The Scope of a Home Inspection
This inspection includes the following systems: exterior, roof, structure, drainage, foundation, attic, interior, plumbing, electrical and heating. The evaluation is based limited observations that are primarily visual and non-invasive. This inspection and report are not intended to be technically exhaustive.
A home inspection is visual and not destructive
We inspect the aspects of the structure that can be viewed without dismantling, damaging, or disfiguring the structure and without moving furniture and interior furnishings. Areas that are concealed, hidden or inaccessible to view are not covered by this inspection. Some systems cannot be tested during this inspection as testing risks damaging the building. For example, overflow drains on bathtubs are generally not tested because if they were found to be leaking they could damage the finishes below. Our procedures involve non-invasive investigation and non-destructive testing which will limit the scope of the inspection.
This is not an inspection for code compliance
This inspection and report are not intended for city / local code compliance. All houses fall out of code compliance shortly after they are built, as the codes continually change. There are generally no requirements to bring older homes into compliance unless substantial renovation is being done. This inspection will instead seek to find deficiencies that may warrant homeowner attention, such as leaking plumbing, unsafe wiring, or fire hazards. When a deficiency is noted, recommendations will often cite current code as goal standard for repair.
Due Diligence: This report seeks to identify any deficiencies that may exist and is limited to a visual examination. Further diagnosis by a specialized contractor is likely to reveal related concerns. Clients should arrange for further evaluation and obtain cost and repair estimates from qualified parties. In professional trades, qualified parties are those trained to work in a specialized field and have appropriate contractor's licenses; for example, licensed electrical contractors, plumbing contractors, HVAC contractors, roofing contractors, etc. Prompt follow-up by seeking the advice of qualified professionals diminishes the chances of discovering unpleasant or costly surprises after completing price negotiations or closing. When clients arrange for repairs instead of relying on sellers to hire contractors, purchasers are usually in a stronger bargaining position if work is later found to be substandard.
Form 17: The home inspection is only part of the process that purchasers participate in when buying a property. Clients should study Form 17 (the real property disclosure statement) and, as applicable, follow up on the information therein. Sellers, with exception of some bank-owned properties, are obligated to disclose known deficiencies with the building or the lot. Those deficiencies may not be observable at the time of the inspection, for example, signs of past moisture, flooding, or matters involving pests. Due diligence on the part of clients includes studying Form 17, verifying listing information and data that is available from the County Assessor's Office: https://cp.spokanecounty.org/scout/scoutdashboard/
How to Read This Report
All narrative observations are colored, numbered and labeled to help you find, refer to, and understand the severity of the observation. Observation colors and labels used in this report are:
- Primary Concern:Repair items that may cost significant money to correct now or in the near future, or items that require immediate attention to prevent additional damage or eliminate safety hazards.
- Repair:Repair and maintenance items noted during inspection. Please note that some repair items can be expensive to correct such as re-finishing hardwood floors, but are considered simply repair items due to their cosmetic nature.
- Recommended Maintenance:These are repair items that should be considered "routine home ownership items," such as servicing the furnace, cleaning the gutters or changing the air filters in the furnace.
- Improve:Observations that are not necessarily defects, but which could be improved for safety, efficiency, or reliability reasons.
- Monitor:Items that should be watched to see if correction may be needed in the future.
- Due Diligence:Observation such as a buried oil tank that may require further investigation to determine the severity and / or urgency of repair.
- Future Project:A repair that may be deferred for some time but should be on the radar for repair or replacement in the near future.
- Efficiency:Denotes observations that are needed to make the home more energy efficient as well as to bring the home up to modern insulation standards. This category typically includes windows and insulation. Other items, such as lighting and appliances, are not inspected for their energy status.
- Note:Refers to aside information and /or any comments elaborating on descriptions of systems in the home or limitations to the home inspection.
- Description:Detailed description of various aspects of the property noted during the inspection.
Summary Page
Primary Concerns
- ES-2 Electric Service:
Overall, numerous problems were noted in the wiring system indicating older, incomplete and unreliable wiring practices. The house has an obsolete fused electric panel that has been incorrectly modified to accommodate modern electrical demands. Many insurance companies will not insure homes with fused panels. This type of circuit protection is generally obsolete, and difficult to add onto without full service equipment replacement. For example, modern AFCI requirements for new circuits would mean you would need to replace this panel as soon as you want to add a new circuit in the house.
The following issues were noted:
- Multiple Double-tapped circuits: this is when two conductors share the same breaker. This condition creates poorly protected circuits and is a possible fire hazard. Double lugged conductors may create poorly protected conductors that are more vulnerable to arcing and overheating.
Safety Note: One set of wires is bypassing all circuit breaker or fuse protection, presenting a significant hazard because the circuit is permanently live and cannot be disabled.
- Primary panel enclosures are unbonded - this can allow the metal enclosure to become electrified.
I recommend a complete evaluation of the entire electrical system by a qualified electrical contractor. Implement repairs and updates as recommended.
Repairs
- G1-3 Grounds:
The guardrail system for the side stairs is missing and is a required modern safety standard.
- Handrails should be provided on at least one side of each flight of stairs with four or more risers.
- Stairs and landings more than 30-inches above the surrounding area should have a guardrail system for safety.
- Guardrails should have openings no larger than 4 inches, railings should be 36 inches high and strong enough to hold a falling adult.
This may be an homeowner insurance policy concern. Consult a licensed general contractor to further evaluate and repair.
- ESDW-2 Exterior Siding, Doors and Windows:
Stair step cracking was noted in the brick siding system. This is typically an indication of settlement in either the house or the brick cladding system or both. I recommend additional inspection of the brick siding system by a qualified mason or general contractor.
- DPB-1 Decks, Porches and Balconies:
The concrete pad on the side porch has cracked and requires repair. Sometimes these can be lifted back into place by slab jacking. If this concrete is too old, often this will not work and proper repair can necessitate removal. Note the water drip line in all photos indicates active water draining onto these landings, this likely affects the stability of the soils. Gutter installation will alleviate future problems. Consult a general contractor or concrete placement specialist to evaluate and repair.
- G-2 Garage:
Insulation in the garage has been installed in direct contact with the roof sheathing. This is not recommended. Without a proper air gap for ventilation, this condition is likely to trap moisture from condensation. This can lead to molds and wood decay of the roof decking. I recommend removing this insulation and treating the wood with mold resistant primer. If insulating the garage is desired, consult with a qualified general contractor about options for installing thermal barriers correctly.
- G-3 Garage:
Several electrical issues were noted in the garage.
- Ground Fault Current Interrupter (GFCI) protection is required at the first outlet entering the garage, unprotected wiring can be a hazard with amount of water present.
- The receptacle near the garage door is wired incorrectly and shows "open ground" - indicating it is ungrounded and a potential shock hazard.
- The outdoor light appears to not function and is plugged into an outlet, this should be hard-wired.
Consult an electrician for evaluation and repair.
- RCG-2 Roof, Chimney and Gutters:
Roof Repairs Needed. This is an older roof in the last 1/3 of it's service life, but appears to be performing well for its age. The roofing material on this building is done in 3-tab composition shingle. These shingles are often rated as 25-30 year shingles, though I find in practice, 18-22 years is more realistic depending on the quality of the installation, the amount of exposure and the pitch of the roof. Examples of specific observations noted during inspection include:
Eaves
- Water damage and damaged wood noted in the eaves.
Drainage
- Low-slope areas of the roof were noted where the roof may not shed water reliably. Monitor these areas and keep them clean of organic debris.
Field Shingles
- Moderate granular loss was noted on some of the field shingles. Once shingles loose their granular coatings they will deteriorate more quickly from UV exposure.
Flashings
- Plumbing vent flashings are poorly mounted and vulnerable to leaks.
Inspector Notes
- Drip edge flashings were noted - this is good, these are now required.
Recommendation: Consult a licensed roofing contractor to further evaluate the roof to ensure reliable performance. Consider the cost of periodic repairs vs. replacement for this roof.
- RCG-4 Roof, Chimney and Gutters:
Repairs are needed to the masonry chimney. The conditions noted here could increase the risk of moisture control problems related to the chimney. Neglecting maintenance on masonry chimneys can also lead to loose or damaged bricks and eventually a failing masonry system. Consult a licensed masonry contractor to further evaluate and repair the masonry chimney as recommended.
Examples of observations noted during inspection include:
Chimney Flashings
- The chimney flashings are loose and have large voids that may allow wind-driven snow or rain to enter.
Chimney Caps
- The chimney rain cap is loose and not reliably secured - this could be vulnerable to wind damage.
- The concrete chimney cap is not sealed well where it meets the flue liner - this can lead to moisture control problems
- The concrete chimney cap is cracked - this can lead to moisture control problems as well as physical damage.
Chimney Masonry
- Failing mortar was noted - this can lead to moisture control and structural problems with the chimney
- EDFW-1 Electric Distribution and Finish Wiring:
A number of defects and red flags were noted in the wiring system indicating old, unreliable and incomplete wiring practices. I recommend additional inspection and repair of the entire wiring system by a licensed electrical contractor as additional repairs could be needed that are latent or concealed. Examples of observations include:
- The kitchen appears to be under-wired - modern standards recommended at least two 20-amp circuits for countertop receptacles.
- Ungrounded receptacles were noted in several locations, this is common in older buildings (prior to 1962) where three prong receptacles have been installed on an older two wire system. This creates a safety hazard as it is false advertising; appliances that rely on an equipment ground to discharge a fault can be plugged into ungrounded circuits. This disables the important safety feature of an equipment ground.
- Reverse polarity was noted - this happens when the hot and neutral wire are reversed and can create a shock hazard. This is also a sign of amateur workmanship.
- GFCI (Ground Fault Circuit Interruption) protection is missing in all areas. GFCI protection is recommended for the electrical receptacles in the following locations: the two dedicated kitchen appliance circuits, all receptacles within 6 feet of a sink, bathrooms, exterior, garage, unfinished basements, laundry and all wet and damp locations. GFCI's protect against electrocution by limiting the duration of an electrical shock.
Recommendation: Consult a licensed electrician to evaluate and repair.
- P-3 Plumbing:
The inside valve to shut off the exterior hose bib showed slight leakage at the time of inspection. This leak is likely to increase over time as the valve is operated each season and may cause water damage to the finishes in the basement. I recommend a licensed plumber evaluate and repair.
- P-6 Plumbing:
Install a foam pad below the water heater to prevent corrosion of the tank and to reduce heat loss to the cold concrete slab. Please note that foam pads are required for electric water heaters installed in contact with a concrete floor. They are recommended for gas water heater installed on concrete. This may be a DIY fix or via general handyman.
- P-7 Plumbing:
Install listed seismic straps to restrain the water heater in the event of an earthquake; none were noted during inspection. Two straps should be located on the water heater: one on upper 1/3rd of tank and one at the lower 1/3rd. Consult a general contractor, plumber or handyman for this repair.
Note: This is an issue that often affects the home appraisal process.
- K-1 Kitchen:
The supply piping below the kitchen sink is showing some minor corrosion and evidence of prior leaking. This was dry at the time of inspection but should be monitored as repair could be needed here to ensure reliable performance. There appears to be a recent repair with a black steel gas pipe. This is not designed for water and will corrode on the interior, it should be replaced by a licensed plumber.
- MB-1 Main Bathroom:
Signs of amateur workmanship were noted at the waste plumbing below the master bathroom sink. This should be further investigated and repaired by a licensed plumber to ensure reliable performance. Corrugated waste pipe was used to drain this sink. This is not a listed "self scouring" plumbing product and indicates plumbing work that has not been done by a licensed plumber. Use smooth wall pipe only to prevent clogs. The waste plumbing below is leaking and requires immediate repair, this may be DIY or hire a licensed plumber to further evaluate and repair.
- MB-4 Main Bathroom:
The lower edge of the tub should be filled with flexible silicone caulk but has been filled with non-flexible grout. This will allow water entry and eventual damage inside the wall.
- BB-1 Basement Bathroom:
The basement sink has an active leak from the pop up control arm. This is typically easily fixed with a new gasket. Additionally, the pop-up stopper is missing. Excess corrosion indicates a full drain rebuild may be beneficial. This may be a homeowner DIY, handyman repair, or accomplished in conjunction with other plumbing repairs.
Full Report
Grounds
Grounds Inspection Criteria
Drainage and Site
Driveways/Walkways/Flatwork
Grounds, Trees and Vegetation
Exterior Stairs
Exterior Siding, Doors and Windows
Exterior Inspection Criteria
Siding and Trim
Eaves
Exterior Doors
Exterior Window Frames
Garage
Garage Inspection Criteria
Garage General
Garage Doors and Automatic Openers
Garage Floor
Garage Stairs
Roof, Chimney and Gutters
Roof System Inspection Criteria
Roof Materials
Gutters and Downspouts
Chimneys
Electric Service
Electrical System Inspection Criteria
Electric Service Voltage Tested
Electric Service
Electric Service Equipment
Electrical Grounding System
Electrical Bonding System
Electric Distribution and Finish Wiring
Branch Wiring
Receptacles and Fixtures
Smoke and Carbon Monoxide Alarm Systems
Interior
General Interior Inspection Criteria
Floors and Floor Materials
Walls, Ceilings, Trim, Hallways and Closets
Wall Insulation and Air Bypass
Stairs and Railings
Interior Doors
Windows
Heating, Cooling, Fireplaces and Ventilation
Heating & Cooling Inspection Criteria
Heating System
Air Filters
Heating and Cooling Distribution Systems
Mechanical Ventilation Systems
Additional Heat Sources
Fireplaces and Stoves Inspection Criteria
Plumbing
Plumbing Inspection Criteria
Water Meter
Water Service Supply
Distribution Pipe
Waste Pipe and Discharge
Water Heater
Water Temperature
Exterior Hose Bibs
Kitchen
Sinks and Faucets
Cabinets and Countertops
Disposers
Dishwasher
Ventilation Method
Ranges, Ovens and Cooktops
Refrigerators
General Kitchen Condition
Structure and Basement
Structure and Basement Inspection Criteria
Foundation
Floor, Wall and Ceiling Framing
Basement
Basement Moisture
General Comments
Building Characteristics, Conditions and Limitations
Style of Home: Ranch
Approximate Square Footage: 1500
The approximate square footage listed here is listed as a courtesy and is based off of public records and disclosure. An evaluation of square footage of the buildings and property lines is beyond the scope of this inspection.
Approximate Year of Original Construction: 1954
Unless the wiring in the building has been fully updated, this building likely has wiring that predates the late 1980's. Branch circuit wiring installed in buildings built prior to the late 1980s is typically rated for a maximum temperature of only 60 degrees Celsius. This includes non-metallic sheathed (Romex) wiring, and both BX and AC metal-clad flexible wiring. Knob and tube wiring, typically installed in homes built prior to 1950, may be rated for even lower maximum temperatures. Newer electric fixtures including lighting and fans typically require wiring rated for 90 degrees Celsius. Connecting newer fixtures to older, 60-degree-rated wiring is a potential fire hazard. Repairs for such conditions may involve replacing the last few feet of wiring to newer fixtures with new 90-degree-rated wire, and installing a junction box to join the old and new wiring. It is beyond the scope of this inspection to determine if any such incompatible components are installed. Based on the age of this building, be aware that such components may be present.
In 1978, federal laws were passed to prohibit use of lead and asbestos in building materials. Manufacturers of building materials were allowed to sell existing stocks of materials that were manufactured with lead and asbestos, so even buildings constructed as late as the mid-1980's could possibly contain lead or asbestos. Identification and testing for lead and asbestos and other environmental testing is beyond the scope of this home inspection. If you wish to seek additional information, I recommend contacting an environmental lab or industrial hygienist.
Attending the Inspection: Vacant (inspector only), Buyer
Occupancy: Unoccupied
Animals Present: No
Weather during the inspection: Snow, Ice, Light Rain
Please note that snow and ice will limit the scope of the inspection. Typically, a visual inspection of the roof and grounds on the outside of the house is severely limited when snow and ice are present.
Approximate temperature during the inspection: Below 45[F]
Ground/Soil surface conditions: Frozen, Snow-covered, Wet
For the Purposes of This Report, the Front Door Faces: South
This house was vacant / unoccupied at the time of inspection. Vacant and unoccupied houses present unique challenges for home inspection, especially the piping and wiring systems which have not be subject to regular use prior to the inspection. While these systems can be tested during inspection, this one-time test is different than regular use and it is difficult to know how these systems will respond to regular use after the inspection. For example, septic systems may initially function and then fail under regular daily use. Plumbing traps may operate with no signs of leaks and then let go when being actively used for a few days. Shower pans may only leak when someone is standing in the shower and taking a shower. Seals for plumbing fixtures can dry up and leak when not is use. Sewer lines with roots may allow water flow, but then fail when waste and tissue are flushed; it can take a few days for that to backup. Please understand we are trying our best to look for clues of past or existing problems to paint a realistic best-guess as to the reliability of these systems during inspection.
Grounds
Grounds Inspection Criteria
Site. The inspection of the site includes the building perimeter, land grade, and water drainage directly adjacent to the foundation; trees and vegetation that adversely affect the structure; walks, grade steps, driveways, patios, and retaining walls contiguous with the structure.
The inspector will:
(a) Describe the material used for driveways, walkways, patios and other flatwork around the home.
(b) Inspect
(i) For serviceability of the driveways, steps, walkways, patios, flatwork and retaining walls contiguous with the structure.
(ii) For proper grading and drainage slope.
(iii) Vegetation in close proximity to the home.
(c) Describe any deficiencies of these systems or components
Drainage and Site
Site Description: Flat
Driveways/Walkways/Flatwork
Driveway: alley way
Walkways: Concrete
Patios: Concrete
Cracks were noted in walkway flatwork. No immediate repair appears necessary, though water will continue to deteriorate the surface until the walkway is repaired or replaced.
Grounds, Trees and Vegetation
Trees/Vegetation too near building: Yes - Prune Vegetation off House
Exterior Stairs
Exterior Stairs: Guardrail - Non-standard, missing, loose, incomplete
The guardrail system for the side stairs is missing and is a required modern safety standard.
- Handrails should be provided on at least one side of each flight of stairs with four or more risers.
- Stairs and landings more than 30-inches above the surrounding area should have a guardrail system for safety.
- Guardrails should have openings no larger than 4 inches, railings should be 36 inches high and strong enough to hold a falling adult.
This may be an homeowner insurance policy concern. Consult a licensed general contractor to further evaluate and repair.
Exterior Siding, Doors and Windows
Exterior Inspection Criteria
Exterior. An inspection of the exterior includes the visible wall coverings, trim, protective coatings and sealants, windows and doors, attached porches, decks, steps, balconies, handrails, guardrails, carports, eaves, soffits, fascias and visible exterior portions of chimneys.
The inspector will:
• Describe the exterior components visible from ground level.
• Inspect visible wall coverings, trim, protective coatings and sealants, windows and doors, attached porches, decks, steps, balconies, handrails, guardrails, carports, eaves, soffits, fascias and visible exterior portions of chimneys.
• Probe exterior components where deterioration is suspected or where clear indications of possible deterioration exist. Probing is not required when probing will damage any finished surface or where no deterioration is suspected.
• Describe any deficiencies of these systems or components.
Siding and Trim
Trim Material: Masonry
Siding Material: Brick
Stair step cracking was noted in the brick siding system. This is typically an indication of settlement in either the house or the brick cladding system or both. I recommend additional inspection of the brick siding system by a qualified mason or general contractor.
Eaves
Plywood
Exterior Doors
Exterior Door Styles: Solid core
Exterior Window Frames
Window Frames: Wood
Decks, Porches and Balconies
Concrete Decks, Stoops, Landings and Porches
Concrete Structure: Settlement and/or Cracking Noted
The concrete pad on the side porch has cracked and requires repair. Sometimes these can be lifted back into place by slab jacking. If this concrete is too old, often this will not work and proper repair can necessitate removal. Note the water drip line in all photos indicates active water draining onto these landings, this likely affects the stability of the soils. Gutter installation will alleviate future problems. Consult a general contractor or concrete placement specialist to evaluate and repair.
Garage
Garage Inspection Criteria
Attached garages or carports. The inspection of attached garages and carports includes their framing, siding, roof, doors, windows, and installed electrical/mechanical systems pertaining to the operation of the home.
The inspector will:
• Inspect the condition and function of the overhead garage doors and associated hardware.
• Test the function of the garage door openers, their auto-reverse systems and secondary entrapment devices (photoelectric and edge sensors) when present.
• Inspect the condition and installation of any pedestrian doors.
• Inspect fire separation between the house and garage when applicable.
• Report as a fire hazard the presence of any ignition source (gas and electric water heaters, electrical receptacles, electronic air cleaners, motors of installed appliances, etc.) that is within eighteen inches of the garage floor.
• Describe any deficiencies of these systems or components.
Garage General
Garage Type: Detached
Insulation in the garage has been installed in direct contact with the roof sheathing. This is not recommended. Without a proper air gap for ventilation, this condition is likely to trap moisture from condensation. This can lead to molds and wood decay of the roof decking. I recommend removing this insulation and treating the wood with mold resistant primer. If insulating the garage is desired, consult with a qualified general contractor about options for installing thermal barriers correctly.
Several electrical issues were noted in the garage.
- Ground Fault Current Interrupter (GFCI) protection is required at the first outlet entering the garage, unprotected wiring can be a hazard with amount of water present.
- The receptacle near the garage door is wired incorrectly and shows "open ground" - indicating it is ungrounded and a potential shock hazard.
- The outdoor light appears to not function and is plugged into an outlet, this should be hard-wired.
Consult an electrician for evaluation and repair.
Garage Doors and Automatic Openers
Overhead Garage Door Type: Metal
Automatic Garage Opener: None noted
You will likely want to install an automatic garage door opener as none has been installed for the garage door.
Garage Floor
Garage Slab: Concrete
Garage Stairs
Garage Stairs: None noted
Roof, Chimney and Gutters
Roof System Inspection Criteria
Roofs. An inspection of the roof includes the roof covering materials; gutters and downspout systems; visible flashings; roof vents; skylights, and any other roof penetrations; and the portions of the chimneys and flues visible from the exterior.
The inspector will:
• Traverse the roof to inspect it.
• Inspect the gutters and downspout systems, visible flashings, soffits and fascias, skylights, and other roof penetrations.
• Report the manner in which the roof is ventilated.
• Describe the type and general condition of roof coverings.
• Report multiple layers of roofing when visible or readily apparent.
• Describe any deficiencies of these systems or components.
Roof Materials
Method of Roof Inspection: Walked on roof
Roof Style: Hip
Flashings, Valleys and Penetrations: Present and Visually Standard
Roof flashings are used to keep a roofing system waterproof where the roofing material starts, stops, changes direction or is penetrated. During inspection, we look for standard flashing techniques that could be considered normal or standard in our region. Damaged, incomplete or non-standard flashings can be a sign of an older or less reliable roofing system and may require repair. Any non-standard flashings noted during inspection will be reported on below if found.
Roof Covering Materials: Three-tab composition shingle
Approximate Age of Roof Covering: 16-18 Years
Overlay Roof: No
Shingle Fastening Accessible For Inspection : No
Please note that when inspecting composition roof installations, I try and look under shingles to see how the shingles have been fastened. Proper fastening is critical for successful roof performance. Often the shingles are bonding so well, they cannot be lifted to inspect the fastening. In this case, I was unable to lift the shingles and see the fastening pattern - they are bonded well and I do not use a flat bar to pry them apart as part of a visual inspection unless there is a reason to start chasing visible leaks. While this limits my visual inspection, this is a good sign, as loose, un-bonded shingles can lead to wind damage and would be written up as a defect.
Roof Repairs Needed. This is an older roof in the last 1/3 of it's service life, but appears to be performing well for its age. The roofing material on this building is done in 3-tab composition shingle. These shingles are often rated as 25-30 year shingles, though I find in practice, 18-22 years is more realistic depending on the quality of the installation, the amount of exposure and the pitch of the roof. Examples of specific observations noted during inspection include:
Eaves
- Water damage and damaged wood noted in the eaves.
Drainage
- Low-slope areas of the roof were noted where the roof may not shed water reliably. Monitor these areas and keep them clean of organic debris.
Field Shingles
- Moderate granular loss was noted on some of the field shingles. Once shingles loose their granular coatings they will deteriorate more quickly from UV exposure.
Flashings
- Plumbing vent flashings are poorly mounted and vulnerable to leaks.
Inspector Notes
- Drip edge flashings were noted - this is good, these are now required.
Recommendation: Consult a licensed roofing contractor to further evaluate the roof to ensure reliable performance. Consider the cost of periodic repairs vs. replacement for this roof.
Gutters and Downspouts
Gutter and Downspout Materials: None
Gutters and downspouts are missing at important drainage areas. Gutter and downspout systems are critical for controlling roof runoff and preventing water from damaging the building. Downspouts should direct water 3-5 feet from the foundation to prevent damage. Examples of specific observations noted during inspection include:
- Localized swelling and separation of fascia and soffits
- Localized rot on fasica
Recommendation: Have a roofing contractor assess drainage in conjunction with the roof evaluation.
Chimneys
Present
Chimney Material: Masonry
Chimney Flue Liners: Present
Repairs are needed to the masonry chimney. The conditions noted here could increase the risk of moisture control problems related to the chimney. Neglecting maintenance on masonry chimneys can also lead to loose or damaged bricks and eventually a failing masonry system. Consult a licensed masonry contractor to further evaluate and repair the masonry chimney as recommended.
Examples of observations noted during inspection include:
Chimney Flashings
- The chimney flashings are loose and have large voids that may allow wind-driven snow or rain to enter.
Chimney Caps
- The chimney rain cap is loose and not reliably secured - this could be vulnerable to wind damage.
- The concrete chimney cap is not sealed well where it meets the flue liner - this can lead to moisture control problems
- The concrete chimney cap is cracked - this can lead to moisture control problems as well as physical damage.
Chimney Masonry
- Failing mortar was noted - this can lead to moisture control and structural problems with the chimney
Fuel Storage and Distribution
Gas Meter
Present
Gas Pipe Materials: Steel and flex pipe
The gas meter is located on the west side of the home. The attached graphic shows how to turn off the gas supply in the event of an emergency such as gas leak in the house or local wildfires.
Gas, Propane and Oil Piping
Gas Piping Materials Noted: Steel
Electric Service
Electrical System Inspection Criteria
Electrical system. The inspection of the electrical system includes the service drop through the main panel; subpanels including feeders; branch circuits, connected devices, and lighting fixtures.
The inspector will:
(a) Describe in the report the type of primary service, whether overhead or underground, voltage, amperage, over-current protection devices (fuses or breakers) and the type of branch wiring used.
(b) Report
(i) The existence of a connected service-grounding conductor and service-grounding electrode when same can be determined.
(ii) When no connection to a service grounding electrode can be confirmed.
(c) Inspect the main and branch circuit conductors for proper over-current protection and condition by visual observation after removal of the readily accessible main and sub-electric panel cover(s).
(d) Report, if present, solid conductor aluminum branch circuits. Include a statement in the report that solid conductor aluminum wiring may be hazardous and a licensed electrician should inspect the system to ensure it's safe.
(e) Verify
(i) The operation of a representative number of accessible switches, receptacles and light fixtures.
(ii) The grounding and polarity of a representative number of receptacles; particularly in close proximity to plumbing fixtures or at the exterior.
(iii) Ground fault circuit interrupter (GFCI) protection and arc-fault circuit interrupter (AFCI) protection where required.
(f) Report the location of any inoperative or missing GFCI and/or AFCI devices when they are recommended by industry standards.
(g) Advise clients that homes without ground fault protection should have GFCI devices installed where recommended by industry standards.
(h) Report on any circuit breaker panel or subpanel known within the home inspection profession to have safety concerns.
(i) Describe any deficiencies of these systems or components.
Electric Service Voltage Tested
Service Voltage: 120/240
Electric Service
Service Entrance: Above Ground
Meter Base Amperage: 200
Electric Service Equipment
Service Entrance (SE) conductor Size: Aluminum, #2, 100 amps
Main Panel Amperage: 100 amps
Electric Service Amperage: 100 amps
Main Electric Panel Location: Basement
Panel Manufacturer: Cutler Hammer
Overall, numerous problems were noted in the wiring system indicating older, incomplete and unreliable wiring practices. The house has an obsolete fused electric panel that has been incorrectly modified to accommodate modern electrical demands. Many insurance companies will not insure homes with fused panels. This type of circuit protection is generally obsolete, and difficult to add onto without full service equipment replacement. For example, modern AFCI requirements for new circuits would mean you would need to replace this panel as soon as you want to add a new circuit in the house.
The following issues were noted:
- Multiple Double-tapped circuits: this is when two conductors share the same breaker. This condition creates poorly protected circuits and is a possible fire hazard. Double lugged conductors may create poorly protected conductors that are more vulnerable to arcing and overheating.
Safety Note: One set of wires is bypassing all circuit breaker or fuse protection, presenting a significant hazard because the circuit is permanently live and cannot be disabled.
- Primary panel enclosures are unbonded - this can allow the metal enclosure to become electrified.
I recommend a complete evaluation of the entire electrical system by a qualified electrical contractor. Implement repairs and updates as recommended.
AFCI (arc fault protection) is now required on all branch circuits supplying outlets or devices installed in residential dwelling unit kitchens, family rooms, dining rooms, living rooms, parlors, libraries, dens, bedrooms, sunrooms, recreation rooms, closets, hallways, laundry areas, and similar rooms and areas. The goal of this protection is to reduce risks of electrical fires. This home pre-dates the latest code updates, and and upgrades to fault protection are good safety consideration. AFCI protection is commonly absent from older homes. Consult a licensed electrician about improving circuit protection as desired. I would consider this improvement in the context of other electrical repairs or upgrades.
Please note that if you add or replace receptacle outlets to the existing system, they should comply with modern AFCI standards.
Electrical Grounding System
Present - Could Not Confirm
During a home or property inspection, every effort is made to inspect the visible components of the electrical system grounding. The grounding system is critical for safely discharging electrical surges, especially in the case of lightning strikes. There is no way in the context of a home inspection to verify the "effectiveness" of the grounding system as much of the system is not visible and there are not practical tests one can perform in the way we can test a furnace or a plumbing fixture. However, there are many things that can lead me to recommend further evaluation of the grounding system by a licensed electrical contractor and they will be documented in the observations below if discovered.
Electrical Bonding System
Bonding Noted on Water Pipes, Bonding Noted on Gas Pipes
Bonding connections were noted on the gas and water pipes.
Electric Distribution and Finish Wiring
Branch Wiring
Wire Material: Copper
Wiring Method: Non-metallic sheathed cable
Receptacles and Fixtures
Inspection Method: Tested All Accessible
During inspection I make an effort to test and inspect all accessible electric receptacles and switches. In general, the scope of testing is directly related to access; where personal belonging and furniture obstruct access to receptacles and fixtures, fewer of them can be reasonably tested during inspection. All defects found during inspection today will be listed in this report.
A number of defects and red flags were noted in the wiring system indicating old, unreliable and incomplete wiring practices. I recommend additional inspection and repair of the entire wiring system by a licensed electrical contractor as additional repairs could be needed that are latent or concealed. Examples of observations include:
- The kitchen appears to be under-wired - modern standards recommended at least two 20-amp circuits for countertop receptacles.
- Ungrounded receptacles were noted in several locations, this is common in older buildings (prior to 1962) where three prong receptacles have been installed on an older two wire system. This creates a safety hazard as it is false advertising; appliances that rely on an equipment ground to discharge a fault can be plugged into ungrounded circuits. This disables the important safety feature of an equipment ground.
- Reverse polarity was noted - this happens when the hot and neutral wire are reversed and can create a shock hazard. This is also a sign of amateur workmanship.
- GFCI (Ground Fault Circuit Interruption) protection is missing in all areas. GFCI protection is recommended for the electrical receptacles in the following locations: the two dedicated kitchen appliance circuits, all receptacles within 6 feet of a sink, bathrooms, exterior, garage, unfinished basements, laundry and all wet and damp locations. GFCI's protect against electrocution by limiting the duration of an electrical shock.
Recommendation: Consult a licensed electrician to evaluate and repair.
Smoke and Carbon Monoxide Alarm Systems
CO Alarms Noted:In bedrooms
CO Alarms: Present
The installation of carbon monoxide alarms is recommended for all homes that have fuel burning appliances such as gas or oil furnaces, gas water heaters, gas ovens and cook-tops, gas fireplaces and wood stoves. In addition, Washington State law (WAC 51-51-0315) now requires UL 2034 approved carbon monoxide alarms in ALL homes and condominiums being sold in Washington State. The location should be: at least one alarm outside of all sleeping areas and one on each floor of the house. Best practices are to have these alarms hardwired with a battery back-up - though requirements are for the installation to meet manufacturer's specifications. Carbon monoxide is a colorless, odorless gas that can cause sickness, nausea and even death. Alarms have a useful service life of roughly 6 years, so changing them more frequently than smoke alarms is recommended.
Smoke Alarms: Present, Old, Updating Recommended
During the home inspection, I try and test a representative sample of the smoke alarms by using the test button on the alarms. This is NOT an accurate test of the sensor just a test to see if the unit is powered. For reliability, fire marshals recommended updating smoke alarms every 10 years and changing batteries bi-annually. The latest data indicate that we should be using photoelectric technology in our smoke alarms for improved fire detection and to reduce problems with false alarms which can lead to disabling of this important safety system. Unfortunately, the alarms have to be removed to determine if they are photo-electric or ionization types. It is surprisingly complex to accurately test a smoke alarm system and determine the reliability, age, and type of sensor technology used, especially as many homes can have half a dozen or more alarms throughout the house. A complete evaluation of smoke alarms is beyond the scope of this inspection. For optimal fire safety, I recommend taking control of these important safety devices and learning about how to service and maintain your smoke alarm system to keep the building occupants safe. For more information, please read this link. For more information, please read this link.
There appear to be smoke alarms reaching 10 years old. These are getting old. Fire marshals recommended updating smoke alarms every 10 years to ensure reliable performance. Updating to hardwired system is recommended. None of these alarms operated when tested; some were missing batteries.
Carbon monoxide alarms were found and noted during inspection. Be sure to check these regularly. The standard is 1/ floor and 1 outside all sleeping areas. Currently they are installed in each bedroom and one should also be installed near the furnace in basement.
Interior
General Interior Inspection Criteria
The living room has no interior light. Based on the build era, it was common to use lamps on wall switch. Consult an electrician for options to install dedicated lighting.
Interiors. The inspection of the interior includes the walls, ceilings, floors, windows, and doors; steps, stairways, balconies and railings.
The inspector will:
(a) Verify that steps, handrails, guardrails, stairways and landings are in- stalled wherever necessary and report when they are missing or in need of repair and report when baluster spacing exceeds four inches.
(b) Inspect
(i) The overall general condition of cabinets and countertops.
(ii) Caulking and grout at kitchen and bathroom counters.
(iii) The interior walls, ceilings, and floors for indicators of concealed structural deficiencies, water infiltration or major damage.
(iv) The condition and operation of a representative number of windows and doors.
(c) Comment on the presence or absence of smoke detectors.
(d) Describe any non-cosmetic deficiencies of these systems or components.
Floors and Floor Materials
Floor Materials: Hardwood, Plastic laminate, Vinly asbestos tiles
Squeaky wood flooring was noted. This happens when wood finish floors are not adequately secured to the sub-floor. Special nails can be used to remove squeaks from hardwood floors. Consult a qualified contractor to further evaluate and repair the squeaky floors.
The old flooring in the basement of the home may contain asbestos. Asbestos identification and all asbestos testing is beyond the scope of this inspection. If removal of this flooring is desired, I recommend testing this material prior to removing. Once asbestos becomes friable or airborne it becomes a safety hazard. As long as these tiles are not disturbed or are encapsulated, they should not pose a health risk, but they could pose a future disposal liability. Prior to remodeling an older home it is recommended that you have a thorough lead and asbestos evaluation by a certified specialist and remediate all contaminates as recommended. Old buildings often contain lead and asbestos in an assortment of building materials.
Walls, Ceilings, Trim, Hallways and Closets
Wall and Ceiling Materials: Drywall, Lath and Plaster, Ceiling tiles
Fairly routine light plaster cracks were noted in walls and ceilings. This is characteristic of old plaster walls and ceilings and does not require repair unless the keys that bond the plaster to the lath fail. Light surface cracking can be repaired prior to painting as desired. This may be a DIY fix or sourced to a licensed general contractor.
The ceiling in basement rooms of this house contains popcorn texture. This product may contain asbestos as many of these products contained asbestos prior to 1978. After 1978, remaining stocks of material containing asbestos were sold and as the product was slowly phased out. Asbestos testing is beyond the scope of this inspection. The health risks posed by this substance are minimal unless the texture becomes friable or air borne. If you wish to remove the popcorn texture or have remodel plans that could involve cutting or removing this sheetrock, asbestos testing is recommended. One option is always to sheetrock over this texture if you wish to have a different ceiling finish. Consult with an environmental lab for more information on asbestos testing.
Wall Insulation and Air Bypass
Wall Insulation: Not Visible
Stairs and Railings
The stairs to the basement are old non-conforming stairs. Modern stairs have specific safety requirements regarding the size and configuration of the stair treads, risers, guardrails and handrails. Older stairs seldom meet modern safety standard and it may not be cost-effective to bring completely to modern standards. Use caution when navigating these stairs. Improvements can often be made to the handrail system to improve the safety of the stairs.
Consult with a qualified general contractor about options for improvements as feasible.
Examples of observations noted during inspection include:
- The guardrail is missing on one side and should run the length of the stairs
- Inadequate ceiling height was noted - today a minimum of 6-feet 8-inches is needed for headroom clearance
- The graspable handrail is incomplete and should run the length of the stairs
Interior Doors
Interior Doors: Hollow Core, Finishes (Refinishing Needed, Hole in Hollow Door)
Windows
Window Glazing: Single pane, Double pane
Interior Window Frame: Wood, Metal
Window Styles: Single hung
Water stains were noted by the window. These stains were dry at the time of inspection but may indicate prior leakage. Inquire with the seller for any history of leakage here and monitor as some repair could be needed. At the time of inspection no water damage was found and visible red flags do not merit repair.
All of the windows in this home are old wood windows that require maintenance and repair. You need to decide how you want to approach the windows in this home as they are generally older and do not comply with modern standards for safety glass and energy efficiency. Many can be repaired by replacing putty seal on the outside of the window. Repairs can be made on an as-needed basis and efficiency can be added with storm windows and curtains. Some are missing storm windows or storm windows will not open. Existing windows that have character are often worth preserving and restoring, where windows that are in worse condition and have less character may be good candidates for replacement. The windows are in fairly typical condition for age and type.
Examples of observations:
- Upstairs bedroom window does not lock completely
- Basement laundry window is inoperable and covered in bubble wrap
- Basement bedroom window has glazing putty failing inside and outside.
- Cracked glass in the kitchen window above the sink
- Kitchen window glazing is not sealed on outside
Consult with a window specialist or general contractor for evaluation and repair as desired.
Heating, Cooling, Fireplaces and Ventilation
Heating & Cooling Inspection Criteria
Heating system. The inspection of the heating system includes the fuel source; heating equipment; heating distribution; operating controls; flue pipes, chimneys and venting; auxiliary heating units.
The inspector will:
(a) Describe the type of fuel, heating equipment, and heating distribution systems.
(b) Operate the system using normal readily accessible control devices.
(c) Open readily accessible access panels or covers provided by the manufacturer or installer, if readily detachable.
(d) Inspect
(i) The condition of normally operated controls and components of systems.
(ii) The condition and operation of furnaces, boilers, heat pumps, electrical central heating units and distribution systems.
(iii) Visible flue pipes and related components to ensure functional operation and proper clearance from combustibles.
(iv) Each habitable space in the home to determine whether or not there is a functioning heat source present.
(v) Spaces where fossil fuel burning heating devices are located to ensure there is air for combustion.
(vi) Electric baseboard and in-wall heaters to ensure they are functional.
(e) Report any evidence that indicates the possible presence of an underground storage tank.
(f) Describe any deficiencies of these systems or components.
Air conditioning systems. The inspection of the air conditioning system includes the cooling equipment; cooling distribution equipment and the operating controls.
The inspector will:
(a) Describe the central air conditioning system and energy sources.
(b) Operate the system using normal control devices and measure and record temperature differential.
(c) Open readily accessible access panels or covers provided by the manufacturer or installer.
(d) Inspect the condition of controls and operative components of the complete system; conditions permitting.
(e) Describe any deficiencies of these systems or components in the inspection report.
Heating System
Energy Source: Natural gas
Heating Method: Gas forced air furnace
This house has a gas forced air furnace. A critical component to all combustion heating equipment is the heat exchanger. This is the welded metal assembly inside the furnace that contains the products of combustion so that moisture, carbon monoxide and other products of combustion do not mix with interior air and get safely vented to the exterior. Heat exchangers on modern furnaces have an average life expectancy of 15-20 years. Unfortunately, heat exchangers are concealed inside the heating equipment; they are not visible and specifically excluded from a home inspection. Cracks in heat exchangers may be concealed and can pose a potential safety hazard.
Manufacturer: Rheem
Capacity: 80,000 btu's
Age: 1981
Annual servicing of gas forced air furnaces is recommended for safe and reliable heat. The furnace was tested during inspection and was operational. This unit is an older low-efficiency model and may be nearing the end of service life, as parts will become hard to acquire. I recommend contacting an HVAC contractor for servicing and cost of replacement to enable budgeting for future replacement.
Examples of observations noted during inspection include:
- The air filter was dirty at the time of inspection
- Mineralization build-up was noted below the burners
- The blower fan was dirty at the time of inspection
- Corrosion stains were noted on the furnace cabinet
- The system was tested and operating at the time of inspection
- No recent service records were noted
Air Filters
Filtration Systems: Disposable
The heating system has disposable air filters installed. These should be changed quarterly or more to ensure proper air flow at the furnace. Be sure to install the filters with the arrows pointing in the same direction as the air flow in the furnace.
Heating and Cooling Distribution Systems
Heat Source in Each Room: Present
Distribution Method: Forced Air / Ducts, Electric Baseboard Heaters
Mechanical Ventilation Systems
Bath Fan Ducting: Disconnected in Attic
Kitchen Fan Ducting: None noted
Additional Heat Sources
Description: Electric baseboard
This home has electric baseboard heaters installed in the basement. These can get very hot during operation. Be sure to keep all drapes, curtains, furniture, electric cords and other flammable items away from these heaters when they are one. Also be careful with small children to avoid a burn hazard. Consider upgrading by extending existing furnace ducting to this room. Have this evaluated by an HVAC professional in conjunction with furnace servicing.
Fireplaces and Stoves Inspection Criteria
Fireplaces and stoves. Includes solid fuel and gas fireplaces, stoves, dampers, fireboxes and hearths.
The inspector will:
• Describe fireplaces and stoves.
• Inspect dampers, fireboxes and hearths.
• Describe any deficiencies of these systems or components.
Plumbing
Plumbing Inspection Criteria
Plumbing system. An inspection of the plumbing system includes visible water supply lines; visible waste/soil and vent lines; fixtures and faucets; domestic hot water system and fuel source.
The inspector will:
(a) Describe the visible water supply and distribution piping materials; drain, waste and vent materials; water-heating equipment.
(b) Report
(i) The presence and functionality of sump pumps/waste ejector pumps when visible or confirm the float switch activates the pump when the sump is dry.
(ii) The presence and location of a main water shutoff valve and/or fuel shutoff valve(s), or report that they were not found.
(iii) The presence of the temperature and pressure relief (TPR) valve and associated piping.
(iv) Whether or not the water temperature was tested and state that the generally accepted safe water temperature is one hundred twenty degrees Fahrenheit.
(c) Inspect the condition of accessible and visible water supply pipes, drain/waste plumbing and the domestic hot water system, when possible operate fixtures in order to observe functional flow.
(d) Check for functional drainage from fixtures.
(e) Describe any deficiencies of these systems or components in the inspection report.
Water Meter
Water pressure at 60 psi. This is a good pressure and should not exceed 85 PSI.
Water Service Supply
Pipe Material: Galvanized
Water Supply: Public water
Water Pressure: 60 PSI
Pressure Reducing Valve: None noted
Main Water Shut-off Location: Not Found - House
The inside valve to shut off the exterior hose bib showed slight leakage at the time of inspection. This leak is likely to increase over time as the valve is operated each season and may cause water damage to the finishes in the basement. I recommend a licensed plumber evaluate and repair.
Distribution Pipe
Pipe Insulation: Present
The visible portions of the supply piping appear to be insulated. However, prior to freezing weather it is always a good idea to check pipes and hose bibs for adequate insulation and freeze protection to protect pipes from cold weather and freezing conditions. Hose bibs can often be winterized prior to cold weather.
Supply Pipe Materials: Galvanized Steel
Please note that when old galvanized steel pipe is eventually replaced, be sure to have the electrical bonding and grounding system evaluated and repaired / updated as needed by a licensed electrical contractor. It is common to update old metal piping using plastic piping. This can have the unintended consequence of disrupting important electrical grounding and bonding systems.
Functional Flow: Average
Budget to replace the remaining galvanized steel supply pipe at some point in the near term and definitely during any remodel work to kitchens, laundry or bathrooms. The average life of this pipe can vary widely, but tends to be between 40-60 years. As this pipe gets old and corrodes, the insides of the pipe fill with rust, causing restrictions in the pipe. This can be tolerated for some time, but eventually the functional flow becomes so diminished that pipe replacement is necessary. At the time of inspection, functional flow was adequate and no active leaks were found.
Waste Pipe and Discharge
Discharge Type: Public Sewer - Seller
Waste and Vent Pipe Materials: ABS plastic, Galvanized steel
Some of the waste plumbing system in this building is done with old metal pipe, while some of the waste pipe has been updated with plastic. No leaks were noted at the time of inspection, but updating and on-going repairs could be needed at any time. Old metal pipes are subject to internal corrosion which can make it impossible to spot older weaker pipe until it starts to leak. During any renovations to the home be sure to have this old piping evaluated and updated as recommended by a licensed plumber. As a general rule the old cast iron pipe often lasts a very long time - even as much as 100 years. Galvanized and copper waste pipe can have a shorter useful service life - sometime 50 years. The service life from this pipe has a lot to do with water quality and occupant behavior - use of cleaning chemicals like Drain-O can be tough on metal pipes.
Water Heater
Manufacturer: Reliance
Data Plate: Shown Here
Size: 40 gal
Age: 2013
Energy Source: Electricity
Straps : None Found
Pad: None Noted - Required
Drain Pan: Not Needed
Relief Valve: Terminates Too High
Install a foam pad below the water heater to prevent corrosion of the tank and to reduce heat loss to the cold concrete slab. Please note that foam pads are required for electric water heaters installed in contact with a concrete floor. They are recommended for gas water heater installed on concrete. This may be a DIY fix or via general handyman.
Install listed seismic straps to restrain the water heater in the event of an earthquake; none were noted during inspection. Two straps should be located on the water heater: one on upper 1/3rd of tank and one at the lower 1/3rd. Consult a general contractor, plumber or handyman for this repair.
Note: This is an issue that often affects the home appraisal process.
Water Temperature
Water Temperature Measured During Inspection: 126 Degrees F
Testing of the plumbing system today, the water tested as too hot - 136 degrees F. This is a scald hazard. To prevent scalding, standards recommend indoor hot water temperatures do not exceed 120 degrees. There is some evidence that hot water temperatures should be greater than 130 degrees to prevent Legionnaires' disease from developing in the water heater. If this is a concern, you can heat the water in the tank to 140 degrees F and have a tempering valve installed at the hot water tank. Have this further evaluated and repaired by a licensed plumber or simply turn down the temperature as desired to eliminate a scald hazard. Please note that during inspection it is difficult to accurately test the water temperature as it can vary between fixtures. Testing is done in multiple locations during inspection and a median temperature is taken.
Exterior Hose Bibs
Not operating, Winterized - not tested
The exterior hose bibs were winterized at the time of inspection and could not be tested. Inquire with the seller to see if they are generally operable.
Kitchen
Sinks and Faucets
Tested
The supply piping below the kitchen sink is showing some minor corrosion and evidence of prior leaking. This was dry at the time of inspection but should be monitored as repair could be needed here to ensure reliable performance. There appears to be a recent repair with a black steel gas pipe. This is not designed for water and will corrode on the interior, it should be replaced by a licensed plumber.
Corrosion was noted below the kitchen sink indicating this sink likely needs replacement in the near term to ensure reliable performance. Monitor this area for signs of water leakage and replace.
Cabinets and Countertops
Countertop Material: Plastic laminate
Cabinet Material: Wood
The gap between the countertop and the backsplash in the kitchen needs to be re-sealed with caulking to prevent water accumulation behind the finished surfaces,
Disposers
Disposer: None noted
Dishwasher
Dishwasher: None Noted - No Plumbing and No Location for One
There is no dishwasher for the kitchen and no space in which to install a dishwasher. If you wish to have a dishwasher here you will need to have one installed including provisions for electricity, drain lines and water supply.
Ventilation Method
No Fan - Just a Window
The kitchen has no provisions for ventilation. An exhaust fan that ducts to the exterior is required at least somewhere in the kitchen - in this case, the window is the ventilation and is difficult to open. Lack of ventilation to the exterior could be inconvenient with cooking odors. Consult a qualified contractor to further evaluate this installation and install a cooktop fan and exhaust system to the outdoors.
Ranges, Ovens and Cooktops
Range/ Oven /Cook-tops: Electric
Refrigerators
Refrigerator: Operating, Ice Maker (Off, No Ice)
General Kitchen Condition
Standard
Bedrooms
Main Bedroom
Smoke Alarm: No battery
Bedroom 2
Smoke Alarm: not working
Electric Switches and Receptacles: two separate light switches
Closets: Door not functioning, new hardware on floor, water main in closet
Main Bathroom
Sinks and Cabinets
Tested, Galvanized Steel Pipe Noted
Signs of amateur workmanship were noted at the waste plumbing below the master bathroom sink. This should be further investigated and repaired by a licensed plumber to ensure reliable performance. Corrugated waste pipe was used to drain this sink. This is not a listed "self scouring" plumbing product and indicates plumbing work that has not been done by a licensed plumber. Use smooth wall pipe only to prevent clogs. The waste plumbing below is leaking and requires immediate repair, this may be DIY or hire a licensed plumber to further evaluate and repair.
Toilet
Tested
The toilet in the family bath has not been caulked to the floor. This is generally recommended though opinions on this can vary. Leaving toilets un-caulked makes them more vulnerable to coming loose on the floor. I prefer caulking the toilet to the floor, but leaving a gap on the back of the toilet that remains un-caulked so if the toilet leaks, water has an escape route. Repair as recommended by a licensed plumber.
Bathtub / Shower
Tested
The lower edge of the tub should be filled with flexible silicone caulk but has been filled with non-flexible grout. This will allow water entry and eventual damage inside the wall.
The stopper in the family bathtub is missing and requires repair or replacement - or a rubber stopper can be used.
Bathroom Ventilation
Type: Bath fan
General Bath Condition
Standard
Basement Bathroom
Sinks and Cabinets
Tested, Galvanized Steel Pipe Noted
The basement sink has an active leak from the pop up control arm. This is typically easily fixed with a new gasket. Additionally, the pop-up stopper is missing. Excess corrosion indicates a full drain rebuild may be beneficial. This may be a homeowner DIY, handyman repair, or accomplished in conjunction with other plumbing repairs.
Toilet
Tested
Bathroom Ventilation
Type: None noted
General Bath Condition
Standard
Structure and Basement
Structure and Basement Inspection Criteria
Structure. An inspection of the structure will include the visible foundation; floor framing; roof framing and decking; other support and substructure/superstructure components; stairs; ventilation (when applicable); and exposed concrete slabs in garages and habitable areas.
The inspector will:
• Describe the type of building materials comprising the major structural components.
• Enter and traverse attics and subfloor crawlspaces.
• Inspect:
(a) The condition and serviceability of visible, exposed foundations and grade slabs, walls, posts, piers, beams, joists, trusses, subfloors, chimney foundations, stairs and the visible roof structure and attic components where readily and safely accessible.
(b) Subfloor crawlspaces and basements for indications of flooding and moisture penetration.
• Probe a representative number of structural components where deterioration is suspected or where clear indications of possible deterioration exist. Probing is not required when probing will damage any finished surface or where no deterioration is suspected.
Foundation
% of Foundation Not Visible: 20%
Evidence of Seismic Protection: None Found - Old House
Building Configuration: Basement
Foundation Description: Poured concrete
Minor to moderate cracks were noted in the poured concrete foundation. The purpose of the foundation is to connect the weight of the building to well-compacted soils below the house so that the house does not move or settle. Concrete cracking can indicate poorly compacted soils below the house which could require a repair, but small cracks can also be a sign of routine concrete shrinkage. It is not possible to determine or verify the cause of these cracks during a visual inspection. The hope on older buildings is that poorly compacted soils below the foundation are now compacted by the weight of the building and no additional movement will occur. One of the better ways to prevent on-going settlement in buildings is to keep the soils around the house as dry as possible. Additional inspection by a specialist is needed to determine if repairs are needed to prevent additional movement or not. Please note that the scope and urgency of repairs for conditions like this can differ between contractors and you may want to seek more than one additional opinion.
Note: These cracks do not appear recent or include shifting in multiple planes - indicating this may be a historic problem and may allow time for diligence. I recommend additional inspection of this structure by a qualified general contractor or structural engineer to determine the cost and urgency of repairs to prevent on-going settlement.
Floor, Wall and Ceiling Framing
Wall Framing: Not visible
Wall Sheathing: Not visible
Floor Framing: 2x12
Sub-Floor Material: Shiplap
Ceiling Framing: 2x6, Partly visible
Basement
Full
Basement Moisture
I inspected all around the basement for signs of moisture and / or moisture control problems. No water stains, or damaged baseboard were noted and no signs of paint touch up near the floor. The basement did not smell musty at the time of inspection and seems to be performing well to date.
Laundry Facilities
Washer
None noted
Dryer
None noted
Exhaust Duct: Behind Dryer (Plastic Transition Duct)
Plastic dryer transition duct was noted in use to connect the dryer to the rigid vent. This product is not recommended as it has proven to be unreliable and a potential fire hazard. Improvement to a corrugated metal flex duct is recommended.
The electric receptacle to the dryer is three-prong or three-wire system. This is an older configuration. Modern electric dryers circuits require a four-wire system. These older three-wire circuits are still allowed, but be sure to tell your appliance installer that you have a three prong outlet so the cord can be swapped out and the appliance appropriately bonded.
Laundry Sinks
Tested
Laundry Ventilation
Type: None noted
Attic
Insulation and Ventilation Inspection Criteria
Insulation and ventilation. The inspection of the insulation and ventilation includes the type and condition of the insulation and ventilation in viewable unfinished attics and subgrade areas as well as the installed mechanical ventilation systems.
The inspector will:
• Inspect the insulation, ventilation and installed mechanical systems in viewable and accessible attics and unfinished subfloor areas.
• Describe the type of insulation in viewable and accessible unconditioned spaces.
• Report missing or inadequate vapor barriers in subfloor crawlspaces with earth floors.
• Report the absence of insulation at the interface between conditioned and unconditioned spaces where visible.
• Report the absence of insulation on heating system ductwork and supply plumbing in unconditioned spaces.
• Describe any deficiencies of these systems or components.
Attic Access
Crawled partial
Roof Framing and Sheathing
Rafters: 2x6
Sheathing: Tongue and groove
Attic Insulation
Insulation Type: Rock wool, Fiberglass
Approximate Insulation R-Value on Attic Floor: 30
Approximate Insulation R-Value on Attic Ceiling: 0
Approximate Insulation R-Value on Attic Walls: 0
The attic has a combination of old rock wool insulation topped with newer insulation batts. It appears well installed and the attic temperature was close to exterior temperature. This is good for avoiding ice damming and premature shingle aging.
Attic Fan Exhaust Vents
The exhaust ductwork for the bathroom fan is disconnected in the attic and requires repair to ensure fan exhaust is properly venting to the exterior. Having exhaust fans venting into the attic can cause lead to seasonal condensation and moisture control problems and could damage the attic building materials. Repair to ensure proper discharge of air to the exterior and be sure exhaust ductwork is insulated to R-8 or better to reduce risks of seasonal condensation. Consult a general contractor or HVAC specialist for options.
Attic and Roof Cavity Ventilation
Attic Ventilation Method: Soffit vents, Gable vents, Ridge vents, Power ventilator
Attic and roof cavity ventilation is a frequently misunderstood element of residential construction. All roof cavities are required to have ventilation. The general default standard is 1 to 150 of the attic area and ideally, this comes from at least 60% lower roof cavity ventilation and 40% upper, but this is a wild over-simplifications of the subject. As a good guiding principle the most important elements for healthy attic spaces, which are traditionally insulated and ventilated are:
- Make sure the ceiling between the living space and the attic is airtight
- Ventilate consistently across the whole lower part of the roof cavity with low, intake soffit venting
- Upper roof cavity venting is less important and if over-installed can exacerbate air migration into the attic from the living space.
- Avoid power ventilators which can depressurize the attic and exacerbate air migration from the house into the attic.
For more information, please see: Link
About the Inspection
Expectations
Closure: Construction techniques and standards vary. There is no one way to build a house or install a system in a house. The observations in this report are the opinions of the home inspector. Other inspectors and contractors are likely to have some differing opinions. You are welcome to seek opinions from other professionals.
Receipt -- Full Report
123 Sample Lane Spokane WA
Inspection Fee | $0.00 |
Radon Sampling | $0.00 |
Sewer Scope | $0.00 |
$0.00 | |
0.00 | |
PAID |
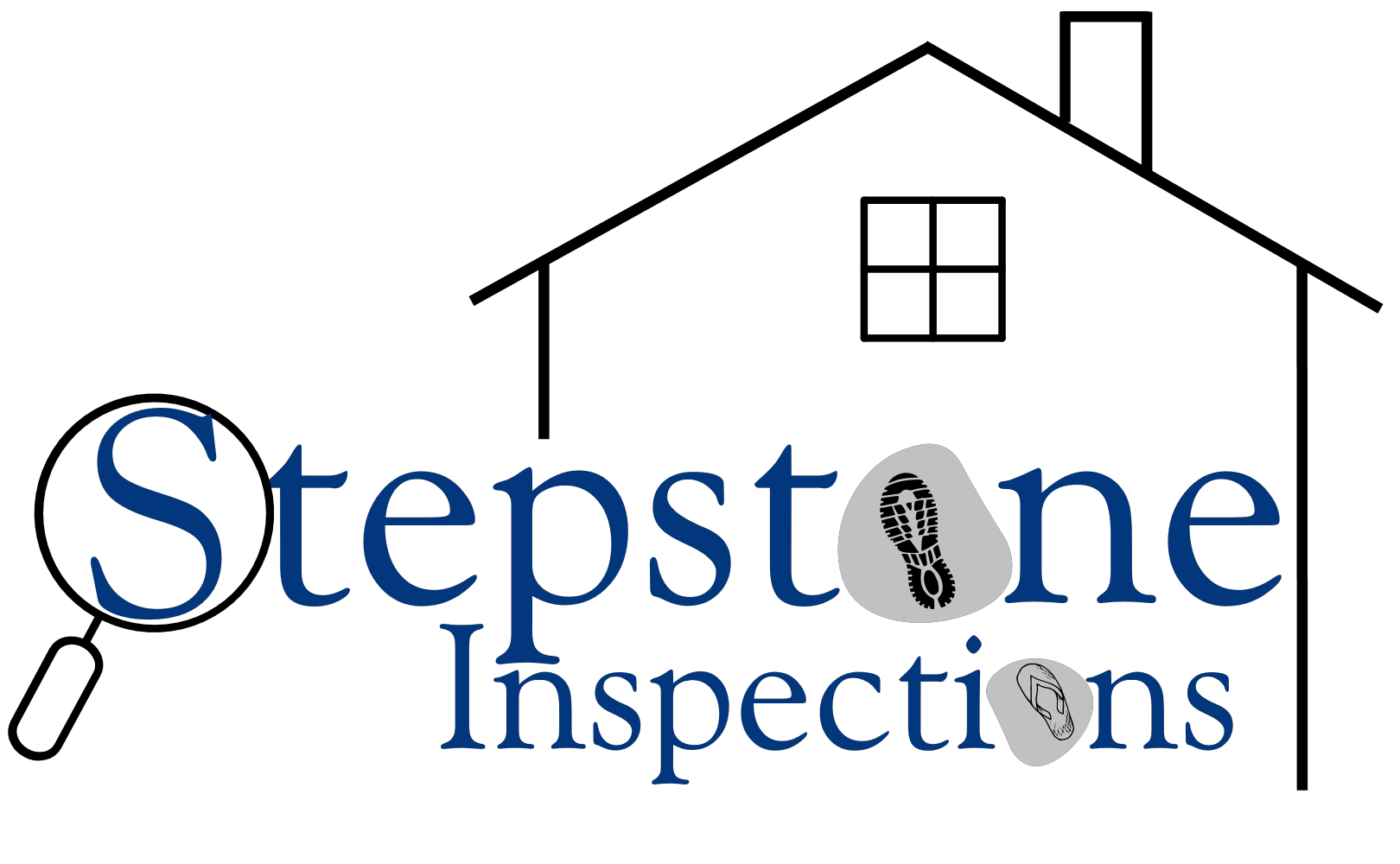