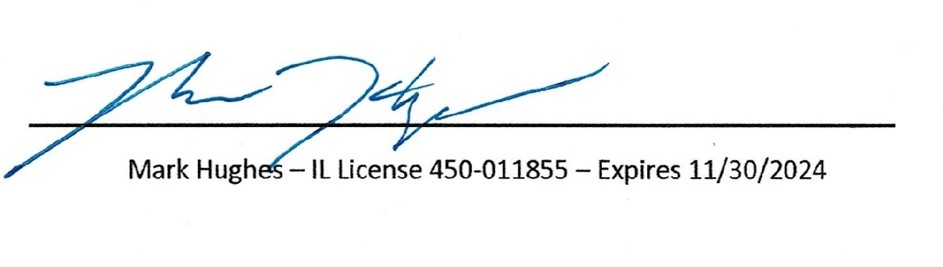
Mark Hughes, License #451.011855
The Scope and Purpose of a Property Condition Assessment
Basis and Limitations of Inspection
This inspection is a visual examination of the interior and exterior common elements that would be the responsibility of the Condominium Association. The inspection is being performed to determine the condition of these elements and the anticipated work and that may be needed immediately and in the future. The findings will attempt to provide guidance on maintenance and construction work that is needed on the structure.
The inspection is visual and not destructive
The descriptions and observations in this report are based on a visual inspection of the structure. We inspect the aspects of the structure that can be viewed without dismantling, damaging or disfiguring the structure and without moving objects. Areas that are concealed, hidden or inaccessible to view cannot be examined and the inspector can always return to gather more information if obstructions are removed at some point in the future.
This is not an inspection for code compliance
This inspection and report are not intended for city / local code compliance. During the construction process structures are inspected for code compliance by municipal inspectors. Framing is open at this time and conditions can be fully viewed. Framing is not open during inspections of finished structures, and this limits the inspection. All structures fall out of code compliance shortly after they are built, as the codes continually change. National codes are augmented at least every three years for all of the varying disciplines. Municipalities can choose to adopt and phase in sections of the codes on their own timetables. There are generally no requirements to bring older structures into compliance unless substantial renovation is being done.
This is just our opinion
Construction techniques and standards vary. There is no one way to build a structure or install systems in a structure. The observations in this report are the opinions of the inspector. Other inspectors and contractors are likely to have some differing opinions. You are welcome to seek opinions from other professionals, however, make sure they can clearly explain the purpose behind their actions and any industry based standards that they may be using as guides for their work.
Your expectations and participation in the solution
The overall goal of this inspection is to identify the critical elements that need to be addressed in the structure. The near and long term maintenance and restoration items will be identified and prioritize.
How to Read This Report
Getting the Information to You
This report is designed to deliver important and technical information in a way that is easy for anyone to access and understand. If you are in a hurry, you can take a quick look at our "Summary Page” and quickly get critical information for important decision making. However, we strongly recommend that you take the time to read the full Report, which includes digital photographs, captions, diagrams, descriptions, videos and hot links to additional information.
The best way to get the layers of information that are presented in this report is to read your report online (the HTML version), which will allow you to expand your learning about your house. You will notice some words or series of words highlighted in blue and underlined – clicking on these will provide you with a link to additional information. The HTML version of this report also contains streaming videos. Short video clips often contain important information and critical context and sounds that can be difficult to capture in words and still pictures.
For the most reliable viewing experience, I recommend viewing the report on as large a screen as practical, as much detail can be lost on small devices like smart phones. For similar reasons, reports should only be printed in color to retain as much detail as possible and minimize misinterpretation of photographs.
This report can also be printed on paper or to a PDF document.
Chapters and Sections
This report is divided into chapters that parcel the structure into logical inspection components. Each chapter is broken into sections that relate to a specific system or component of the structure. You can navigate between chapters with the click of a button on the left side margin.
Most sections will contain some descriptive information done in black font. Observation narrative, done in colored boxes, will be included if a system or component is found to be significantly deficient in some way or if we wish to provide helpful additional information about the system or the scope of our inspection. If a system or component of the home was deemed to be in satisfactory or serviceable condition, there may be no narrative observation comments in that section and it may simply say “tested,” or “inspected.”
Observation Labels
All narrative observations are colored, numbered and labeled to help you find, refer to, and understand the severity of the observation. Observation colors and labels used in this report are:
- Major Concern:Repair items that may cost significant money to correct now or in the near future, or items that require immediate attention to prevent additional damage or eliminate safety hazards.
- Repair:Repair and maintenance items noted during inspection. Please note that some repair items can be expensive to correct such as re-finishing hardwood floors, but are considered simply repair items due to their cosmetic nature.
- Recommended Maintenance:These are repair items that should be considered "routine home ownership items," such as servicing the furnace, cleaning the gutters or changing the air filters in the furnace.
- Improve:Observations that are not necessarily defects, but which could be improved for safety, efficiency, or reliability reasons.
- Due Diligence:Observation such as a buried oil tank that may require further investigation to determine the severity and / or urgency of repair.
- Future Project:A repair that may be deferred for some time but should be on the radar for repair or replacement in the near future.
- Description:Detailed description of various aspects of the property noted during the inspection.
Summary
Major Concerns
- EWGCE-6 EXTERIOR WALLS< GROUNDS, CHIMNEYS. ETC:
Some of the lintels are rusting at the windows. Recommend properly sealing the metal to help prevent additional damage.
- EWGCE-10 EXTERIOR WALLS< GROUNDS, CHIMNEYS. ETC:
Numerous repairs are needed to the decking systems on this building to ensure safe and reliable performance. Some of these repairs can be made, while other issues may be difficult to fully correct until the deck is rebuilt. I recommend additional inspection and repair of these decks by a qualified general contractor. Options include a full re-building or implementing repairs as are feasible to safely prolong the useful life of the deck.
Note: The dryer exhaust dampers and furnace exhaust piping needs to be removed from ledge board and under the decking. These two items are contributing to the deleterious and corrosive conditions of the deck structure.
Repair cost per contractors bid $94,550.00, Replacement cost per contractor bid $131,150.00
Examples of observations and defects noted during inspection include:
Ledger Board
- Incorrect Bolting: The ledger board is not correctly bolted - see attached information in the DCA-6 for proper ledger bolting
- Hangers Corroded: The metal hangers used to connect the floor joists to the ledger board are corroded and require replacement
- Corrode ledge fasteners: Corroded ledger board fasteners were noted - this can lead to detachment and potential deck collapse issue.
- Hanger Fasteners are Incomplete: The metal hangers used to connect the floor joists to the ledger board are missing proper fasteners - all round holes in the hangers should have a nail
- Ledger Flashings Missing: The ledger board is missing proper proper flashings - this can lead to moisture control problems and even deck failure
- Lateral Load Connectors Missing: The ledger board is missing recommended lateral load connectors, these are now required
- Ledger Board is Improperly Notch / Cut
Guards
- Wood Decay in Guardrail Posts: Rotted wood noted on the guardrail posts. This can weaken the guardrail system presenting a possible safety hazard.
- Guardrail is Loose: The guardrail is loose and may not adequately withstand the force of a falling adult presenting a possible safety hazard.
Decking
- Slippery Decking: The decking is currently presenting a slippery walking surface. This is a safety hazard. Clean and stain the decking for improved safety and to better preserve the wood.
Floor Structure
- Positive Connections Missing: The floor frame is lacking proper positive connections between posts and beams. Deck framing connections should be made with reliable connectors designed to resist failure.
Posts and Footings
- Cracked Post: The support post have advanced cracking. This can weaken the deck structure and present a possible safety issue.
- Piers At Grade: The deck footing system appears to be done at grade. Standards call for deck footings to be at least 12 inches below grade and resting on well-compacted soils. This recommended is designed to resist deck settlement.
Stairs
- Stringers Lacking Positive Attachment: The stair stringers have not been properly attached to the landing
Positive Connections
- The post to beam connections are missing proper positive connections - metal connectors that reliably attach the post to the beam.
- The brackets that connect the base of the posts to the footings are significantly corroded and may require replacement
- RCRFRD-5 ROOF COVERINGS, ROOF FLASHING, ROOF DRAINAGE:
Blisters/tenting was noted on areas of the rolled roofing. A roof blister/tenting is a raised area on the roof that looks like a bubble where there is a loss of adhesion in a portion of the roof that can fill up with air or water. If left untreated, a blister/tenting can grow larger and allow additional moisture to enter which exacerbates detachment until more extensive repairs and possible replacement is necessary.
- PSDFAV-1 PLUMBING SUPPLY, DRAINS, FIXTURES AND VENTS:
A video camera sewer scope is recommended. An evaluation of the plumbing vent stacks and sewer line below the ground is beyond the scope of this inspection. Due to the age and location of the building, a sewer scope is recommended to further evaluate the sewer line and the below ground connections between the building and the municipal sewer line. Sewer scopes are done using video cameras and can reveal the materials, condition and reliability of the sewer line. If that has been done recently, I recommend having a sewer scope performed.
✒
- It was reported that there have been back-up issues in the past.
- I would have the plumbing venting system evaluated during this additional inspection. Inspector observed blocked, deteriorating plumbing vent stacks which can cause inadequate venting.
- PSDFAV-3 PLUMBING SUPPLY, DRAINS, FIXTURES AND VENTS:
The exhaust pipe at the water heater is not properly configured or secured. This condition increases the risk for noxious fumes or carbon monoxide intrusion into the occupied space. It is strongly recommended that a qualified mechanical contractor should make the appropriate repairs needed and certify that the exhaust piping conforms to the manufacturer's installation requirements for proper venting.
- PSDFAV-5 PLUMBING SUPPLY, DRAINS, FIXTURES AND VENTS:
The A.O.Smith water heater was observed to be leaking; Possibly is in need of replacement to prevent a interruption in the domestic hot water supply or water damage to the building materials from a catastrophic leak.
Approximate replacement cost $ 9,800.00 to 11,500.00
- PSDFAV-7 PLUMBING SUPPLY, DRAINS, FIXTURES AND VENTS:
Incoming main water line is galvanized steel and visible signs of corrosion are present. Recommend a qualified/licensed plumber evaluate and replace as needed.
- IAF-3 INTERIORS AND FINISHES:
FYI: Stairwells in older homes may not meet modern building standards of practice. The steps rise and run are often different and may be steeper. Height and width clearances required of modern homes may not be present and railings are often not up to today's standards. Upgrading stairs in some older homes can be difficult or impractical in some cases. The client should be aware some limitations may be present and care should be taken when traversing non standard stairs.
- O-4 OTHER:
The smoke detectors noted in the building appeared to be at or beyond the end of their service lives, typically taken to be 10 years for smoke detectors and 5 years for carbon monoxide detectors. It is recommended that the smoke detector and carbon monoxide detector systems be upgraded to reflect current life safety codes which include; smoke detectors on each level of living space, hard-wired 120 V smoke detectors that are interconnected in order to alarm simultaneously when any individual smoke detector responds, and carbon monoxide detectors at every level of living space. The installation of these critical life safety devices by a licensed and competent electrician is recommended.
Repairs
- EWGCE-1 EXTERIOR WALLS< GROUNDS, CHIMNEYS. ETC:
The existing caulking around the windows is missing, cracked and old. Exterior sealant performance is directly related to the joint preparation and application. For increased service life, performance and aesthetics, the exterior of the structure should be carefully examined and old deteriorated and/or improper caulking should be removed and the exterior of the structure caulked via appropriate means and materials. Proper joint preparation and the use of compliant exterior rated sealants of good quality is recommended .
All caulk joints should then be inspected annually and be repaired as needed. ALL exterior wall penetrations such as: piping, conduit, vent caps, exterior light fixtures and receptacles should be sealed against moisture intrusion through the use of the appropriate caulking methods and materials. An intentional opening/gap at the base of electrical fixtures should remain open to allow any moisture penetration an avenue of escape.
Several sources regarding caulking preparation can be found online, here is a link to one source: Caulking Basics
- EWGCE-2 EXTERIOR WALLS< GROUNDS, CHIMNEYS. ETC:
The exterior concrete walks, retaining walls have cracks and deteriorating concrete which can allow moisture penetration that creates the potential for further damage from freeze/thaw cycles. In order to reduce the potential for moisture related damage, the cracks should be sealed and deteriorating concrete repaired to prevent further ongoing weathering from the elements.
- EWGCE-3 EXTERIOR WALLS< GROUNDS, CHIMNEYS. ETC:
The front public sidewalk is cracked, settled and uneven which creates potential trip hazards. In order to reduce the potential for injury, it is recommended that the homeowners association contact the local municipality regarding any potential cost sharing sidewalk replacement program. Typically most municipalities will pay for up to half of the cost for sidewalk replacement for the portions of the walk that are determined to be unsafe.
- EWGCE-4 EXTERIOR WALLS< GROUNDS, CHIMNEYS. ETC:
Some of the painted/stained wood surfaces have deteriorating finish materials, flaking paint or are exposed. In order to prolong the life of materials on the exterior of the home, all exposed wood surfaces should be professionally primed and painted by a qualified painting contractor or handyman.
- EWGCE-5 EXTERIOR WALLS< GROUNDS, CHIMNEYS. ETC:
The butt joints between the individual sections of clay tile coping have been sealed with cement mortar and roofing tar. The mortar and tar is cracking and the joints are open which creates a risk for moisture saturation/damage to the masonry walls below. The coping tiles serve to protect the underlying brick masonry walls from wetting/drying and freezing/thawing damage and should be neatly joined and properly sealed in order to perform this function. The coping tiles should be repaired or replaced as needed by a qualified masonry or roofing contractor. It is recommended that the individual clay tiles be removed and reinstalled using backer rod and polyurethane caulk to seal the joints.
- EWGCE-7 EXTERIOR WALLS< GROUNDS, CHIMNEYS. ETC:
The space around the downspout entry into the subsurface drain should be sealed to prevent debris entry and clogging.
- EWGCE-8 EXTERIOR WALLS< GROUNDS, CHIMNEYS. ETC:
The mortar joints at the corners of the stone window sills and between all limestone copings/sills is cracked and deteriorated. In order to reduce the risk of moisture saturation, moisture intrusion to the interior and damage to the brick masonry below the sills, the mortar in the joints should be raked out and sealed instead with a high-quality masonry caulking compound by a qualified masonry restoration contractor or handyman.
- EWGCE-9 EXTERIOR WALLS< GROUNDS, CHIMNEYS. ETC:
The masonry walls of the three-story portion of the building are in overall good condition, considering its age. However, areas in need of repair were noted. It's recommended that the HOA make plans for phased-in repairs to the exterior masonry walls. Of particular concern are the deteriorated brick masonry units and mortar joints at the parapet walls as well as the front porch columns. Application of a penetrating masonry sealant is also recommended in order to reduce direct moisture absorption by the aged and deteriorated common bricks.
Note: The repointing performed at the exterior masonry walls was not executed in accordance with accepted industry standards and practices. Proper repointing generally requires the deteriorated mortar joints to be ground out to a depth of approximately twice that of the width of the mortar joint, and re-pointed using mortar of the same strength and composition as the original mortar. The existing flush mortar joints pose an increased potential for moisture absorption, masonry saturation and accelerated deterioration. For our climate, the mortar joints should be compacted and tooled into a concave profile for greater resistance against moisture absorption, moisture related damage to the masonry, and moisture intrusion/damage to interior finishes.
- EWGCE-11 EXTERIOR WALLS< GROUNDS, CHIMNEYS. ETC:
There are improper or missing handrails on the basement stairs. In order to reduce the potential for injury, It is recommended that a qualified carpenter or handyman install appropriate code conforming handdrails where needed.
- EWGCE-12 EXTERIOR WALLS< GROUNDS, CHIMNEYS. ETC:
The aluminum window/door casings have not been sealed with appropriate materials that would reduce the potential for damaging moisture to come into contact with them. Exposure to moisture can lead to shortened life of building components that includes but is not limited to the existing masonry, wood framing, windows and interior finishes.
NOTE- Contractors differ on this subject because many times the existing wood casings are in substantially good shape and don't require repairs but are covered anyway in order to reduce maintenance and for the sake of appearance. The Inspector's OPINION is that it is better to seal the gap between the metal capping and masonry to reduce moisture loads at known entry points. The use of a weep at the bottom of the casings is recommended to convey trapped moisture to the exterior.
- EWGCE-13 EXTERIOR WALLS< GROUNDS, CHIMNEYS. ETC:
The limestone entry pads shows evidence of ice melting salt damage via spalling and an irregular, 'popped' surface. While mainly cosmetic this condition does not improve and will likely worsen. Some temporary measures may be taken to thwart continued decay such as the cessation of salt use and cleaning/sealing of the existing concrete surfaces.
- EWGCE-14 EXTERIOR WALLS< GROUNDS, CHIMNEYS. ETC:
All dissimilar elements at the exterior walls of the building such as: brick-to-stone; brick-to-concrete block; concrete block-to-glass block, etc. should be joined one to the other and sealed against moisture through the use of backer rod and urethane caulk or its equivalent. These dissimilar elements have differing coefficients of expansion and contraction in relation to temperature and moisture. This can lead to cracking of the cladding material and/or of the mortar joints. The existing cement mortar joints should be ground out and replaced with the appropriate backer rod and ASTM approved caulking. This procedure is in keeping with the standards set forth by the Brick Industry Association. Further information is available at www.bia.org
- EWGCE-15 EXTERIOR WALLS< GROUNDS, CHIMNEYS. ETC:
The masonry wall flashings are either missing or improperly installed. The flashings should be used in conjunction with stainless steel drip edge, should be 'end dammed' and should be present at the following locations: the top of the foundation wall; above the masonry pockets where the floor joists are set into the masonry wall; above and below every window, door and all lintels/beams. Missing or improperly installed wall flashing can allow moisture to enter the structure and cause rot, mold growth and structural damage. The exterior masonry walls of this structure should be evaluated and repaired by a qualified masonry contractor.
Here is a link to an article from the Mason Contractors of America Association that discusses proper masonry flashing: Masonry Wall Flashings
Here is a link to additional information from the National Concrete Masonry Association regarding flashing in masonry walls: Flashing Strategies for Concrete Masonry Walls
NOTE: While the cost to retrofit missing or improperly installed masonry wall flashings for the window and door lintels can vary significantly depending on the height of the work, the need for sidewalk canopies, proximity of overhead power lines, etc., a commonly quoted cost for such work is approximately $225 per lineal foot.
- EWGCE-16 EXTERIOR WALLS< GROUNDS, CHIMNEYS. ETC:
The exterior window lintels have been sealed and can no longer drain moisture which increases the potential for corrosion of the lintels. Over time the corroding steel will expand which can damage the adjacent masonry walls and allow moisture to penetrate to the interior of the living space. In order to reduce the potential for moisture related damage, the lintel drainage space should be repaired by a qualified masonry restoration contractor.
- RCRFRD-1 ROOF COVERINGS, ROOF FLASHING, ROOF DRAINAGE:
The modified bitumen roof covering is not properly secured to the back of the roof gutter. This defect presents an increased risk for damage from ice damming and from water backing up at the gutter. It is recommended that the roof/gutter interface be repaired by a qualified roofing contractor.
- RCRFRD-2 ROOF COVERINGS, ROOF FLASHING, ROOF DRAINAGE:
In order to reduce stress on the modified bitumen roof where it meets the parapet wall and to prevent both cracking and premature failure, cant strip is required to be installed at the inside corners by roof covering manufacturers. This component was found to be missing in multiple locations and in order to determine if retrofitting of the cant strip is feasible and cost-effective, further evaluation by a qualified roofing contractor is recommended.
- RCRFRD-6 ROOF COVERINGS, ROOF FLASHING, ROOF DRAINAGE:
Best roofing practices call for the roof covering to be held back and terminated along the parapet wall typically between 12" and 36" depending on the height of the parapet wall itself. When the membrane is wrapped up and over the parapet top it prevents moisture from draining/evaporating at that side and will reduce mortar and brick life on the opposite side as moisture seeks pathways to drain or evaporate. It is recommended that the membrane be removed and terminated at an appropriate height on the parapet wall with appropriate base and counterflashing. Once the roofing has been removed the masonry parapet walls should be evaluated by a qualified masonry restoration contractor and mortar repairs should be expected where the roof concealed masonry details.
- RCRFRD-7 ROOF COVERINGS, ROOF FLASHING, ROOF DRAINAGE:
The tree limbs that are in contact with the roof or hanging near the roof should be trimmed by a qualified arborist. In order to determine the long term prognosis for the tree, the health and condition should also be assessed at the time of the trimming.
- RCRFRD-8 ROOF COVERINGS, ROOF FLASHING, ROOF DRAINAGE:
Missing and improperly sealed flashings were noted on the modified bitumen roof covering. The use of tar as was noted here, greatly increases the risk of leaking and neatly applied modified bitumen patches should be used instead. All of the rooftop penetrations, such as plumbing vent pipes, skylights, electrical conduit, and air conditioning line sets should be evaluated and repaired by a licensed and competent roofing contractor.
- RCRFRD-9 ROOF COVERINGS, ROOF FLASHING, ROOF DRAINAGE:
The A/C refrigerant line roof penetrations are sealed with caulk and/or tar which is a high maintenance, low performance solution that creates the potential for damaging and mold causing moisture to enter the structure. It is recommended that the roof penetrations be repaired by a qualified roofing and/or HVAC contractor and the solutions should include pitch pocket flashing or rubber boot flashing specifically designed for the various diameter tubing sizes in order to separate the lines and create the potential for more effective sealing of the A/C refrigerant lines.
- RCRFRD-10 ROOF COVERINGS, ROOF FLASHING, ROOF DRAINAGE:
Termination bar flashing should be installed and all areas where the modified bitumen roof covering is terminated. Failure to install the appropriate flashing at these areas can result in delamination, breaching, moisture intrusion, and extensive damage.
- RCRFRD-11 ROOF COVERINGS, ROOF FLASHING, ROOF DRAINAGE:
The thin aluminum flashing member noted at the top of the parapet walls does not constitute a proper modified bitumen termination flashing. This thin aluminum strip is intended to be covered with a wider counter flashing.
- RCRFRD-12 ROOF COVERINGS, ROOF FLASHING, ROOF DRAINAGE:
The limestone capping above the parapet walls and its ancillary flashing are improperly configured, loose, cracked, improperly sealed and present a significant risk for moisture penetration, moisture saturation, and damage to the adjacent brick masonry. Roofing tar appears to have been smeared over the joints between the stone sills/copings and cracks were noted on the sides of the tarred joints. A thin smear of roofing tar over a brittle substrate such as cement mortar, does not constitute an appropriate sealant joint. The mortar joints between all limestone copings/sills have a tendency to crack and the observed tar was most likely applied in response to moisture intrusion. In order to reduce the risk of moisture related damage to the interior and the masonry below the sills the parapet wall capstones should be sloped inward toward the roof surface so that runoff is properly channeled to the roof drains and so that the amount of moisture running onto the exterior masonry walls is limited. It is recommended that the existing limestone capping be removed; stainless steel drip edge be set into a thick bed of high-quality caulking along both the inner and outer top masonry courses; that heavy, self-adhesive, elastomeric flashing be installed as a waterproof bridge across the entire depth of the masonry wall; and that the existing limestone capping or new limestone capping be set into place and secured with stainless steel pins; and that properly configured caulked joints be used at the butt joints of the limestone capping slabs.
- RCRFRD-13 ROOF COVERINGS, ROOF FLASHING, ROOF DRAINAGE:
Porch roof deck support post was noted to be missing a positive connection. I recommend installing positive connections at post to beam juncture for the back porch roof to better protect the roof frame from damage.
- SAF-1 STRUCTURE AND FOUNDATION:
Cracking and spalling cementious patch / skim coating was observed at the West foundation wall. This condition is an indication of moisture in contact with the foundation. Repairs are needed to prevent further deterioration and moisture intrusion.
- SAF-2 STRUCTURE AND FOUNDATION:
This older building has stone foundation walls. A white efflorescent powder and crystals were noted on the foundation walls which is generally a sign of moisture slowly passing through the walls. While no specific signs of active leakage were noted at the time of the inspection, however; signs of prior leakage were observed. In order to reduce the potential for moisture related damage, it is recommended that consideration be given towards having a qualified basement waterproofing contractor install a perimeter drainage system.
Here is a link to an article from a contractor that installs these systems that details the process: Interior Weeping Tile Perimeter Drainage Systems
Approximate cost for perimeter drainage system range between $38,000.00 to $50,000.00
- ESGCDAF-1 ELECTRICAL SYSTEM, GROUNDING, CONNECTED DEVICES AND FIXTURES:
The grounding electrode conductor and the water meter bonding jumper are not properly secured to the water piping system or to their clamps. The stranded copper grounding conductor has been squeezed between the clamp and the piping. This is not allowed and is unsafe since it makes the clamp prone to loosening and can reduce the safety and effectiveness of the bonding and grounding system. The existing clamps should be replaced with ones that can properly secure the grounding electrode conductor and bonding jumpers into screw terminals. Further evaluation and repair by a licensed and competent electrical contractor is recommended.
- ESGCDAF-3 ELECTRICAL SYSTEM, GROUNDING, CONNECTED DEVICES AND FIXTURES:
Extinguished or otherwise inoperative luminaires (light bulbs) were noted during the inspection. All of the lighting in the structure should be made fully operational for the final walk-through so that the proper operation of all the lighting can be verified and differentiated from defective switches, fixtures, etc.
NOTE: Some exterior fixtures may be controlled by photocells that will only allow the lights to operate at night and operation of all exterior fixtures should be verified at the final walk-through prior to closing.
- ESGCDAF-5 ELECTRICAL SYSTEM, GROUNDING, CONNECTED DEVICES AND FIXTURES:
No ground rod was not found outside, no ground rod was found Inside. A ground rod is recommended along with a plumbing ground to provide adequate grounding for the electrical system. Depending on when the home was built and the towns requirements, a ground rod may or may not be required. Recommend checking with town for local requirements and qualified electrician to assess further for safety and to meet the towns requirements.
- ESGCDAF-6 ELECTRICAL SYSTEM, GROUNDING, CONNECTED DEVICES AND FIXTURES:
In order to reduce the risk for electrical shock from inadvertent contact with exposed current carrying equipment and in order to contain molten copper created by high temperature arcing and sparking of energized wiring. One or more receptacles in the basement is missing a cover plate. It is recommended that all electrical connections be concealed inside covered metal junction boxes and cover plates be installed were needed.
- ESGCDAF-7 ELECTRICAL SYSTEM, GROUNDING, CONNECTED DEVICES AND FIXTURES:
A spot check of the battery operated emergency lighting system/s revealed one or more non-functioning units. It is strongly recommended that these critical life safety devices be regularly evaluated and repaired as needed by a qualified electrician.
- ESGCDAF-8 ELECTRICAL SYSTEM, GROUNDING, CONNECTED DEVICES AND FIXTURES:
It is recommended that the exterior electrical receptacles be provided with "in use" covers in order to reduce the risk for contact between energized electrical equipment and moisture. Such contact can result in arcing/sparking, shock, fire, etc.
- PSDFAV-4 PLUMBING SUPPLY, DRAINS, FIXTURES AND VENTS:
A cover should be installed over the floor drain to prevent the entry of debris into the drain that could result in clogging.
- PSDFAV-6 PLUMBING SUPPLY, DRAINS, FIXTURES AND VENTS:
The discharge tube for the water heater temperature and pressure relief valve is incorrectly installed. The discharge tube should not have threaded fittings at the end of the tube as this risks the discharge being capped. Hire a licensed plumbing contractor to further evaluate and repair. Ideally, the discharge tube for a relief valve:
- Terminates to an exterior location or above a drain, though this is not always possible
- Terminates between 6 and 24-inches off the ground (UPC)
- Slopes to drain to prevent water pooling inside the discharge tube
- Is not made from pipe with an inside diameter less than 3/4 on an inch
- Is made from an approved supply piping material: copper, PEX, CPVC or galvanized steel
- Terminates to a visible location that can be monitored for leaks and discharges
- Does not have a threaded termination point which would prevent accidental capping of this important discharge
I recommend having this relief valve discharge tube further investigated and repaired as recommended by a licensed plumber.
- IVAE-1 INSULATION, VENTILATION, ATTICS, ETC.:
The existing cheap plastic vent and/or dryer dampers are cracked warped and/or missing slats and are open to the exterior which creates the potential for cold air to enter and condense on warmer interior components and for flying pests to enter the open dryer venting. In order to reduce the potential for corrosion and moisture related damage and unwanted visitors, all dryer and exhaust vent dampers on the exterior walls should be replaced with high-quality, gasketed, vent dampers.
NOTE: In order to ensure proper performance of the dryer vents, regular examination and cleaning of dryer vents is recommended.
- IVAE-2 INSULATION, VENTILATION, ATTICS, ETC.:
The plenum venting appears inadequate for the square footage as well as the known poor airflow characteristics/placement of the installed vents noted. This can contribute to elevated energy costs, moisture related deterioration to roofing and/or structural framing, and reduced roof life. The ventilation should be improved by a qualified roofing contractor with a written ventilation calculation performed. The Inspection Firm recommends this type for increased performance: Aura Roof Vents
- IVAE-3 INSULATION, VENTILATION, ATTICS, ETC.:
The inspector was unable to verify the presence or absence of thermal insulation in the walls or ceilings.
- IAF-1 INTERIORS AND FINISHES:
Open gaps were noted in the basement ceiling that can allow smoke, carbon monoxide, and superheated gases to pass into other areas of the building in the event of a fire. In order to close off the gaps it is recommended that all openings be sealed with 5/8 drywall, intumescent foam or other appropriate fireproofing materials.
- IAF-2 INTERIORS AND FINISHES:
The interior walls, floors, ceiling, and trim have normal wear and tear. Interior blemishes or required repairs exist, some of which are omitted from this report and considered maintenance/basic wear-and-tear. A qualified drywall, plaster/painting contractor or handyman is recommended to repair these areas as needed for proper appearance. The photo/s are representative, not all inclusive, of repairs needed.
NOTE: Caulk/sealant is a temporary building material and will require relatively frequent repairs or replacement. The highest quality sealant affordable is recommended for improved service life.
- IAF-4 INTERIORS AND FINISHES:
The existing handrails have open ends that project from the wall. Modern safety standards require that interior handrails be returned 90 degrees to the wall and in order to reduce the risk of snagging, falls and injuries and the handrails should be modified or replaced by a qualified carpenter or handyman.
- IAF-5 INTERIORS AND FINISHES:
The staircase was noted as being sloped/unlevel. This can be a result of settlement in the surrounding framing members over time. Without having direct access to the framing underneath, it is impossible to tell what is the cause without doing invasive inspection procedures.
- WDS-1 WINDOWS, DOORS, SKYLIGHTS:
The installation of high quality rubber bulb weatherstripping is recommended at the top and sides of the entry door/s. The installation of a weatherstripped threshold is recommended at the bottom of the building entry doors. These modifications will conserve energy, reduce cold drafts, and reduce noise levels inside the living space.
- WDS-2 WINDOWS, DOORS, SKYLIGHTS:
One or more window frames were noted to be detached, open, loose or bent. This is indicative of moisture, rodent, insect intrusion or biological growth to the interior wall structure.
- O-1 OTHER:
Due to the age of the building and the existence of multiple layers of paint, the possibility exists that lead based paint is present in one or more areas of the structure. Further evaluation by a qualified lead paint or environmental specialist is recommended. Occupants should assume that any painted surface in an older structure contains lead based paint and should be handled with all appropriate precautions.
Here is a link to a webpage from the EPA that provides answers to frequently asked questions regarding lead based paint: Lead Based Paint - Frequently Asked Questions
- O-3 OTHER:
Large devices typically associated with rats were noted around the perimeter of the property and larger holes were noted near the building. Rats are extremely common in the City and typically attracted to waste and hidden nesting areas. Any areas that provide a safe haven for rats should be cleared of clutter that provides the ability for concealment and all waste should be kept in special waste containers.
The City of Chicago has a program to assist in controlling rats through a special waste container distribution program and via other means. Here is a link to the City's webpage that provides information regarding ongoing rat control: Rodent Control (Rodent Baiting)
- O-5 OTHER:
Fire Extinguishers Need Servicing. There were missing or expired service tags on the fire extinguishers. It is recommend that all fire/ life safety devices be inspected and serviced as needed on an annual basis.
Recommended Maintenance Items
- RCRFRD-14 ROOF COVERINGS, ROOF FLASHING, ROOF DRAINAGE:
Debris was observed on the roof covering. This can lead to punctures, tears, ponding areas, damage to the substrate, possibility of roof leaks and water damage. The debris should be removed safely so as not to compromise the roof covering or building components.
Improves
- ESGCDAF-2 ELECTRICAL SYSTEM, GROUNDING, CONNECTED DEVICES AND FIXTURES:
It is recommended that all electrical receptacles in the bathrooms, unfinished basement areas, kitchen counters and islands, jetted tubs, laundry area, sump pumps, food waste disposers, garage, and all exterior locations that are not already GFCI protected, be upgraded to GFCI protected receptacles by a licensed and competent electrician in order to reduce the risk of electrical shock and injury.
It is further advised that any pre 2007 GFCI type receptacles be upgraded to Smart GFCI receptacles. Smart GFCI receptacles will not continue to allow electrical current if the on board trip mechanism is no longer functional, or if the receptacle is improperly wired. Smart GFCI receptacles are easily recognized by an on board LED status light.
Due Diligences
- GI-1 GENERAL INFORMATION:
All of the recommendations for repairs or alterations that are contained in this report should be performed by licensed and competent contractors with expertise in the appropriate trade or specialty. It is recommended that the repairs/alterations be completed prior to closing. The contractor/s who perform the recommended repairs at the seller's direction should provide the buyer/client with all appropriate documentation regarding the materials and methods used in the work. A list of contractors who have been rated and recommended by consumers can be found at www.angieslist.com
- ESGCDAF-4 ELECTRICAL SYSTEM, GROUNDING, CONNECTED DEVICES AND FIXTURES:
The evaluation of the low-voltage equipment in the home: alarm, communication, audiovisual, etc., is beyond the scope of the home inspection and should be performed by a qualified low-voltage electrical contractor. In order to reduce the potential for confusion and to reduce clutter around the home, any wiring, panels, cabinets, etc. for any equipment that is no longer in use should be removed.
- PSDFAV-2 PLUMBING SUPPLY, DRAINS, FIXTURES AND VENTS:
The outside water shut-off, a.k.a. the 'buffalo box', was not located during the inspection. It is recommended that the municipal water utility be contacted for a 'locate and test' (usually a provided to the taxpayer as a free service) be provided so that the outside shut-off can be operated for repairs or in an emergency.
- O-2 OTHER:
Prior to circa 1980, asbestos was in relatively common use in the building material industry. In order to reduce the potential for the spread of asbestos fibers throughout the residence, any aged building product in the structure of uncertain content that is being disturbed should first be evaluated by a qualified environmental remediation contractor or testing laboratory.
In order to determine if asbestos is present in these materials, it may be possible for the buyer/homeowner to carefully collect a small sample of the material/s to send to a lab for analysis.
Here is a link to a Chicago testing lab that may be able to perform this testing: Indoor Science Testing Lab
Here is a link to a Chicago suburban testing lab that may be able to perform this testing: UAS Laboratory Services
Future Projects
- RCRFRD-3 ROOF COVERINGS, ROOF FLASHING, ROOF DRAINAGE:
Alligatoring is a sign that your roof is aging. The sun’s UV rays dry and damage the roof’s surface, and after three to five years, the coating may develop small cracks. If left untended, the problem will get worse. Ice, sunlight and the heating and cooling shifts between day and night will all cause new cracks to appear while widening the existing cracks.
- RCRFRD-4 ROOF COVERINGS, ROOF FLASHING, ROOF DRAINAGE:
Ponded areas were noted on the low slope roof. Ponding accelerates the rate of roof wear/deterioration and increases the risk for leaking. When a new roof covering is installed, plans should be made to re-pitch the roof using tapered roof insulation.
The Full Report
GENERAL INFORMATION
TYPE OF STRUCTURE: Low Rise Condominium
NUMBER OF BEDROOMS: Unknown
APPROXIMATE AGE OF STRUCTURE: Per Listing Built, 1907
STRUCTURE FACES: South, West
CLIENT PRESENT: Yes
RADON TEST: No
WATER QUALITY TEST: No
WEATHER CONDITIONS: Clear, Hot and Humid
AMBIENT TEMPERATURE: Over 60
NUMBER OF STORIES: Three Story
EXTERIOR WALL CONSTRUCTION: Masonry
PRIMARY EXTERIOR WALL CLADDING MATERIAL: Brick
FOUNDATION: Stone Foundation Walls, Full Basement (Partially Finished), Foundation not Fully Visible, Stored Items Limited the Inspectors Ability to View the Foundation Walls
All of the recommendations for repairs or alterations that are contained in this report should be performed by licensed and competent contractors with expertise in the appropriate trade or specialty. It is recommended that the repairs/alterations be completed prior to closing. The contractor/s who perform the recommended repairs at the seller's direction should provide the buyer/client with all appropriate documentation regarding the materials and methods used in the work. A list of contractors who have been rated and recommended by consumers can be found at www.angieslist.com
Report images are examples of conditions present at the time of inspection, However; the images do not represent every instance of conditions present at the subject property.
EXTERIOR WALLS< GROUNDS, CHIMNEYS. ETC
GAS SHUT-OFF LOCATION: Common Area Meter Room
WALKWAYS PATIOS DRIVEWAYS: Concrete Patio, Concrete Walks, Cracking and Settling Noted at Concrete Walkways, Reverse Sloping of Exterior Grading Increases Risk for Basement Seepage
VEGETATION/GRADING/DRAINAGE: Inadequate Clearance between Masonry Wall and Exterior Grade Level, Large Trees at Front Yard Present. Risk for Sewer Blockage.
EXTERIOR STEPS/STAIRWAYS/RAILINGS: Missing Handrail at Basement Stairway, Wood Porch/Deck at Rear, Wood Stairs at Rear
The existing caulking around the windows is missing, cracked and old. Exterior sealant performance is directly related to the joint preparation and application. For increased service life, performance and aesthetics, the exterior of the structure should be carefully examined and old deteriorated and/or improper caulking should be removed and the exterior of the structure caulked via appropriate means and materials. Proper joint preparation and the use of compliant exterior rated sealants of good quality is recommended .
All caulk joints should then be inspected annually and be repaired as needed. ALL exterior wall penetrations such as: piping, conduit, vent caps, exterior light fixtures and receptacles should be sealed against moisture intrusion through the use of the appropriate caulking methods and materials. An intentional opening/gap at the base of electrical fixtures should remain open to allow any moisture penetration an avenue of escape.
Several sources regarding caulking preparation can be found online, here is a link to one source: Caulking Basics
The exterior concrete walks, retaining walls have cracks and deteriorating concrete which can allow moisture penetration that creates the potential for further damage from freeze/thaw cycles. In order to reduce the potential for moisture related damage, the cracks should be sealed and deteriorating concrete repaired to prevent further ongoing weathering from the elements.
The front public sidewalk is cracked, settled and uneven which creates potential trip hazards. In order to reduce the potential for injury, it is recommended that the homeowners association contact the local municipality regarding any potential cost sharing sidewalk replacement program. Typically most municipalities will pay for up to half of the cost for sidewalk replacement for the portions of the walk that are determined to be unsafe.
Some of the painted/stained wood surfaces have deteriorating finish materials, flaking paint or are exposed. In order to prolong the life of materials on the exterior of the home, all exposed wood surfaces should be professionally primed and painted by a qualified painting contractor or handyman.
The butt joints between the individual sections of clay tile coping have been sealed with cement mortar and roofing tar. The mortar and tar is cracking and the joints are open which creates a risk for moisture saturation/damage to the masonry walls below. The coping tiles serve to protect the underlying brick masonry walls from wetting/drying and freezing/thawing damage and should be neatly joined and properly sealed in order to perform this function. The coping tiles should be repaired or replaced as needed by a qualified masonry or roofing contractor. It is recommended that the individual clay tiles be removed and reinstalled using backer rod and polyurethane caulk to seal the joints.
Some of the lintels are rusting at the windows. Recommend properly sealing the metal to help prevent additional damage.
The space around the downspout entry into the subsurface drain should be sealed to prevent debris entry and clogging.
The mortar joints at the corners of the stone window sills and between all limestone copings/sills is cracked and deteriorated. In order to reduce the risk of moisture saturation, moisture intrusion to the interior and damage to the brick masonry below the sills, the mortar in the joints should be raked out and sealed instead with a high-quality masonry caulking compound by a qualified masonry restoration contractor or handyman.
The masonry walls of the three-story portion of the building are in overall good condition, considering its age. However, areas in need of repair were noted. It's recommended that the HOA make plans for phased-in repairs to the exterior masonry walls. Of particular concern are the deteriorated brick masonry units and mortar joints at the parapet walls as well as the front porch columns. Application of a penetrating masonry sealant is also recommended in order to reduce direct moisture absorption by the aged and deteriorated common bricks.
Note: The repointing performed at the exterior masonry walls was not executed in accordance with accepted industry standards and practices. Proper repointing generally requires the deteriorated mortar joints to be ground out to a depth of approximately twice that of the width of the mortar joint, and re-pointed using mortar of the same strength and composition as the original mortar. The existing flush mortar joints pose an increased potential for moisture absorption, masonry saturation and accelerated deterioration. For our climate, the mortar joints should be compacted and tooled into a concave profile for greater resistance against moisture absorption, moisture related damage to the masonry, and moisture intrusion/damage to interior finishes.
Numerous repairs are needed to the decking systems on this building to ensure safe and reliable performance. Some of these repairs can be made, while other issues may be difficult to fully correct until the deck is rebuilt. I recommend additional inspection and repair of these decks by a qualified general contractor. Options include a full re-building or implementing repairs as are feasible to safely prolong the useful life of the deck.
Note: The dryer exhaust dampers and furnace exhaust piping needs to be removed from ledge board and under the decking. These two items are contributing to the deleterious and corrosive conditions of the deck structure.
Repair cost per contractors bid $94,550.00, Replacement cost per contractor bid $131,150.00
Examples of observations and defects noted during inspection include:
Ledger Board
- Incorrect Bolting: The ledger board is not correctly bolted - see attached information in the DCA-6 for proper ledger bolting
- Hangers Corroded: The metal hangers used to connect the floor joists to the ledger board are corroded and require replacement
- Corrode ledge fasteners: Corroded ledger board fasteners were noted - this can lead to detachment and potential deck collapse issue.
- Hanger Fasteners are Incomplete: The metal hangers used to connect the floor joists to the ledger board are missing proper fasteners - all round holes in the hangers should have a nail
- Ledger Flashings Missing: The ledger board is missing proper proper flashings - this can lead to moisture control problems and even deck failure
- Lateral Load Connectors Missing: The ledger board is missing recommended lateral load connectors, these are now required
- Ledger Board is Improperly Notch / Cut
Guards
- Wood Decay in Guardrail Posts: Rotted wood noted on the guardrail posts. This can weaken the guardrail system presenting a possible safety hazard.
- Guardrail is Loose: The guardrail is loose and may not adequately withstand the force of a falling adult presenting a possible safety hazard.
Decking
- Slippery Decking: The decking is currently presenting a slippery walking surface. This is a safety hazard. Clean and stain the decking for improved safety and to better preserve the wood.
Floor Structure
- Positive Connections Missing: The floor frame is lacking proper positive connections between posts and beams. Deck framing connections should be made with reliable connectors designed to resist failure.
Posts and Footings
- Cracked Post: The support post have advanced cracking. This can weaken the deck structure and present a possible safety issue.
- Piers At Grade: The deck footing system appears to be done at grade. Standards call for deck footings to be at least 12 inches below grade and resting on well-compacted soils. This recommended is designed to resist deck settlement.
Stairs
- Stringers Lacking Positive Attachment: The stair stringers have not been properly attached to the landing
Positive Connections
- The post to beam connections are missing proper positive connections - metal connectors that reliably attach the post to the beam.
- The brackets that connect the base of the posts to the footings are significantly corroded and may require replacement
There are improper or missing handrails on the basement stairs. In order to reduce the potential for injury, It is recommended that a qualified carpenter or handyman install appropriate code conforming handdrails where needed.
The aluminum window/door casings have not been sealed with appropriate materials that would reduce the potential for damaging moisture to come into contact with them. Exposure to moisture can lead to shortened life of building components that includes but is not limited to the existing masonry, wood framing, windows and interior finishes.
NOTE- Contractors differ on this subject because many times the existing wood casings are in substantially good shape and don't require repairs but are covered anyway in order to reduce maintenance and for the sake of appearance. The Inspector's OPINION is that it is better to seal the gap between the metal capping and masonry to reduce moisture loads at known entry points. The use of a weep at the bottom of the casings is recommended to convey trapped moisture to the exterior.
The limestone entry pads shows evidence of ice melting salt damage via spalling and an irregular, 'popped' surface. While mainly cosmetic this condition does not improve and will likely worsen. Some temporary measures may be taken to thwart continued decay such as the cessation of salt use and cleaning/sealing of the existing concrete surfaces.
All dissimilar elements at the exterior walls of the building such as: brick-to-stone; brick-to-concrete block; concrete block-to-glass block, etc. should be joined one to the other and sealed against moisture through the use of backer rod and urethane caulk or its equivalent. These dissimilar elements have differing coefficients of expansion and contraction in relation to temperature and moisture. This can lead to cracking of the cladding material and/or of the mortar joints. The existing cement mortar joints should be ground out and replaced with the appropriate backer rod and ASTM approved caulking. This procedure is in keeping with the standards set forth by the Brick Industry Association. Further information is available at www.bia.org
The masonry wall flashings are either missing or improperly installed. The flashings should be used in conjunction with stainless steel drip edge, should be 'end dammed' and should be present at the following locations: the top of the foundation wall; above the masonry pockets where the floor joists are set into the masonry wall; above and below every window, door and all lintels/beams. Missing or improperly installed wall flashing can allow moisture to enter the structure and cause rot, mold growth and structural damage. The exterior masonry walls of this structure should be evaluated and repaired by a qualified masonry contractor.
Here is a link to an article from the Mason Contractors of America Association that discusses proper masonry flashing: Masonry Wall Flashings
Here is a link to additional information from the National Concrete Masonry Association regarding flashing in masonry walls: Flashing Strategies for Concrete Masonry Walls
NOTE: While the cost to retrofit missing or improperly installed masonry wall flashings for the window and door lintels can vary significantly depending on the height of the work, the need for sidewalk canopies, proximity of overhead power lines, etc., a commonly quoted cost for such work is approximately $225 per lineal foot.
The exterior window lintels have been sealed and can no longer drain moisture which increases the potential for corrosion of the lintels. Over time the corroding steel will expand which can damage the adjacent masonry walls and allow moisture to penetrate to the interior of the living space. In order to reduce the potential for moisture related damage, the lintel drainage space should be repaired by a qualified masonry restoration contractor.
ROOF COVERINGS, ROOF FLASHING, ROOF DRAINAGE
Roof Covering: Blistered, Missing Reflective Coating, Modified Bitumen, Ponded Areas Noted
Roof Viewed: Roof Was Walked
The modified bitumen roof covering is not properly secured to the back of the roof gutter. This defect presents an increased risk for damage from ice damming and from water backing up at the gutter. It is recommended that the roof/gutter interface be repaired by a qualified roofing contractor.
In order to reduce stress on the modified bitumen roof where it meets the parapet wall and to prevent both cracking and premature failure, cant strip is required to be installed at the inside corners by roof covering manufacturers. This component was found to be missing in multiple locations and in order to determine if retrofitting of the cant strip is feasible and cost-effective, further evaluation by a qualified roofing contractor is recommended.
Alligatoring is a sign that your roof is aging. The sun’s UV rays dry and damage the roof’s surface, and after three to five years, the coating may develop small cracks. If left untended, the problem will get worse. Ice, sunlight and the heating and cooling shifts between day and night will all cause new cracks to appear while widening the existing cracks.
Ponded areas were noted on the low slope roof. Ponding accelerates the rate of roof wear/deterioration and increases the risk for leaking. When a new roof covering is installed, plans should be made to re-pitch the roof using tapered roof insulation.
Blisters/tenting was noted on areas of the rolled roofing. A roof blister/tenting is a raised area on the roof that looks like a bubble where there is a loss of adhesion in a portion of the roof that can fill up with air or water. If left untreated, a blister/tenting can grow larger and allow additional moisture to enter which exacerbates detachment until more extensive repairs and possible replacement is necessary.
Best roofing practices call for the roof covering to be held back and terminated along the parapet wall typically between 12" and 36" depending on the height of the parapet wall itself. When the membrane is wrapped up and over the parapet top it prevents moisture from draining/evaporating at that side and will reduce mortar and brick life on the opposite side as moisture seeks pathways to drain or evaporate. It is recommended that the membrane be removed and terminated at an appropriate height on the parapet wall with appropriate base and counterflashing. Once the roofing has been removed the masonry parapet walls should be evaluated by a qualified masonry restoration contractor and mortar repairs should be expected where the roof concealed masonry details.
The tree limbs that are in contact with the roof or hanging near the roof should be trimmed by a qualified arborist. In order to determine the long term prognosis for the tree, the health and condition should also be assessed at the time of the trimming.
Missing and improperly sealed flashings were noted on the modified bitumen roof covering. The use of tar as was noted here, greatly increases the risk of leaking and neatly applied modified bitumen patches should be used instead. All of the rooftop penetrations, such as plumbing vent pipes, skylights, electrical conduit, and air conditioning line sets should be evaluated and repaired by a licensed and competent roofing contractor.
The A/C refrigerant line roof penetrations are sealed with caulk and/or tar which is a high maintenance, low performance solution that creates the potential for damaging and mold causing moisture to enter the structure. It is recommended that the roof penetrations be repaired by a qualified roofing and/or HVAC contractor and the solutions should include pitch pocket flashing or rubber boot flashing specifically designed for the various diameter tubing sizes in order to separate the lines and create the potential for more effective sealing of the A/C refrigerant lines.
Termination bar flashing should be installed and all areas where the modified bitumen roof covering is terminated. Failure to install the appropriate flashing at these areas can result in delamination, breaching, moisture intrusion, and extensive damage.
The thin aluminum flashing member noted at the top of the parapet walls does not constitute a proper modified bitumen termination flashing. This thin aluminum strip is intended to be covered with a wider counter flashing.
The limestone capping above the parapet walls and its ancillary flashing are improperly configured, loose, cracked, improperly sealed and present a significant risk for moisture penetration, moisture saturation, and damage to the adjacent brick masonry. Roofing tar appears to have been smeared over the joints between the stone sills/copings and cracks were noted on the sides of the tarred joints. A thin smear of roofing tar over a brittle substrate such as cement mortar, does not constitute an appropriate sealant joint. The mortar joints between all limestone copings/sills have a tendency to crack and the observed tar was most likely applied in response to moisture intrusion. In order to reduce the risk of moisture related damage to the interior and the masonry below the sills the parapet wall capstones should be sloped inward toward the roof surface so that runoff is properly channeled to the roof drains and so that the amount of moisture running onto the exterior masonry walls is limited. It is recommended that the existing limestone capping be removed; stainless steel drip edge be set into a thick bed of high-quality caulking along both the inner and outer top masonry courses; that heavy, self-adhesive, elastomeric flashing be installed as a waterproof bridge across the entire depth of the masonry wall; and that the existing limestone capping or new limestone capping be set into place and secured with stainless steel pins; and that properly configured caulked joints be used at the butt joints of the limestone capping slabs.
Porch roof deck support post was noted to be missing a positive connection. I recommend installing positive connections at post to beam juncture for the back porch roof to better protect the roof frame from damage.
Debris was observed on the roof covering. This can lead to punctures, tears, ponding areas, damage to the substrate, possibility of roof leaks and water damage. The debris should be removed safely so as not to compromise the roof covering or building components.
STRUCTURE AND FOUNDATION
FLOOR STRUCTURE: Unable to Determine
CRAWLSPACE ACCESS: No Crawlspace
MAIN FLOOR BEAM AND POSTS: Structural Steel Posts and Beams
Cracking and spalling cementious patch / skim coating was observed at the West foundation wall. This condition is an indication of moisture in contact with the foundation. Repairs are needed to prevent further deterioration and moisture intrusion.
This older building has stone foundation walls. A white efflorescent powder and crystals were noted on the foundation walls which is generally a sign of moisture slowly passing through the walls. While no specific signs of active leakage were noted at the time of the inspection, however; signs of prior leakage were observed. In order to reduce the potential for moisture related damage, it is recommended that consideration be given towards having a qualified basement waterproofing contractor install a perimeter drainage system.
Here is a link to an article from a contractor that installs these systems that details the process: Interior Weeping Tile Perimeter Drainage Systems
Approximate cost for perimeter drainage system range between $38,000.00 to $50,000.00
ELECTRICAL SYSTEM, GROUNDING, CONNECTED DEVICES AND FIXTURES
ELECTRICAL SERVICE: 240 volts, Service Conductors, Not Visible/Unknown, Overhead service
LOCATION OF MAIN SERVICE DISCONNECT: Electric service panel
SERVICE PANEL AMPACITY: 800 AMPS, Main Panel and Sub-panel, 100 AMP, 15 Service Panels
OVERCURRENT PROTECTION DEVICES: Circuit Breakers
SERVICE PANEL BRAND: SIEMENS, GENERAL ELECTRIC
BRANCH CIRCUIT CONDUCTORS: Not fully visible
NUMBER OF CIRCUITS USED - NUMBER OF CIRCUITS AVAILABLE FOR USE: Unknown
WIRING METHODS: Armored Cable (BX), Electrical Metallic Tubing EMT (Conduit), Not Fully Visible
ELECTRICAL GROUNDING CONDUCTOR/CLAMP LOCATION: Basement Floor, Water Pipe Grounding Clamp, The Bonding/Grounding Is Defective and Should Be Repaired by a Qualified Electrical Contractor As Soon As Practical, Water Pipe Grounding Clamp - GEC Improper
The grounding electrode conductor and the water meter bonding jumper are not properly secured to the water piping system or to their clamps. The stranded copper grounding conductor has been squeezed between the clamp and the piping. This is not allowed and is unsafe since it makes the clamp prone to loosening and can reduce the safety and effectiveness of the bonding and grounding system. The existing clamps should be replaced with ones that can properly secure the grounding electrode conductor and bonding jumpers into screw terminals. Further evaluation and repair by a licensed and competent electrical contractor is recommended.
It is recommended that all electrical receptacles in the bathrooms, unfinished basement areas, kitchen counters and islands, jetted tubs, laundry area, sump pumps, food waste disposers, garage, and all exterior locations that are not already GFCI protected, be upgraded to GFCI protected receptacles by a licensed and competent electrician in order to reduce the risk of electrical shock and injury.
It is further advised that any pre 2007 GFCI type receptacles be upgraded to Smart GFCI receptacles. Smart GFCI receptacles will not continue to allow electrical current if the on board trip mechanism is no longer functional, or if the receptacle is improperly wired. Smart GFCI receptacles are easily recognized by an on board LED status light.
Extinguished or otherwise inoperative luminaires (light bulbs) were noted during the inspection. All of the lighting in the structure should be made fully operational for the final walk-through so that the proper operation of all the lighting can be verified and differentiated from defective switches, fixtures, etc.
NOTE: Some exterior fixtures may be controlled by photocells that will only allow the lights to operate at night and operation of all exterior fixtures should be verified at the final walk-through prior to closing.
The evaluation of the low-voltage equipment in the home: alarm, communication, audiovisual, etc., is beyond the scope of the home inspection and should be performed by a qualified low-voltage electrical contractor. In order to reduce the potential for confusion and to reduce clutter around the home, any wiring, panels, cabinets, etc. for any equipment that is no longer in use should be removed.
No ground rod was not found outside, no ground rod was found Inside. A ground rod is recommended along with a plumbing ground to provide adequate grounding for the electrical system. Depending on when the home was built and the towns requirements, a ground rod may or may not be required. Recommend checking with town for local requirements and qualified electrician to assess further for safety and to meet the towns requirements.
In order to reduce the risk for electrical shock from inadvertent contact with exposed current carrying equipment and in order to contain molten copper created by high temperature arcing and sparking of energized wiring. One or more receptacles in the basement is missing a cover plate. It is recommended that all electrical connections be concealed inside covered metal junction boxes and cover plates be installed were needed.
A spot check of the battery operated emergency lighting system/s revealed one or more non-functioning units. It is strongly recommended that these critical life safety devices be regularly evaluated and repaired as needed by a qualified electrician.
It is recommended that the exterior electrical receptacles be provided with "in use" covers in order to reduce the risk for contact between energized electrical equipment and moisture. Such contact can result in arcing/sparking, shock, fire, etc.
PLUMBING SUPPLY, DRAINS, FIXTURES AND VENTS
POTABLE WATER SOURCE: Public
WATER SERVICE PIPING MATERIAL: Galvanized
MAIN WATER SHUT-OFF LOCATION: Interior - By water meter in basement
WATER DISTRIBUTION PIPING MATERIAL: Copper, Not Fully Visible
WATER PRESSURE AND FLOW: Unknown
PLUMBING WASTE SYSTEM: Public Sewer
PLUMBING WASTE PIPING MATERIAL: Cast iron, PVC, Not Fully Visible
WATER HEATER SIZE AND POWER SOURCE: 2 units, 90 Gallons, 100 Gallons
BTU OR WATT INPUT RATING: 199,000
WATER HEATER MANUFACTURER: Water Heater Statistical Service Life is 13 years., A.O. Smith, Rheem
APPROXIMATE AGE IN YEARS: 14 , 10
A video camera sewer scope is recommended. An evaluation of the plumbing vent stacks and sewer line below the ground is beyond the scope of this inspection. Due to the age and location of the building, a sewer scope is recommended to further evaluate the sewer line and the below ground connections between the building and the municipal sewer line. Sewer scopes are done using video cameras and can reveal the materials, condition and reliability of the sewer line. If that has been done recently, I recommend having a sewer scope performed.
✒
- It was reported that there have been back-up issues in the past.
- I would have the plumbing venting system evaluated during this additional inspection. Inspector observed blocked, deteriorating plumbing vent stacks which can cause inadequate venting.
The outside water shut-off, a.k.a. the 'buffalo box', was not located during the inspection. It is recommended that the municipal water utility be contacted for a 'locate and test' (usually a provided to the taxpayer as a free service) be provided so that the outside shut-off can be operated for repairs or in an emergency.
The exhaust pipe at the water heater is not properly configured or secured. This condition increases the risk for noxious fumes or carbon monoxide intrusion into the occupied space. It is strongly recommended that a qualified mechanical contractor should make the appropriate repairs needed and certify that the exhaust piping conforms to the manufacturer's installation requirements for proper venting.
A cover should be installed over the floor drain to prevent the entry of debris into the drain that could result in clogging.
The A.O.Smith water heater was observed to be leaking; Possibly is in need of replacement to prevent a interruption in the domestic hot water supply or water damage to the building materials from a catastrophic leak.
Approximate replacement cost $ 9,800.00 to 11,500.00
The discharge tube for the water heater temperature and pressure relief valve is incorrectly installed. The discharge tube should not have threaded fittings at the end of the tube as this risks the discharge being capped. Hire a licensed plumbing contractor to further evaluate and repair. Ideally, the discharge tube for a relief valve:
- Terminates to an exterior location or above a drain, though this is not always possible
- Terminates between 6 and 24-inches off the ground (UPC)
- Slopes to drain to prevent water pooling inside the discharge tube
- Is not made from pipe with an inside diameter less than 3/4 on an inch
- Is made from an approved supply piping material: copper, PEX, CPVC or galvanized steel
- Terminates to a visible location that can be monitored for leaks and discharges
- Does not have a threaded termination point which would prevent accidental capping of this important discharge
I recommend having this relief valve discharge tube further investigated and repaired as recommended by a licensed plumber.
Incoming main water line is galvanized steel and visible signs of corrosion are present. Recommend a qualified/licensed plumber evaluate and replace as needed.
INSULATION, VENTILATION, ATTICS, ETC.
ATTIC INSULATION & VAPOR RETARDERS: No Attic Access, Unable to Determine Whether or Not Insulation Is Present in the Walls and Ceilings
VENTILATION: Unknown
The existing cheap plastic vent and/or dryer dampers are cracked warped and/or missing slats and are open to the exterior which creates the potential for cold air to enter and condense on warmer interior components and for flying pests to enter the open dryer venting. In order to reduce the potential for corrosion and moisture related damage and unwanted visitors, all dryer and exhaust vent dampers on the exterior walls should be replaced with high-quality, gasketed, vent dampers.
NOTE: In order to ensure proper performance of the dryer vents, regular examination and cleaning of dryer vents is recommended.
The plenum venting appears inadequate for the square footage as well as the known poor airflow characteristics/placement of the installed vents noted. This can contribute to elevated energy costs, moisture related deterioration to roofing and/or structural framing, and reduced roof life. The ventilation should be improved by a qualified roofing contractor with a written ventilation calculation performed. The Inspection Firm recommends this type for increased performance: Aura Roof Vents
The inspector was unable to verify the presence or absence of thermal insulation in the walls or ceilings.
INTERIORS AND FINISHES
COUNTERTOPS/CABINETS: Unknown
Open gaps were noted in the basement ceiling that can allow smoke, carbon monoxide, and superheated gases to pass into other areas of the building in the event of a fire. In order to close off the gaps it is recommended that all openings be sealed with 5/8 drywall, intumescent foam or other appropriate fireproofing materials.
The interior walls, floors, ceiling, and trim have normal wear and tear. Interior blemishes or required repairs exist, some of which are omitted from this report and considered maintenance/basic wear-and-tear. A qualified drywall, plaster/painting contractor or handyman is recommended to repair these areas as needed for proper appearance. The photo/s are representative, not all inclusive, of repairs needed.
NOTE: Caulk/sealant is a temporary building material and will require relatively frequent repairs or replacement. The highest quality sealant affordable is recommended for improved service life.
FYI: Stairwells in older homes may not meet modern building standards of practice. The steps rise and run are often different and may be steeper. Height and width clearances required of modern homes may not be present and railings are often not up to today's standards. Upgrading stairs in some older homes can be difficult or impractical in some cases. The client should be aware some limitations may be present and care should be taken when traversing non standard stairs.
The existing handrails have open ends that project from the wall. Modern safety standards require that interior handrails be returned 90 degrees to the wall and in order to reduce the risk of snagging, falls and injuries and the handrails should be modified or replaced by a qualified carpenter or handyman.
The staircase was noted as being sloped/unlevel. This can be a result of settlement in the surrounding framing members over time. Without having direct access to the framing underneath, it is impossible to tell what is the cause without doing invasive inspection procedures.
WINDOWS, DOORS, SKYLIGHTS
The installation of high quality rubber bulb weatherstripping is recommended at the top and sides of the entry door/s. The installation of a weatherstripped threshold is recommended at the bottom of the building entry doors. These modifications will conserve energy, reduce cold drafts, and reduce noise levels inside the living space.
One or more window frames were noted to be detached, open, loose or bent. This is indicative of moisture, rodent, insect intrusion or biological growth to the interior wall structure.
OTHER
Due to the age of the building and the existence of multiple layers of paint, the possibility exists that lead based paint is present in one or more areas of the structure. Further evaluation by a qualified lead paint or environmental specialist is recommended. Occupants should assume that any painted surface in an older structure contains lead based paint and should be handled with all appropriate precautions.
Here is a link to a webpage from the EPA that provides answers to frequently asked questions regarding lead based paint: Lead Based Paint - Frequently Asked Questions
Prior to circa 1980, asbestos was in relatively common use in the building material industry. In order to reduce the potential for the spread of asbestos fibers throughout the residence, any aged building product in the structure of uncertain content that is being disturbed should first be evaluated by a qualified environmental remediation contractor or testing laboratory.
In order to determine if asbestos is present in these materials, it may be possible for the buyer/homeowner to carefully collect a small sample of the material/s to send to a lab for analysis.
Here is a link to a Chicago testing lab that may be able to perform this testing: Indoor Science Testing Lab
Here is a link to a Chicago suburban testing lab that may be able to perform this testing: UAS Laboratory Services
Large devices typically associated with rats were noted around the perimeter of the property and larger holes were noted near the building. Rats are extremely common in the City and typically attracted to waste and hidden nesting areas. Any areas that provide a safe haven for rats should be cleared of clutter that provides the ability for concealment and all waste should be kept in special waste containers.
The City of Chicago has a program to assist in controlling rats through a special waste container distribution program and via other means. Here is a link to the City's webpage that provides information regarding ongoing rat control: Rodent Control (Rodent Baiting)
The smoke detectors noted in the building appeared to be at or beyond the end of their service lives, typically taken to be 10 years for smoke detectors and 5 years for carbon monoxide detectors. It is recommended that the smoke detector and carbon monoxide detector systems be upgraded to reflect current life safety codes which include; smoke detectors on each level of living space, hard-wired 120 V smoke detectors that are interconnected in order to alarm simultaneously when any individual smoke detector responds, and carbon monoxide detectors at every level of living space. The installation of these critical life safety devices by a licensed and competent electrician is recommended.
Fire Extinguishers Need Servicing. There were missing or expired service tags on the fire extinguishers. It is recommend that all fire/ life safety devices be inspected and serviced as needed on an annual basis.
Reserve Study.