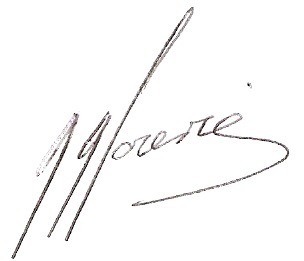
Jurie Fourie, South Africa State License #NACHI14102004
The Scope and Purpose of this Commercial Property Inspection
Purchasing property involves risk
The purpose of this inspection report is to help reduce the risk associated with the purchase or maintenance of a structure by providing professional observations about the overall condition of the structure. A property inspection is a limited visual inspection and cannot eliminate all the risks. Some buildings present more risk than others. If you attended the inspection, I would have tried to inform you of my concerns during the inspection process. This is more difficult to convey in a report and is one of the many reasons why I recommend attendance during the inspection.
A property inspection is not an insurance policy
This report does not substitute for or serve as a warranty or guarantee of any kind. Home warranties can be purchased separately from insurance firms that provide this service.
A property inspection is visual and not destructive
The descriptions and observations in this report are based on a visual inspection of the structure. I inspect the aspects of the structure that can be viewed without dismantling, damaging or disfiguring the structure and without moving furniture and interior furnishings. Areas that are concealed, hidden, inaccessible or unsafe to view are not covered in this inspection. Some systems cannot be tested during this inspection as testing risks damage to the building. For example, overflow drains on baths are generally not tested because if they were found to be leaking they could damage the finishes below. My procedures involve non-invasive investigation and non-destructive testing which limit the scope of the inspection.
This is not an inspection for Building Regulation/Municipal Compliance
Although this inspection report may refer to SANS (South African National Standards) and municipal by-laws, this report is not intended to be an NBR (National Building Regulation) or a local Municipal By-law Compliance inspection. Although some safety issues may be addressed in this report, this inspection is not a safety inspection and I am not required to identify all potential hazards.
This is not an inspection for Mould or Wood Destroying Organisms
The Commercial Standards of Practice of the International Association of Certified Home Inspectors (InterNACHI) do not require me to determine the presence of mould, mildew or fungus! Nor do they require me to determine the presence of wood-destroying organisms (WDO) or pests. Observations of mould-like substances, WDO and pests may be included in this report as a courtesy. These observations are identified by WDO at the beginning of the narratives. However, this report is not a mould or WDO report. Mould and WDO inspections are separate inspections that are performed on request and quoted for and reported separately!
My observations are based on my tertiary qualifications, InterNACHI's Continuing Education requirements, research and workplace experience
Construction techniques and standards vary. There are different ways to build a house or install a system in a house. The observations in this report are based on my tertiary qualifications, research and workplace experience. Other inspectors and contractors may have some differing opinions. You are welcome to seek opinions from other professionals.
The scope of this inspection
This inspection will include the following systems depending on the type of inspection required: exterior, roof, structure, drainage, foundation, roof space, interior, plumbing, electrical and heating. The evaluation will be based on limited observations that are primarily visual and non-invasive. This report may include further research depending on your requirements. The objective of the research, including the review of documents and the performing of interviews, is to augment the information obtained during the inspection and to provide supporting documentation to the inspection report. This inspection and report are not intended to be technically exhaustive.
Your expectations
The overall goal of a property inspection is to help ensure your expectations are appropriate for the building you have bought or are proposing to buy. To this end, I assist with the discovery by showing and documenting observations made during the property inspection. This should not be mistaken for a technically exhaustive inspection designed to uncover every defect in the building. Such inspections are available but they are generally cost-prohibitive to most property buyers and property owners.
Your participation was requested
Your presence was requested during this inspection. A written report will not substitute for all the possible information that can be conveyed verbally by a shared visual observation of the conditions of the property.
Ownership of the report
I am the sole owner of the report and have all rights to it until such time that you have paid the total amount of my invoice. Once paid, the report becomes your property. My inspection and report are for your use only.
How to Read This Report
Getting the Information to You
This report is designed to deliver important and technical information in a way that is easy to access and understand. This report may include a summary page. If you are in a hurry, you can take a quick look at my "Summary Page” and quickly get the critical information for important decision-making. However, I strongly recommend that you take the time to read the full report, which includes digital photographs, captions, diagrams, descriptions, videos and hot links to additional information.
The best way to get the layers of information that are presented in this report is to read your report online, which will allow you to expand your knowledge about your house. You will notice some words or series of words highlighted in blue and underlined – clicking on these will provide you with a link to additional information.
This report can also be printed on paper or in a PDF document.
Chapters and Sections
This report is divided into chapters that parcel the buildings into logical inspection components. Each chapter is broken into sections that relate to a specific system or component of the buildings. You can navigate between chapters with the click of a button on the left-side margin.
Most sections will contain some descriptive information in black font. Observation narratives, done in coloured boxes, will be included if a system or component is found to be significantly deficient in some way or if I wish to provide helpful additional information about the system or the scope of my inspection. If a system or component of the home was deemed to be in satisfactory or serviceable condition, there may be no narrative observation comments in that section and it may simply say “tested,” or “inspected.”
Unless defective or maintenance items are specifically allocated to rooms or areas they should be regarded as generally defective items that can be found throughout the property.
Photographs
Photographs take up a lot of space, therefore, the photographs about a particular defect do not necessarily include all the photographs or defects of the particular defect identified.
Note: For a better view of the photographs included in the report, click on the photographs to enlarge them.
Observation Labels
All narrative observations are coloured, numbered and labelled to help you find, refer to, and understand the severity of the observation. Observation colours and labels that may be used in this report are:
- NOTE:Refers to aside information and /or any comments elaborating on descriptions of systems in the home or limitations to the home inspection.
- COMMENT:A comment of the general condition of various aspects of the property noted during the inspection.
- MAJOR CONCERN:Repair items that may cost a significant amount of money to correct now or in the near future, or items that require immediate attention to prevent additional damage or eliminate safety hazards.
- DEFICIENT:Repair and maintenance items noted during inspection. Please note that some repair items can be expensive to correct such as re-finishing hardwood floors, but are considered simply repair items due to their cosmetic nature.
- MAINTENANCE REQUIRED:A system or component requiring maintenance appears to be functioning as intended, but would benefit from minor repair, maintenance or improvement at this time. General deficiencies include patching, painting, cleaning, cleaning the gutters or changing the filters.
- MONITOR:An area, condition, system or component that is in need of monitoring appears to be functioning as intended and capable of safe usage in its present condition; however, the inspector's concern stated in the report should be monitored or further evaluated by an appropriate person.
- PREVENTATIVE:Any improvement to an area, system, component or condition that would help prevent a deficiency from occurring.
- FUTURE PROJECT:A repair that may be deferred for some time but should be on the radar for repair or replacement in the near future.
Summary Page
The summary page is intended to provide you and interested other parties directly involved with this building a convenient and cursory preview of some of the conditions and components that I have identified within my report as needing further evaluation or service by an appropriately qualified specialist or that pose a potential health and safety risk. It is not intended to be comprehensive, and should not be used as a substitute for reading the entire property inspection report or be viewed as a tacit endorsement of the condition of components or features that do not appear in this summary report. The entire report must be read to get a complete understanding of this report as the Summary Page does not include photographs or photo captions.
Summary
Major Concerns
- HB-17 Hostel Block:
Some bricks appeared to have been dislodged at the top of the southeast corner of the building. If these bricks fall they may be a danger to people using the walkway below. The bricks should be mortared back in place. This is a safety hazard!
- HB-42 Hostel Block:
The padlocks on both ground floor electrical boards were broken allowing unauthorised entry to the circuit breakers. There were uncovered openings in 3 electrical panels' internal covers that expose those who have access to the panel to shock hazards. These openings will need to be covered with approved panel block-out covers. Have a suitably qualified electrician check and repair the installations. This is a safety issue.
- HB-43 Hostel Block:
The exterior of the electrical panel on the 1st-floor was corroded and required further evaluation by a licensed electrician to insure safe and reliable performance. Corrosion outside the panel is a red flag that the panel could be having moisture problems and this could result in poor and unsafe wiring connections. Repair as recommended by a licensed electrician.
- HB-47 Hostel Block:
The gaps and holes at light switches and plug points should be sealed to prevent access to the wiring! This is a safety hazard! Have these gaps and holes sealed!
- HB-51 Hostel Block:
The wiring to the floodlight mounted on the exterior of the building was suspect and required to be corrected to building regulation standards.
- HB-55 Hostel Block:
The electric tankless hot water heater was not working. There was no isolator on the electrical supply to the geyser as required by the building regulations. The hot water heater will need to be repaired or replaced.
- HB-76 Hostel Block:
The tankless electric geyser was in working order but the isolator was faulty! It could not be switched off! Have this checked and repaired by a registered electrician!
- HB-103 Hostel Block:
All the hose reels should be checked and serviced if necessary. All were overdue for an inspection!
Some are shown below:
- HB-104 Hostel Block:
All the fire extinguishers should be checked and serviced if necessary. Some fire extinguishers need to be erected onto brackets within easy reach. Most were overdue for an inspection!
Some are shown below:
- HW-30 House with Workshop:
The main electrical panel and service disconnect was obstructed which prevents easy access to the panel front incase of an emergency! I recommend that the stored goods be moved from the face of the panel for safe and proper access. The work space required in front of the main panel is 900 mm from the front, 2.2 m vertically from the floor and 760 mm width.
- HW-31 House with Workshop:
Some plugs were not connected through the earth leakage circuit breaker which poses a serious safety risk! The plugs should either be disconnected or correctly wired through the ELCB! Have this done a a registered electrician!
- BS-26 Beauty Salon:
Inadequate labelling of the main electrical panel circuit breakers was noted during the inspection. Some circuit breakers on the board were not identified. This should be corrected for improved safety.
- G-5 Grounds:
A portion of the precast concrete wall at the south side of the property was leaning, potentially rendering it unstable. The wall may need to be stabilised to prevent further movement.
- G-6 Grounds:
The precast boundary walls on the north, east and south were plastered to provide a decorative finish. In some areas, the decorative finish had cracked or fallen off the wall portions of the wall. Where this has occurred any areas of potential collapse must be removed to prevent possible further collapse! This is a safety concern!
- PS-8 Pools and Spas:
This sub-board control of the pool pump was in a shocking state. Rather replace it with a new board that is easily accessible.
Deficients
- HB-7 Hostel Block:
A crack in the parapet wall as a result of the differential movement in building materials. This section of the wall should be rebuilt making sure that it is not attached to the staircase to allow for expansion and contraction! Note that the steel L on top of the wall provided stability to the steel columns that were providing additional support for the cantilever slab but was not bolted to the top of the wall along its length to allow for expansion and contraction!
- This crack had been caused by the fixing through the angle bolted to the wall. It was not structurally significant but will allow moisture intrusion into the wall. Patching and paint were required.
- The offset crack in the brickwork was caused by differential movements between the brickwork and steelwork.
- The fixing points here were the problem. The self-supporting staircase can be attached to the metal angle on top of the wall but should be separated from the balcony wall and balcony slab because the steel's expansion and contraction far exceed that of the brickwork and concrete.
- Remove this section of the wall and rebuilt it free of the staircase steelwork.
- HB-9 Hostel Block:
The ceiling in the gym was moisture damaged in various areas from roof leaks. This could mean the roof screw gaskets had failed or the roof sheeting had leaked at the side laps or both! It is far better and longer lasting to replace roofing screws and gaskets than to patch over the screws with an acrylic waterproofing system. Roof sheeting manufacturers recommend that all low slope IBR roofs below 15° should be sealed and stitched with roof screws and gaskets every 600 mm along the length of the side laps of the sheeting. Furthermore, they recommend that the wide pans of the roof sheeting should be turned up to prevent windblown rainwater from entering the building between the ridge and roof sheeting. Have a suitably qualified roof contractor check and repair the roof as necessary!
- HB-10 Hostel Block:
Several barge boards were missing on the gable sides of the IBR roof on the east and west side of the house which exposes the roof structure to the elements. The barge boards must be installed to prevent moisture damage to the roof structure.
- The asbestos L-profile bargeboards were not the correct material to use on this roof's verges! With the long fixing points between roof purlins, strong winds will continually blow the bargeboards off the roof which is a safety hazard. Rather fit metal barge boards!
- Missing bargeboards on the east side of the building.
- Falling barge boards are a safety hazard!
- The open ends of the metal roof purlins can allow wind-blown rainwater to penetrate into the building!
- HB-12 Hostel Block:
The stairs appeared to have only been painted with red oxide primer. Areas of corrosion were noted on both the structure and the guardrails. All the metal should be sanded down, cleaned, primed and painted to protect the staircases and guardrails.
- Note the corrosion on the landing!
- The stair treads were corroded.
- Pooling of rainwater on the landings and stair treads should be avoided! Drill holes in the areas affected to allow the rainwater to drain away!
- Corrosion on the stair structure.
- Corrosion, if allowed to continue, will result in serious damage to the structure of the stairs.
- HB-14 Hostel Block:
The roof rainwater spouts on the verandah and balcony were undersized and blocked by leaves and other debris. Many spouts were too high and none were waterproofed which allowed pooling on the balcony and verandah. Hail may also block the outlets. I recommend that the spouts be replaced with larger diameter spouts (50 mm) at the correct height in relation to the balcony floor finish that can be properly sealed against the brickwork to prevent moisture intrusion between the spouts and the parapet walls.
Some examples are shown below:
- HB-21 Hostel Block:
The columns appeared to have only been painted with red oxide primer. Areas of corrosion were noted on the structure. All the metal should be sanded down, cleaned, primed and painted to protect the steel structure against corrosion.
- HB-22 Hostel Block:
Moisture damage on the bathroom walls from the leaking of the plumbing wastepipes and fixtures!
- Flaking Paintwork and efflorescence on the column for a waterpipe leak.
- Efflorescence was a sign of moisture in the wall structure that had evaporated leaving behind a white powder which are salts absorbed by the water in the structure.
- Efflorescence was a sign of moisture in the wall structure that had evaporated leaving behind a white powder which are salts absorbed by the water in the structure.
- Moisture damage and flaking paintwork as a result of penetrating damp in the wall.
- Flaking paintwork as a result of penetrating damp in the wall.
- Flaking paintwork as a result of penetrating damp in the wall.
- HB-24 Hostel Block:
The door thresholds were not sufficiently sloped to the outside to throw the water away from the doors. The thresholds and frames should be sealed at the junction of the frames with the thresholds and brickwork and the junction of thresholds and brickwork to prevent corrosion from occurring. There may have been windblown rainwater entering through the door. The doors will require weatherboards or aluminium weather door seals fitted to the doors in the absence of a correctly placed water bar on the door threshold.
- The flat thresholds had probably allowed windblown rainwater to enter under the doors.
- Wind-driven rainwater was entering here! The doors should be sealed with silicone to prevent moisture damage to the doors.
- Signs of rainwater seeping through the bottom ledger on the inside of the door. This was common to most of the doors.
- HB-25 Hostel Block:
Many exterior doors required adjustment and repair for proper operation. At the time of inspection, the doors were hooking on the frame, had faulty mortice locks, were not latching properly or had missing striker plates and more.
Some examples are shown below:
- Mortice lock is stuck in the open position.
- The tongue of the mortice lock was stuck inside the mortice lock.
- No striker plate on the door frame for the door lock to latch into.
- The door and mortice lock face plate was chafing on the frame. Adjustment was required.
- The hinge pins should be seated properly.
- Doors binding on the door frame will eventually loosen the hinges and not close properly.
- Damaged door frame at the striker plate seating and a missing striker plate.
- Loose striker plate and screws prevent the door from closing!
- HB-28 Hostel Block:
Both the external timber doors and the steel door frames at the 2nd-floor gym were moisture damaged. The doors should be replaced by a professional carpenter to function correctly.
- The bottom of the southeast side door was badly moisture damaged. The door frame was corroded in places! Note the flat threshold!
- The whole surface of the gym door was very dry to the touch and had no protection against moisture damage.
- The whole surface of the gym door on the northeast side was very dry to the touch and had no protection against moisture damage.
- The bottom portion of the exterior of the gym door was moisture damaged. The doors should have weatherboards fitted to the bottom of the doors to divert rainwater away from the doors and thresholds.
- The lock cover plate was damaged and should be replaced! The door hit against the door frame and could not be closed. Note the holes between the brickwork and door frame. All door frames should be properly sealed at the brickwork!
- HB-30 Hostel Block:
Most of the bedroom and bathroom window putty was cracked and in some instances, the protective paint was flaking. Painting the putty will seal the cracks for some time but replacement is preferable! The windows frames appeared to require sanding down and repainting anyway! Most of the bedroom and bathroom windows were not properly sealed at the sills and the reveals of the windows. Monitor during or after rainstorms to determine whether windblown rainwater reaches these areas. If it does, the windows will need to be sealed to prevent moisture intrusion into the walls!
Some examples are shown below:
- These gaps at the window reveal and sill may allow moisture intrusion into the brick reveal and sill.
- Cracked putty and peeling window paint on the bedroom window.
- Cracked putty on a 1st-floor window.
- HB-31 Hostel Block:
The brick window sill of this bedroom window on the ground floor needed to be repaired to prevent moisture intrusion into the sill and wall.
- HB-33 Hostel Block:
A couple of tiles in room 10 were broken. They should be replaced or the holes filled with mortar.
- HB-34 Hostel Block:
There were cracks in tiling at some door openings. Cracks of this nature are normally due to bad building practices. Movement joints should always be formed through the slab and floor finish at doorways. Floors always crack at the weakest (narrow) part of concrete slabs.. In most cases, the cracking in the surface of the surface bed appeared to be more unaesthetic than structurally significant.
- HB-36 Hostel Block:
There was efflorescence and flaking paintwork that was signs of rising damp and penetrating damp on the lower portion of the walls internally in bedroom 1 which appeared to be a result of moisture intrusion from a source such as a leak in the shower, water pipe leak or a waste pipe leak. in the bathroom next door. I recommend an inspection and repair by a suitably qualified plumber. The wall can be repaired and painted once the source of the moisture is found and repaired.
- HB-37 Hostel Block:
Generally, the floor tiling, guard walls and guardrails were in a reasonable condition. Additional items are specifically listed
- HB-38 Hostel Block:
A few areas on the ground and 1st floor had cracked and missing potions of tiles on the floor and skirtings. The cracked and broken tiles appeared to be the result of the lack of expansion joints, hollow tiles or the result of physical damage. The damage was not structurally significant.
- HB-40 Hostel Block:
The metal walkway on the east side of the gym required sealing between the walkway and the gym walls to prevent the staining below the walkway. An appropriate silicone sealer will be required!
- HB-41 Hostel Block:
The plasterwork on the edge of the upper walkway slab was stained and moisture damaged! The plasterwork will need to be repaired and painted. In those areas where the plasterwork is repaired form a drip groove about 25mm in from the edge of the bottom of the slab!
- HB-48 Hostel Block:
Not all the rooms had ceiling fans installed. The installed fans were tested. The majority of the fans were unbalanced and should be adjusted with weights on the blades to function properly.
- HB-49 Hostel Block:
Some ceiling lights in the bedrooms did not respond to switching. The fluorescent tubes should be replaced to check if the fittings are in working order.
- HB-50 Hostel Block:
There were a few places on the inside of the bedrooms where junction boxes had no covers. Have covers fitted!
- HB-53 Hostel Block:
The waste piping on the exterior of the bathrooms on the ground and 1st floor required general maintenance and repairs.
- I could not determine what was used to connect or seal this waste pipe. PVC adhesive should have been used!
- Another place where I could not determine what was used to connect or seal this waste pipe. PVC adhesive should have been used!
- Another elbow sealed with the incorrect adhesive or sealer. Note the broken strapping on the PVC strap on boss!
- These waste pipes required addition support! Have the appropriate brackets installed.
- A hole in this elbow on this wastepipe! The elbow should be replaced!
- Another repair on wastepipe that had leaked or is leaking!
- This waste pipe had been blocked off from a plumbing fixture rendering it unusable!
- This Polycop waterpipe is only suitable for underground use. It does not have a SABS mark. Rather replace it with a copper pipe!
- HB-65 Hostel Block:
The wall and ceiling above the showers and geyser were moisture damaged and stained. This could be a result of leaking from the bathroom above or condensation. Please note this condition risks concealed water damage.
- HB-66 Hostel Block:
Only one of the 2 extractor fans were operational! Repair or replacement was required!
- HB-72 Hostel Block:
The extractor fans were not operational. The fans will need to be repaired to provide adequate ventilation. The windows should be opened to allow through ventilation.
- HB-74 Hostel Block:
Of the four showers, 3 appeared to be defective! Two shower heads were leaking at the connection of the shower rose and arm. One shower head was missing!
- HB-81 Hostel Block:
The pedestal of this basin had broken and should be replaced. Pedestal provide secondary support only for the basin which is bolted onto the wall. The basin and taps were functional.
- HB-82 Hostel Block:
The electric tankless hot water heater had been removed. The hot water heater will need to be replaced to provide hot water to the bathroom.
- HB-88 Hostel Block:
The ceiling above the showers were moisture damaged and stained. This could be a result of leaking from the bathroom above or condensation. Please note this condition risks concealed water damage.
- HB-89 Hostel Block:
The extractor fans were not operational. The fans will need to be repaired to provide adequate ventilation. The windows should be opened to allow through ventilation.
- HB-91 Hostel Block:
The electric tankless hot water heater had been removed. The hot water heater will need to be replaced to provide hot water to the bathroom.
- HB-93 Hostel Block:
A tap on a basin next to the bath was loose and required repair to prevent leaks and insure reliable performance.
- HB-95 Hostel Block:
The toilet seat on this toilet pan was broken and loose and required replacement.
- HB-98 Hostel Block:
Poor functional flow was noted at the hot water side of the bath mixer tap. This may be from localized restrictions in the water supply or it may be indicative of a larger problem with the supply plumbing system. Hire a licensed plumbing contractor to further evaluate and repair.
- HB-100 Hostel Block:
The showers had defects! A shower head were leaking at the connection of the shower rose and arm. One stopcock cover was missing which will allow moisture intrusion into the wall! Another appeared to have been leaking at the shower head!
- HW-2 House with Workshop:
Minor floor settlement and cracking was noted in the workshop floor during my inspection indicating a need for preventative maintenance. The cracks appeared to be the result of thermal movement and slight subsidence as a result of the lack of expansion joints in the floor slab. The cracked areas should be cleaned out and filled with cold asphalt or concrete to prevent moisture intrusion under the concrete slab that may cause further settlement.
- HW-7 House with Workshop:
Viewed from the trap door, none of the roof purlins and trusses internally in the roof space appeared to be seriously moisture damaged at this stage! However, another season of rainwater intrusion may change this situation drastically. The roof sheeting should be sealed urgently to prevent further damage to the roof structure.
- HW-11 House with Workshop:
The original front veranda of the house had been covered with a corrugated roof and appeared to be used as a storage area. The roof had leaked onto the roof beams supporting the roof. The roof will need to be sealed to prevent further moisture intrusion.
- HW-17 House with Workshop:
On buildings that have do not have the DPC running al the way to the outside of the joint between the plinth and superstructure walls, a mortar "bridge" may result in rising damp above the damp proof course level (DPC) if the brickwork on the plinth is not properly separated from the plasterwork on the superstructure at floor level. The only way to separate the two is to form a deep joint horizontally through onto the DPC at the DPC level to prevent rising damp bridging the DPC into the superstructure above. Consider having these joints properly installed to prevent rising damp into the structure above the floor levels to save on future expensive maintenance (the joint can be cut with doubled up cutting discs on an electric saw or angle grinder)!
Examples are shown below:
- Rising damp manifesting as crazing cracking on the wall above the driveway paving.
- The open joints in the driveway and the wall allows rain and stormwater to collect in the joint causing rising damp. Seal the joint with mortar.
- Fine cracking and bubbling paintwork along the cracking of the plasterwork was an indication of the moisture trapped in the wall.
- HW-19 House with Workshop:
Water stained and rotted roof structure was evident under the eaves at the northeast side the house which is an indication that the gutters have overflowed in the past. The timber roof and structure should be repaired as soon as possible to prevent the roof from deteriorating further.
- HW-20 House with Workshop:
The "back door" consisted of a covered safety gate to provide privacy. A property timber or steel door should be installed.
- HW-21 House with Workshop:
The threshold was missing on the side door. This is a common area where rising damp occurs as water collects on the unfinished threshold and soaks into the structure below and on the sides of the door. Repair the threshold sloping it to the outside to ensure that rainwater flows away from the door.
- HW-23 House with Workshop:
The window putty on all the windows of the building was cracked or missing. Badly cracked putty should be removed, the putty redone and painted to prevent leakage and corrosion of the frames. Where the window putty has been replaced, the putty should be painted within 2 weeks to prevent the premature drying out and cracking of the putty.
Examples are shown below:
- HW-24 House with Workshop:
There were gaps on the window sills and the reveals (sides) which were open to moisture intrusion and will require sealing. The window exteriors should be sealed with silicon at the junction of all window frames and the brickwork at the heads, reveals and sills. Gaps at the junction between the brickwork and the frames can allow moisture intrusion into the wall structure.
Some examples are listed:
- HW-25 House with Workshop:
This house has a hodge podge of different floor finishes ranging from painted screeding to rubber tiles that are in generally less than average condition. Depending on what the house will be used for the floors may require updating for comfort and performance.
- HW-26 House with Workshop:
There was evidence of some moisture damage to most of the ceilings and walls in the house. There were cracks at the cornices and moisture staining on some ceilings that would need repair. The ceiling damage was caused by leaks in the roof. Repairs to the ceilings can be done once the roof is repaired!
The following issues were observed:
- There was bubbling paint on a wall.
- Cracks between the cornices and walls.
- Staining between the cornices and walls.
- Staining on walls
- Deviations in the ceiling level.
- Ghosting.
- A partly collapsed ceiling.
- A hole in the ceiling.
The above are all indications of moisture damage! Some examples are shown below:
- HW-28 House with Workshop:
There were some obvious observable signs of moisture staining and evidence of roof leakage on the beams of the roof. See Floor, Wall and Roof Structure.
- HW-32 House with Workshop:
These plug points were inoperative. No sign of power was found when the plugs were switch on and tested. Have this further investigated and repaired as needed. The electrician who does the electrical CoC should repair this!
- HW-33 House with Workshop:
There were two hobs, two eyelevel ovens and one under counter oven. Only the hob above the under counter oven was operational and responded to the the controls.
- Only this hob was operational!
- This hob was inoperative!
- These oven were inoperative
- HW-34 House with Workshop:
One light fittings was not functional in the bedroom. Either the globes was defective or the light fitting was defective. All the light fittings and globes should be checked and replaced where necessary!
- HW-35 House with Workshop:
There was no bathroom in the house. The toilet and basin at the back entrance to the house was not functional. There was no water supply to the house!
- HW-36 House with Workshop:
There were two sinks stands in the house which were inoperative because of the lack of a water supply.
- BS-8 Beauty Salon:
The exposed surfaces of portions of the roof tiling showed signs of weathering and appeared to be porous. While a porous roof tile will not necessarily leak, a porous tile is weaker than a tile that's in good condition. The increase in holes and little cracks will compromise the overall integrity of the tile, making it more susceptible to breaking or further damage. As the porosity of the tiles increases, things such as storms, strong winds or walking on them could cause the tiles to completely break apart. Sealing and repainting the concrete roof tiles will extent their lifespan by reducing further weathering and will reduce maintenance and possible replacement costs in the long run.
- BS-9 Beauty Salon:
There were some tiles that were not properly interlocked on areas of the roof. These can allow the ingress of rainwater onto the roof structure and into the house under windy conditions. The tiles should be adjusted and fixed to the roof structure to interlock properly.
- BS-10 Beauty Salon:
All bargeboards were incorrectly installed and had allowed wind-blown rainwater onto the timber roof structure that they were fixed to. The bargeboards are not merely decorative and should be installed flat onto or against the underside of the ridge of the roof tiles to prevent the ingress of water and deterioration of the roof structure under the last row of tiles at the roof verge. Employ a suitably qualified roofing contractor to refit or replace the barge boards. There may be additional concealed water damage to the roof structure!
The following issues were observed:
- The bargeboards should have been installed flat onto the roof tiles to prevent the ingress of windblown rainwater and the deterioration of the roof timbers on the verge of the roof (see the example).
- The counter battens and tilting battens had been exposed to the ingress of rainwater.
- Some of the bargeboards were pulling away from the counter battens they were fixed to.
- Most of the nails securing the bargeboards were corroded.
- Moisture damaged roof structure.
- Missing bargeboards.
- Peeling flaking paintwork on the bargeboards.
Some examples are shown below:
- BS-12 Beauty Salon:
The gutters and downpipes were old and incomplete and appear to be close to the end of their useful service life. I noted some gutters were corroded. While repair is possible in the short term, replacement with new gutters and downpipes is recommended for scheduled maintenance.
Some of the shortcomings noted:
- Some gutters on the house were corroded and appeared to be leaking in places.
- When a coating or painted finish fails on a galvanised metal gutter, rust soon sets in.
- A gutter stop end was missing. Replace to prevent splashing up on the wall of the house.
- Downpipes were missing.
- There were no gutters on some eaves.
Some issues are shown below:
- BS-20 Beauty Salon:
The window putty at the of the windows of the house was cracked. Badly cracked putty should be removed, redone and repainted to prevent leakage and corrosion of the frames. Where the window putty has been replaced, the putty should be painted within 14 days to prevent the premature drying out and cracking of the putty.
- BS-22 Beauty Salon:
There was some unevenness in certain areas where internal walls had been removed to enlarge the usable area.
- BS-24 Beauty Salon:
There were signs of rising damp, bubbling paintwork and flaking paintwork on the lower portion of the walls which appeared to be a result of moisture intrusion from an external source such as pooling water on the paving or from splashing up from the gutters where the downpipes were missing. The walls should be monitored externally after the next rainstorm to check if water is pooling against the wall structure. If water is pooling against the structure the water should be directed away from the walls.
- Splashing up from the gutter.
- Seal up the holes to prevent moisture intrusion!
- G-4 Grounds:
It appeared that stormwater was pooling close to or against the buildings as a result of the level and slope of the landscaping on the east side. As a preventive measure drainage and/or grading conditions in these areas should be improved upon to prevent this condition from occurring.
- G-7 Grounds:
The steel palisade fencing and gates bordering the front of the property were rusting and may have a limited future service span if not properly maintained. Sanding down, priming and painting were required.
- G-8 Grounds:
The security gates were not functional. The motors were not functional or missing. There did not appear to be any system of locking the gates and was a security risk. The gate motors should be repaired as soon as possible or alternative arrangements be made to secure the gates in a closed position.
- PS-2 Pools and Spas:
There was some cracking above the waterline level below the pool coping. Care should be taken not to fill up to or above the cracking until the cracks are sealed. I recommend that the pool body be evaluated by an appropriately qualified swimming pool specialist for further recommendations and repairs.
- PS-3 Pools and Spas:
The marbelite pool finish was stained and flaking in places. The marbelite finish on a swimming pool usually lasts between 15 to 20 years. The pool will need to be completely drained so that the flaking marbelite can be removed and redone or fibreglassed. Consult with a pool specialist.
- PS-5 Pools and Spas:
The filter multi-port valve at the pool filter was damaged and needed to be replaced.
- PS-10 Pools and Spas:
The pool gate did not comply with safety standards. The gate for the pool opens in toward the pool. Gates for pools need to open away from the pool. Any gate that gives pool access is required to be self-closing and self-latching.
- PS-11 Pools and Spas:
Sections of the pool coping have lifted off the bond beam and will need to be repaired. No expansion joint had been provided between the pool coping and the pool paving. Expansion joints are necessary as they help prevent cracking of the coping and the pool tiling.
- PS-12 Pools and Spas:
There were cracks and missing grout in the joints between the copings and pavers of the pool. At a minimum, the joints will need to be filled with an appropriate grout to help prevent additional cracks or loosening of the copings and pavers.
- PWDO-1 Pests and Wood Destroying Organisms:
There was evidence of termite infestation on the southwest side of the property. I recommend an additional inspection by a pest control operator to further evaluate the property and treat the infestation as recommended. A guarantee from a pest control officer or company that is a member of the South African Pest Control Association (SAPCA) should be issued. The certificate of guarantee should state that termite proofing was done in accordance with National Building Regulations and guaranteed for 5 years from the date of issue.
- IA-1 Invoice and Attachments:
Maintenance Requireds
- HB-27 Hostel Block:
One sliding door at the gym was not fully functional. The sliding action was reasonably stiff. The door required adjustment and repair to function properly. The other sliding door was locked and could not be tested!
- HB-29 Hostel Block:
Some of the steel windows in this building were very exposed to the weather and will require regular painting and sealing maintenance to preserve the windows and prevent corrosion. At the time of inspection, some windows were in need of maintenance. There were gaps at some window sills and the reveals which were open to moisture intrusion and will require sealing. This is especially important at window exteriors where there is less protection from a reduced roof overhang or balcony overhang. The maintenance will need to be done soon.
Some examples are shown:
- The west-facing windows on the 2nd floor had peeling paint on the window putty that should be maintained to prevent further deterioration of the putty and corrosion of the window frames.
- Note the corrosion of the window hinge!
- The 2nd-floor windows on the gym required serious maintenance on the putty and general paintwork of the windows.
- The exposed windows required sealing around the window frame and sills to prevent moisture intrusion!
- HB-58 Hostel Block:
The toilets were functional and responded properly when flushed. Leaks were observed at the wastepipe, cistern flush pipe or pan connector at the time of the inspection.
- HB-59 Hostel Block:
One cistern could not be flushed because the cistern flushing handle had broken. The handle was being replaced at the time of the inspection.
- HB-60 Hostel Block:
A urinal was taped and marked as faulty! It appeared to have been leaking!
- HB-61 Hostel Block:
A basin pedestal had been replaced to support a basin but had not been installed properly.
- HB-62 Hostel Block:
Of the four showers, 3 appeared to be defective! A shower head were leaking at the connection of the shower rose and arm. One shower head was missing! Another appeared to have been leaking at the shower arm at the tiled wall!
- HB-64 Hostel Block:
There were cracked wall tiles in the shower area, which should be repaired or replaced to forestall moisture intrusion into the structure and floor.
- HB-67 Hostel Block:
Taking into consideration the defective, maintenance or deferred items listed above, this bathroom was only in a partly serviceable condition. The bathroom should not be used until the defects listed above are repaired.
- HB-70 Hostel Block:
A urinal was taped up to prevent use! It appeared to have been leaking!
- HB-71 Hostel Block:
The toilets were functional and responded properly when flushed. Leaks were observed at two toilets at the wastepipe or cistern flush pipe at the time of the inspection.
- HB-75 Hostel Block:
The ceiling above the toilets and showers were moisture damaged and stained. This could be a result of condensation or leaking from the gym above.
- HB-78 Hostel Block:
Taking into consideration the defective, maintenance or deferred items listed above, this bathroom was only in a partly serviceable condition. The bathroom should not be used until the defects listed above are repaired.
- HB-79 Hostel Block:
This basin was not functional. Both taps had been taped to prevent open the taps.
- HB-80 Hostel Block:
One of the taps on this basin was not functional and will need to be repaired or replaced.
- HB-83 Hostel Block:
The toilets were functional and responded properly when flushed. Leaks were observed at one of the toilets at the wastepipe or cistern flush pipe at the time of the inspection.
- HB-85 Hostel Block:
The fiberglass bath had scratches and stains on the bath finish. Hire a specialist to restore the cosmetic finish. Although this can be done with a repair kit from the hardware store without hiring a specialist, it can be difficult to match the existing colour.
- HB-86 Hostel Block:
The bath shower wand was not functional and required repair. The shower wand was leaking at the connection of the shower wand handle.
- HB-90 Hostel Block:
Taking into consideration the defective, maintenance or deferred items listed above, this bathroom was only in a partly serviceable condition. The bathroom should not be used until the defects listed above are repaired.
- HB-96 Hostel Block:
The toilets were functional and responded properly when flushed. Leaks were observed at the toilets at the wastepipe, cistern flush pipe or pan connector at the time of the inspection.
- HB-99 Hostel Block:
The acrylic or fiberglass bath had scratches and stains on the bath finish. Hire a specialist to restore the cosmetic finish. Although this can be done with a repair kit from the hardware store without hiring a specialist, it can be difficult to match the existing colour.
- HB-101 Hostel Block:
Taking into consideration the defective, maintenance or deferred items listed above, this bathroom was only in a partly serviceable condition. The bathroom should not be used until the defects listed above are repaired.
- HW-9 House with Workshop:
Corrosion was noted on the corrugated roofing material. For extended service life from this roofing material I recommend removing the corrosion and sealing with a rust inhibitive paint. Acrylic and fabric waterproofing applied over screw heads do not provide long term leak protection and will need to be monitored and maintained frequently to help prevent moisture intrusion. Screw and gasket replacement is usually a better option! Consult with a qualified roofing contractor about the best options to sealing and repair the roof sheeting to prolong the useful life of this material and prevent the spread of corrosion.
- HW-14 House with Workshop:
Part of the bargeboards were missing on the house. The bargeboards around the roof needed to be repaired, cleaned and painted.
- HW-18 House with Workshop:
Paint loss, patchiness and deterioration was observed to the plastered and painted walls on all sides of the house. I recommend that the walls be repainted for protection against the elements. The areas to be repainted should be sealed either with a plaster primer or sealer before the top coats are applied.
- BS-11 Beauty Salon:
A fascia board was broken. The fascia board should be repaired or replaced to prevent possible or further damage to the roof structure.
- BS-14 Beauty Salon:
The exterior walls need to be re-painted to preserve and maintain the wall finish. Budget for re-painting the exterior in the near term. This is a routine maintenance item. Examples of specific observations noted during the inspection include:
- fine cracking of the plaster finish
- Fading of the paint finish on the sun-exposed sides of the building.
- BS-18 Beauty Salon:
The sliding doors on the north side were not fully functional. The sliding action was very stiff. The doors required adjustment and repair to function properly.
- BS-19 Beauty Salon:
Some of the steel windows in this house were very exposed to the weather and will require regular painting and sealing maintenance to preserve the windows and prevent corrosion. At the time of inspection, some windows were in need of maintenance. There were gaps at some window sills and the reveals which were open to moisture intrusion and will require sealing. This is especially important on window exteriors where there is less protection from a roof overhang. The maintenance will need to be done soon.
Monitors
- HB-77 Hostel Block:
One toilet door was locked and the cubicle could not be accessed. It may be the the toilet was not functional!
- HB-87 Hostel Block:
The showers was not tested. The showers was being used for storage and as a laundry preventing testing.
- PS-4 Pools and Spas:
The filter will need to be evaluated by an appropriately qualified swimming pool contractor for further remarks and recommendations.
- PS-7 Pools and Spas:
The pool pump was not tested. The water level was too low.
Preventatives
- HW-12 House with Workshop:
On all metal roofs the pans (valleys) of all sheets should be turned up at the top end to stop rainwater from being wind driven over the roof sheeting and into the building. On these roofs they did not appear to be! Have this done!
- HW-16 House with Workshop:
The roof gutter system for this building was incomplete and required installation and repairs to ensure proper control of roof runoff. Gutters are installed on buildings to control rainwater discharging from the roof. Uncontrolled rainwater discharging onto the ground or paving erodes paving and removes the jointing between the paving. Furthermore, the falling rainwater causes splashing up onto the lower portions of the house's walls. This splashing up against the walls can cause serious damage to plastered and painted finishes and will cause rising damp. Serious consideration should be given to the installation of a complete roof drainage system to control and direct rainwater away from the house.
- BS-16 Beauty Salon:
The top of the wall should be waterproofed to prevent moisture intrusion in the wall. Acrylic and membrane waterproofing and silicon systems are usually used for this application.
Future Projects
- HB-19 Hostel Block:
The plastered walls on the exterior of the building will require repainting within the next 12 months to preserve the condition of the plasterwork on the building. Allow for it in the maintenance budget!
- HB-26 Hostel Block:
Budget to repaint door frames and the exterior of the doors to ensure protection against the elements.
The Complete Report
Hostel Block
Foundation
Floor, Wall and Roof Structure
Roofing
Fascia boards, Barge boards and Verge Tiles
Exterior Stairs
Roof and Balcony Drainage
Exterior Walls
Eaves and Verges
Exterior Doors and Thresholds
Window Exteriors and Sills
Interior Floors and Floor Materials
Interior Walls and Ceilings
Balconies and Verandahs
Electrical
Plumbing
Ground Floor Male Bathroom
1st Floor Male Bathroom
Ground Floor Female Bathroom
1st Floor Female Bathroom
Fire Suppression
House with Workshop
Foundation
Floor, Wall and Roof Structure
Roofing
Fascia boards, Barge boards and Verge Tiles
Roof Drainage
Exterior Walls
Eaves and Verges
Exterior Doors and Thresholds
Window Exteriors and Sills
Interior Floors and Floor Materials
Interior Walls and Ceilings
Balconies and Verandahs
Electrical
Plumbing
Beauty Salon
Foundation
Floor, Wall and Roof Structure
Roofing
Fascia boards, Barge boards and Verge Tiles
Roof Drainage
Exterior Walls
Exterior Doors and Thresholds
Window Exteriors and Sills
Interior Floors and Floor Materials
Interior Walls and Ceilings
Electrical
Plumbing
Grounds
Driveways, Walkways and Flatwork
Gradients, Drainage and Elevations
Boundary Walls, Yard Walls, Gates and Fences
General Comments
Building Characteristics, Conditions and Limitations
The Occupational Safety Act requires that all house electrical installations must be installed and repaired under the control of a registered electrician. The act also requires that the property owner must be in possession of a Certificate of Compliance (CoC) at all times for any new installations and changes to the wiring of the building. An updated document is required every time a property is sold (transferred) and every time an electrical installation is altered. Make sure you have a copy!
By law, property owners in South Africa have to ensure that all the buildings on their properties are on the plan and that the plans have been approved by the relevant local authorities and comply with Building Regulations. Final approval of the building is in the form of an Occupation Certificate which is issued by the building control element of the municipality to certify that the construction have been executed in accordance with the approved drawings. It is important to have the approved plans and occupation certificate for the property. The Building Regulations apply to all buildings within the borders of South Africa.
Hostel Block
Foundation
The hostel's foundations appeared to be concrete strip foundation footings. Strip footings are a type of shallow foundation that is used to provide a continuous, level or stepped strip of firm concrete support for walls built centrally above them. Concrete strip footings can be reinforced or not depending on the soil founding conditions. The footing size or depth below the ground level could not be verified.
Floor, Wall and Roof Structure
The hostel's internal and external wall structure was generally in a good condition. Additional exceptions are specifically listed.
The visible portions of the concrete ground floor structure appeared to be in satisfactory condition at the time of the inspection.
The visible portions of the house's 1st-floor slab and 2nd-floor slab structure appeared to be in good condition at the time of the inspection.
The eaves and verges on the house were in a reasonable condition except where defects are specifically listed.
Viewed from the ground and 2nd-floor, the roof structure appeared to be in satisfactory condition considering the roof structure's age. Other roof and ceiling issues may be mentioned elsewhere.
A crack in the parapet wall as a result of the differential movement in building materials. This section of the wall should be rebuilt making sure that it is not attached to the staircase to allow for expansion and contraction! Note that the steel L on top of the wall provided stability to the steel columns that were providing additional support for the cantilever slab but was not bolted to the top of the wall along its length to allow for expansion and contraction!
- This crack had been caused by the fixing through the angle bolted to the wall. It was not structurally significant but will allow moisture intrusion into the wall. Patching and paint were required.
- The offset crack in the brickwork was caused by differential movements between the brickwork and steelwork.
- The fixing points here were the problem. The self-supporting staircase can be attached to the metal angle on top of the wall but should be separated from the balcony wall and balcony slab because the steel's expansion and contraction far exceed that of the brickwork and concrete.
- Remove this section of the wall and rebuilt it free of the staircase steelwork.
Roofing
Roof Covering Materials: Sheeted roofs
The roof material on the hostel roof consisted of IBR profile sheeting which appeared to be fixed with pierced fixings. Pierced roof sheeting material can last between 40 to 70 years. However, much depend on the installation of the roofing. Items like roof screws, washers and rubber gaskets do not last as long! They typically last about 20 years, but roof sheet and screw movement can shorten this time! A pierced fixing roof system is installed by securing the sheets down by screwing through the metal. This method doesn’t allow the metal to expand and contract naturally causing the screws to enlarge the holes in the roof sheeting they are fixed through. In addition, heat and movement may cause the gaskets that come with the roof screws to deteriorate and fail. This leads to leaks and the need for regular maintenance. See Interior: Walls and Ceilings.
The ceiling in the gym was moisture damaged in various areas from roof leaks. This could mean the roof screw gaskets had failed or the roof sheeting had leaked at the side laps or both! It is far better and longer lasting to replace roofing screws and gaskets than to patch over the screws with an acrylic waterproofing system. Roof sheeting manufacturers recommend that all low slope IBR roofs below 15° should be sealed and stitched with roof screws and gaskets every 600 mm along the length of the side laps of the sheeting. Furthermore, they recommend that the wide pans of the roof sheeting should be turned up to prevent windblown rainwater from entering the building between the ridge and roof sheeting. Have a suitably qualified roof contractor check and repair the roof as necessary!
Fascia boards, Barge boards and Verge Tiles
Barge Boards/Verge Tiles: Asbestos/Fibre Board
Several barge boards were missing on the gable sides of the IBR roof on the east and west side of the house which exposes the roof structure to the elements. The barge boards must be installed to prevent moisture damage to the roof structure.
- The asbestos L-profile bargeboards were not the correct material to use on this roof's verges! With the long fixing points between roof purlins, strong winds will continually blow the bargeboards off the roof which is a safety hazard. Rather fit metal barge boards!
- Missing bargeboards on the east side of the building.
- Falling barge boards are a safety hazard!
- The open ends of the metal roof purlins can allow wind-blown rainwater to penetrate into the building!
Exterior Stairs
The stairs leading up to the 1st and 2nd floors were functional. The balustrading was functional and secure. Exceptions are specifically listed below.
The stairs appeared to have only been painted with red oxide primer. Areas of corrosion were noted on both the structure and the guardrails. All the metal should be sanded down, cleaned, primed and painted to protect the staircases and guardrails.
- Note the corrosion on the landing!
- The stair treads were corroded.
- Pooling of rainwater on the landings and stair treads should be avoided! Drill holes in the areas affected to allow the rainwater to drain away!
- Corrosion on the stair structure.
- Corrosion, if allowed to continue, will result in serious damage to the structure of the stairs.
Roof and Balcony Drainage
Gutter and Downpipe Materials: None
Verandah and Balcony Spout Materials: PVC spouts
Gutters and downpipes are not decorative installations. They are specifically installed on buildings to control rainwater discharging from the roof. Uncontrolled rainwater discharging onto the paving and ground may cause erosion of the paving. Furthermore, the falling rainwater causes splashing up onto the lower portions of the building's walls. This splashing up against the walls causes staining, serious damage to plastered finishes and erosion of the brick joints of facebrick finishes. Splashing up also causes rising damp and penetrating damp on the facebrick and plastered and painted walls. Serious consideration should be given to the installation of a complete roof drainage system to control and direct rainwater away from the building.
Some examples are shown below:
The roof rainwater spouts on the verandah and balcony were undersized and blocked by leaves and other debris. Many spouts were too high and none were waterproofed which allowed pooling on the balcony and verandah. Hail may also block the outlets. I recommend that the spouts be replaced with larger diameter spouts (50 mm) at the correct height in relation to the balcony floor finish that can be properly sealed against the brickwork to prevent moisture intrusion between the spouts and the parapet walls.
Some examples are shown below:
Exterior Walls
Exterior Plinth Finish: Fair faced (face, semi-face or clinker brick), Plastered and Painted
External Superstructure Finish: Plastered and Painted, Fair faced (face, semi-face or clinker brick)
This building had a very exposed design because of its height which will result in higher exterior maintenance costs and shorter life cycles from exterior systems. Buildings with this design in this climate should be considered higher maintenance and when implementing repairs they should be done in a professional and detailed way to prevent premature failure.
Where visible, the facebrick plinth and superstructure walls were in satisfactory condition except where additional items are specifically listed.
The plastered and painted wall finish of the building was generally in a reasonable condition. Additional exceptions are specifically listed.
The plastered walls on the exterior of the building will require repainting within the next 12 months to preserve the condition of the plasterwork on the building. Allow for it in the maintenance budget!
The exposed steel structure on the 2nd floor of the building was mostly in satisfactory condition. Additional items are specifically listed.
Moisture damage on the bathroom walls from the leaking of the plumbing wastepipes and fixtures!
- Flaking Paintwork and efflorescence on the column for a waterpipe leak.
- Efflorescence was a sign of moisture in the wall structure that had evaporated leaving behind a white powder which are salts absorbed by the water in the structure.
- Efflorescence was a sign of moisture in the wall structure that had evaporated leaving behind a white powder which are salts absorbed by the water in the structure.
- Moisture damage and flaking paintwork as a result of penetrating damp in the wall.
- Flaking paintwork as a result of penetrating damp in the wall.
- Flaking paintwork as a result of penetrating damp in the wall.
Eaves and Verges
Eaves Finish: Open rafters
Verge Finish: Open rafters
Exterior Doors and Thresholds
Door Types: FL&B timber doors
The exterior doors and frames were in fair condition except where additional items are specifically listed.
The door thresholds were not sufficiently sloped to the outside to throw the water away from the doors. The thresholds and frames should be sealed at the junction of the frames with the thresholds and brickwork and the junction of thresholds and brickwork to prevent corrosion from occurring. There may have been windblown rainwater entering through the door. The doors will require weatherboards or aluminium weather door seals fitted to the doors in the absence of a correctly placed water bar on the door threshold.
- The flat thresholds had probably allowed windblown rainwater to enter under the doors.
- Wind-driven rainwater was entering here! The doors should be sealed with silicone to prevent moisture damage to the doors.
- Signs of rainwater seeping through the bottom ledger on the inside of the door. This was common to most of the doors.
Many exterior doors required adjustment and repair for proper operation. At the time of inspection, the doors were hooking on the frame, had faulty mortice locks, were not latching properly or had missing striker plates and more.
Some examples are shown below:
- Mortice lock is stuck in the open position.
- The tongue of the mortice lock was stuck inside the mortice lock.
- No striker plate on the door frame for the door lock to latch into.
- The door and mortice lock face plate was chafing on the frame. Adjustment was required.
- The hinge pins should be seated properly.
- Doors binding on the door frame will eventually loosen the hinges and not close properly.
- Damaged door frame at the striker plate seating and a missing striker plate.
- Loose striker plate and screws prevent the door from closing!
Budget to repaint door frames and the exterior of the doors to ensure protection against the elements.
One sliding door at the gym was not fully functional. The sliding action was reasonably stiff. The door required adjustment and repair to function properly. The other sliding door was locked and could not be tested!
Both the external timber doors and the steel door frames at the 2nd-floor gym were moisture damaged. The doors should be replaced by a professional carpenter to function correctly.
- The bottom of the southeast side door was badly moisture damaged. The door frame was corroded in places! Note the flat threshold!
- The whole surface of the gym door was very dry to the touch and had no protection against moisture damage.
- The whole surface of the gym door on the northeast side was very dry to the touch and had no protection against moisture damage.
- The bottom portion of the exterior of the gym door was moisture damaged. The doors should have weatherboards fitted to the bottom of the doors to divert rainwater away from the doors and thresholds.
- The lock cover plate was damaged and should be replaced! The door hit against the door frame and could not be closed. Note the holes between the brickwork and door frame. All door frames should be properly sealed at the brickwork!
Window Exteriors and Sills
Window Types: Steel windows
Some of the steel windows in this building were very exposed to the weather and will require regular painting and sealing maintenance to preserve the windows and prevent corrosion. At the time of inspection, some windows were in need of maintenance. There were gaps at some window sills and the reveals which were open to moisture intrusion and will require sealing. This is especially important at window exteriors where there is less protection from a reduced roof overhang or balcony overhang. The maintenance will need to be done soon.
Some examples are shown:
- The west-facing windows on the 2nd floor had peeling paint on the window putty that should be maintained to prevent further deterioration of the putty and corrosion of the window frames.
- Note the corrosion of the window hinge!
- The 2nd-floor windows on the gym required serious maintenance on the putty and general paintwork of the windows.
- The exposed windows required sealing around the window frame and sills to prevent moisture intrusion!
Most of the bedroom and bathroom window putty was cracked and in some instances, the protective paint was flaking. Painting the putty will seal the cracks for some time but replacement is preferable! The windows frames appeared to require sanding down and repainting anyway! Most of the bedroom and bathroom windows were not properly sealed at the sills and the reveals of the windows. Monitor during or after rainstorms to determine whether windblown rainwater reaches these areas. If it does, the windows will need to be sealed to prevent moisture intrusion into the walls!
Some examples are shown below:
- These gaps at the window reveal and sill may allow moisture intrusion into the brick reveal and sill.
- Cracked putty and peeling window paint on the bedroom window.
- Cracked putty on a 1st-floor window.
Interior Floors and Floor Materials
Where visible, the tile flooring in the bedrooms and bathrooms appeared to be in clean, decorative and fair order except where addition items are specifically listed.
There were cracks in tiling at some door openings. Cracks of this nature are normally due to bad building practices. Movement joints should always be formed through the slab and floor finish at doorways. Floors always crack at the weakest (narrow) part of concrete slabs.. In most cases, the cracking in the surface of the surface bed appeared to be more unaesthetic than structurally significant.
Interior Walls and Ceilings
Generally, the ceiling and wall finishes were in fair condition. Exceptions are listed.
There was efflorescence and flaking paintwork that was signs of rising damp and penetrating damp on the lower portion of the walls internally in bedroom 1 which appeared to be a result of moisture intrusion from a source such as a leak in the shower, water pipe leak or a waste pipe leak. in the bathroom next door. I recommend an inspection and repair by a suitably qualified plumber. The wall can be repaired and painted once the source of the moisture is found and repaired.
Balconies and Verandahs
Generally, the floor tiling, guard walls and guardrails were in a reasonable condition. Additional items are specifically listed
A few areas on the ground and 1st floor had cracked and missing potions of tiles on the floor and skirtings. The cracked and broken tiles appeared to be the result of the lack of expansion joints, hollow tiles or the result of physical damage. The damage was not structurally significant.
Electrical
Inspection Method: Random Testing
Electric Plug Points: Three wire receptacles
The padlocks on both ground floor electrical boards were broken allowing unauthorised entry to the circuit breakers. There were uncovered openings in 3 electrical panels' internal covers that expose those who have access to the panel to shock hazards. These openings will need to be covered with approved panel block-out covers. Have a suitably qualified electrician check and repair the installations. This is a safety issue.
The exterior of the electrical panel on the 1st-floor was corroded and required further evaluation by a licensed electrician to insure safe and reliable performance. Corrosion outside the panel is a red flag that the panel could be having moisture problems and this could result in poor and unsafe wiring connections. Repair as recommended by a licensed electrician.
An earth leakage circuit breaker (ELCB) socket tester was used to test plug points. All tested plug points were in safe working order.
All tested interior and exterior light fixtures and switches were in working order except where additional items are reported.
The earth leakage circuit breakers at the electrical panels responded to their test buttons. An earth leakage circuit breaker (ELCB) socket tester was used to trip the earth leakage circuit breakers. The breakers tripped at 30 mA as required.
Plumbing
Generally, the plumbing in the hostel block appeared to have been poorly maintained over the years by unqualified workers. It will be good idea to have the plumbing evaluated by an appropriately qualified licensed plumber for further remarks and recommendations.
The waste piping on the exterior of the bathrooms on the ground and 1st floor required general maintenance and repairs.
- I could not determine what was used to connect or seal this waste pipe. PVC adhesive should have been used!
- Another place where I could not determine what was used to connect or seal this waste pipe. PVC adhesive should have been used!
- Another elbow sealed with the incorrect adhesive or sealer. Note the broken strapping on the PVC strap on boss!
- These waste pipes required addition support! Have the appropriate brackets installed.
- A hole in this elbow on this wastepipe! The elbow should be replaced!
- Another repair on wastepipe that had leaked or is leaking!
- This waste pipe had been blocked off from a plumbing fixture rendering it unusable!
- This Polycop waterpipe is only suitable for underground use. It does not have a SABS mark. Rather replace it with a copper pipe!
This shows the main water shut off valves to the bathrooms on the north side of the hostel block.
- The water supply shut-off valve on the ground floor.
- The water supply shut off valve on the 1st-floor.
Ground Floor Male Bathroom
The basins, taps and drains were functional. The basins were filled and allowed to drain. No leaking was noticeable at the time of the inspection except where additional items are specifically listed.
The shower doors were in good working order.
Only one of the 2 extractor fans were operational! Repair or replacement was required!
Taking into consideration the defective, maintenance or deferred items listed above, this bathroom was only in a partly serviceable condition. The bathroom should not be used until the defects listed above are repaired.
1st Floor Male Bathroom
The basins, taps and drains were functional. The basins were filled and allowed to drain. No leaking was noticeable at the time of the inspection except where additional items are specifically listed.
The extractor fans were not operational. The fans will need to be repaired to provide adequate ventilation. The windows should be opened to allow through ventilation.
The shower doors were in good working order.
One toilet door was locked and the cubicle could not be accessed. It may be the the toilet was not functional!
Taking into consideration the defective, maintenance or deferred items listed above, this bathroom was only in a partly serviceable condition. The bathroom should not be used until the defects listed above are repaired.
Ground Floor Female Bathroom
The bath drain and mixer tap appeared to be functional. The bath was filled and allowed to drain. No leaking from the bath was noticeable at the time of the inspection. Additional items are specifically listed.
The extractor fans were not operational. The fans will need to be repaired to provide adequate ventilation. The windows should be opened to allow through ventilation.
Taking into consideration the defective, maintenance or deferred items listed above, this bathroom was only in a partly serviceable condition. The bathroom should not be used until the defects listed above are repaired.
1st Floor Female Bathroom
The basins, taps and drains were functional. The basins were filled and allowed to drain. No leaking was noticeable at the time of the inspection except where additional items are specifically listed.
The bath, mixer tap, shower wand and drain appeared to be functional. The bath was filled and allowed to drain. No leaking from the bath was noticeable at the time of the inspection. Additional items are specifically listed.
The acrylic or fiberglass bath had scratches and stains on the bath finish. Hire a specialist to restore the cosmetic finish. Although this can be done with a repair kit from the hardware store without hiring a specialist, it can be difficult to match the existing colour.
Taking into consideration the defective, maintenance or deferred items listed above, this bathroom was only in a partly serviceable condition. The bathroom should not be used until the defects listed above are repaired.
Fire Suppression
Any fire-fighting equipment, installations and fire protection systems in the building should be so installed and maintained as to be ready for their purpose at all times. SANS 1475 requires that the service and maintenance of fire extinguishers, fire hose reels and above-ground hydrants must be carried out annually with the additional requirement that powder, foam, water and water-based extinguishers should be pressure tested every 5 years and CO2 extinguishers every 10 years. The South African Qualification Certificating Committee (SAQCC) has been appointed to ensure that servicing and maintenance of fire protection equipment are conducted according to the specifications laid out in SANS 1475 and that technicians have the correct training, qualifications and experience.
Make sure that the persons or company employed to inspect and service the fire suppression equipment have the necessary permits and qualifications! Insist on such a person or company being registered with the SAQCC (South African Qualification & Certification Committee) which will ensure that you are working with a competent and qualified person or company.
House with Workshop
Foundation
The building's foundations appeared to be concrete strip foundation footings. Strip footings are a type of shallow foundation that is used to provide a continuous, level or stepped strip of firm concrete support for walls built centrally above them. Concrete strip footings can be reinforced or not depending on the soil founding conditions. The footing size or depth below the ground level could not be verified.
Floor, Wall and Roof Structure
Minor floor settlement and cracking was noted in the workshop floor during my inspection indicating a need for preventative maintenance. The cracks appeared to be the result of thermal movement and slight subsidence as a result of the lack of expansion joints in the floor slab. The cracked areas should be cleaned out and filled with cold asphalt or concrete to prevent moisture intrusion under the concrete slab that may cause further settlement.
The visible portions of the concrete ground floor structure of the house appeared to be in satisfactory condition at the time of the inspection.
The visible portions of the workshop's roof structure structure appeared to be in good condition at the time of the inspection.
The house's internal and external wall structure was generally in a reasonable condition. No serious structural issues were noticeable.
Viewed from the trap door, the roof structure appeared to be in a average condition considering the roof structure's age. Other roof and ceiling issues may be mentioned below or elsewhere.
Viewed from the trap door, none of the roof purlins and trusses internally in the roof space appeared to be seriously moisture damaged at this stage! However, another season of rainwater intrusion may change this situation drastically. The roof sheeting should be sealed urgently to prevent further damage to the roof structure.
Roofing
Roof Covering Materials: Sheeted roofs (Metal with exposed fasteners)
The roof material on the 1st bedroom, house and workshop's roof consisted of corrugated iron and IBR profile sheeting which appeared to be fixed with pierced fixings. Pierced roof sheeting material can last between 40 to 70 years. However, much depend on the installation of the roofing. Items like roof screws, washers and rubber gaskets do not last as long! They typically last about 20 years, but roof sheet and screw movement can shorten this time! A pierced fixing roof system is installed by securing the sheets down by screwing through the metal. This method doesn’t allow the metal to expand and contract naturally causing the screws to enlarge the holes in the roof sheeting they are fixed through. In addition, heat and movement may cause the gaskets that come with the roof screws to deteriorate and fail. This leads to leaks and the need for regular maintenance.
Corrosion was noted on the corrugated roofing material. For extended service life from this roofing material I recommend removing the corrosion and sealing with a rust inhibitive paint. Acrylic and fabric waterproofing applied over screw heads do not provide long term leak protection and will need to be monitored and maintained frequently to help prevent moisture intrusion. Screw and gasket replacement is usually a better option! Consult with a qualified roofing contractor about the best options to sealing and repair the roof sheeting to prolong the useful life of this material and prevent the spread of corrosion.
The original front veranda of the house had been covered with a corrugated roof and appeared to be used as a storage area. The roof had leaked onto the roof beams supporting the roof. The roof will need to be sealed to prevent further moisture intrusion.
Fascia boards, Barge boards and Verge Tiles
The asbestos/fibre barge boards generally appeared to be in satisfactory condition except where addition items or problems are specifically listed.
Roof Drainage
Gutter and Downpipe Materials: Galvanised steel gutters and downpipes
Generally, the galvinised steel gutters and downpipes that were installed appeared to be in average condition. No leaks were noticeable at any joints in the guttering..
The roof gutter system for this building was incomplete and required installation and repairs to ensure proper control of roof runoff. Gutters are installed on buildings to control rainwater discharging from the roof. Uncontrolled rainwater discharging onto the ground or paving erodes paving and removes the jointing between the paving. Furthermore, the falling rainwater causes splashing up onto the lower portions of the house's walls. This splashing up against the walls can cause serious damage to plastered and painted finishes and will cause rising damp. Serious consideration should be given to the installation of a complete roof drainage system to control and direct rainwater away from the house.
Exterior Walls
Exterior Plinth Finish: Plastered and Painted
On buildings that have do not have the DPC running al the way to the outside of the joint between the plinth and superstructure walls, a mortar "bridge" may result in rising damp above the damp proof course level (DPC) if the brickwork on the plinth is not properly separated from the plasterwork on the superstructure at floor level. The only way to separate the two is to form a deep joint horizontally through onto the DPC at the DPC level to prevent rising damp bridging the DPC into the superstructure above. Consider having these joints properly installed to prevent rising damp into the structure above the floor levels to save on future expensive maintenance (the joint can be cut with doubled up cutting discs on an electric saw or angle grinder)!
Examples are shown below:
- Rising damp manifesting as crazing cracking on the wall above the driveway paving.
- The open joints in the driveway and the wall allows rain and stormwater to collect in the joint causing rising damp. Seal the joint with mortar.
- Fine cracking and bubbling paintwork along the cracking of the plasterwork was an indication of the moisture trapped in the wall.
Paint loss, patchiness and deterioration was observed to the plastered and painted walls on all sides of the house. I recommend that the walls be repainted for protection against the elements. The areas to be repainted should be sealed either with a plaster primer or sealer before the top coats are applied.
Eaves and Verges
Water stained and rotted roof structure was evident under the eaves at the northeast side the house which is an indication that the gutters have overflowed in the past. The timber roof and structure should be repaired as soon as possible to prevent the roof from deteriorating further.
Exterior Doors and Thresholds
The threshold was missing on the side door. This is a common area where rising damp occurs as water collects on the unfinished threshold and soaks into the structure below and on the sides of the door. Repair the threshold sloping it to the outside to ensure that rainwater flows away from the door.
The sliding door at the verandah was in good working order at the time of the inspection.
Window Exteriors and Sills
Window Types: Steel windows
The window putty on all the windows of the building was cracked or missing. Badly cracked putty should be removed, the putty redone and painted to prevent leakage and corrosion of the frames. Where the window putty has been replaced, the putty should be painted within 2 weeks to prevent the premature drying out and cracking of the putty.
Examples are shown below:
There were gaps on the window sills and the reveals (sides) which were open to moisture intrusion and will require sealing. The window exteriors should be sealed with silicon at the junction of all window frames and the brickwork at the heads, reveals and sills. Gaps at the junction between the brickwork and the frames can allow moisture intrusion into the wall structure.
Some examples are listed:
Interior Floors and Floor Materials
This house has a hodge podge of different floor finishes ranging from painted screeding to rubber tiles that are in generally less than average condition. Depending on what the house will be used for the floors may require updating for comfort and performance.
Interior Walls and Ceilings
There was evidence of some moisture damage to most of the ceilings and walls in the house. There were cracks at the cornices and moisture staining on some ceilings that would need repair. The ceiling damage was caused by leaks in the roof. Repairs to the ceilings can be done once the roof is repaired!
The following issues were observed:
- There was bubbling paint on a wall.
- Cracks between the cornices and walls.
- Staining between the cornices and walls.
- Staining on walls
- Deviations in the ceiling level.
- Ghosting.
- A partly collapsed ceiling.
- A hole in the ceiling.
The above are all indications of moisture damage! Some examples are shown below:
Balconies and Verandahs
The verandah had been enclosed with a corrugated roof structure and the sides with plastic membrane, shutter board and some wrought ironwork and was being used for storage.
There were some obvious observable signs of moisture staining and evidence of roof leakage on the beams of the roof. See Floor, Wall and Roof Structure.
Electrical
Inspection Method: Random Testing
Electric Plug Points: Three wire receptacles
The main panel and its components in the kitchen had no visible defects or except where additional items are listed.
The main electrical panel and service disconnect was obstructed which prevents easy access to the panel front incase of an emergency! I recommend that the stored goods be moved from the face of the panel for safe and proper access. The work space required in front of the main panel is 900 mm from the front, 2.2 m vertically from the floor and 760 mm width.
There were two hobs, two eyelevel ovens and one under counter oven. Only the hob above the under counter oven was operational and responded to the the controls.
- Only this hob was operational!
- This hob was inoperative!
- These oven were inoperative
Beauty Salon
Foundation
The building's foundations appeared to be concrete strip foundation footings. Strip footings are a type of shallow foundation that is used to provide a continuous, level or stepped strip of firm concrete support for walls built centrally above them. Concrete strip footings can be reinforced or not depending on the soil founding conditions. The footing size or depth below the ground level could not be verified.
Floor, Wall and Roof Structure
The house's internal and external wall structure was generally in a good condition.
The visible portions of the concrete ground floor structure appeared to be in satisfactory condition at the time of the inspection.
The eaves and verges on the house were in a reasonable condition except where defects are specifically listed.
The roof structure appeared to be in satisfactory condition considering the roof structure age. Other roof and ceiling issues may be mentioned elsewhere.
Roofing
Roof Covering Materials: Roof tiles (Concrete tiles)
Unlike other roofing materials, concrete roof tiles actually become stronger over time. Because of roof tile's superior quality and minimal maintenance requirements, most roof tiles will last at least 50 years to the lifetime of the structure (100 years +). Like most roof finishes, the top surface may deteriorate in time and become porous. When this happens, the roof tiles may need to be sealed using modern roof coating systems to extend the roof tile's life expectancy and restore their aesthetic appeal.
The exposed surfaces of portions of the roof tiling showed signs of weathering and appeared to be porous. While a porous roof tile will not necessarily leak, a porous tile is weaker than a tile that's in good condition. The increase in holes and little cracks will compromise the overall integrity of the tile, making it more susceptible to breaking or further damage. As the porosity of the tiles increases, things such as storms, strong winds or walking on them could cause the tiles to completely break apart. Sealing and repainting the concrete roof tiles will extent their lifespan by reducing further weathering and will reduce maintenance and possible replacement costs in the long run.
There were some tiles that were not properly interlocked on areas of the roof. These can allow the ingress of rainwater onto the roof structure and into the house under windy conditions. The tiles should be adjusted and fixed to the roof structure to interlock properly.
Fascia boards, Barge boards and Verge Tiles
All bargeboards were incorrectly installed and had allowed wind-blown rainwater onto the timber roof structure that they were fixed to. The bargeboards are not merely decorative and should be installed flat onto or against the underside of the ridge of the roof tiles to prevent the ingress of water and deterioration of the roof structure under the last row of tiles at the roof verge. Employ a suitably qualified roofing contractor to refit or replace the barge boards. There may be additional concealed water damage to the roof structure!
The following issues were observed:
- The bargeboards should have been installed flat onto the roof tiles to prevent the ingress of windblown rainwater and the deterioration of the roof timbers on the verge of the roof (see the example).
- The counter battens and tilting battens had been exposed to the ingress of rainwater.
- Some of the bargeboards were pulling away from the counter battens they were fixed to.
- Most of the nails securing the bargeboards were corroded.
- Moisture damaged roof structure.
- Missing bargeboards.
- Peeling flaking paintwork on the bargeboards.
Some examples are shown below:
Roof Drainage
Gutter and Downpipe Materials: Galvanised steel gutters and downpipes
The gutters and downpipes were old and incomplete and appear to be close to the end of their useful service life. I noted some gutters were corroded. While repair is possible in the short term, replacement with new gutters and downpipes is recommended for scheduled maintenance.
Some of the shortcomings noted:
- Some gutters on the house were corroded and appeared to be leaking in places.
- When a coating or painted finish fails on a galvanised metal gutter, rust soon sets in.
- A gutter stop end was missing. Replace to prevent splashing up on the wall of the house.
- Downpipes were missing.
- There were no gutters on some eaves.
Some issues are shown below:
Exterior Walls
The plastering on the walls was generally in a reasonable condition. Additional issues are specifically listed.
The exterior walls need to be re-painted to preserve and maintain the wall finish. Budget for re-painting the exterior in the near term. This is a routine maintenance item. Examples of specific observations noted during the inspection include:
- fine cracking of the plaster finish
- Fading of the paint finish on the sun-exposed sides of the building.
Exterior Doors and Thresholds
Window Exteriors and Sills
Window Types: Steel windows
Some of the steel windows in this house were very exposed to the weather and will require regular painting and sealing maintenance to preserve the windows and prevent corrosion. At the time of inspection, some windows were in need of maintenance. There were gaps at some window sills and the reveals which were open to moisture intrusion and will require sealing. This is especially important on window exteriors where there is less protection from a roof overhang. The maintenance will need to be done soon.
The window putty at the of the windows of the house was cracked. Badly cracked putty should be removed, redone and repainted to prevent leakage and corrosion of the frames. Where the window putty has been replaced, the putty should be painted within 14 days to prevent the premature drying out and cracking of the putty.
Interior Floors and Floor Materials
Comment: Where visible, the tile flooring in the house appeared to be in a reasonable, clean and decorative order except where additional items are specifically listed.
Interior Walls and Ceilings
Generally, the ceiling and wall finishes were in fair condition. Exceptions are listed.
There were signs of rising damp, bubbling paintwork and flaking paintwork on the lower portion of the walls which appeared to be a result of moisture intrusion from an external source such as pooling water on the paving or from splashing up from the gutters where the downpipes were missing. The walls should be monitored externally after the next rainstorm to check if water is pooling against the wall structure. If water is pooling against the structure the water should be directed away from the walls.
- Splashing up from the gutter.
- Seal up the holes to prevent moisture intrusion!
Electrical
Inspection Method: Random Testing
Electric Plug Points: Three wire receptacles
The main panel and its components in the house had no visible defects or except where additional items are listed.
All tested interior light fixtures and switches were in working order.
An earth leakage circuit breaker (ELCB) socket tester was used to test plug points. All tested plug points were in safe working order.
Plumbing
The sink, mixer and drain point appeared to be functional. The sink was filled and allowed to drain. No leaking was noticeable at the time of the inspection.
A basin was installed in the bathroom. The basin, taps and drain were functional. The basin was filled and allowed to drain. No leaks were observed during the inspection.
The toilet was functional and responded properly when flushed. No leaks were observed at the toilet at the waste pipe, cistern flush pipe or water supply at the time of the inspection.
Hot water was available at the hot water taps from the geyser. The hot water supply to the bathroom was tested.
Grounds
Driveways, Walkways and Flatwork
The driveway on the west side of the properties were mostly in a reasonable condition.
Gradients, Drainage and Elevations
Clearance to Landscaping: Standard
Site Description: Slight slope
Less than a 10% incline is considered a slight slope, while a slope between 11-20% is considered moderate. Anything above 20% is deemed to be a steep slope. Attention to drainage for both surface and subsurface water is crucial to a building on any slope but more so on flat and slight-sloped sites! This site was considered a slight-sloped site.
There was generally an adequate difference in elevation between the exterior ground level and the interior floors.
It appeared that stormwater was pooling close to or against the buildings as a result of the level and slope of the landscaping on the east side. As a preventive measure drainage and/or grading conditions in these areas should be improved upon to prevent this condition from occurring.
Boundary Walls, Yard Walls, Gates and Fences
The precast boundary walls on the north, east and south were plastered to provide a decorative finish. In some areas, the decorative finish had cracked or fallen off the wall portions of the wall. Where this has occurred any areas of potential collapse must be removed to prevent possible further collapse! This is a safety concern!
The security gates were not functional. The motors were not functional or missing. There did not appear to be any system of locking the gates and was a security risk. The gate motors should be repaired as soon as possible or alternative arrangements be made to secure the gates in a closed position.
Pools and Spas
Pool or Spa Type
Pool Body: Below Ground
The pool body finish was marbelite plaster. The water was murky with some dirt deposited on horizontal surfaces. There were some cracks in the pool body.
There was some cracking above the waterline level below the pool coping. Care should be taken not to fill up to or above the cracking until the cracks are sealed. I recommend that the pool body be evaluated by an appropriately qualified swimming pool specialist for further recommendations and repairs.
The marbelite pool finish was stained and flaking in places. The marbelite finish on a swimming pool usually lasts between 15 to 20 years. The pool will need to be completely drained so that the flaking marbelite can be removed and redone or fibreglassed. Consult with a pool specialist.
Filters
Filter Type: Sand Filter
The filter multi-port valve at the pool filter was damaged and needed to be replaced.
Pumps, Blowers and Valves
Pumps: Circulation pump
A new pump, some pipework and a filter multi-port valve had been installed.
The pool pump was not tested. The water level was too low.
Pool/Spa Electrical
Fencing, Decking, Paving and Coping
The pool enclosure to the property (security gates and boundary walls), conformed to common safety standards. Pool enclosures and/or fencing are typically required to be a minimum 1.2 metres high when measured on the side facing away from the pool.
Pests and Wood Destroying Organisms
Wood Destroying Organisms
There was evidence of termite infestation on the southwest side of the property. I recommend an additional inspection by a pest control operator to further evaluate the property and treat the infestation as recommended. A guarantee from a pest control officer or company that is a member of the South African Pest Control Association (SAPCA) should be issued. The certificate of guarantee should state that termite proofing was done in accordance with National Building Regulations and guaranteed for 5 years from the date of issue.