About A Home Inspection
All components designated for inspection in the ASHI Standards of Practice are inspected, except as may be noted in the sections within this report.
ItThe goal of the inspection is put a home buyer in a better position to make a buying decision. Not all improvements will be identified during this inspection. Unexpected repairs should still be anticipated. The inspection should not be considered a guarantee or warranty of any kind.
Please refer to the pre-inspection contract for a full explanation of the scope of the inspection.
How to Read This Report
Getting the Information to You
This report is designed to deliver important and technical information in a way that is easy for anyone to access and understand. If you are in a hurry, you can take a quick look at our "Summary Page” and quickly get the critical information for important decision-making. However, we strongly recommend that you take the time to read the full "Report", which includes digital photographs, captions, diagrams, descriptions, videos, and hot links to additional information.
The best way to get the layers of information that are presented in this report is to read your report online, which will allow you to expand your learning about your house. You will notice some words or series of words highlighted in blue and underlined – clicking on these will provide you with a link to additional information.
This report can also be printed on paper or as a PDF document.
Chapters and Sections
This report is divided into chapters that parcel the home into logical inspection components. Each chapter is broken into sections that relate to a specific system or component of the home. You can navigate between chapters with the click of a button on the left-side margin.
Most sections will contain some descriptive information in black font. Observation narrative, done in colored boxes, will be included if a system or component is found to be significantly deficient in some way or if we wish to provide helpful additional information about the system or the scope of our inspection. If a system or component of the home was deemed to be in satisfactory or serviceable condition, there may be no narrative observation comments in that section and it may simply say “tested,” or “inspected.”
Observation Labels
All narrative observations are colored, numbered, and labeled to help you find, refer to, and understand the severity of the observation. Observation colors and labels used in this report are:
Summary Page
The Summary Page is designed as a bulleted overview of all the observations noted during the inspection. This helpful overview is not a substitute for reading the entire inspection report. The entire report must be read to get a complete understanding of this inspection report as the Summary Page does not include photographs or photo captions.
Summary
Major Concerns
- HFV-6 Heating, Fireplaces, and Ventilation:
The B-vent flue for the furnace is corroded above the roofline and the hat is missing, this requires replacement. Have this flue piping further evaluated and repaired as recommended by a qualified heating contractor as water staining and minor corrosion were noted in the utility room on the flue piping as well. Please note that the correct cap design can help prevent corrosion of the top of the vent pipe.
Repair Items
- GD-3 Grounds and Drainage:
All trees, branches, and vegetation should be pruned at least one foot away from the sides of the building and six feet away from the roof to eliminate a condition conducive to wood-destroying organisms and a path for rodent entry.
- ED-7 Exteriors and Decks:
Some of the exterior siding flashings are inconsistently executed. Proper flashing techniques are important to ensure the siding system sheds water reliably. I recommend additional inspection and repair by a qualified contractor to ensure the siding system reliably sheds water.
- Lap siding trim window openings missing head flashing on the north side
- K-1 Kitchen:
The trap seal for the kitchen sink waste piping is too deep - this seal should not exceed 4 inches - the trap pipe was installed backward. This could lead to sediment build-up in the pipes. Hire a licensed plumber to further evaluate and repair.
- K-2 Kitchen:
The dishwasher drain line is missing a proper air gap to prevent siphoning waste water back into the dishwasher. This should be done so that the drain is not always submerged in the wastewater. The dishwasher drain connection point should be moved higher onto the sink downpipe. This should be repaired by a qualified plumber
- HB-3 Hallway Bathroom:
The fill valve inside the hallway bathroom toilet tank is leaking and requires repair or replacement. It was also very slow to refill. This should be repaired by a qualified plumber.
- MB-1 Master Bathroom:
The hot faucet handle to the left master bathroom sink would not turn and requires repair to ensure reliable performance.
- MB-2 Master Bathroom:
The right master bathroom sink faucet handles are leaking and require repair or replacement. Hire a licensed plumber to further evaluate and repair.
- MB-3 Master Bathroom:
The waste plumbing below the right master bathroom sink is leaking and requires immediate repair. Hire a licensed plumber to further evaluate and repair.
- MB-6 Master Bathroom:
The fan in the master bath toilet room did not appear operational. I tried all switches on the walls and the fan did not come one: is there a hidden switch? Have this fan repaired as needed to ensure adequate ventilation for this bathroom.
- BB-1 Basement Bathroom:
The basement bathroom toilet appears to keep running after flushing. This can often be stopped by jiggling the handle. This is not satisfactory. Hire a plumber to further evaluate and repair this toilet to prevent water waste.
- AP-2 Additional Plumbing:
The irrigation well cap was loose and not properly secured to the well casing. This should be repaired to prevent things from accidentally being put down the well. Have repaired by a qualified plumber.
- HFV-4 Heating, Fireplaces, and Ventilation:
The whole house humidifier was inoperative and lacked maintenance. Cleaning and repairs should be undertaken when the filter is replaced. This should be done annually, watch out for humidifier leaks into the furnace where costly (and hidden) damage can occur.
- EP-1 Electric Panels:
Hire a licensed electrician to correct the double-tapped circuit in the electric panel - this is when two conductors share the same breaker. This condition risks poorly protected circuits and as such is a latent fire hazard if conductors are not properly torqued. This requires additional evaluation by an electrician.
- EDFW-1 Electric Distribution and Finish Wiring:
Abandoned wiring was noted in the attic. This should be eliminated or properly terminated inside a listed junction box. It is often not feasible to determine if the wire is still connected to a power source. I can test these with a voltage sensor, but they could be shut off by a switch or temporarily disconnected. For safety, all abandoned wires should be eliminated.
Significant Repair/Safety Items
- GD-6 Grounds and Drainage:
The riser heights for the exterior back stairs are not even and are not to modern standards. This is a trip and safety hazard. The height of the tallest riser shall not exceed the smallest riser by more than 3/8th of an inch. Hire a licensed general contractor to further evaluate and repair.
- GD-7 Grounds and Drainage:
The exterior stairway to the front door appears to be too narrow. Stairways shall not be less than 36 inches in clear width at all points above the permitted handrail height and below the required headroom height. Handrails shall not project more than 4.5 inches on either side of the stairway and the minimum clear width of the stairway at and below the handrail height, including treads and landings, shall not be less than 31.5 inches where a handrail is installed on one side and 27 where handrails are provided on both sides. Have this further evaluated and repaired as recommended by a qualified general contractor.
- G-3 Garage:
The overhead garage doors in the garage do not reverse under resistance to closing. Adjustment of the sensitivity is recommended for improved safety. An adjustment setting can often be found as a plastic screw on the opener - I recommend consulting with the owners' manual or looking up the manual online as needed.
- FSD-1 Fuel Storage and Distribution:
The 2009 edition of NFPA 54, National Fuel Gas Code, includes new requirements for bonding CSST gas piping systems to the grounding conductor of the building's electrical system, to reduce the possibility of damage by lightning strikes by reducing the electrical potential between metallic objects and building systems, including gas distribution. I was unable to locate a bonding connection for the CSST during inspection today. Have this further evaluated and repaired as recommended by a qualified CSST installer.
- EDFW-3 Electric Distribution and Finish Wiring:
The installation of carbon monoxide alarms is recommended for all homes that have fuel-burning appliances such as gas or oil furnaces, gas water heaters, gas ovens, cook-tops, gas fireplaces, and wood stoves. Carbon monoxide is a colorless, odorless gas that can cause sickness, nausea, and even death. For more information, consult the Consumer Product Safety Commission at 1-800-638-2772 (C.P.S.C.) Modern standards in many states now recommend one CO alarm outside of all bedrooms and at least 1 per floor of the house.
Maintenance Items
- RC-1 Roof and Chimney:
The exposed nail heads found on the roof should be sealed to prevent corrosion of the nail and possible leaking in the future.
- RC-5 Roof and Chimney:
Leaks were noted in the gutter and downspout system that need to be repaired to control roof runoff. Seal-up all leaking areas and tune-up to ensure gutters are properly secured and sloped to drain.
- GD-5 Grounds and Drainage:
Typical cracks were noted in cement flat work. No immediate repair appears necessary, though water will continue to deteriorate the surface until the cracks are sealed.
- ED-2 Exteriors and Decks:
Areas for re-caulking were noted on the exterior - see around window frames, door frames, and utility penetrations. Preventative caulking maintenance can help keep these spots weatherproof.
- ED-3 Exteriors and Decks:
The exterior wood siding and trim need to be re-painted to preserve and maintain the siding system. Budget for re-painting the exterior in the near term. This is routine maintenance but is a concern due to upcoming costs.
- ED-10 Exteriors and Decks:
The window well is full of vegetation and organic debris and needs to be cleaned to eliminate a condition conducive to wood destroying organisms. Remove all soils and vegetation and repair any hidden rot to wood as needed.
- BWB-1 Basement Wet Bar:
The basement wet bar refrigerator ice maker was noted to be full of coagulated ice. Remove old ice, clean ice try and change any water filters as needed.
- LF-2 Laundry Facilities:
The dryer exhaust ductwork is dirty and needs to be cleaned for improved safety. This is important for regular maintenance to eliminate a potential fire hazard. This should be cleaned annually to prevent lint build-up.
- HB-1 Hallway Bathroom:
The faucet handle in the hallway bathroom on the sink spins - see how the handle just spins around. Have this repaired by a licensed plumber.
- HB-5 Hallway Bathroom:
The hallway bathroom caulking is needed on the sink countertop and backsplash, around the base of the toilet, at the tub and floor joint and around the tub spout in the bathroom to prevent water from damaging the floor.
- MB-4 Master Bathroom:
The master bathroom toilet was fussy to operate, the handle hits the lid. The handle had to be held down for some time to get the unit to flush properly. Repair, adjust, or replace the toilet as needed for reliable performance.
- MB-5 Master Bathroom:
The shower head in the master bathroom shower needs to be cleaned or replaced. Calcium build-up and scaling are causing the shower head to spray at right angles and water is spraying out of the shower. If the house is on a well system, this can also indicate that sediment is entering the water supply. If this is a persistent problem, it can often be corrected by adding a filter at the well.
- MB-7 Master Bathroom:
The master bathroom caulking is needed on the sink countertop and backsplash, around the base of the toilet, at the tub and floor joint, around the tub spout and on the tub ledge in the bathroom to prevent water from damaging the floor.
- BB-2 Basement Bathroom:
The shower head in the basement bath is leaky and requires repair to prevent wasting water and control water flow.
- BB-3 Basement Bathroom:
The basement bathroom caulking is needed around the base of the toilet and at the tub and floor joint in the bathroom to prevent water from damaging the floor.
- I-1 Interior:
Minor amounts of rodent feces were visible on the wet bar countertop and below the sink in the wet bar cabinet. Traps should be set for mice and avenues of entry located and blocked.
- AP-3 Additional Plumbing:
The sprinklers need general adjustments to prevent spraying the house. This will possibly cause siding damage over time if not corrected. Zones that need to be adjusted are as follows:
- Zone 2 on the south side
- AP-4 Additional Plumbing:
The sprinklers need repair to operate properly. This should be repaired by a qualified irrigation contractor. Zones that need to be adjusted are as follows:
- Zone 2 - One head on the east side is damaged
- Zone 5 - One head on the north side is under the gutter splash block
- HFV-2 Heating, Fireplaces, and Ventilation:
Annual servicing of the gas forced air furnace is recommended for safe and reliable heat. I could not find recent service records on the furnace. The furnace was tested during inspection and was operational. The design life of these forced air furnaces is 20-25 years. I recommend having it serviced and keeping it on an annual service schedule until updated.
- HFV-3 Heating, Fireplaces, and Ventilation:
The dirty air filter for the forced air furnace should be replaced. Plan on replacing air filters every 2-3 months during the heating season.
- HFV-5 Heating, Fireplaces, and Ventilation:
The whole house humidifier filter should be replaced and has lacked maintenance. Cleaning and repairs should be undertaken when the filter is replaced. This should be done annually, watch out for humidifier leaks into the furnace where costly (and hidden) damage can occur.
- F-1 Fireplaces:
The glass for the gas log fireplaces is cloudy. Though very common, this is not the intended appearance of a decorative gas log fireplace. Sometimes, silicates from the logs can get etched onto the glass which can make cleaning difficult. Hire a gas log specialist to service the gas log fireplaces and clean or replace the glass as needed.
The following is a recommended procedure for cleaning the glass on gas fireplaces.
1) Make sure your glass is cool to the touch. It is also recommended that your pilot is turned off before you begin to clean the glass.
2) Remove the front face or louvers of your fireplace.
3) Follow the instructions in your manual to carefully remove the glass assembly. Lay it on a soft surface.
4) Using a soft cloth, clean both sides of the glass with a household glass cleaner. Do not use a product with ammonia or any abrasive cloth or cleaner to clean your glass. The glass can shatter if it is scratched. For heavy deposits, use a hard water deposit glass cleaner, such as Stove Bright Glass Cleaner.
5) Follow the instructions in your manual to carefully replace the glass on the front of the fireplace. Make sure you re-latch the glass so it is securely fastened on your fireplace.
- EDFW-4 Electric Distribution and Finish Wiring:
These appear to be the original smoke alarms. These are getting old. Fire marshals recommended updating smoke alarms every 10 years to ensure reliable performance. Updating is recommended.
Improvement Items
- RC-4 Roof and Chimney:
Gutter extensions are recommended to help discharge water at least 5-6 feet away from the foundation. This can cause foundation settlement or basement moisture problems.
- GD-2 Grounds and Drainage:
The grade of the east yard is slopping toward the building and/or there are low spots along the house. Standards recommend a quarter inch/foot slope away from the building or better. The flower beds were sloping towards the house and should be improved. This will help keep the basement/crawl space from leaking.
- ED-4 Exteriors and Decks:
Inadequate clearances were noted between the roof and the siding. A 2 inch air gap is recommended here to keep the siding off the roof and prevent deterioration of the siding. This installation should be accompanied by step flashings that adequately protect the wall and roof juncture from leaks. Hire a licensed general contractor to further evaluate and repair this condition.
- ED-5 Exteriors and Decks:
Improperly installed kick-out flashings were noted between the roof and wall juncture on the west side of the house - it does not properly tuck behind the siding on the upper edge. This could allow water to still get behind the flashing and cause damage over time. These are important to divert water away from the siding and onto the roof to prevent water from running behind the siding. No signs of water damage were found during the inspection, so repair may not be urgent, but problems at the roof-to-wall junctures can cause serious water damage if they develop. Hire a qualified contractor familiar with siding installation to further evaluate and repair when roofing and/or siding repairs are being made.
- ED-9 Exteriors and Decks:
A cover is recommend for the window wells of the house to help keep moisture and debris out.
- US-1 Utility Service:
When static water pressure exceeds 80 PSI, a pressure reducing valve is recommended to prevent accidental damage to the plumbing system. No reducing valve was found during inspection and water pressure is too high - it measured at roughly 105 psi in the front and back hose bib. Hire a licensed plumber to further evaluate and repair high water pressure as needed.
- G-1 Garage:
The control for the automatic garage door opener is not placed correctly. Locate the control button: (a) within sight of the door, (b) at a minimum height of 5ft above floors, landings, steps or any other adjacent walking surface so small children are not able to reach it, and (c) away from all moving parts of the door.
- G-2 Garage:
No strut or brace was found on the top section of the small garage door. This is to prevent the top section from getting damaged if the door is run down on something or someone.
- K-3 Kitchen:
The dishwasher racks are corroded and will eventually need to be replaced.
- HB-4 Hallway Bathroom:
The hallway bath fan is loud during operation. Based on the age and visible condition of the fans, I recommend updating this fan.
- P-3 Plumbing:
The sump pump should have a check valve, or one-way valve, installed on the drain line to prevent water from coming back into the crock after being pumped out. This will also help prevent the pump from being overworked and help it last longer.
- P-5 Plumbing:
The water heater temperature was set too low at the time of inspection - just 112 degrees F. The range of 120-125 degrees F is the generally recommended temperature. Adjust water heater temperature as needed.
- FSD-2 Fuel Storage and Distribution:
The CSST gas tubing is exposed and subject to mechanical damage in the fireplaces cabinet base. The CSST gas line should be protected by a grommet of some kind to prevent rubbing on the sharp edges of the cabinet.
- EDFW-2 Electric Distribution and Finish Wiring:
Modern standards recommend smoke alarms in all bedrooms, in all hallways outside bedrooms, and at least one on each floor of the building. At the time of inspection, no smoke alarms were found in the bedrooms.
Due Diligence Items
- GD-4 Grounds and Drainage:
An arborist should be hired to further evaluate the large trees on the property and prune or remove as recommended. Whenever large trees are located near a house a higher level of maintenance should be expected to keep trees safe and healthy and to eliminate the risks of damage to the home or building materials and to eliminate rodent entry points. With larger trees such as firs pruning is recommended to eliminate the sail effect and reduce strain on these tress during high winds. If an arborist has not been out in the last few years, I recommend a new consultation.
- P-1 Plumbing:
An evaluation of the sewer line below the ground is beyond the scope of this inspection. Due to the age and location of the building, a sewer scope is recommended to further evaluate the sewer line and the below-ground connections between the house and the municipal sewer line. Sewer scopes are done using video cameras and can reveal the materials, condition, and reliability of the sewer line.
- AP-1 Additional Plumbing:
An exterior irrigation system was noted for this home. Sprinkler systems are beyond the scope of this inspection. My own experience with irrigation systems is that they require annual attention/repair/servicing after every winter. Inquire with the seller for any information about how to winterize this system as this should be done before cold weather. When testing the system, be sure sprinkler heads are adjusted so the system is not watering the side of the house. Hire a specialist to further evaluate this system as desired.
Monitors
- RC-3 Roof and Chimney:
The roofing was showing signs of average granular loss for the age. As your roof ages, losing some granular textures is normal. Though age is the most common cause of granule loss, there are several other factors that can contribute to the premature failure of this protective coating. Severe weather such as heavy rain, hail, or strong winds can also knock your granules loose. Following a storm, you may find an increased amount of shingle granules in your gutters or in your yard. Granules help keep your roof weatherproofed, so without them, it’s easier for the sun and water to cause roof leaks and deterioration.
- GD-1 Grounds and Drainage:
Inadequate clearance between the siding and the hardscape of the front porch and back patio was noted. This is conducive to wood-destroying organisms as it can trap water against the siding. Where possible, an air gap should be provided to allow the wood to keep dry. Generally, a 2-inch clearance is recommended between the siding and the hardscape. Please note that this is a fairly common installation, and may not be cost-effective to correct at this point. It is difficult to predict if or when this condition will cause concealed damage to the wood behind.
- ED-8 Exteriors and Decks:
Visual inspection of the fiber cement siding installation showed the need for repairs as well as some installation details that are not consistent with modern manufacturers' installation requirements. This is typical for this age of construction. Some of the items noted can be repaired or improved, while others simply are the way they are until a larger re-siding is needed. Consult with a qualified contractor to further investigate the siding and repair as recommended to prolong the useful life of the siding. Examples of observations noted during the inspection include:
- HB-2 Hallway Bathroom:
The waste plumbing below the hallway bathroom sink has an older weep leak - see stains below the pipe. I ran lots of water today. No leakage was found. Monitor.
- P-4 Plumbing:
This water heater is likely nearing the end of its useful service life. The average life of these water heaters is statistically 8-12 years though in practice, they can vary widely between 8-20 years depending on water quality and maintenance schedule such as frequency of flushing the tank and replacing sacrificial anodes. Budget to replace this water heater at any time. The water was hot at the time of inspection.
- AP-5 Additional Plumbing:
This house has a water feature installed. It was operating at the time of inspection. Evaluation of water features is beyond the scope of this inspection. Water features often have filters, pumps, and other components that require regular servicing, maintenance, and cleaning. Water features can also pose a hazard for small children. Use caution if small children are around these water features. Remove or fence as deemed necessary for safety.
- HFV-1 Heating, Fireplaces, and Ventilation:
Furnaces have a typical life expectancy of 20 to 25 years. The existing unit is approaching this age range. One cannot predict with certainty when replacement will become necessary.
Efficiency Iaqs
- A-1 Attic:
The attic wall insulation was loose/missing on one section of the kitchen knee wall. Repair damaged thermal barriers as needed.
Future Projects
- ED-6 Exteriors and Decks:
Some of the penetrations in the siding do not have adequate mounting blocks. For penetrations in the building envelope such as hose bibs and holes 1½ inch diameter or larger, such as dryer vents, a block shall be installed around the point of penetration. Blocking should be a minimum 3 in.. radius greater than the radius of the penetration. To install a block around an existing penetration, it may be necessary to cut the block into two pieces. In this case, weather-cut the trim to fit it into place. Install flashing over the top of the trim block. Penetrations through a building envelope are made to accommodate needs such as hose bibs, dryer and furnace vents, electrical conduit, etc. It is important to restore the weather-resistant barrier of the home after cutting a hole for the penetration.
- C-1 Cooling:
A/C units have a typical life expectancy of 10 to 15 years. The existing unit(s) have exceeded this age range. One cannot predict with certainty when replacement will become necessary.
- LF-1 Laundry Facilities:
A moisture alarm with water shut-off features is recommended under the washing machine to protect against accidental leaks in the supply hoses. Pans can be effective when there is a drain, but even these will not protect against a burst supply connector. A moisture alarm with automatic shut-off will. Watts is a brand I have seen installed: Link.
- P-2 Plumbing:
The sump pump system does not appear to have any provisions for alarming the occupant if the system is disabled or failing. Consider installing a moisture alarm system to alert you if the pump were to fail or become disabled.
- EP-2 Electric Panels:
AFCI (arc fault protection) is now required on all branch circuits supplying outlets or devices installed in residential dwelling unit kitchens, family rooms, dining rooms, living rooms, parlors, libraries, dens, bedrooms, sunrooms, recreation rooms, closets, hallways, laundry areas, and similar rooms and areas. The goal of this protection is to reduce the risks of electrical fires. Consult with a licensed electrician about improving circuit protection as desired. Please note that if you add or replace receptacle outlets to the existing system, they should comply with modern AFCI standards.
📚PORTAL to the FULL REPORT
Grounds and Drainage
Drainage and Site
Grounds, Trees and Vegetation
Driveways/Walkways/Flatwork
Exterior Stairs
Exterior Hose Bibs
Exteriors and Decks
Exterior Elevations
Siding and Trim
Exterior Doors
Exterior Window Frames
Window Wells and Stairwells
Utility Service
Electric Service
Electrical Grounding System
Electrical Bonding System
Water Meter
Water Service Supply
Gas Meter
Kitchen
Sinks and Faucets
Cabinets and Countertops
Disposers
Dishwasher
Ranges, Ovens and Cooktops
Ventilation Method
Refrigerators
Heating, Fireplaces, and Ventilation
House Heating System
Air Filters
Whole House Humidifier
Vents and Flues
Heating and Cooling Distribution Systems
General Comments
Building Characteristics, Conditions and Limitations
Type of Building : Single Family (1 story with Basement)
Approximate Year of Original Construction: 2007
Attending the Inspection: Buyer and Buyer's Agent
Occupancy: Occupied
This home was occupied at the time of the inspection. Inspection of occupied homes presents some challenges as occupant belongings can obstruct visual inspection of and access to parts of the building. We do our best during inspection to work around belongings to discover as much as possible about the house without moving or damaging personal property, however, the presence of personal items does limit the inspection.
Weather during the inspection: Clear
Approximate temperature during the inspection: 60-70[F]
Ground/Soil surface conditions: Dry
For the Purposes of This Report, the Front Door Faces: East
Roof and Chimney
House Roof Materials
Method of Roof Inspection: Walked on roof
Roof Style: Gable
Flashings: Present and Visually Standard
Roof flashings are used to keep a roofing system waterproof where the roofing material starts, stops, changes direction, or is penetrated. During the inspection, we look for standard flashing techniques that could be considered normal in our region. Damaged, incomplete or non-standard flashings can be a sign of an older or less reliable roofing system and may require repair. Any non-standard flashings noted during the inspection will be reported below if found.
Roof Covering Materials: Architectural grade composition shingle
Approximate Age of Roof Covering: 10-15+ Years
Overlay Roof: No
Composition Comments: Exposed nails
The roofing was showing signs of average granular loss for the age. As your roof ages, losing some granular textures is normal. Though age is the most common cause of granule loss, there are several other factors that can contribute to the premature failure of this protective coating. Severe weather such as heavy rain, hail, or strong winds can also knock your granules loose. Following a storm, you may find an increased amount of shingle granules in your gutters or in your yard. Granules help keep your roof weatherproofed, so without them, it’s easier for the sun and water to cause roof leaks and deterioration.
Many criteria are used to "guesstimate" the age of the roof. Listing information, age of home, assessor information, google maps drive-by pictures, disclosure statements, deterioration or lack thereof, pipe flashings, exposure, date stamps on pipe flashings, roof type, and color, and experience. One or more of these indicators are used to make this judgment--it is NOT absolute and should not be taken as such.
Gutters and Downspouts
Gutter and Downspout Materials: Aluminum
Downspout discharge: Above grade
Grounds and Drainage
Drainage and Site
Clearance to Grade: Siding Too Close to Hardscape - Not Ideal, Standard
Site Description: Moderate slope, Grade Toward Building
The grade of the east yard is slopping toward the building and/or there are low spots along the house. Standards recommend a quarter inch/foot slope away from the building or better. The flower beds were sloping towards the house and should be improved. This will help keep the basement/crawl space from leaking.
Inadequate clearance between the siding and the hardscape of the front porch and back patio was noted. This is conducive to wood-destroying organisms as it can trap water against the siding. Where possible, an air gap should be provided to allow the wood to keep dry. Generally, a 2-inch clearance is recommended between the siding and the hardscape. Please note that this is a fairly common installation, and may not be cost-effective to correct at this point. It is difficult to predict if or when this condition will cause concealed damage to the wood behind.
Grounds, Trees and Vegetation
Trees/Vegetation too near building: Yes - Prune Vegetation off House, Arborist Recommended
An arborist should be hired to further evaluate the large trees on the property and prune or remove as recommended. Whenever large trees are located near a house a higher level of maintenance should be expected to keep trees safe and healthy and to eliminate the risks of damage to the home or building materials and to eliminate rodent entry points. With larger trees such as firs pruning is recommended to eliminate the sail effect and reduce strain on these tress during high winds. If an arborist has not been out in the last few years, I recommend a new consultation.
Driveways/Walkways/Flatwork
Driveway: Concrete
Walkways: Concrete
Patios: Concrete
Typical cracks were noted in cement flat work. No immediate repair appears necessary, though water will continue to deteriorate the surface until the cracks are sealed.
Exterior Stairs
Exterior Stairs: Stairway Too Narrow
The riser heights for the exterior back stairs are not even and are not to modern standards. This is a trip and safety hazard. The height of the tallest riser shall not exceed the smallest riser by more than 3/8th of an inch. Hire a licensed general contractor to further evaluate and repair.
The exterior stairway to the front door appears to be too narrow. Stairways shall not be less than 36 inches in clear width at all points above the permitted handrail height and below the required headroom height. Handrails shall not project more than 4.5 inches on either side of the stairway and the minimum clear width of the stairway at and below the handrail height, including treads and landings, shall not be less than 31.5 inches where a handrail is installed on one side and 27 where handrails are provided on both sides. Have this further evaluated and repaired as recommended by a qualified general contractor.
Exterior Hose Bibs
Operating
Exteriors and Decks
Siding and Trim
Siding Material: Brick, Fiber-cement
Manufacturers of fiber cement siding have done a poor job helping inspectors and consumers distinguish their products after installation; these products have few if any distinguishing characteristics. This report will site James Hardie manufacturers installation requirements for reference because they are the most common manufacturer of fiber cement siding and the various manufactures seem to share similar installation guidelines. However, reference of these guidelines in this report does not ensure that the fiber cement siding here is a James Hardie product.
Trim Material: Wood
Eaves: Plywood
Some of the exterior siding flashings are inconsistently executed. Proper flashing techniques are important to ensure the siding system sheds water reliably. I recommend additional inspection and repair by a qualified contractor to ensure the siding system reliably sheds water.
- Lap siding trim window openings missing head flashing on the north side
Areas for re-caulking were noted on the exterior - see around window frames, door frames, and utility penetrations. Preventative caulking maintenance can help keep these spots weatherproof.
The exterior wood siding and trim need to be re-painted to preserve and maintain the siding system. Budget for re-painting the exterior in the near term. This is routine maintenance but is a concern due to upcoming costs.
Inadequate clearances were noted between the roof and the siding. A 2 inch air gap is recommended here to keep the siding off the roof and prevent deterioration of the siding. This installation should be accompanied by step flashings that adequately protect the wall and roof juncture from leaks. Hire a licensed general contractor to further evaluate and repair this condition.
Improperly installed kick-out flashings were noted between the roof and wall juncture on the west side of the house - it does not properly tuck behind the siding on the upper edge. This could allow water to still get behind the flashing and cause damage over time. These are important to divert water away from the siding and onto the roof to prevent water from running behind the siding. No signs of water damage were found during the inspection, so repair may not be urgent, but problems at the roof-to-wall junctures can cause serious water damage if they develop. Hire a qualified contractor familiar with siding installation to further evaluate and repair when roofing and/or siding repairs are being made.
Visual inspection of the fiber cement siding installation showed the need for repairs as well as some installation details that are not consistent with modern manufacturers' installation requirements. This is typical for this age of construction. Some of the items noted can be repaired or improved, while others simply are the way they are until a larger re-siding is needed. Consult with a qualified contractor to further investigate the siding and repair as recommended to prolong the useful life of the siding. Examples of observations noted during the inspection include:
Some of the penetrations in the siding do not have adequate mounting blocks. For penetrations in the building envelope such as hose bibs and holes 1½ inch diameter or larger, such as dryer vents, a block shall be installed around the point of penetration. Blocking should be a minimum 3 in.. radius greater than the radius of the penetration. To install a block around an existing penetration, it may be necessary to cut the block into two pieces. In this case, weather-cut the trim to fit it into place. Install flashing over the top of the trim block. Penetrations through a building envelope are made to accommodate needs such as hose bibs, dryer and furnace vents, electrical conduit, etc. It is important to restore the weather-resistant barrier of the home after cutting a hole for the penetration.
Exterior Doors
Solid core, Sliding glass, Glass panel doors
Exterior Window Frames
Vinyl
Window Wells and Stairwells
Present, Window Well (Organic Debris)
Utility Service
Electric Service
Service Entrance: Below Ground
Meter Base Amperage: 200
Electrical Grounding System
UFER Ground Noted
A UFER ground connection was noted for the electrical grounding system. These are required and standard on newer construction houses. These grounds connect the electrical system to Rebar in the house foundation and make a reliable path to the earth for "earthing" or grounding the electrical system.
Electrical Bonding System
Present - Could Not Confirm
During the inspection, I attempt to visually document electrical system bonding. There is no way in the context of a home inspection to verify the "effectiveness" of system bonding. All metallic systems in the building are required to be "bonded" (connected) to the the building's electrical grounding system. Bonding creates a pathway to shunt static charges (that would otherwise build up on the system) to earth, and to provide a pathway to trip a breaker in the event that these bonded metallic components became energized. There are many things that can lead me to recommend further evaluation of this system by a licensed electrical contractor and they will be documented as repair items in the observations below if discovered.
Water Meter
Water Service Supply
Pipe Material: Plastic
Water Supply: Public water
Water Pressure: 105 PSI
Pressure Reducing Valve: None noted
When static water pressure exceeds 80 PSI, a pressure reducing valve is recommended to prevent accidental damage to the plumbing system. No reducing valve was found during inspection and water pressure is too high - it measured at roughly 105 psi in the front and back hose bib. Hire a licensed plumber to further evaluate and repair high water pressure as needed.
Cooling
Cooling Systems and Heat Pumps
Air Conditioning / Heat Pump: Air Conditioning Present
System Type: Air Source
Manufacturer: Carrier
Age: 2007
A/C units have a typical life expectancy of 10 to 15 years. The existing unit(s) have exceeded this age range. One cannot predict with certainty when replacement will become necessary.
Garage
Garage General
Garage Type: Attached
Garage Doors and Automatic Openers
Overhead Garage Door Type: Metal
Automatic Garage Opener: Present
Garage Occupant Door: Solid Wood
The overhead garage doors in the garage do not reverse under resistance to closing. Adjustment of the sensitivity is recommended for improved safety. An adjustment setting can often be found as a plastic screw on the opener - I recommend consulting with the owners' manual or looking up the manual online as needed.
The control for the automatic garage door opener is not placed correctly. Locate the control button: (a) within sight of the door, (b) at a minimum height of 5ft above floors, landings, steps or any other adjacent walking surface so small children are not able to reach it, and (c) away from all moving parts of the door.
Garage Stairs and Railings
Standard
Garage Floor
Garage Slab: Concrete
Attic
Attic Access
Crawled partial
Roof Framing and Sheathing
Rafters: Truss
Sheathing: OSB
Attic Insulation
Insulation Type: Rock wool
Approximate Insulation R-Value on Attic Floor: 30, 20
Approximate Insulation R-Value on Attic Walls: 13, Falling Down
Attic and Roof Cavity Ventilation
Attic Ventilation Method: Soffit vents, Roof jack vents
Attic and roof cavity ventilation is a frequently-misunderstood element of residential construction. All roof cavities are required to have ventilation. The general default standard is 1 to 150 of the attic area and ideally, this comes from at least 60% lower roof cavity ventilation and 40% upper, but this is a wild over-simplifications of the subject. As a good guiding principle the most important elements for healthy attic spaces, which are traditionally insulated and ventilated are:
- Make sure the ceiling between the living space and the attic is airtight
- Ventilate consistently across the whole lower part of the roof cavity with low, intake soffit venting
- Upper roof cavity venting is less important and if over-installed can exacerbate air migration into the attic from the living space.
- Avoid power ventilators which can depressurize the attic and exacerbate air migration from the house into the attic.
For more information, please see: Link
Kitchen
Sinks and Faucets
Tested
Cabinets and Countertops
Countertop Material: Granite
Cabinet Material: Wood laminate
Disposers
Disposer: Operated
Dishwasher
Dishwasher: Operated, Rack (Corroded)
Dishwasher Air Gap: Present, Air Gap Is Below Kitchen Sink
The dishwasher drain line is missing a proper air gap to prevent siphoning waste water back into the dishwasher. This should be done so that the drain is not always submerged in the wastewater. The dishwasher drain connection point should be moved higher onto the sink downpipe. This should be repaired by a qualified plumber
The dishwasher racks are corroded and will eventually need to be replaced.
Ranges, Ovens and Cooktops
Range/ Oven /Cook-tops: Electric
Ventilation Method
Fan Ducted to Exterior
Refrigerators
Refrigerator: Operating
Basement Wet Bar
Sinks and Faucets
Tested
Cabinets and Countertops
Countertop Material: Plastic laminate
Cabinet Material: Wood laminate
Disposers
Disposer: Operated
Dishwasher
Dishwasher: Operated
Dishwasher Air Gap: Present
Refrigerators
Refrigerator: Operating, Ice Maker (Coagulated Ice)
The basement wet bar refrigerator ice maker was noted to be full of coagulated ice. Remove old ice, clean ice try and change any water filters as needed.
Laundry Facilities
Washer
Not tested, Moisture Alarm System - Recommended
A moisture alarm with water shut-off features is recommended under the washing machine to protect against accidental leaks in the supply hoses. Pans can be effective when there is a drain, but even these will not protect against a burst supply connector. A moisture alarm with automatic shut-off will. Watts is a brand I have seen installed: Link.
Dryer
Not tested
Power Source: Electric
Exhaust Duct: Ducted to Exterior, Cleaning Needed
The dryer exhaust ductwork is dirty and needs to be cleaned for improved safety. This is important for regular maintenance to eliminate a potential fire hazard. This should be cleaned annually to prevent lint build-up.
Hallway Bathroom
Sinks and Cabinets
Tested
Toilet
Tested
Bathtub / Shower
Tested
Bathroom Ventilation
Type: Bath fan
The hallway bath fan is loud during operation. Based on the age and visible condition of the fans, I recommend updating this fan.
General Bath Condition
Caulking: Normal caulking maintenance
The hallway bathroom caulking is needed on the sink countertop and backsplash, around the base of the toilet, at the tub and floor joint and around the tub spout in the bathroom to prevent water from damaging the floor.
Master Bathroom
Sinks and Cabinets
Tested
Toilet
Tested
The master bathroom toilet was fussy to operate, the handle hits the lid. The handle had to be held down for some time to get the unit to flush properly. Repair, adjust, or replace the toilet as needed for reliable performance.
Bathtub / Shower
Tested
The shower head in the master bathroom shower needs to be cleaned or replaced. Calcium build-up and scaling are causing the shower head to spray at right angles and water is spraying out of the shower. If the house is on a well system, this can also indicate that sediment is entering the water supply. If this is a persistent problem, it can often be corrected by adding a filter at the well.
Bathroom Ventilation
Type: Bath fan
The fan in the master bath toilet room did not appear operational. I tried all switches on the walls and the fan did not come one: is there a hidden switch? Have this fan repaired as needed to ensure adequate ventilation for this bathroom.
General Bath Condition
Caulking: Normal caulking maintenance
The master bathroom caulking is needed on the sink countertop and backsplash, around the base of the toilet, at the tub and floor joint, around the tub spout and on the tub ledge in the bathroom to prevent water from damaging the floor.
Basement Bathroom
Sinks and Cabinets
Tested
Toilet
Tested
The basement bathroom toilet appears to keep running after flushing. This can often be stopped by jiggling the handle. This is not satisfactory. Hire a plumber to further evaluate and repair this toilet to prevent water waste.
Bathtub / Shower
Tested
Bathroom Ventilation
Type: Bath fan
General Bath Condition
Caulking: Normal caulking maintenance
The basement bathroom caulking is needed around the base of the toilet and at the tub and floor joint in the bathroom to prevent water from damaging the floor.
Interior
Windows
Window Glazing: Double pane
Interior Window Frame: Vinyl
Window Styles: Casement, Fixed pane, Sliding
Stairs and Railings
Standard
Walls, Ceilings, Trim and Closets
Wall and Ceiling Materials: Drywall
Plumbing
Distribution Pipe
Supply Pipe Materials: Copper, PEX
Copper water supply pipes were installed. Copper pipes installed before the late 1980s may be joined with solder that contains lead, which is a known health hazard, especially for children. Laws were passed in 1985 prohibiting the use of lead in solder, but before that solder normally contained approximately 50% lead. The client should be aware of this, especially if children will be using this water supply system. Note that the inspector does not test for toxic materials such as lead. The client should consider having a qualified lab test for lead, and if necessary take steps to reduce or remove lead from the water supply. Various solutions include:
- Flush water taps or faucets. Do not drink water that has been sitting in the plumbing lines for more than 6 hours
- Install appropriate filters at points of use
- Use only cold water for cooking and drinking, as hot water dissolves lead more quickly than cold water
- Treat well water to make it less corrosive
- Have a qualified plumber replace supply pipes and/or plumbing components as necessary
Functional Flow: Excellent
Circulation Pump: None Noted
Waste Pipe and Discharge
Discharge Type: Public Sewer - Buyer
Waste and Vent Pipe Materials: PVC
An evaluation of the sewer line below the ground is beyond the scope of this inspection. Due to the age and location of the building, a sewer scope is recommended to further evaluate the sewer line and the below-ground connections between the house and the municipal sewer line. Sewer scopes are done using video cameras and can reveal the materials, condition, and reliability of the sewer line.
Sump Pumps and Drains
Floor Drain: Present
Sump Pumps: Present, No Alarm Noted
The sump pump system does not appear to have any provisions for alarming the occupant if the system is disabled or failing. Consider installing a moisture alarm system to alert you if the pump were to fail or become disabled.
Water Heater
System Type: Tank
Energy Source: Gas
Manufacturer: State Select
Age: 2007
Size: 50 gal
Temperature Pressure Relief Value: Present - Not Tested
The temperature and pressure relief valve are arguably one of the most important safety devices in your house. Should the thermostats fail inside your water heater, the TPRV allows excess pressure to "blow off," which will prevent the catastrophic build-up of temperature and pressure which can make water heaters explosive. I do not test the "blow off valve" during the inspection as there is a risk it could stick open and testing could cause the need for a repair. Manufacturers of these relief valves recommend that these be tested annually. You need to decide for yourself if this is the type of annual testing you wish to perform.
Drain Pan: Not Needed
This water heater is likely nearing the end of its useful service life. The average life of these water heaters is statistically 8-12 years though in practice, they can vary widely between 8-20 years depending on water quality and maintenance schedule such as frequency of flushing the tank and replacing sacrificial anodes. Budget to replace this water heater at any time. The water was hot at the time of inspection.
Water Temperature
Water Temperature Measured During Inspection: 112 Degrees F
Additional Plumbing
Irrigation
Sprinkler System: Noted For Buyer
Private Well: Location (West)
Controller : North exterior
Back-flow Valve: Not needed because of irrigation well
Zones: Visible water piping material (Plastic (PVC, CPVC, PEX))
An exterior irrigation system was noted for this home. Sprinkler systems are beyond the scope of this inspection. My own experience with irrigation systems is that they require annual attention/repair/servicing after every winter. Inquire with the seller for any information about how to winterize this system as this should be done before cold weather. When testing the system, be sure sprinkler heads are adjusted so the system is not watering the side of the house. Hire a specialist to further evaluate this system as desired.
Water Features
Common: Working
This house has a water feature installed. It was operating at the time of inspection. Evaluation of water features is beyond the scope of this inspection. Water features often have filters, pumps, and other components that require regular servicing, maintenance, and cleaning. Water features can also pose a hazard for small children. Use caution if small children are around these water features. Remove or fence as deemed necessary for safety.
Heating, Fireplaces, and Ventilation
House Heating System
Energy Source: Natural gas
Heating Method: Gas forced air furnace
This house has a gas-forced air furnace. A critical component of all combustion equipment like this is the heat exchanger. This is the welded clam-shell piece of metal inside the furnace that contains the products of combustion so that moisture, carbon monoxide, and other products of combustion do not mix with interior air and get safely vented to the exterior. Heat exchangers on modern furnaces have an average life expectancy of 15-20 years. Unfortunately, heat exchangers are buried inside heating equipment; they are not visible and specifically excluded from a home inspection.
Manufacturer: Carrier
Age: 2007
Annual servicing of the gas forced air furnace is recommended for safe and reliable heat. I could not find recent service records on the furnace. The furnace was tested during inspection and was operational. The design life of these forced air furnaces is 20-25 years. I recommend having it serviced and keeping it on an annual service schedule until updated.
Furnaces have a typical life expectancy of 20 to 25 years. The existing unit is approaching this age range. One cannot predict with certainty when replacement will become necessary.
Air Filters
Filtration Systems: Disposable
Your heating and cooling system has disposable air filters installed. One-inch filters should be changed quarterly or more and five-inch filters should be changed every six months or more to ensure proper airflow at the furnace. Be sure to install the filters with the arrows pointing in the same direction as the airflow in the furnace.
The dirty air filter for the forced air furnace should be replaced. Plan on replacing air filters every 2-3 months during the heating season.
Whole House Humidifier
Whole House Humidifier Installed: Did not operate using normal controls
Vents and Flues
The B-vent flue for the furnace is corroded above the roofline and the hat is missing, this requires replacement. Have this flue piping further evaluated and repaired as recommended by a qualified heating contractor as water staining and minor corrosion were noted in the utility room on the flue piping as well. Please note that the correct cap design can help prevent corrosion of the top of the vent pipe.
Heating and Cooling Distribution Systems
Heat Source in Each Room: Present
Distribution Method: Forced Air / Ducts
Fireplaces
Gas Fireplaces
Fireplace Types: Direct vent - decorative log set
Gas Shut off Noted: Yes
System Responded to Testing: Yes and I did a CO test
I tested the gas log fireplaces today and did a carbon monoxide test. The appliances appeared to be operating as intended and no CO was detected. It is always a good idea to have carbon monoxide detectors in a house when using gas appliances.
The glass for the gas log fireplaces is cloudy. Though very common, this is not the intended appearance of a decorative gas log fireplace. Sometimes, silicates from the logs can get etched onto the glass which can make cleaning difficult. Hire a gas log specialist to service the gas log fireplaces and clean or replace the glass as needed.
The following is a recommended procedure for cleaning the glass on gas fireplaces.
1) Make sure your glass is cool to the touch. It is also recommended that your pilot is turned off before you begin to clean the glass.
2) Remove the front face or louvers of your fireplace.
3) Follow the instructions in your manual to carefully remove the glass assembly. Lay it on a soft surface.
4) Using a soft cloth, clean both sides of the glass with a household glass cleaner. Do not use a product with ammonia or any abrasive cloth or cleaner to clean your glass. The glass can shatter if it is scratched. For heavy deposits, use a hard water deposit glass cleaner, such as Stove Bright Glass Cleaner.
5) Follow the instructions in your manual to carefully replace the glass on the front of the fireplace. Make sure you re-latch the glass so it is securely fastened on your fireplace.
Fuel Storage and Distribution
Gas, Propane and Oil Piping
Gas Piping Materials Noted: Steel, CSST
The 2009 edition of NFPA 54, National Fuel Gas Code, includes new requirements for bonding CSST gas piping systems to the grounding conductor of the building's electrical system, to reduce the possibility of damage by lightning strikes by reducing the electrical potential between metallic objects and building systems, including gas distribution. I was unable to locate a bonding connection for the CSST during inspection today. Have this further evaluated and repaired as recommended by a qualified CSST installer.
The CSST gas tubing is exposed and subject to mechanical damage in the fireplaces cabinet base. The CSST gas line should be protected by a grommet of some kind to prevent rubbing on the sharp edges of the cabinet.
Electric Panels
Main Panel
Service Entrance (SE) conductor Size: Aluminum, 4/0, 200 amps
Main Panel Amperage: 200 amps
Electric Service Amperage: 200 amps
Main Electric Panel Location: Basement, Bedroom
Panel Manufacturer: Siemens
Notes and Limitations: Modern AFCI and GFCI Note
Hire a licensed electrician to correct the double-tapped circuit in the electric panel - this is when two conductors share the same breaker. This condition risks poorly protected circuits and as such is a latent fire hazard if conductors are not properly torqued. This requires additional evaluation by an electrician.
AFCI (arc fault protection) is now required on all branch circuits supplying outlets or devices installed in residential dwelling unit kitchens, family rooms, dining rooms, living rooms, parlors, libraries, dens, bedrooms, sunrooms, recreation rooms, closets, hallways, laundry areas, and similar rooms and areas. The goal of this protection is to reduce the risks of electrical fires. Consult with a licensed electrician about improving circuit protection as desired. Please note that if you add or replace receptacle outlets to the existing system, they should comply with modern AFCI standards.
Appliance Disconnects
Disconnects Noted: Air Conditioner
Electric Distribution and Finish Wiring
Branch Wiring
Wire Material: Copper, Multi-strand Copper
Wiring Method: Non-metallic sheathed cable, Armored Flexible Cable
Abandoned wiring was noted in the attic. This should be eliminated or properly terminated inside a listed junction box. It is often not feasible to determine if the wire is still connected to a power source. I can test these with a voltage sensor, but they could be shut off by a switch or temporarily disconnected. For safety, all abandoned wires should be eliminated.
Receptacles and Fixtures
Inspection Method: Random Testing
Electric Receptacles: Three wire receptacles
Ceiling Fans
Ceiling Fans: Present and Tested
Smoke and Carbon Monoxide Alarm Systems
CO Alarms: None Noted
The installation of carbon monoxide alarms is recommended for all homes that have fuel burning appliances such as gas or oil furnaces, gas water heaters, gas ovens and cook-tops, gas fireplaces and wood stoves. The location should be: at least one alarm outside of all sleeping areas and one on each floor of the house. Best practices are to have these alarms hardwired with a battery back-up - though requirements are for the installation to meet manufacturer's specifications. Carbon monoxide is a colorless, odorless gas that can cause sickness, nausea and even death. Alarms have a useful service life of roughly 6 years, so changing them more frequently than smoke alarms is recommended.
Smoke Alarms Noted:On Main Floor
In Basement
Smoke Alarms: None In Bedrooms, Present, Old, Updating Recommended
During the home inspection, I try and test a representative sample of the smoke alarms by using the test button on the alarms. This is NOT an accurate test of the sensor just a test to see if the unit is powered. For reliability, fire marshals recommended updating smoke alarms every 10 years and changing batters bi-annually. The latest data indicate that we should be using photo-electric technology in our smoke alarms for improved fire detection and to reduce problems with false alarms which can lead to disabling of this important safety system. Unfortunately, the alarms have to be removed to determine if they are photo-electric or ionization types. It is surprisingly complex to accurately test a smoke alarm system and determine the reliability, age, and type of sensor technology used, especially as many homes can have half a dozen or more alarms throughout the house. A complete evaluation of smoke alarms is beyond the scope of this inspection. For optimal fire safety, I recommend taking control of these important safety devices and learning about how to service and maintain your smoke alarm system to keep the building occupants safe. For more information, please read this link. For more information, please read this link.
The installation of carbon monoxide alarms is recommended for all homes that have fuel-burning appliances such as gas or oil furnaces, gas water heaters, gas ovens, cook-tops, gas fireplaces, and wood stoves. Carbon monoxide is a colorless, odorless gas that can cause sickness, nausea, and even death. For more information, consult the Consumer Product Safety Commission at 1-800-638-2772 (C.P.S.C.) Modern standards in many states now recommend one CO alarm outside of all bedrooms and at least 1 per floor of the house.
These appear to be the original smoke alarms. These are getting old. Fire marshals recommended updating smoke alarms every 10 years to ensure reliable performance. Updating is recommended.
Structure and Basement
Foundation
% of Foundation Not Visible: 80%
Building Configuration: Basement, Slab on grade (garage slab)
Foundation Description: Poured concrete
Floor, Wall and Ceiling Framing
Wall Framing: 2x4
Wall Sheathing: OSB
Floor Framing: Trusses
Sub-Floor Material: OSB
Ceiling Framing: Bottom cord of truss
Basement
Full
Basement Moisture
None noted
Checking Out Procedure
Check Out List
Oven:Off
Lights:Seller Still in House
Heating and Cooling:Restored to Pre-inspection temperatures
Appliances:Off / finishing cycle
Receipt -- 📚PORTAL to the FULL REPORT
123 Abc Ct. Wichita, KS 67212
Inspection | $375.00 |
$0.00 | |
375 | |
PAID |
Top Gear Home Inspections, LLC
P.O. Box 34
Mulvane, KS 67110
(316) 351-8784
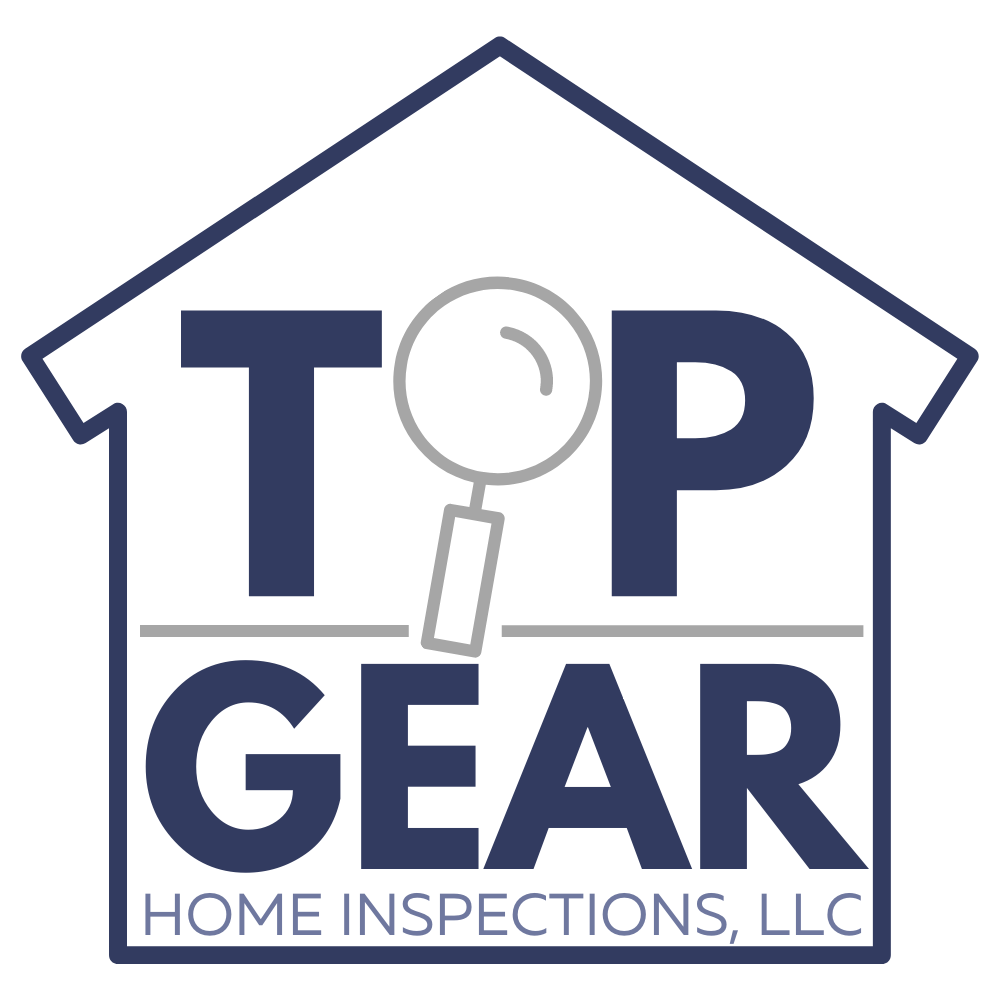