation Description: Poured concrete
Estimated Percentage of Visible Foundation: 30%
Evidence of Seismic Protection: Not visible
Visible portions of the foundation walls were inspected looking for significant cracking, moisture intrusion, or any other indications of damage or significant deficiencies. No reportable conditions were observed at the time of inspection unless otherwise noted in this report.
Info and LMT's. A representative sample of the visible structural components were inspected. Full inspection of all structural components (posts/girders, foundation walls, sub flooring, and/or framing) is not possible in areas/rooms where there are finished walls, ceilings and floors. Engineering or architectural services such as calculation of structural capacities, adequacy, or integrity are not part of a home inspection.
Info and LMT's. The inspection included an assessment of areas below ground level for any signs of past or present water intrusion. This involved examining visible sections of the foundation walls, floors, and/or soil for evidence such as moisture stains or other indicators of current or previous water penetration. No signs of water or moisture intrusion were observed in the visible areas below ground level, unless otherwise specified in this report.
It's important to note that only conditions observed at the time of inspection can be reported. However, it cannot be guaranteed that water will not infiltrate these areas in the future, particularly during heavy rainfall or due to changes in environmental conditions. There have been instances where homes showed no signs of water intrusion during inspection, but later experienced infiltration following a rainfall event.
The inspection of the poured concrete foundation is non-invasive and visual in nature. While we assess visible areas for cracks, moisture, and apparent defects, underlying conditions, such as hidden cracks or structural concerns within the concrete, may not be fully determined without destructive testing or specialized equipment
Info and LMT's. The footing that the foundation sits on is not fully visible at the time of inspection.
Info and LMT's. Snow cover limited the scope of this inspection. I was unable to see the roof and exposed flatwork such as the patio and driveway.
19.3 Floor, Wall and Ceiling Framing
Wall Framing: Partially Visible, 2x4
Wall Sheathing: Not visible
Floor Framing: Partly visible, 2x12
Sub-Floor Material: Partly visible, Plywood
Ceiling Framing: Not visible
Floor, Wall and Ceiling Framing Visual Obstructions:: HVAC Ductwork
Visible and accessible portions of the structure were inspected looking for damage or other significant deficiencies. No reportable conditions were visibly present at the time of inspection unless otherwise noted in this report.
Info and LMT's. Portions of the framing, wall sheathing and subfloor were not visible due to the referenced obstructions above. The possibility of reportable deficiencies exists in areas that were not visible/accessible.
The general home inspection does not include evaluation of structural components hidden behind finishing materials, but is visual and non-invasive only.
19.4 Basement
Description: Full
Info and LMT's. A typical home inspection of a basement is primarily visual in nature due to practical limitations. Home inspectors visually examine the basement to evaluate its overall condition, identify visible issues such as water damage, structural concerns, or safety hazards. They rely on observable elements without employing invasive techniques, as accessing hidden areas may necessitate destructive actions.
Although a visual inspection offers valuable insights, it's crucial to acknowledge its inherent limitations. Considering additional assessments may be necessary to gain a comprehensive understanding of the basement's condition.
19.5 Basement Slab
Concrete
Completed Visible portions of the concrete slab was inspected looking for significant deficiencies and/or significant cracking. No reportable conditions were present at the time of inspection unless otherwise noted in this report.
Any references to cracks on basement or garage concrete slabs will need to be sealed with an appropriate material by a qualified person at a minimum, regardless of the cracks size. This will prevent the possibility of moisture/water infiltration rising through the crack(s) during periods of heavy rainfall.
19.6 Basement Moisture
None noted
No leaks were observed during the course of the inspection. Although no active moisture penetration was noted, it is advised that you always monitor this area and as good practice consider any basement as wet until experience proves it dry.
19.7 General Structure and Basement Observations and Recommendations
Small vertical cracks were observed in the foundation wall. While these are often considered normal settling cracks, it is recommended to monitor them for any signs of widening or moisture infiltration.
Recommendations:
If further concerns arise, a foundation specialist should be consulted for evaluation.
This more than likely occurred when the concrete was poured
Minor cracks were observed in the basement slab. While these do not appear to pose an immediate structural concern, it is recommended to monitor the cracks for any significant widening or moisture intrusion.
Recommendations:
If further concerns arise, a foundation specialist should be consulted for evaluation.
Ch. 20 Crawl Space
20.1 General Crawl Space
Crawl Space: None Noted
Ch. 21 Cracking, Settlement and Movement
21.1
Note
Exterior Hardscapes & Flatwork: None Present on the Day of Inspection
Exterior Walls: None Present on the Day of Inspection
Interior Area(s): None Present on the Day of Inspection
Foundation Walls: Present
Slabs: Present
This section of the report will address concerns and deficiencies related to cracking, settlement, or movement. The inspection covered visible areas of the exterior, interior, and foundation, with particular attention to identifying cracks and signs of movement or settlement. The assessment of cracking acceptability depends on the client's preferences and exceeds the scope of a standard home inspection and any associated repairs are at the discretion of the client. No visible indications of these conditions were observed during the inspection, unless otherwise specified in this report.
The foundation walls underwent inspection for cracking, settlement, and movement at visible portions, and any such conditions observed are documented in this report if visibly present.
Assessing the acceptability of foundation cracks, settlement, and movement goes beyond the scope of a home inspection. Determining the cause, recent activity, and severity of such conditions requires invasive inspections, quantitative measurements, and discussions with the seller(s) regarding its history.
It's crucial to recognize the challenge of assessing recent activity in cracking during a home inspection. It's difficult to determine whether a crack has been present for years with no ongoing movement or if it is still active. Most structural engineers recommend monitoring the area for further movement over time.
Consulting with the seller(s) about any cracking activity and arranging for an evaluation by a foundation contractor or structural engineer is recommended. Foundation contractors can provide repair quotes for any crack, regardless of severity. If you wish to have cracks repaired or ensure no further movement occurs (stabilization), obtaining quotes from a foundation contractor before the end of your inspection contingency period is advisable.
Any references to cracks on foundation walls below grade should be sealed at least by a qualified person to prevent the possibility of moisture/water infiltration, regardless of the crack's size.
Some degree of foundation wall cracking, settlement, or movement was observed at this property.
Foundation wall conditions are documented based on their presence and visual appearance as observed at the time of inspection. They are categorized as within normal tolerances, borderline, or outside of normal tolerances according to their appearance during the inspection:
"Within Normal Tolerances" conditions have a crack width of less than 1/8", show no lateral displacement, and/or exhibit no tapering of the crack width.
"Borderline" conditions have a crack width greater than 1/8", some degree of lateral displacement, or tapering crack widths.
"Outside of Normal Tolerances" conditions have a crack width of 1/4" or greater, visible lateral displacement, or other characteristics typically indicating the need for repairs or stabilization.
The garage and basement slabs (where applicable) were inspected for cracking and signs of movement and settlement. The acceptability of any cracking is subject to the client's discretion and exceeds the scope of a home inspection. Cracks are categorized as minor, moderate, or significant based on their appearance at the time of inspection, and decisions regarding associated repairs are left to the client.
Cracking, regardless of severity, typically results from underlying conditions such as improper preparation of the slab's support, improper concrete mixtures, soil erosion beneath the slab, or inadequate relief, control, and expansion joints. It's important to note that cracking may worsen if left unaddressed. Therefore, it is recommended that an evaluation and any necessary repairs to the mentioned cracks be conducted by a qualified contractor.
Ch. 22 Thermal Imaging
22.1 Thermal Images
An infrared camera was utilized selectively to address specific areas of concern or to validate suspected issues, and its utilization should not be misconstrued as a comprehensive thermal assessment of the entire structure. Its deployment was at my discretion to furnish as much insight as possible, acknowledging that its application exceeds the standard scope of a home inspection. A comprehensive thermal assessment of the property is available as an optional service, subject to additional terms and fees outlined in a separate agreement.
Temperature readings depicted on thermal images within this report are provided as a gesture of goodwill and should not be solely relied upon, given that a home inspection focuses on qualitative rather than quantitative assessments. These readings may deviate by up to +/- 2% or more from the displayed values. Furthermore, they may indicate surface temperatures, necessitating air temperature readings for certain elements, which falls beyond the purview of a standard home inspection.
Ch. 23 Environmental Information
23.1 Moisture, Water Penetration and Active Leaks
None noted at the time of inspection
I inspected all around the basement, perimeter and attic for signs of moisture and / or moisture control problems. No water stains, or damaged baseboard were noted and no signs of paint touch up near the floor. Basement did not smell musty at the time of inspection and seems to be performing well to date. These findings can only be verified per date and time of inspection. Any findings after said inspection would require further evaluation and recommendations.
23.2 Mold and Bio-Growth
Please note that, mold testing and indoor air quality are beyond the scope of this inspection. If you are concerned about bio-growth or indoor quality, I recommend additional inspection by a specialist. As a general rule, localized problems can often be easily repaired by removing or sealing the localized area that got wet. Best practices to control bio-growth in buildings are to spend limited resources diagnosing and repairing water problems. Where water problems are chronic, bio-growth problems can be more complex and expensive to correct. Where water problems are localized, mold repairs tend to be more limited in scope and less complex.
23.3 Pest/Insects/Wildlife Concerns: WDI- Termite Informations/Exclusions
Examining and reporting on the existence of wood destroying organisms (WDI) such as termites, powder post beetles, carpenter ants, carpenter bees, etc., falls outside the parameters of a standard home inspection. This is explicitly excluded by the Standards of Practice and is therefore not covered in this inspection. It is strongly advised that you arrange for a WDI-Termite inspection before the conclusion of your inspection contingency period. Any remarks regarding such activity in this report are provided as a courtesy and should not be considered exhaustive. Further assessment by a licensed pest control company is recommended.
Ch. 24. Checking Out Procedure
24.1 Check Out List
Heating and Cooling:Restored to Pre-inspection temperatures
Oven:Off
Appliances:Off / finishing cycle
GFCI Reset: Reset
Lights:Crew on site
Keys and Lockbox:Crew on site
All accessible GFCI outlets were tested during the inspection. Each outlet was reset to its operational state before leaving the property.
24.2 Verbal Consultation
In person
24.3 One Year Follow Up
Once you approach the one-year mark of the purchase of your new home. A one-year inspection is a proactive measure to ensure the continued well-being of your property and identify any potential issues that may have arisen since the initial assessment.
If you wish to have this completed, please contact me for details at: 1-614-296-3721 or schedule online at olonzoinspections.godaddysites.com
Receipt -- 📃 The Complete Inspection Report
123 ABC Street Some City, OH. 43064
Home Inspection | $475.00 |
Radon | $175.00 |
$650.00 | |
PAID |
Olonzo Inspections
237 Olde Mound ln
Pickerington, Ohio 43147
(614) 296-3721
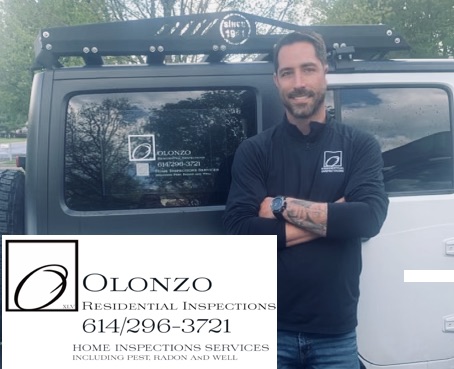