The Scope and Purpose of a Home Inspection
Purchasing property involves risk
Buying a home—whether for yourself, your family, or as an investment—is a major decision. It’s not just about money; it’s about where and how you’ll live. My role is to support you in this process by offering a clear, honest, and detailed look at the condition of the property on the day of the inspection.
This home inspection is a limited, visual review of the building. It’s designed to help you better understand what you’re buying, not to give you a guarantee or make the decision for you. Old homes, new builds, quirky spaces, and fixer-uppers all come with their own stories and surprises—and that’s okay. My job is to help you see the parts that are visible and raise awareness about what may be hidden, uncertain, or outside the inspection’s scope.
I believe that good decisions come from good information. You won’t hear “don’t worry” from me—I’ll give you what I see, what I know, and what I don’t. That includes moments where I simply don’t have full access or where something needs a specialist’s opinion. Whenever possible, I encourage you to attend the inspection. Being there gives you a richer, real-time understanding of the property that’s hard to capture fully in a written report.
Whether you’re buying your first home or your fifth, in Lisbon or Leiria, the goal is the same: make informed, confident decisions about where you’ll live, grow, or invest.
This report is prepared in accordance with the terms of your inspection agreement with SEGUNDOS AFAMADOS - LDA and reflects the conditions observed on the date of inspection.
A home inspection is not an insurance policy
A home inspection is not a warranty or insurance policy. It won’t protect you from future problems or guarantee that nothing will go wrong with the house. Think of it instead as a snapshot of the property’s condition on a specific day, taken by someone who knows what to look for.
A home inspection is visual and not destructive
The inspection is visual and non-invasive. That means I don’t move furniture, open walls, dismantle equipment, or disturb finishes. I inspect only what’s accessible and visible without causing damage. Some systems—like overflow drains or waterproofing—can’t be tested without risk to the structure and are therefore excluded from direct testing. Tools such as thermal cameras or moisture meters may be used to support these observations. These tools provide visual context only and are not calibrated instruments for diagnostic or certified measurements.
This is not an inspection for code compliance
In Portugal, like many countries, there is no single national standard for home inspections, and we don’t check for compliance with municipal building codes. Code compliance is something typically reviewed by licensed architects or municipal officials during the construction phase, not after the home is finished. Building codes also evolve frequently, and older homes are not required to meet the latest standards unless major renovations are done.
In short: this inspection won’t catch everything, and it’s not meant to. But it will give you grounded, expert feedback on what’s visible and noteworthy—and that can make a world of difference in your planning and decision-making.
This is just our opinion
Every house is a little different—each with its own quirks, history, and construction choices. There’s no single “correct” way to build or repair everything, and that’s part of what makes homes so unique.
This report reflects my professional opinion, based on 20+ years of experience restoring and evaluating properties. But it’s still just that—an informed opinion. Other inspectors or contractors might see things differently, and that’s okay. You’re always welcome to get second opinions, especially on complex systems or repairs.
What I offer is context and perspective. I don’t just note problems; I explain them. And when something’s uncertain, I’ll say so. That might mean recommending further evaluation by a specialist, or simply highlighting something that’s outside the scope of this inspection.
In the end, this report isn’t a checklist—it’s a conversation starter. It gives you the groundwork to make your next steps with clarity and confidence.
The scope of this inspection
This inspection includes a visual evaluation of the exterior, roof, structure, foundation, attic, interior spaces, plumbing, electrical, and heating systems. I also assess conditions related to indoor air quality and the potential for mold growth where relevant. In some cases, I use tools such as a moisture meter, thermal camera or other handheld testers to gather additional visual context. These tools assist in visual evaluation but are not used to deliver technical measurements, official diagnostics, or precise readings. Any findings based on these tools will be included in the report where applicable.
Only areas that are accessible and safe on the day of the inspection will be included. When more detailed analysis is necessary, I’ll note it and recommend appropriate follow-up.
For clients who request it, I offer floor plans as an additional service. These are for reference only and are not intended for permitting, renovation planning, or any official use.
Your expectations
The goal of this inspection is to help align your expectations with the home you’re planning to buy. No home is perfect—every property has a history, and part of my job is to give you a clear picture of what that looks like on the day of the inspection.
I aim to highlight what’s working, what might need attention, and what’s unknown. This isn’t about finding every flaw—it’s about helping you make an informed decision. If you’re expecting a checklist of every minor issue, this report won’t provide that. But if you’re looking for guidance grounded in experience and transparency, that’s exactly what this offers.
This process is about discovery. It’s about seeing the home with informed eyes so you can decide how it fits into your plans.
How to Read This Report
Getting the Information to You
This report is designed to be clear and approachable, even if you’re not familiar with construction terms. If you’re short on time, you can start with the Summary Page to quickly see the most important findings. Just keep in mind—it’s not a replacement for reading the full report.
The full report includes photos, captions, descriptions, and links to more information to help you understand what you’re seeing. Some words or phrases may be highlighted and underlined—clicking on these will take you to additional resources or definitions.
You’ll also notice the use of emojis throughout the report. These are visual markers meant to draw your attention to specific items—they are not used to indicate the severity of an issue. The true meaning of each observation is described in the associated text and clearly labeled with a severity modifier.
For the best experience, I recommend reading the report online. It’s interactive, easy to navigate, and allows you to dive deeper into any areas that matter most to you. You can also download it as a PDF, and if needed, I can provide a high-quality translation to Portuguese.
Chapters and Sections
This report is organized into chapters, each covering a major part of the home. Within each chapter, you’ll find sections that focus on specific systems or components—like the roof, plumbing, or electrical. This structure makes it easy to navigate and understand the findings.
You’ll see most sections begin with a brief description in standard text. If I’ve observed something notable—whether it’s a concern or just something worth explaining more—you’ll find a colored box with a narrative. These narratives are meant to help you understand not just what was seen, but what it might mean in context.
Observation Labels used for John
Observations are numbered, colored, and labeled for clarity. The labels follow a standard set of observation modifiers, which define the nature and severity of each observation. If something is functioning as expected, the report may simply note “tested” or “inspected,” and no further comment will be needed.
Detailed description of various aspects of the property noted during the inspection.
Summary Page
The Summary Page at the front of the report gives you a quick overview of the key findings. It’s a helpful tool for fast reference, but it’s not a substitute for reading the full report. The summary doesn’t include photo captions or detailed context, so for a full understanding, be sure to explore the full report.
Summary
Critical Issues
- ES-3 Electric Service:
Flammable materials stored near electrical panel – Paint cans and other flammable liquids were observed stored inside a cabinet that also contains the main electrical panel. This poses a potential fire hazard and is not recommended. Combustible materials should be stored away from electrical equipment to reduce the risk of ignition in the event of a short circuit or overheating. Relocation of these materials to a safe, ventilated storage area is advised.
Safety or Major Repairs
- RACG-2 Roof, Attics, Chimney and Gutters:
"MANSARD" ROOF COVERING CONDITIONS
There were issues documented below in bulleted lists, narratives, and/or pictures related to the roof surface that should be evaluated and replaced by a qualified roofing contractor. The pictures below document some of the concerns related to this roof and should not be construed to mean there are no other conditions that need to be addressed. Hidden damage is common with roofs. I recommend factoring replacement of the roof as soon as practical
SINGLE-PLY CONCERNS:
- Roof covering past expected life. A full evaluation/repair of underlying surfaces is recommended and proper repairs made as deemed necessary. Some amount of hidden damage should be anticipated.
- Evidence of less than professional installation
GENERAL CONDITIONS:
- Temporary repair material being used in a permanent manner
- Less than professional repairs
- Paint and coating deterioration visible on all surfaces of mansard roof covering
- ES-2 Electric Service:
RCD BREAKER:
There were issues documented below in bulleted lists, narratives and pictures related to the RCD breakers to the property that should be evaluated, repaired and maintained as deemed necessary by a licensed electrical contractor. Additional issues should be anticipated and uncovered during repairs.
SELT TEST:
- ⚠️ Self-test not attempted — the RCD’s self-test function was not engaged during the inspection. Regular testing is essential to ensure safety; it’s recommended to perform this test periodically as per manufacturer guidelines.
BREAKER RATING:
- Breaker rated above 30 mA – acceptable only for specific applications (e.g., 100 mA for fault protection or 300 mA for fire protection); verify correct application
🛑 Safety 🔨Repair
- EDFW-3 Electric Distribution and Finish Wiring:
RCD INFORMATION:
There were issues related to the RCD's. These bulleted lists, narratives and/or pictures document some of those concerns, but not likely all of them. I recommend evaluation by the licensed electrical contractor in the context of other electrical repairs at the home. Observations/recommendations/issues include:
RCD'S CONCERNS:
- Receptacle failed High.During RCD testing, failure is indicated by a red screen. The receptacle failed to trip at the standard 30 mA threshold, indicating either an excessively high tripping value or a complete lack of proper RCD functionality. This malfunction suggests that the protective device is not operating within its specified limits, which compromises electrical safety. Immediate evaluation and corrective action by a qualified electrician are recommended to ensure proper operation and compliance with safety standards.
🛑 Safety 👁🗨 Monitor ➕ Upgrade
- BIDS-1 Building Interiors, Doors and Stairs:
BUILDING INTERIORS:
Concerns noted below in bulleted lists, narratives and/or pictures related to the interior spaces of the home should be evaluated, maintained, and repaired as deemed necessary by the appropriate qualified party.
LOFTS:
- ◽Ceiling height under structural elements less than 2.1 meters – Structural beams, girders, or ductwork should allow at least 2.1 meters of clearance beneath.
- ◽Ceiling height less than 2.5 meters – For habitable rooms, the minimum required ceiling height is 2.5 meters. In circulation areas or non-habitable rooms (such as storage), reduced heights may be acceptable down to 2.2 meters.
- ◽No natural light or ventilation – All habitable rooms must have windows or other natural openings providing natural light and cross ventilation, with a minimum glazed area of 1/8 the floor area of the room.
- Loft guard not adequate – Any platform or edge with a drop should include a secure guardrail at a height of at least 90 cm for safety.
- BIDS-2 Building Interiors, Doors and Stairs:
SHARP EDGES ON LATHE: A section of interior stucco cladding has been intentionally removed to expose the underlying wooden lathe as a design feature. While the work appears to be carefully executed with sealed transitions, some of the exposed wood slats are broken or have sharp edges. Care should be taken to ensure that exposed materials do not pose safety or maintenance concerns. Edges should be smoothed and protected to minimize risk
Repair or Replace
- RACG-1 Roof, Attics, Chimney and Gutters:
ATTIC AREA CONDITIONS: There were issues documented below in bulleted lists, narratives, and/or pictures related to the roof and attic area components that should be evaluated and repaired as deemed necessary by a qualified party.
ROOF INSULATION:
- Thermal bridging noted – Structural elements not covered by insulation (e.g., concrete beams) create cold spots, increasing energy loss and condensation risk. These are often observable via infrared imaging or visible staining.
FIBERGLASS BATTS:
- Out of place – batts have shifted from original position, leaving gaps and creating thermal bridges
- Voids – observable gaps between insulation batts or structural elements; may cause cold spots and energy inefficiency
🔧 Maintenance (as needed) 👁🗨 Monitor
- ES-1 Electric Service:
ELECTRICAL SERVICE EQUIPMENT:
There were issues documented below in bulleted lists, narratives and/or pictures related to the electrical service equipment that should be evaluated or repaired as deemed necessary by the licensed electrical contractor.
SERVICE CONDUCTORS:
- MULTIPLE SERVICE CONDUCTORS INSTALLED — A larger ampacity rated wire was installed and remains unused in the panel
PANEL CONDITION:
- Missing breaker knockouts – openings should be properly covered with manufacturer-specific filler plates
- Multiple wires on breakers – double tapping where manufacturer does not allow
MULTIPLE LUGS:
- Improper Hot Terminal Connections – Multiple wires connected to a single terminal; though common, using dedicated junction terminals is safer and more compliant
- Multiple Lugging of Neutral Wires — more than one neutral conductor terminated under a single lug is only allowed if the lug is explicitly rated by the manufacturer for that use and the conductor sizes are appropriate; this installation should be corrected unless compliance can be verified by a licensed electrician
- Multiple Lugging of Ground Wires — more than one equipment grounding conductor (EGC) under a single lug is acceptable only when the lug is rated for multiple conductors and the wire types/sizes conform to regulations; improper terminations should be corrected
- EDFW-1 Electric Distribution and Finish Wiring:
RECEPTACLE OUTLET CONDITIONS:
There were issues documented below in bulleted lists, narratives and/or pictures related to the receptacles in the home:
UNGROUNDED 3-PRONG RECEPTACLES:
- Some 3-prong receptacles tested ungrounded – Select locations lacked functional grounding; others appeared compliant ; None of the receptacles in the kitchen appeared to have a ground wire
RECEPTACLE GENERAL CONDTION:
- Electrical receptacles painted over – One or more electrical outlets were observed to have been painted, which can interfere with proper contact, conceal damage, or make future servicing more difficult.
I recommend evaluation and repairs by a licensed electrical contractor. Other similar conditions should be anticipated.
- EDFW-2 Electric Distribution and Finish Wiring:
LIGHTING OUTLET CONDITIONS:
There were issues documented below in bulleted lists, narratives and/or pictures related to the lighting components in the home including:
STORAGE LIGHTING:
- Partially exposed incandescent bulbs.
- Temporary lights used as primary means of illumination.
SWITCHES:
- Switch damage – Painted switches are affecting the functionality of mechanism
While the pictures below document some of these concerns, I recommend all lighting locations be evaluated and repaired as deemed necessary by a licensed electrical contractor.
- K-1 Kitchen:
KITCHEN SINKS/COUNTERTOPS/CABINETS:
There were issues documented below in bulleted lists, narratives and/or pictures related to the Kitchen sink, countertops, and cabinets:
SINK CONCERNS:
- SINK NOT PROPERLY CAULKED AT CONNECTION WITH COUNTERTOP – hygiene concern due to unsealed edges
- PRESENT WATER LEAKS UNDER SINK IN CABINET EVIDENT – visible signs of leakage
DRAINAGE:
- TRAP/COMPONENTS NOT PROFESSIONALLY INSTALLED – trap shape, seal, and arm must be to standard with listed components and proper venting
- CORRUGATED TRAP/DRAIN COMPONENTS PRESENT – prone to clogging and poor flow
CABINET CONCERNS:
- Cabinet Face or Door misalignment - uneven separation in the gap between cabinet components.
I recommend evaluation and repair by a qualified party.
- LF-1 Laundry Facilities:
FLOORS/WALLS/CEILINGS/CLOSETS:
There were issues documented below in bulleted lists, narratives and/or pictures related to the ceilings:
WALL/CEILING CONCERNS;
- Cracks in glass ceiling panels – may effect moisture entry
I recommend evaluation by a qualified party as desired.
- B-2 Bathrooms:
BATHROOM SINKS/COUNTERTOPS/CABINETS:
There were issues documented below in bulleted lists, narratives and/or pictures related to the sink, cabinets and countertops:
DRAINAGE:
- CORROSION ON CHROME TRAP EVIDENT – indicates wear or past leaks
- TRAP/COMPONENTS NOT PROFESSIONALLY INSTALLED – trap shape, seal, and arm must be to standard with listed components and proper venting
- CORRUGATED TRAP/DRAIN COMPONENTS PRESENT – prone to clogging and poor flow
- CORRUGATED DRAIN DOES NOT CONTAIN P-TRAP– corrugated line is connected directly to wall drain resulting in a missing p-trap that could allow sewer gas to enter the room
I recommend evaluation and improvements by a licensed plumber.
Recommended Improvements
- ED-1 Exteriors and Decks:
EXTERIOR DOOR CONDITIONS:
There were issues documented below in bulleted lists, narratives and/or pictures related to the exterior doors of the home. All should be evaluated, repaired and maintained as deemed necessary by a qualified door installation contractor or other qualified party.
DOOR CONDITIONS:
- Condos — responsibility for exterior doors not determined, recommend discussing with Condo Association
JAMB/OPENING:
- Mechanical damage to trim/jamb — combined damage to both components
WEATHER-STRIPPING CONDITION:
- Weather-stripping missing at bottom — recommend installation
THRESHOLD WEATHER-STRIPPING:
- No bottom weather-stripping present — not required in all cases, but recommended for energy efficiency and moisture protection l
Concerns will be documented in the pictures below but should not be construed to be all inclusive but instead more representative:
- BIDS-3 Building Interiors, Doors and Stairs:
FLOORS:
There were issues documented below in bulleted lists, narratives and/or pictures related to the floors:
WOOD FLOORING:
- Exposed nail heads observed – presents safety hazard; proper setting and patching recommended
- Patching or repairs noted – inlay or fill consistent with past damage or alteration
CONSTRUCTION:
- Sloped floor sections observed – uneven floor plane may relate to framing deflection or prior settlement consistent with other structures of this building age
Wood Destroying Insects:
- Evidence of past damage from
- Woodworm — general term for beetle larvae boring into wood, causing widespread tunneling
I recommend evaluation, repairs and maintenance by a qualified party as desired.
- BIDS-4 Building Interiors, Doors and Stairs:
STAIR CONDITIONS:
There were issues documented below in bulleted lists, narratives and/or pictures related to the stairs that indicate the need for evaluation, repairs and maintenance by a qualified stair installation contractor.
CONDO STAIRS:
- ◽Discuss with the Condo Association to your satisfaction.
STAIR RISERS:
- Evidence of past damage from
- Woodworm — general term for beetle larvae boring into wood, causing widespread tunneling
METAL:
- Paint failure on guard components — increases vulnerability to weathering and moisture damage
🔨Repair
- B-1 Bathrooms:
FLOORS/WALLS/CEILINGS/CLOSETS:
There were issues documented below in bulleted lists, narratives and/or pictures related to the floors/walls and ceilings:
WALL/CEILING CONCERNS;
- Mechanical damage present – punctures, scrapes, or dents to wall or ceiling finishes
- Ceiling/wall cracks consistent with truss uplift – separation where ceiling meets interior wall
I recommend evaluation, repairs and maintenance by a qualified party as desired.
- IC-1 Indoor Climate:
INDOOR AIR QUALITY:
There were issues documented below in bulleted lists, narrative notes, and/or pictures related to indoor air quality that may indicate environmental or mechanical concerns. These conditions suggest the need for evaluation, repair, or improvement by a qualified indoor air quality specialist or building systems contractor. I recommend that appropriate corrective action be taken based on the findings before continued or extended occupancy, particularly for sensitive individuals such as children, the elderly, or those with respiratory conditions.
PM2.5 /PM10:
- PM2.5 peak reading __25 µg/m³__
- PM10 peak reading ___37 µg/m³_
- PM2.5 threshold is 25 µg/m³
- PM10 threshold is 50 µg/m³
POTENTIAL SOURCES:
- Pollen and dust from open windows – Especially during spring or dry seasons
- Construction or renovation dust – Tiling, stucco, or masonry work indoors
CONTRIBUTING FACTORS:
- Lack of windows on opposing walls – Building layout limits cross-ventilation capability
CORRECTIONS or RECOMMENDATIONS:
- Create cross-breeze paths – Open windows on opposing walls when outdoor air is clean
CO (CARBON MONOXIDE):
- CO Peak Reading: ___0__ppm
CO₂ (Carbon Dioxide)
- CO₂ Peak Reading: __521_ppm
- CO₂ Threshold: 1250 ppm
TVOC (Total Volatile Organic Compounds):
- TVOC Peak Reading: _____.17____ppm
- TVOC Protection Threshold: .16 ppm
POTENTIAL SOURCES:
- Adhesives, sealants, and paints – Especially in recently renovated or rented units; products may release VOCs for weeks after application.
- Cleaning and disinfecting products – Strong-smelling cleaners used in kitchens and bathrooms, often stored indoors without sealed containment.
- New furniture or textiles – Upholstered furniture, rugs, and curtains may off-gas VOCs, particularly when unboxed or recently installed.
CONTRIBUTING FACTORS:
- Recent renovation or redecorating – New paint, floors, or finishes noted without increased ventilation.
- Storage of VOC-emitting products indoors – Paint cans, solvents, or adhesives stored in utility or living spaces.
CORRECTIONS or RECOMMENDATIONS:
- Ventilate spaces after renovations – Open windows and run fans for extended periods post-installation.
- Store chemicals outside conditioned spaces – Keep solvents, paints, and other VOC sources in garages or sealed cabinets.
HCHO (Formaldehyde):
- HCHO Peak Reading: _.02_____ppm
- Protection Threshold: 0.08 ppm
The Full Report
Electric Distribution and Finish Wiring
Branch Wiring
Wiring Photo Bucket
Electrical Distribution and Finish Wiring Observations
Plumbing
Supply Plumbing
Supply Plumbing Photo Bucket
Water Heater
Water Heater Photo Bucket
Water Heater Observations
General Comments
Building Characteristics, Conditions and Limitations
Style of Home: Pombaline (Pombalino 🇵🇹), urban housing
Type of Building : Row House/Townhouse (Moradia em Banda 🇵🇹)
Approximate Year of Original Construction: Historic Period: (1910–1919)
Reported Area: 88m2 x2
Reported Energy Class: Not Reported
Reported Bedrooms: T1
Reported Bathrooms: 1
Attending the Inspection: Owner
Personal Belongings Present: Yes
Occupancy: Occupied
Animals Present: No
Weather during the inspection: Partly Cloudy
Approximate temperature during the inspection: 20°C to 25°C
Last Measurable Rain : more than one month
Front Façade Orientation: North (Norte 🇵🇹)
Pre-2004 Structures: Lead
Homes constructed prior to 1962 in Portugal likely contain lead-based paints, both interior and exterior. While lead in paints was significantly restricted starting in 1962, materials already in use remained in place, and some exposure risk may still exist, particularly where paints are deteriorating or disturbed. Lead is not considered hazardous when it is intact and not friable (i.e., not chipping or airborne), but deteriorating surfaces can pose health concerns.
Lead was common in paints, lead supply piping, glazes of old bathtubs, brass fixtures, galvanized pipes (zinc has small amounts of lead) and numerous other building materials. The acidity of the water is an important factor in how much lead is leached from plumbing fixtures and pipes.
As Portugal aligned with European Union directives in the 1980s and 1990s, including those on drinking water quality and construction products, the use of lead was further restricted. Notably, the REACH Regulation and the Drinking Water Directive set limits on the allowable levels of lead in plumbing and consumer materials, effectively eliminating its use in modern construction.
It is advisable to maintain painted surfaces in good condition and avoid sanding or stripping old paint unless proper lead-safe practices are followed. When remodeling or removing old materials, professional evaluation and handling are recommended to minimize lead exposure risks.
Regardless the date, there is no guarantee houses after this date do not have lead.
Pre-1999 Structures: Abestos
Homes constructed prior to 2005 in Portugal may contain asbestos in various building materials, including roofing panels, insulation, floor tiles, pipe insulation, and certain textured wall or ceiling coatings. Asbestos is not considered a health risk when intact and undisturbed, but it becomes hazardous if the material is damaged or deteriorates, releasing fibers into the air. Inhalation of asbestos fibers can cause serious health problems, including asbestosis, mesothelioma, and lung cancer. It is strongly recommended not to disturb suspected asbestos-containing materials. If renovations or repairs are planned, especially in older homes, a licensed professional should evaluate the materials and, if necessary, conduct testing and removal in accordance with applicable safety regulations. For safety, materials suspected of containing asbestos should be left intact and encapsulated unless professional removal is required.
Grounds
Grounds Information
Walkway Composition: Calçada
Calçada is a traditional style of Portuguese paving made from limestone pieces arranged in intricate, decorative patterns. Commonly seen in historic city centers, sidewalks, and public plazas, calçada is celebrated for its aesthetic appeal and cultural significance. However, maintaining calçada requires regular attention. Over time, weather conditions can cause the stones to shift or become uneven, and the joints between stones may deteriorate, leading to gaps or weed growth. Periodic cleaning is necessary to remove dirt, moss, and algae that can accumulate, while occasional re-leveling and repointing are recommended to restore its original appearance and ensure the durability of the pavement.
Walkway Information: Uneven or shifting surfaces
Uneven or shifting surfaces can create significant safety hazards. When the surface becomes irregular, it may lead to tripping hazards for pedestrians and can also cause damage to vehicles, compromising overall accessibility.
Grounds Limitations and Exclusions: Common Ones
A Standard Home Inspection does not include evaluation of elements such as outbuildings, fencing, and planters. Evaluation of these elements, if present, may be warranted, any comments made or made as a courtesy, whether done verbally or included in the written report.
The following limitations and exclusions were noted:
THE FOLLOWING LIMITATIONS AND EXCLUSIONS WERE NOTED:
- Building is built to assumed property corners
HOMEOWNER ASSOCIATION RELATED:
- ◽In this instance all or most of these elements would be deferred to the Condo Association as well.
Exteriors and Decks
Info for Exteriors and Decks
Trim Material: Granite
Siding Material: Stucco
Eaves: Parapet wall
Exterior Doors: Solid Core
Exterior of Windows: Metal
Window opening types: Tilt and Turn
Deck, Porches, Balconies: Narrow Balcony
Guardrail: Wrought Iron Railings
Decking materials: Tile Over Membrane
Limitations/Exclusions Related to Exteriors: Present
The following limitations and exclusions were noted related to the exterior of the home;
EXTERIORS LIMITATIONS:
- Most of exterior difficult to assess due to proximity to adjacent buildings
- Some components not included in this inspection
HOMEOWNER ASSOCIATION:
- Some components deferred to Condo Association
Exterior and Deck Observations
EXTERIOR DOOR CONDITIONS:
There were issues documented below in bulleted lists, narratives and/or pictures related to the exterior doors of the home. All should be evaluated, repaired and maintained as deemed necessary by a qualified door installation contractor or other qualified party.
DOOR CONDITIONS:
- Condos — responsibility for exterior doors not determined, recommend discussing with Condo Association
JAMB/OPENING:
- Mechanical damage to trim/jamb — combined damage to both components
WEATHER-STRIPPING CONDITION:
- Weather-stripping missing at bottom — recommend installation
THRESHOLD WEATHER-STRIPPING:
- No bottom weather-stripping present — not required in all cases, but recommended for energy efficiency and moisture protection l
Concerns will be documented in the pictures below but should not be construed to be all inclusive but instead more representative:
Roof, Attics, Chimney and Gutters
Roof info
Method of Roof Inspection: Viewed from pole camera
Roof Style: Mansard
Roof Structure: Timber, Dimensional Lumber
Roof Covering Materials: Marseilles Tiles (flat), Single-Ply membrane
Flashings: Present and Visually Standard, Mortar Flashing
Approximate Age of Roof Covering: Unknown
Gutters and Downspouts: Plastic, Built-in at eaves
Roof Inspection Limitations / Exclusions: Includes attic spaces
This report provides an opinion of the general condition of the roof system based on a visual inspection of representative areas. The inspector does not offer an opinion or warranty as to whether the roof leaks or is subject to future leakage.
- Water stains on ceilings, walls, and soffits that tested dry at the time of inspection may test elevated for moisture under other conditions or at another time.
- Specific notation of leakage or stains does not preclude additional areas of leakage and/or hidden damage. Monitor attic for any changes; ongoing or questionable situations should be assessed and corrected. Leakage can lead to Mold or Mold-like/Fungal Growth.
- It is common for there to be multiple layers of different kinds of insulation in the attic. It is possible for hidden layers to be discovered especially when the attics could not be inspected. The following limitations were present:
LIMITATIONS TO INSPECTION OF ROOF/STRUCTURES:
- Not walked on
- Some components not included in this inspection
- Lichen growth in some areas
HOMEOWNER ASSOCIATION:
- Some components deferred to Condo Association
Roof, Attic, Chimney and Gutter Observations
ATTIC AREA CONDITIONS: There were issues documented below in bulleted lists, narratives, and/or pictures related to the roof and attic area components that should be evaluated and repaired as deemed necessary by a qualified party.
ROOF INSULATION:
- Thermal bridging noted – Structural elements not covered by insulation (e.g., concrete beams) create cold spots, increasing energy loss and condensation risk. These are often observable via infrared imaging or visible staining.
FIBERGLASS BATTS:
- Out of place – batts have shifted from original position, leaving gaps and creating thermal bridges
- Voids – observable gaps between insulation batts or structural elements; may cause cold spots and energy inefficiency
🔧 Maintenance (as needed) 👁🗨 Monitor
ROOF GENERAL CONDITIONS:
There were issues documented below in bulleted lists, narratives, and/or pictures related to the roof. I recommend evaluation and routine maintenance of the roof by a the Condo Association or other appropriate parties. Conditions related to specific types of roof coverings will be discussed below. The conditions should not be construed to be all inclusive but instead more representative:
NOT INSPECTED/TRAVERSED:
- Roof NOT walked on
MOSS/LICHEN/ALGAE:
- Lichen colonization – Lichen formations noted on tile surfaces, which can penetrate and deteriorate the tile material over time.
- Maintenance Recommendations:
- Regular inspections – Conduct periodic roof inspections to identify and address early signs of biological growth.
- Cleaning protocols – Employ appropriate cleaning methods to remove moss, lichen, and algae without damaging tiles.
- Ensure proper drainage – Keep gutters and downspouts clear to prevent water accumulation on the roof.
"MANSARD" ROOF COVERING CONDITIONS
There were issues documented below in bulleted lists, narratives, and/or pictures related to the roof surface that should be evaluated and replaced by a qualified roofing contractor. The pictures below document some of the concerns related to this roof and should not be construed to mean there are no other conditions that need to be addressed. Hidden damage is common with roofs. I recommend factoring replacement of the roof as soon as practical
SINGLE-PLY CONCERNS:
- Roof covering past expected life. A full evaluation/repair of underlying surfaces is recommended and proper repairs made as deemed necessary. Some amount of hidden damage should be anticipated.
- Evidence of less than professional installation
GENERAL CONDITIONS:
- Temporary repair material being used in a permanent manner
- Less than professional repairs
- Paint and coating deterioration visible on all surfaces of mansard roof covering
Electric Service
Electric Service Main Panel
Service Power: Single-Phase Service Amperage Options (4.6 kVA (~20A))
Service Entrance: Below Grade
Main Panel Amperage Rating: 40A
Main Electric Panel Location: Kitchen
Panel Manufacturer: Hager
RCD breaker: labeled all
Electrical System Limitations/Exclusions: Panel Information
The following conditions limited inspection of the electrical system:
HOMEOWNER ASSOCIATION:
- Some components deferred to Condo Association
Main Panel Photo Bucket
Main Panel Observations
ELECTRICAL SERVICE EQUIPMENT:
There were issues documented below in bulleted lists, narratives and/or pictures related to the electrical service equipment that should be evaluated or repaired as deemed necessary by the licensed electrical contractor.
SERVICE CONDUCTORS:
- MULTIPLE SERVICE CONDUCTORS INSTALLED — A larger ampacity rated wire was installed and remains unused in the panel
PANEL CONDITION:
- Missing breaker knockouts – openings should be properly covered with manufacturer-specific filler plates
- Multiple wires on breakers – double tapping where manufacturer does not allow
MULTIPLE LUGS:
- Improper Hot Terminal Connections – Multiple wires connected to a single terminal; though common, using dedicated junction terminals is safer and more compliant
- Multiple Lugging of Neutral Wires — more than one neutral conductor terminated under a single lug is only allowed if the lug is explicitly rated by the manufacturer for that use and the conductor sizes are appropriate; this installation should be corrected unless compliance can be verified by a licensed electrician
- Multiple Lugging of Ground Wires — more than one equipment grounding conductor (EGC) under a single lug is acceptable only when the lug is rated for multiple conductors and the wire types/sizes conform to regulations; improper terminations should be corrected
RCD BREAKER:
There were issues documented below in bulleted lists, narratives and pictures related to the RCD breakers to the property that should be evaluated, repaired and maintained as deemed necessary by a licensed electrical contractor. Additional issues should be anticipated and uncovered during repairs.
SELT TEST:
- ⚠️ Self-test not attempted — the RCD’s self-test function was not engaged during the inspection. Regular testing is essential to ensure safety; it’s recommended to perform this test periodically as per manufacturer guidelines.
BREAKER RATING:
- Breaker rated above 30 mA – acceptable only for specific applications (e.g., 100 mA for fault protection or 300 mA for fire protection); verify correct application
🛑 Safety 🔨Repair
Flammable materials stored near electrical panel – Paint cans and other flammable liquids were observed stored inside a cabinet that also contains the main electrical panel. This poses a potential fire hazard and is not recommended. Combustible materials should be stored away from electrical equipment to reduce the risk of ignition in the event of a short circuit or overheating. Relocation of these materials to a safe, ventilated storage area is advised.
Electric Distribution and Finish Wiring
Branch Wiring
Wire Material: Copper
Wiring Method: Non-metallic sheathed cable
Receptacles Outlets: Some tested, Three wire receptacles
Light fixtures present: Yes
Lighting Outlets: Some tested
Surge Protection:Point of use
Door Bell : Door Actuator
Electrical System Limitations/Exclusions: RCD requirements
Wiring Photo Bucket
Electrical Distribution and Finish Wiring Observations
RECEPTACLE OUTLET CONDITIONS:
There were issues documented below in bulleted lists, narratives and/or pictures related to the receptacles in the home:
UNGROUNDED 3-PRONG RECEPTACLES:
- Some 3-prong receptacles tested ungrounded – Select locations lacked functional grounding; others appeared compliant ; None of the receptacles in the kitchen appeared to have a ground wire
RECEPTACLE GENERAL CONDTION:
- Electrical receptacles painted over – One or more electrical outlets were observed to have been painted, which can interfere with proper contact, conceal damage, or make future servicing more difficult.
I recommend evaluation and repairs by a licensed electrical contractor. Other similar conditions should be anticipated.
LIGHTING OUTLET CONDITIONS:
There were issues documented below in bulleted lists, narratives and/or pictures related to the lighting components in the home including:
STORAGE LIGHTING:
- Partially exposed incandescent bulbs.
- Temporary lights used as primary means of illumination.
SWITCHES:
- Switch damage – Painted switches are affecting the functionality of mechanism
While the pictures below document some of these concerns, I recommend all lighting locations be evaluated and repaired as deemed necessary by a licensed electrical contractor.
RCD INFORMATION:
There were issues related to the RCD's. These bulleted lists, narratives and/or pictures document some of those concerns, but not likely all of them. I recommend evaluation by the licensed electrical contractor in the context of other electrical repairs at the home. Observations/recommendations/issues include:
RCD'S CONCERNS:
- Receptacle failed High.During RCD testing, failure is indicated by a red screen. The receptacle failed to trip at the standard 30 mA threshold, indicating either an excessively high tripping value or a complete lack of proper RCD functionality. This malfunction suggests that the protective device is not operating within its specified limits, which compromises electrical safety. Immediate evaluation and corrective action by a qualified electrician are recommended to ensure proper operation and compliance with safety standards.
🛑 Safety 👁🗨 Monitor ➕ Upgrade
Plumbing
Supply Plumbing
Water Supply: Public water
Meter: Located at, behind front door
Main Water Shut-off: Meter
Functional Water Flow: Average
Exterior Hose Bibs: None found
Water Filters: Present
Supply Plumbing Photo Bucket
WATER SYSTEMS LOCATED IN BUILDING
Water Heater
System Type: Tank
Age: Recent replacement
Multi-function safety valve: Present
Water Temperature: Testing Note
Having plenty of hot water is not just a convenience, it is considered a necessity in modern homes. However, there are competing concerns related to having plenty of hot water. On the one hand we want to prevent scalding. On the other hand it is a good idea to keep water hot enough to prevent water-borne bacteria from flourishing. It is actually quite complicated to accomplish both goals with storage-tank type water heaters.
What about scaling?
In areas with hard water, temperatures above 49°C can increase scaling inside the tank resulting in damage to heating elements anode rods etc. Installation of water softening equipment on the system prior to the heater is recommended to prevent this damage. On-demand heaters are especially vulnerable to scaling and could increase the frequency of flushing.
Water Heater Photo Bucket
Water Heater Observations
WATER TEMPERATURE CONDITIONS:
Water temperature control in homes is very important to reduce the risk of scalding/burns. I recommend monitoring of the conditions below, as deemed necessary.
WATER TEMPERATURE CONTROL:
- Standards generally expect hot water delivery between 45°C and 49°C (113–120°F), and never above 49°C at the fixture.
Drainage Plumbing
Drains/Vents
Waste Pipe and Venting: Public Sewer
Waste and Vent Pipe Materials: Not visible
Location of Sewer Clean-out: Bathroom floor
Fuel Storage and Distribution
General Comments
Gas Meter: None noted
Gas shut-off Location: Near Interior Entry door
Miscellaneous Plumbing Limitations and Exclusions: Present
The following limitations and exclusions related to the plumbing of the home were noted:
GAS METER:
- Not Installed
- No gas appliances were found
GAS SHUT OFF TO:
- Meter
Heating, Cooling, Fireplaces and Ventilation
Heating System
Heat Source in each room: Not found
Heating/Cooling Limitations and Exclusions: Present
Carbon Monoxide Detectors: None located
Smoke Alarms: None Located
Room directly heated:Living room
No direct heat source found:Kitchen
All Bathrooms
All Bedrooms
HVAC Photo Bucket
Portable appliances not included in inspection – Portable air conditioning units and plug-in electric heaters are not considered part of the permanently installed heating or cooling systems and are therefore excluded from the scope of this inspection. Any photos or mentions of such appliances are for reference only and do not represent an evaluation of their performance, condition, or safety.
Building Interiors, Doors and Stairs
Floors, Walls, Ceilings, Trim and Closets
Floor coverings: Hardwood, Tile
Wall/Ceiling Finishes: Plaster, Brick
Stairs and Railings: Non-standard, Standard
Interior doors: Present
Interior Observations
BUILDING INTERIORS:
Concerns noted below in bulleted lists, narratives and/or pictures related to the interior spaces of the home should be evaluated, maintained, and repaired as deemed necessary by the appropriate qualified party.
LOFTS:
- ◽Ceiling height under structural elements less than 2.1 meters – Structural beams, girders, or ductwork should allow at least 2.1 meters of clearance beneath.
- ◽Ceiling height less than 2.5 meters – For habitable rooms, the minimum required ceiling height is 2.5 meters. In circulation areas or non-habitable rooms (such as storage), reduced heights may be acceptable down to 2.2 meters.
- ◽No natural light or ventilation – All habitable rooms must have windows or other natural openings providing natural light and cross ventilation, with a minimum glazed area of 1/8 the floor area of the room.
- Loft guard not adequate – Any platform or edge with a drop should include a secure guardrail at a height of at least 90 cm for safety.
SHARP EDGES ON LATHE: A section of interior stucco cladding has been intentionally removed to expose the underlying wooden lathe as a design feature. While the work appears to be carefully executed with sealed transitions, some of the exposed wood slats are broken or have sharp edges. Care should be taken to ensure that exposed materials do not pose safety or maintenance concerns. Edges should be smoothed and protected to minimize risk
FLOORS:
There were issues documented below in bulleted lists, narratives and/or pictures related to the floors:
WOOD FLOORING:
- Exposed nail heads observed – presents safety hazard; proper setting and patching recommended
- Patching or repairs noted – inlay or fill consistent with past damage or alteration
CONSTRUCTION:
- Sloped floor sections observed – uneven floor plane may relate to framing deflection or prior settlement consistent with other structures of this building age
Wood Destroying Insects:
- Evidence of past damage from
- Woodworm — general term for beetle larvae boring into wood, causing widespread tunneling
I recommend evaluation, repairs and maintenance by a qualified party as desired.
STAIR CONDITIONS:
There were issues documented below in bulleted lists, narratives and/or pictures related to the stairs that indicate the need for evaluation, repairs and maintenance by a qualified stair installation contractor.
CONDO STAIRS:
- ◽Discuss with the Condo Association to your satisfaction.
STAIR RISERS:
- Evidence of past damage from
- Woodworm — general term for beetle larvae boring into wood, causing widespread tunneling
METAL:
- Paint failure on guard components — increases vulnerability to weathering and moisture damage
🔨Repair
WALLS AND CEILINGS:
There were issues documented below in bulleted lists, narratives and/or pictures related to the ceilings:
WALL/CEILING CONCERNS;
- Unevenness in wall or ceiling finish – surface not flush; may relate to framing, settling, or poor finishing, consistent with other structures of this age
- Mechanical damage present – punctures, scrapes, or dents to wall or ceiling finishes
- Evidence of prior repairs – patches, color mismatch, or retexturing visible
CEILING CONCERNS:
- Exposed ceiling lathe may permit unfiltered airflow from loft areas – This condition can introduce dust and particulate matter into the living space, potentially affecting indoor air quality and cleanliness.
I recommend evaluation, repairs and maintenance by a qualified party as desired.
INTERIOR DOORS:
All of the interior doors show minimal wear-and-tear associated with the age and use of the home. Adjustments and maintenance should be anticipated as normal for all doors. I recommend repairs by a qualified party as warranted. The bulleted lists, narratives and/or pictures below document some of these conditions:
Kitchen
Kitchen Info
Floor/Wall/Ceilings Coverings: Tile, stucco
Sinks: tested
Ventilation method: Fan Ducted to Exterior
Refrigerator: Operating, Filter Noted
Range/cooktop: Electric
Microwave: Functioned
Ovens: Functioned
Kitchen Observations
KITCHEN SINKS/COUNTERTOPS/CABINETS:
There were issues documented below in bulleted lists, narratives and/or pictures related to the Kitchen sink, countertops, and cabinets:
SINK CONCERNS:
- SINK NOT PROPERLY CAULKED AT CONNECTION WITH COUNTERTOP – hygiene concern due to unsealed edges
- PRESENT WATER LEAKS UNDER SINK IN CABINET EVIDENT – visible signs of leakage
DRAINAGE:
- TRAP/COMPONENTS NOT PROFESSIONALLY INSTALLED – trap shape, seal, and arm must be to standard with listed components and proper venting
- CORRUGATED TRAP/DRAIN COMPONENTS PRESENT – prone to clogging and poor flow
CABINET CONCERNS:
- Cabinet Face or Door misalignment - uneven separation in the gap between cabinet components.
I recommend evaluation and repair by a qualified party.
Laundry Facilities
Laundry Info
Washer: Not tested
Dryer: Not tested
Dryer Exhaust: Ductwork Not Visible
Laundry Ventilation: Operable window
Laundry Limitations/Exclusions: Laundry General Information
Evidence of past leaks under laundry sinks is common. While I endeavor to verify current leaks at the time of inspection sometimes leaks are incidental or due to specific uses not duplicated at the time of inspection. Monitoring of moisture conditions under sinks should be a normal part of routine home maintenance. The following limitations and exclusions were noted related to the laundry:
LAUNDRY LIMITATIONS:
- Washer not operated. Washing machines are not operated in the course of the home inspection, and if their operation is important to you, I recommend function be demonstrated during your final walk-through.
- Dryer not operated. Dryers are not operated in the course of the home inspection, and if their operation is important to you, I recommend function be demonstrated during your final walk-through.
BELONGINGS/STORAGE/FURNISHINGS/STAGING:
- Belongings/storage limited inspection
Laundry Observations
Bathrooms
Bathroom info
Floor/Wall/Ceilings Coverings: Tile, Stucco
Sinks & Cabinets: Tested
Toilet: Tested
Shower: Tested
Bathroom Ventilation: Not Present
Bathroom Observations
FLOORS/WALLS/CEILINGS/CLOSETS:
There were issues documented below in bulleted lists, narratives and/or pictures related to the floors/walls and ceilings:
WALL/CEILING CONCERNS;
- Mechanical damage present – punctures, scrapes, or dents to wall or ceiling finishes
- Ceiling/wall cracks consistent with truss uplift – separation where ceiling meets interior wall
I recommend evaluation, repairs and maintenance by a qualified party as desired.
BATHROOM SINKS/COUNTERTOPS/CABINETS:
There were issues documented below in bulleted lists, narratives and/or pictures related to the sink, cabinets and countertops:
DRAINAGE:
- CORROSION ON CHROME TRAP EVIDENT – indicates wear or past leaks
- TRAP/COMPONENTS NOT PROFESSIONALLY INSTALLED – trap shape, seal, and arm must be to standard with listed components and proper venting
- CORRUGATED TRAP/DRAIN COMPONENTS PRESENT – prone to clogging and poor flow
- CORRUGATED DRAIN DOES NOT CONTAIN P-TRAP– corrugated line is connected directly to wall drain resulting in a missing p-trap that could allow sewer gas to enter the room
I recommend evaluation and improvements by a licensed plumber.
Indoor Climate
Climate Info
Indoor climate concerns, such as condensation, humidity, and ventilation, are often influenced by seasonal changes and occupant behavior. While I make observations using tools such as thermal imaging and moisture meters, this is not a comprehensive environmental or air quality analysis. Some conditions—such as intermittent condensation or periods of poor airflow—may not be present or detectable at the time of inspection. Factors like the use of shutters, heating equipment, exhaust fans, or window ventilation routines can significantly affect interior conditions.
No long-term monitoring of humidity, ventilation performance, or airflow patterns is performed. Moisture meters are used in select accessible areas only. This inspection does not include laboratory air sampling, mold testing, or HVAC airflow measurements.
INDOOR CLIMATE LIMITATIONS:
- Single-day inspection – Conditions represent only the moment of the inspection and may not reflect long-term or seasonal trends.
- No continuous environmental monitoring – Temperature, relative humidity, or dew point values were not tracked over time.
- No invasive inspection – Ceilings, walls, and floors were not opened or probed beyond accessible surfaces.
- Thermal imaging is limited – Results may be affected by insulation quality, lighting, or surface temperature variability.
- Moisture meter usage is spot-checked – Readings were taken only in accessible, relevant areas and cannot represent entire surfaces or wall assemblies.
- Furniture and personal belongings – Items such as wardrobes, shelving, and curtains may block visible signs of condensation, mold, or dampness.
- No air sampling performed – No lab-based mold or air quality testing was conducted as part of this inspection.
- Ventilation systems were not performance-tested – No airflow volume, balance, or extraction efficiency was measured.
- Occupant behavior affects readings – Window usage, heating practices, and moisture-producing activities (e.g., laundry, cooking) may distort readings.
- No assessment of airtightness – Door and window seal quality, infiltration, and passive ventilation pathways were not pressure-tested or modeled.
- Weather may influence findings – Rain, temperature, and sunlight conditions may impact surface readings and interior comfort during the inspection.
This indoor air quality (IAQ) assessment aims to provide insight into the presence of airborne substances that may influence the health, safety, and comfort of building occupants. PM2.5 refers to fine particulate matter smaller than 2.5 microns, which can penetrate deep into the lungs and is often produced by combustion sources like cooking, smoking, or outdoor pollution. PM10 includes larger particles such as dust, pollen, and mold fragments that may cause irritation or trigger allergies. Formaldehyde (HCHO) is a volatile organic compound commonly released from pressed wood products, furniture, and construction materials; it is a known respiratory irritant and potential carcinogen. Total Volatile Organic Compounds (TVOCs) represent a group of chemical pollutants emitted from products like paints, cleaning agents, and air fresheners, some of which may cause headaches, dizziness, or longer-term effects with chronic exposure.
Carbon monoxide (CO) is a colorless, odorless gas produced by incomplete combustion—typically from stoves, heaters, or vehicles—and can be dangerous even at low concentrations. Carbon dioxide (CO₂), while not directly harmful in typical residential concentrations, is a key indicator of indoor ventilation quality; elevated levels suggest insufficient fresh air exchange. Radon is a radioactive gas that seeps from soil and rock into basements and lower levels of buildings; long-term exposure is a leading cause of lung cancer in non-smokers. Together, these measurements form a broad picture of the air’s chemical and particulate composition, offering an early indication of potential environmental concerns.
This indoor air quality assessment is intended as a preliminary screening based on instantaneous, localized measurements taken with portable instrumentation. While care has been taken to ensure accuracy, results may vary depending on environmental conditions at the time of inspection, including ventilation, temperature, occupancy, and recent activity. The data collected does not substitute for long-term monitoring, laboratory-grade testing, or specialized evaluations for medical or regulatory compliance. This report does not constitute a health diagnosis nor a certification of air safety. Where elevated readings are observed, further investigation or consultation with an indoor environmental professional is recommended. No guarantee is made regarding ongoing conditions after the time of inspection.
Moisture accumulation is one of the most frequent and complex concerns observed in Portuguese residential buildings, particularly those built prior to modern insulation and ventilation standards. The country’s naturally humid climate, especially in coastal and river valley regions, combined with prolonged rainy winters and poor indoor air exchange, creates a persistent risk for dampness and condensation-related problems. Buildings with concrete frames and masonry infill, common throughout the country, often lack continuous insulation or vapor barriers, allowing warm indoor air to cool rapidly against exterior walls and create surface condensation. This is especially pronounced on north-facing façades, which receive less sunlight and tend to remain cooler throughout the year.
In winter, heating in isolated rooms or intermittent climate control results in temperature differentials across the building envelope, further encouraging condensation in underheated bedrooms, storage areas, and wardrobes. During summer, windows may remain closed for air conditioning or security reasons, limiting natural ventilation and allowing humidity to accumulate, particularly in homes without mechanical ventilation systems. Moisture can also enter the building from ground contact areas (such as basements or slab-on-grade foundations) due to capillary action or hydrostatic pressure in older or poorly drained structures.
In addition to environmental and structural factors, common sources of indoor moisture include poorly ventilated bathrooms, kitchens, and laundry rooms, where steam and vapor remain trapped due to a lack of extraction systems. Deficiencies in flashing, exterior façades, roof membranes, or plumbing systems may also introduce water into wall cavities and finish materials. Without proper ventilation and drying, these moisture-prone areas are ideal environments for mold development, material degradation, and reduced indoor comfort. Identifying the source of moisture through non-invasive tools like thermal imaging and moisture meters is a critical first step in preventing long-term damage and restoring healthy indoor conditions.
This assessment is based on visual inspection, environmental conditions at the time of evaluation, and readings taken using a pinless moisture meter and thermal imaging camera. It is intended as a non-invasive screening tool to identify potential areas of concern. Conditions may vary depending on seasonal weather, occupant habits, and future changes to building use or ventilation. This report does not constitute a mold or structural diagnosis, nor does it guarantee that all sources of moisture have been identified. Where concerns persist or significant anomalies are detected, further investigation by a qualified contractor or indoor environmental specialist is recommended.
Environmental Observations
INDOOR AIR QUALITY:
There were issues documented below in bulleted lists, narrative notes, and/or pictures related to indoor air quality that may indicate environmental or mechanical concerns. These conditions suggest the need for evaluation, repair, or improvement by a qualified indoor air quality specialist or building systems contractor. I recommend that appropriate corrective action be taken based on the findings before continued or extended occupancy, particularly for sensitive individuals such as children, the elderly, or those with respiratory conditions.
PM2.5 /PM10:
- PM2.5 peak reading __25 µg/m³__
- PM10 peak reading ___37 µg/m³_
- PM2.5 threshold is 25 µg/m³
- PM10 threshold is 50 µg/m³
POTENTIAL SOURCES:
- Pollen and dust from open windows – Especially during spring or dry seasons
- Construction or renovation dust – Tiling, stucco, or masonry work indoors
CONTRIBUTING FACTORS:
- Lack of windows on opposing walls – Building layout limits cross-ventilation capability
CORRECTIONS or RECOMMENDATIONS:
- Create cross-breeze paths – Open windows on opposing walls when outdoor air is clean
CO (CARBON MONOXIDE):
- CO Peak Reading: ___0__ppm
CO₂ (Carbon Dioxide)
- CO₂ Peak Reading: __521_ppm
- CO₂ Threshold: 1250 ppm
TVOC (Total Volatile Organic Compounds):
- TVOC Peak Reading: _____.17____ppm
- TVOC Protection Threshold: .16 ppm
POTENTIAL SOURCES:
- Adhesives, sealants, and paints – Especially in recently renovated or rented units; products may release VOCs for weeks after application.
- Cleaning and disinfecting products – Strong-smelling cleaners used in kitchens and bathrooms, often stored indoors without sealed containment.
- New furniture or textiles – Upholstered furniture, rugs, and curtains may off-gas VOCs, particularly when unboxed or recently installed.
CONTRIBUTING FACTORS:
- Recent renovation or redecorating – New paint, floors, or finishes noted without increased ventilation.
- Storage of VOC-emitting products indoors – Paint cans, solvents, or adhesives stored in utility or living spaces.
CORRECTIONS or RECOMMENDATIONS:
- Ventilate spaces after renovations – Open windows and run fans for extended periods post-installation.
- Store chemicals outside conditioned spaces – Keep solvents, paints, and other VOC sources in garages or sealed cabinets.
HCHO (Formaldehyde):
- HCHO Peak Reading: _.02_____ppm
- Protection Threshold: 0.08 ppm
INTERIOR MOISTURE:
Moisture-related conditions were evaluated using thermal imaging, non-invasive moisture meter readings, and visual inspection. Depending on environmental conditions and observed building features, signs of potential or active moisture intrusion were identified. These issues may be seasonal in nature or ongoing and are influenced by both environmental humidity and building design or maintenance. Where elevated readings, staining, or mold-like material is present, or if conditions suggest hidden or structural moisture, further evaluation by a qualified moisture remediation contractor to determine the source and appropriate corrective measures.
0% moisture content is an ideal level for interiors, 1-2% is typically what is seen. Moisture content levels as low as 6% can create paint failure issues and wide spread internal wall damage should be expected when moisture content exceeds 20%.
OBSERVED MOISTURE:
- No visible signs of moisture were present at the time of inspection-
- Conditions were dry and consistent with seasonal expectations, though some risk factors remain.
Foundation
Foundation Info
Foundation Description: On Grade
Method of Inspection: No access
Basement Limitations/Exclusions: Present
LIMITATIONS TO INSPECTION OF THE FOUNDATION:
- Some components not included in this inspection
HOMEOWNER ASSOCIATION:
- Components deferred to Condo Association
Layout
Floor plans
Floor Plans: provided
FLOOR PLANS:
A floor plan was generated during the inspection using a combination of 3D scanning technology and laser-assisted measurement tools. The layout reflects the visible configuration and estimated internal dimensions of the property at the time of inspection. All primary rooms and circulation areas were accessible and included in the measured layout.
The resulting plan is not certified for legal, cadastral, or permitting purposes and should be used for informational and planning reference only. All dimensions are approximate and may vary slightly based on wall finishes, measurement tolerances, or scanning line-of-sight. Clients requiring official square footage or property area certification should consult with a licensed architect, engineer, or surveyor.
Measured interior dimensions of 75m²
Reported vs Measured: present
REPORTED vs OBSERVED:
The reported interior area and number of rooms for this property were sourced from the information provided by the client. These figures are often used for public disclosure, financing, or valuation purposes but may not reflect as-built conditions or subsequent modifications.
GENERAL OBSERVATIONS:
- Discrepancies in layout or use – Notable differences found between reported and observed dimensions or room functions.
- Evidence of undocumented upgrades – Finishes or construction elements suggest changes made after initial approval or registration.
REPORTED AREA:
- Reported Gross Area (Área Bruta Total): ___88_ m²
- Reported Usable Interior Area (Área Útil Interior): __132__ m²
- Measured Usable Interior Area (Área Útil Interior): __75__ m²
LOFT:
- ☐ Irregular ceiling heights limit full inclusion of the space under standard usable area criteria
- ☐ The Loft layout may not be reflected in official documentation or included in the recorded floor area
- ☐ The loft is being used as a functional room but is not included in the reported usable interior area
Invoice -- The Full Report
Flat inspection | $1.00 |
Tax at 23.0%: | $0.23 |
$1.23 | |
DUE |
Ajuda Home Inspections
Avenida Alexandre Herculano Nº56
SEGUNDOS AFAMADOS - LDA NIPC 518659895
Pinhal Novo, Setubal 2955-112
+351 963 514 613
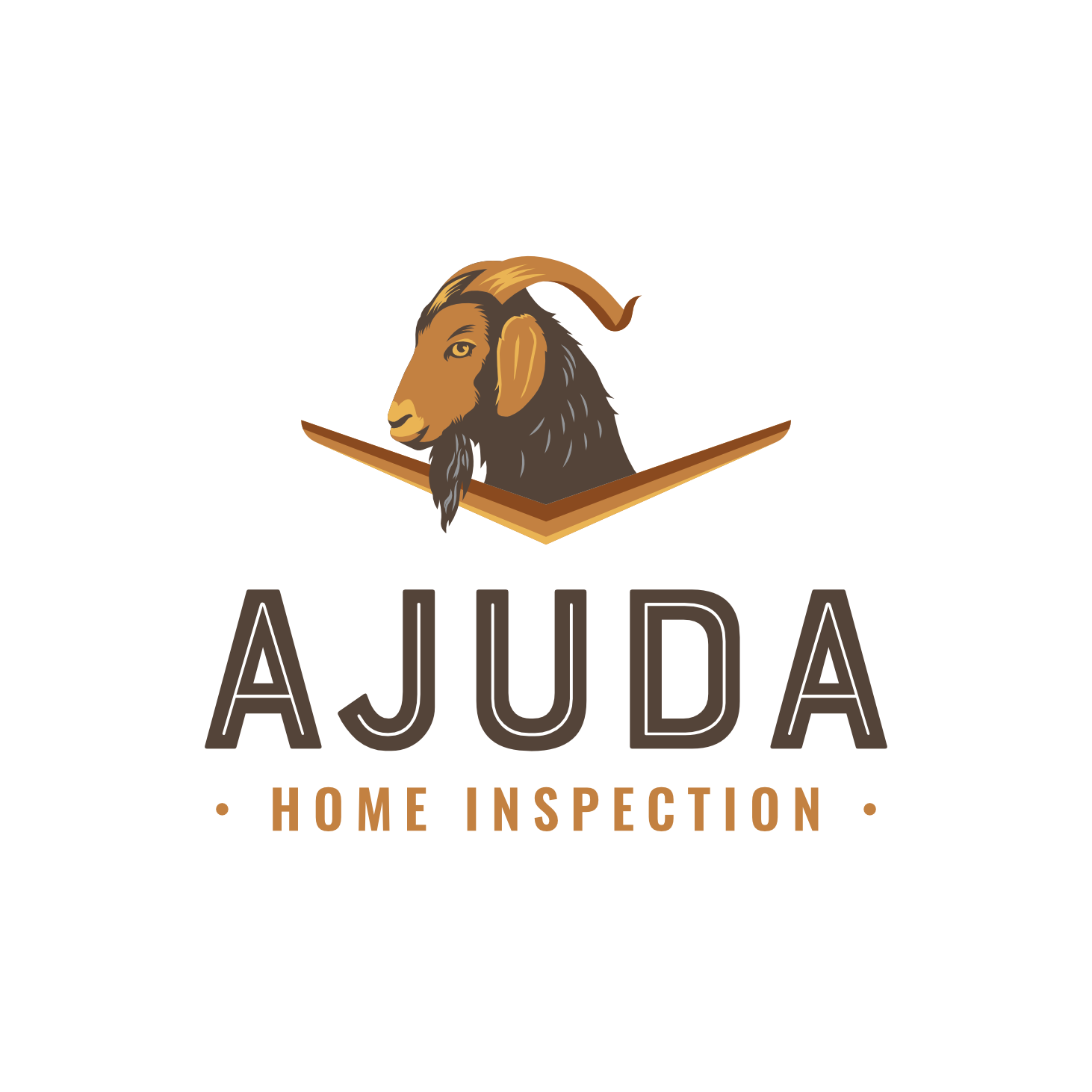