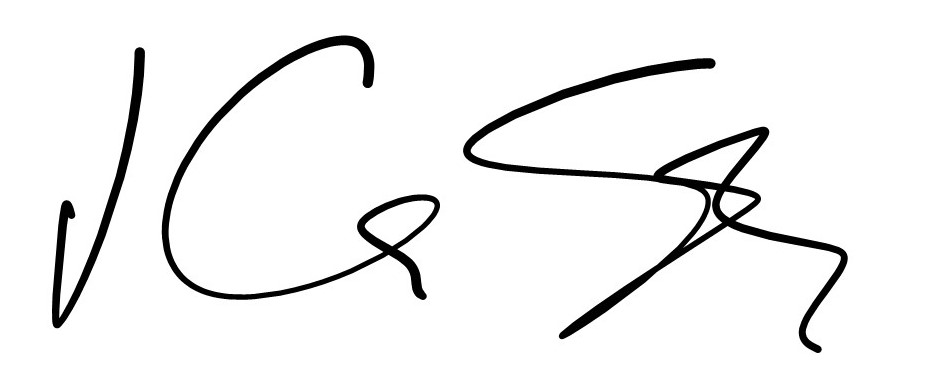
J. Chris Stanley, License #3380001762 (Exp 11/30/24)
The Scope and Purpose of a Home Inspection
Purchasing property involves risk
The purpose of a home inspection is to help reduce the risk associated with the purchase of a structure by providing a professional opinion about the overall condition of the structure. A home inspection is a limited visual inspection and it cannot eliminate this risk. Some homes present more risks than others. We cannot control this, but we try to help educate you about what we donât know during the inspection process. This is more difficult to convey in a report and one of many reasons why we recommend that you attend the inspection. This home inspection report will not reveal every condition that exists or ever could exist, but only those material defects that were observed on the day of the inspection.
A home inspection is not an insurance policy
This report does not substitute for or serve as a warranty or guarantee of any kind. Home warranties can be purchased separately from insuring firms that provide this service.
A home inspection is visual and not destructive
The descriptions and observations in this report are based on a visual inspection of the structure. We inspect the aspects of the structure that can be viewed without dismantling, damaging or disfiguring the structure and without moving furniture and interior furnishings. Areas that are concealed, hidden or inaccessible to view are not covered by this inspection. Some systems cannot be tested during this inspection as testing risks damaging the building. For example, overflow drains on bathtubs are generally not tested because if they were found to be leaking they could damage the finishes below. Our procedures involve non-invasive investigation and non-destructive testing which will limit the scope of the inspection.
This is not an inspection for code compliance
This inspection and report are not intended for city / local code compliance. During the construction process structures are inspected for code compliance by municipal inspectors. Framing is open at this time and conditions can be fully viewed. Framing is not open during inspections of finished homes, and this limits the inspection. All houses fall out of code compliance shortly after they are built, as the codes continually change. National codes are augmented at least every three years for all of the varying disciplines. Municipalities can choose to adopt and phase in sections of the codes on their own timetables. There are generally no requirements to bring older homes into compliance unless substantial renovation is being done.
This is a professional opinion
Construction techniques and standards vary. There is no one way to build a house or install a system in a house. The observations in this report are the opinions of the home inspector, based on training and experience. Other inspectors and contractors are likely to have some differing opinions. You are welcome to seek opinions from other professionals.
The scope of this inspection
The home inspection is conducting following the International Association of Certified Home Inspectors (InterNACHI) Standards of Practice which define the scope of the home inspection and what is required to be inspected. All items in the standards are inspected but may be reported in a section of the report under a different heading. It is recommended that you read the following link to fully understand the scope of the home inspection.
InterNACHI Standards Of Practice
This inspection will include the following systems: exterior, roof, structure, drainage, foundation, attic, interior, plumbing, electrical and heating. The evaluation will be based on limited observations that are primarily visual and non-invasive, and are not intended to be technically exhaustive. Although a home inspection evaluates the function of your home's systems and appliances, it cannot determine how long any particular system will last. Information regarding the typical expected life. expectancies of different home systems is available at the following link
Estimated Life Expectancy of Home Systems
Your expectations
The overall goal of a home inspection is to help ensure that your expectations are appropriate with the house you are proposing to buy. To this end we assist with discovery by showing and documenting observations during the home inspection. This should not be mistaken for a technically exhaustive inspection designed to uncover every defect with a building. Such inspections are available but they are generally cost-prohibitive to most homebuyers.
Your participation is requested
Your presence is requested during this inspection. A written report will not substitute for all the possible information that can be conveyed verbally by a shared visual observation of the conditions of the property.
How to Read This Report
Getting the Information to You
This report is designed to deliver important and technical information in a way that is easy for anyone to access and understand. If you are in a hurry, you can take a quick look at our "Summary Pageâ and quickly get critical information for important decision making. However, we strongly recommend that you take the time to read the full Report, which includes digital photographs, captions, diagrams, descriptions, videos and hot links to additional information.
The best way to get the layers of information that are presented in this report is to read your report online (the HTML version), which will allow you to expand your learning about your house. You will notice some words or series of words highlighted in blue and underlined â clicking on these will provide you with a link to additional information. The HTML version of this report also contains streaming videos. Short video clips often contain important information and critical context and sounds that can be difficult to capture in words and still pictures.
For the most reliable viewing experience, I recommend viewing the report on as large a screen as practical, as much detail can be lost on small devices like smart phones. For similar reasons, reports should only be printed in color to retain as much detail as possible and minimize misinterpretation of photographs.
This report can also be printed on paper or to a PDF document.
Chapters and Sections
This report is divided into chapters that parcel the home into logical inspection components. Each chapter is broken into sections that relate to a specific system or component of the home. You can navigate between chapters with the click of a button on the left side margin.
Most sections will contain some descriptive information done in black font. Observation narrative, done in colored boxes, will be included if a system or component is found to be significantly deficient in some way or if we wish to provide helpful additional information about the system or the scope of our inspection. If a system or component of the home was deemed to be in satisfactory or serviceable condition, there may be no narrative observation comments in that section and it may simply say âtested,â or âinspected.â
Observation Labels
All narrative observations are colored, numbered and labeled to help you find, refer to, and understand the severity of the observation. Observation colors and labels used in this report are:
- Repair:Repair and maintenance items noted during inspection. Please note that some repair items can be expensive to correct such as re-finishing hardwood floors, but are considered simply repair items due to their cosmetic nature.
- Recommended Maintenance:These are repair items that should be considered "routine home ownership items," such as servicing the furnace, cleaning the gutters or changing the air filters in the furnace.
- Improve:Observations that are not necessarily defects, but which could be improved for safety, efficiency, or reliability reasons.
- Monitor:Items that should be watched to see if correction may be needed in the future.
- Due Diligence:Observation such as a buried oil tank that may require further investigation to determine the severity and / or urgency of repair.
- Note:Refers to aside information and /or any comments elaborating on descriptions of systems in the home or limitations to the home inspection.
- Description:Detailed description of various aspects of the property noted during the inspection.
Summary Page
The Summary Page is designed as a bulleted overview of all the observations noted during inspection. This helpful overview is not a substitution for reading the entire inspection report. The entire report must be read to get a complete understanding of this inspection report as the Summary Page does not include photographs or photo captions.
Comments
Any comments/recommendations by the inspector regarding Major Concerns, Repairs, Maintenance, and Improvements suggests a second opinion or further inspection by a licensed contractor. All costs associated with further inspection fees and repair or replacement of item, component or unit should be considered before you purchase the property.
Summary
Repairs
- RGC-4 Roof, Gutters, and Chimneys:
The boots installed on plumbing vents were not properly fastened down on the lower edges. This condition may result in moisture intrusion into the roof sheathing and building materials beneath. At the time of inspection, no moisture was present in the sheathing. The Inspector recommends correction by a licensed contractor
- RGC-5 Roof, Gutters, and Chimneys:
The home had no roof drainage system to channel roof drainage away from the foundation. This condition can result in excessively high moisture levels in soil at the foundation. Excessive moisture levels in soil near the foundation can effect the ability of the soil to support the weight of the structure above. The Inspector recommends installation of a roof drainage system to help protect the home structure and occupants. All work to be performed by a licensed contractor
- A-4 Attic:
The attic floor insulation depth averaged approximately less than 6 inches. This condition will increase heating and cooling costs and reduce comfort levels and may contribute to ice damming of the roof during the winter. The Inspector recommends installing additional insulation to comply with local energy codes. All work should be performed by a licensed contractor.
- A-6 Attic:
Poorly-supported wires were visible in the attic at the time of the inspection. This indicates that wiring may have been installed by persons not qualified to perform the work. Non-workmanlike electrical work may contain hazardous defects. A full electrical inspection lies beyond the scope of the General Home Inspection, and the Inspector recommends evaluation by a licensed electrical contractor to ensure that safe conditions exist.
- G1-3 Grounds:
Tree roots had caused heaving to walkways, creating an uneven walking surface. This could be a trip hazard. The Inspector recommends correction by a licensed contractor
- DPB-1 Decks, Porches, and Balconies:
The supports for the front porch roof were nailed in place, and may not adequately support the roof over time. The Inspector recommends evaluation by a licensed contractor, with correction as directed
- ES-6 Electric Service:
Pointed screws (with sharp ends,) like wood screws, are not recommended to secure the dead-front cover to the electric panel as these can puncture wiring insulation. This is a potential safety hazard as shock or arc flashing may result. The Inspector recommends replacing the current sharp screws with the correct blunt screws for electrical panels. All work should be performed by a licensed electrical contractor
- EDFW-1 Electric Distribution and Finish Wiring:
The cover for an old fuse panel, now possibly used as a junction box, was loose at the time of inspection. The Inspector recommends correction by a licensed electrical contractor
- EDFW-3 Electric Distribution and Finish Wiring:
One or more receptacles in the home tested as not being properly grounded. This is a common condition in older buildings (prior to 1962) where three prong receptacles have been installed on an older two wire system. This creates a safety hazard as it appears receptacles are grounded for safety when they are not, and appliances that rely on an equipment ground to discharge a fault can be plugged into ungrounded circuits. This disables the important safety feature of an equipment ground. Proper repair can include:
- Running an equipment grounding conductor or a new three-wire circuit
- Replacing with two prong receptacles or
- Installing GFCI protection for this circuit and labeling the open ground receptacles
If GFCI protection is used, the outlets on this circuit should be labeled so it is clear they are protected.
The Inspector recommends evaluation of the home's receptacles by a licensed electrical contractor, with correction as directed
- P-2 Plumbing:
Functional flow problems were noted at some of the supply plumbing in this home- with water pressure reducing when multiple plumbing fixtures were operated at the same time (Ex. flushing the toilet while the shower is running.) The Inspector recommends evaluation by a licensed plumbing contractor, with repair if directed.
- P-6 Plumbing:
A PVC water line was present on the exterior, that was not properly protected by insulation. This water line may become damaged in colder months if the pipe freezes. The Inspector recommends installation of insulation or other method of protection from freezing, with work performed by a licensed contractor
- PB-2 Primary Bathroom:
The sink in the Primary Bathroom had a flexible drainpipe installed, which is improper and are often prone to clogging. The Inspector recommends removal of the flex drain, and installation of a correct drainpipe by a licensed plumber.
- PB-5 Primary Bathroom:
A gap was present at the bathtub spout, and the spout was loose. This condition may result in moisture intrusion in the wall behind. The Inspector recommends evaluation and correction by a licensed contractor
- K-3 Kitchen:
The kitchen sink had the hot and cold reversed. This condition may be due to the water supply lines being hooked up backward. This condition is considered a potential scald hazard, and the Inspector recommends correction by a licensed plumbing contractor
- K-7 Kitchen:
The range was not fastened to the floor. A child standing on the open oven door could overturn the range. This condition is a life-safety issue. The Inspector recommends installation of an approved anti-tip device (which is a small clip which secures the back foot to the floor), with work performed by a licensed contractor.
Recommended Maintenance Items
- RGC-2 Roof, Gutters, and Chimneys:
Portions of the roof had intersecting valleys or low slopes which trapped leaves and debris, causing accumulation on the asphalt shingle roof. Debris accumulation will speed deterioration by holding moisture next to the shingles, and in winter it may cause damage as the protective granules are lifted off as moisture expands when it freezes. The Inspector recommends having any accumulated debris cleared, with seasonal cleaning as necessary. All work to be performed by a licensed contractor
- HCFV-3 Heating, Cooling, Fireplaces, and Ventilation:
The heat pump system servicing the home responded to the thermostat when called and produced heat. The heat pump system could only be tested in heating mode, as it was too cold to test cooling. Generally, outdoor temperatures should exceed 65 degrees F for at least 24-hours prior to testing a system in cooling mode, or the exterior coils can be damaged. The Inspector recommends inspection and service by a licensed HVAC contractor to ensure proper operation and efficiency.
- LF-3 Laundry Facilities:
The dryer exhaust duct termination at the exterior of the building is covered with a screen. This is a potential safety hazard that could block lint and cause a fire. Given its location, being lower to the ground and possibly a pest entry point, the Inspector recommends monitoring with cleaning as necessary.
Improves
- A-5 Attic:
Water supply pipes visible in the attic space may be subject to freezing. The Inspector recommends pipe insulation be added by a licensed contractor
- CS-3 Crawl Space:
No insulation was installed in the unheated crawlspace. This condition will draw heat from the living space and increase heating costs. The Inspector recommends installation of thermal insulation in the main floor. All work should be performed by a licensed contractor.
- P-7 Plumbing:
Current safety standards recommend the installation of anti-siphon devices on all exterior hose bibs. The Inspector recommends installation of anti-siphon devices on both exterior hose bibs to conform with current standards and to ensure the home's water supply does not have backflow (contamination) from an exterior source.
- HCFV-4 Heating, Cooling, Fireplaces, and Ventilation:
The condensate line for the HVAC system is draining directly against the foundation. The Inspector recommends having it extended away from the foundation, with work performed by a licensed contractor
- LF-4 Laundry Facilities:
Foil or Mylar transition duct was noted in use to connect the dryer to the rigid vent. This product is generally UL listed for use with a dryer, however, most dryer manufacturers do not recommend it as it has proven to be unreliable and a potential fire hazard. Installation of a UL approved smooth-bore (rigid or flexible) metal duct is recommended, with work performed by a licensed contractor
Monitors
- P-5 Plumbing:
This water heater is likely close to the end of its useful service life. The average life of a water heater is statistically 10-15 years though in practice, they can vary widely between 8-20 years depending on water quality and maintenance schedule such as frequency of flushing the tank and replacing sacrificial anodes. Water was hot at the time of inspection. The Inspector recommends budgeting to replace this water heater at any time.
Due Diligences
- RGC-3 Roof, Gutters, and Chimneys:
The roofing material on this building appears to be a recently installed dimensional or architectural grade shingle. These are often rated as 30-year shingles. Often, the true lifespan of these shingles is usually closer to 20-25 years depending on the quality of the installation, the steepness of the roof and the amount of exposure. The Inspector recommends asking the seller for the contractor used and any warranties which may convey
- G1-4 Grounds:
Large trees were on the property, in close proximity to the home. Whenever large trees are located near a house a higher level of maintenance should be expected to keep trees safe and healthy, to eliminate the risks of damage to the home or building materials from falling limbs, and to eliminate rodent entry points. An arborist should be hired to further evaluate the large trees on the property and prune or remove as recommended.
- S-2 Structure:
Repairs were present in the crawlspace that appeared to be recent, and professionally done. The Inspector recommends asking the seller for any information regarding the repairs performed and the contractor used
- P-3 Plumbing:
A video camera sewer scope is recommended. An evaluation of the sewer line below the ground is beyond the scope of this inspection. Due to the age of the home, a sewer scope is recommended to further evaluate the sewer line and the below ground connections between the house and the municipal sewer line. Sewer scopes are done using video cameras and can reveal the materials, condition and reliability of the sewer line, and can reveal damage or defects.
- P-4 Plumbing:
No cleanout was noted for the sewer line. It is possible there is an accessible cleanout for the sewer line that is concealed behind finishes, belongings, or possibly underground in the yard. Sewer line cleanouts are necessary for clearing drain obstructions and for inspecting the building sewer with a sewer camera. The Inspector recommends asking the seller if one is present, and if not, it is recommended to have one installed as recommended by a licensed plumbing contractor. Please note that many older buildings do not have sewer line cleanouts; these are often added when sewer line work becomes necessary.
Notes
- A-2 Attic:
Roof trusses appeared to have been built on-site instead of being assembled in a manufacturing facility. This indicates that trusses were not designed, inspected or approved by a structural engineer. Trusses which lack proper engineering may be structurally inadequate and have the potential for serious structural failure. The trusses appeared to be adequately designed, built, and installed. Confirmation would require the services of a Structural Engineer.
- G1-5 Grounds:
Present on the property were structures in addition to the home that were not included as part of the General Home Inspection and were not inspected. The Inspector disclaims any responsibility for evaluating their condition.
- ES-5 Electric Service:
The main electrical disconnect is located in the service panel
đ The Complete Inspection Report
General Comments
Building Characteristics, Conditions and Limitations
Type of Building : Single Family (1 story)
Approximate Square Footage: 750
Approximate Year of Original Construction: 1954
Attending the Inspection: Buyer's Agent
Occupancy: Occupied
Animals Present: No
Weather during the inspection: Partly cloudy
Rained within the past 3 days?: Yes
Ground/Soil surface conditions: Damp
The Front Door Faces: Southeast
This home is older than 50 years and the home inspector considers this while inspecting. It is common to have areas that no longer comply with current code. This is not a new home and this home cannot be expected to meet current code standards. While this inspection makes every effort to point out safety issues, it does not inspect for code. It is common that homes of any age will have had repairs performed and some repairs may not be in a workmanlike manner. Some areas may appear less than standard. This inspection looks for items that are not functioning as intended. It does not grade the repair. Always consider hiring the appropriate expert for any repairs or further inspection.
This home was occupied at the time of inspection. Furniture and belongings may limit the visibility of flooring and walls, and may limit the testing of some receptacles, windows, doors, and inspection of some systems. All areas that could be accessed were inspected at the time of inspection. GFCI receptacles are not tested when a home is occupied, to protect any appliances, medical equipment, or electronics which may be plugged in.
Roof, Gutters, and Chimneys
Roof Materials
Method of Roof Inspection: Walked on roof
Roof Style: Gable
Roof Covering Materials: Architectural grade composition shingle
Flashings, Valleys and Penetrations: Inspected
Portions of the roof had intersecting valleys or low slopes which trapped leaves and debris, causing accumulation on the asphalt shingle roof. Debris accumulation will speed deterioration by holding moisture next to the shingles, and in winter it may cause damage as the protective granules are lifted off as moisture expands when it freezes. The Inspector recommends having any accumulated debris cleared, with seasonal cleaning as necessary. All work to be performed by a licensed contractor
The roofing material on this building appears to be a recently installed dimensional or architectural grade shingle. These are often rated as 30-year shingles. Often, the true lifespan of these shingles is usually closer to 20-25 years depending on the quality of the installation, the steepness of the roof and the amount of exposure. The Inspector recommends asking the seller for the contractor used and any warranties which may convey
Plumbing and Combustion Vents
The boots installed on plumbing vents were not properly fastened down on the lower edges. This condition may result in moisture intrusion into the roof sheathing and building materials beneath. At the time of inspection, no moisture was present in the sheathing. The Inspector recommends correction by a licensed contractor
Gutters and Downspouts
The home had no roof drainage system to channel roof drainage away from the foundation. This condition can result in excessively high moisture levels in soil at the foundation. Excessive moisture levels in soil near the foundation can effect the ability of the soil to support the weight of the structure above. The Inspector recommends installation of a roof drainage system to help protect the home structure and occupants. All work to be performed by a licensed contractor
Attic
Roof Framing and Sheathing
Framing Style: Trusses
Sheathing: Plywood
Roof trusses appeared to have been built on-site instead of being assembled in a manufacturing facility. This indicates that trusses were not designed, inspected or approved by a structural engineer. Trusses which lack proper engineering may be structurally inadequate and have the potential for serious structural failure. The trusses appeared to be adequately designed, built, and installed. Confirmation would require the services of a Structural Engineer.
Thermal Envelope
Insulation Type: Fiberglass
Approximate Insulation Depth (Attic):No Insulation
Less than 6 inches
6-8 inches
8-12 inches
12-14 inches
14-16 inches
The attic floor insulation depth averaged approximately less than 6 inches. This condition will increase heating and cooling costs and reduce comfort levels and may contribute to ice damming of the roof during the winter. The Inspector recommends installing additional insulation to comply with local energy codes. All work should be performed by a licensed contractor.
Attic- General Conditions
Poorly-supported wires were visible in the attic at the time of the inspection. This indicates that wiring may have been installed by persons not qualified to perform the work. Non-workmanlike electrical work may contain hazardous defects. A full electrical inspection lies beyond the scope of the General Home Inspection, and the Inspector recommends evaluation by a licensed electrical contractor to ensure that safe conditions exist.
Grounds
Drainage and Site
Site Description: Flat
Driveways/Walkways/Flatwork
Driveway: Gravel
Walkways: Concrete
Tree roots had caused heaving to walkways, creating an uneven walking surface. This could be a trip hazard. The Inspector recommends correction by a licensed contractor
Grounds, Trees and Vegetation
Trees/Vegetation too near building: Trees close to home
Large trees were on the property, in close proximity to the home. Whenever large trees are located near a house a higher level of maintenance should be expected to keep trees safe and healthy, to eliminate the risks of damage to the home or building materials from falling limbs, and to eliminate rodent entry points. An arborist should be hired to further evaluate the large trees on the property and prune or remove as recommended.
Decks, Porches, and Balconies
Exterior Siding, Doors, and Windows
Siding and Trim
Trim Material: Metal clad wood
Siding Material: Vinyl
Eaves
Vinyl- Vented soffit
Crawl Space
Crawl Space Access
Method of Inspection: Crawled
During inspection of the crawl space, every effort is made to inspect the entire space. Visual inspection of crawl spaces is difficult and limited as access is often restricted by pipes, ducts and sub-floor insulation as well as limited clearances.
Crawl Space Ventilation
Ventilation Method: Exterior wall vents
Insulation
Insulation Type: None noted
Structure
Foundation
Foundation Configuration: Crawl space
Foundation Method/Materials: Poured concrete footings
Main Floor Structure- Perimeter Bearing: Rests on top of foundation wall
Main Floor Structure- Intermediate Support: Built-up girder, Mortared-brick columns
Floor, Wall and Ceiling Framing
Wall Framing: Dimensional Lumber
Floor Framing: Dimensional lumber joists
Sub-Floor Material: Plywood
Ceiling Framing: Bottom cord of truss
Electric Service
Electrical Bonding System
Electric Service Equipment
Service Entrance (SE) conductor Size: Aluminum, 4/0, 200 amps
Main Panel Amperage: 200 amps
Electric Service Amperage: 200 amps
Main Electric Panel Location: Exterior
Panel Manufacturer: Square D
Pointed screws (with sharp ends,) like wood screws, are not recommended to secure the dead-front cover to the electric panel as these can puncture wiring insulation. This is a potential safety hazard as shock or arc flashing may result. The Inspector recommends replacing the current sharp screws with the correct blunt screws for electrical panels. All work should be performed by a licensed electrical contractor
Electric Distribution and Finish Wiring
Branch Wiring
Wire Material: Copper, Multi-strand Aluminum
Wiring Method: Non-metallic sheathed cable
Receptacles and Fixtures
Inspection Method: Tested All Accessible
During inspection The Inspector makes an effort to test and inspect all accessible electric receptacles and switches. In general, the scope of testing is directly related to access; where personal belonging and furniture obstruct access to receptacles and fixtures, fewer of them can be reasonably tested during inspection. All defects found during inspection will be listed in this report.
Electric Receptacles: Open Grounds in Old House
One or more receptacles in the home tested as not being properly grounded. This is a common condition in older buildings (prior to 1962) where three prong receptacles have been installed on an older two wire system. This creates a safety hazard as it appears receptacles are grounded for safety when they are not, and appliances that rely on an equipment ground to discharge a fault can be plugged into ungrounded circuits. This disables the important safety feature of an equipment ground. Proper repair can include:
- Running an equipment grounding conductor or a new three-wire circuit
- Replacing with two prong receptacles or
- Installing GFCI protection for this circuit and labeling the open ground receptacles
If GFCI protection is used, the outlets on this circuit should be labeled so it is clear they are protected.
The Inspector recommends evaluation of the home's receptacles by a licensed electrical contractor, with correction as directed
Ceiling Fans
Ceiling Fans: Present and Tested
The ceiling fans were tested and operating during inspection.
Plumbing
Water Service Supply
Pipe Material: Unknown- Not visible at the time of inspection
Water Supply: Public water
Distribution Pipe
Supply Pipe Materials: Copper
Functional Flow: Marginal
Functional flow problems were noted at some of the supply plumbing in this home- with water pressure reducing when multiple plumbing fixtures were operated at the same time (Ex. flushing the toilet while the shower is running.) The Inspector recommends evaluation by a licensed plumbing contractor, with repair if directed.
Sewage and DWV Systems
Discharge Type: Public Sewer - Buyer
Waste and Vent Pipe Materials: PVC, Possibly cast iron in the slab foundation
Location of Sewer Cleanout: Not Found
A video camera sewer scope is recommended. An evaluation of the sewer line below the ground is beyond the scope of this inspection. Due to the age of the home, a sewer scope is recommended to further evaluate the sewer line and the below ground connections between the house and the municipal sewer line. Sewer scopes are done using video cameras and can reveal the materials, condition and reliability of the sewer line, and can reveal damage or defects.
No cleanout was noted for the sewer line. It is possible there is an accessible cleanout for the sewer line that is concealed behind finishes, belongings, or possibly underground in the yard. Sewer line cleanouts are necessary for clearing drain obstructions and for inspecting the building sewer with a sewer camera. The Inspector recommends asking the seller if one is present, and if not, it is recommended to have one installed as recommended by a licensed plumbing contractor. Please note that many older buildings do not have sewer line cleanouts; these are often added when sewer line work becomes necessary.
Water Heater
System Type: Tank
Manufacturer: GE
Size: 40 gal
Age: 2010
Energy Source: Electricity
This water heater is likely close to the end of its useful service life. The average life of a water heater is statistically 10-15 years though in practice, they can vary widely between 8-20 years depending on water quality and maintenance schedule such as frequency of flushing the tank and replacing sacrificial anodes. Water was hot at the time of inspection. The Inspector recommends budgeting to replace this water heater at any time.
Water Temperature
Water Temperature Measured During Inspection: 118 Degrees F
Exterior Hose Bibs
Operating
A PVC water line was present on the exterior, that was not properly protected by insulation. This water line may become damaged in colder months if the pipe freezes. The Inspector recommends installation of insulation or other method of protection from freezing, with work performed by a licensed contractor
Current safety standards recommend the installation of anti-siphon devices on all exterior hose bibs. The Inspector recommends installation of anti-siphon devices on both exterior hose bibs to conform with current standards and to ensure the home's water supply does not have backflow (contamination) from an exterior source.
Heating, Cooling, Fireplaces, and Ventilation
Air Filters
Filtration Systems: Disposable
The heating and cooling system has disposable air filters installed. These should be changed quarterly or more to ensure proper air flow. Be sure to install the filters with the arrows pointing in the same direction as the air flow in the air handler.
Cooling Systems and Heat Pumps
Heat Pump Present
The following list is a minimum set of requirements to be expected of heat pump or air conditioning servicing. These are provided as a courtesy to show how involved proper HVAC maintenance service can be, and to encourage regular professional maintenance from a licensed HVAC contractor.
- Check compressor efficiency
- Check refrigerant level
- Clean the condenser coil
- Change or clean air filters
- Inspect contactors and wiring
- Inspect drive-sheaves, pulleys and belts
- Check and adjust for proper air flow
- Clean the blower motor as needed
- Lubricate all motors and shaft bearings
- Check, calibrate and program the thermostats and be sure the thermostat has adequate batteries as needed
- Check unit smoke detector, clean filter if applicable
- Check safety disconnect, laser-temp -- check across contacts
Manufacturer: Goodman
Age: 2009
The heat pump system servicing the home responded to the thermostat when called and produced heat. The heat pump system could only be tested in heating mode, as it was too cold to test cooling. Generally, outdoor temperatures should exceed 65 degrees F for at least 24-hours prior to testing a system in cooling mode, or the exterior coils can be damaged. The Inspector recommends inspection and service by a licensed HVAC contractor to ensure proper operation and efficiency.
The condensate line for the HVAC system is draining directly against the foundation. The Inspector recommends having it extended away from the foundation, with work performed by a licensed contractor
Heating and Cooling Distribution Systems
Heat Source in Each Room: Present
Distribution Method: Forced Air / Ducts
Interior
Floors and Floor Materials
Floor Materials: Carpet, Luxury Vinyl Plank
Floor Settlement: None noted
Walls, Ceilings, Trim, Hallways and Closets
Wall and Ceiling Materials: Drywall
Wall Insulation and Air Bypass
Wall Insulation: Not Visible
Interior Doors
Interior Doors: Hollow Core
Windows
Window Glazing: Double pane
Interior Window Frame: Vinyl
Window Styles: Double hung
Bedrooms
Primary Bedroom
Windows: Tested- Operational
Doors: Tested- Operational
Electric Switches and Receptacles: Tested- Operational
Walls and Ceilings: Inspected
Floors: Inspected
Primary Bathroom
Sinks and Cabinets
Tested
The sink in the Primary Bathroom had a flexible drainpipe installed, which is improper and are often prone to clogging. The Inspector recommends removal of the flex drain, and installation of a correct drainpipe by a licensed plumber.
Bathtub / Shower
Tested
A gap was present at the bathtub spout, and the spout was loose. This condition may result in moisture intrusion in the wall behind. The Inspector recommends evaluation and correction by a licensed contractor
Bathroom Ventilation
Type: Bath fan
Kitchen
Sinks and Faucets
Tested
The kitchen sink had the hot and cold reversed. This condition may be due to the water supply lines being hooked up backward. This condition is considered a potential scald hazard, and the Inspector recommends correction by a licensed plumbing contractor
Cabinets and Countertops
Countertop Material: Plastic laminate
Cabinet Material: Wood
Ranges, Ovens and Cooktops
Range/ Oven /Cook-tops: Electric, No Anti-Tip
The range was not fastened to the floor. A child standing on the open oven door could overturn the range. This condition is a life-safety issue. The Inspector recommends installation of an approved anti-tip device (which is a small clip which secures the back foot to the floor), with work performed by a licensed contractor.
Laundry Facilities
Dryer
Power Source: Electric
Exhaust Duct: Ducted to Exterior
The dryer exhaust duct termination at the exterior of the building is covered with a screen. This is a potential safety hazard that could block lint and cause a fire. Given its location, being lower to the ground and possibly a pest entry point, the Inspector recommends monitoring with cleaning as necessary.
Foil or Mylar transition duct was noted in use to connect the dryer to the rigid vent. This product is generally UL listed for use with a dryer, however, most dryer manufacturers do not recommend it as it has proven to be unreliable and a potential fire hazard. Installation of a UL approved smooth-bore (rigid or flexible) metal duct is recommended, with work performed by a licensed contractor