The Scope and Purpose of a Home Inspection
Purchasing property involves risk
The purpose of a home inspection is to help reduce the risk associated with the purchase of a structure by providing a professional opinion about the overall condition of the structure. A home inspection is a limited visual inspection and it cannot eliminate this risk. Some homes present more risks than others. We cannot control this, but we try to help educate you about what we don’t know during the inspection process. This is more difficult to convey in a report and one of many reasons why we recommend that you attend the inspection.
A home inspection is not an insurance policy
This report does not substitute for or serve as a warranty or guarantee of any kind. Home warranties can be purchased separately from insuring firms that provide this service.
A home inspection is visual and not destructive
The descriptions and observations in this report are based on a visual inspection of the structure. We inspect the aspects of the structure that can be viewed without dismantling, damaging or disfiguring the structure and without moving furniture and interior furnishings. Areas that are concealed, hidden or inaccessible to view are not covered by this inspection. Some systems cannot be tested during this inspection as testing risks damaging the building. For example, overflow drains on bathtubs are generally not tested because if they were found to be leaking they could damage the finishes below. Our procedures involve non-invasive investigation and non-destructive testing which will limit the scope of the inspection.
This is not an inspection for code compliance
This inspection and report are not intended for city / local code compliance. During the construction process structures are inspected for code compliance by municipal inspectors. Framing is open at this time and conditions can be fully viewed. Framing is not open during inspections of finished homes, and this limits the inspection. All houses fall out of code compliance shortly after they are built, as the codes continually change. National codes are augmented at least every three years for all of the varying disciplines. Municipalities can choose to adopt and phase in sections of the codes on their own timetables. There are generally no requirements to bring older homes into compliance unless substantial renovation is being done.
This is just our opinion
Construction techniques and standards vary. There is no one way to build a house or install a system in a house. The observations in this report are the opinions of the home inspector. Other inspectors and contractors are likely to have some differing opinions. You are welcome to seek opinions from other professionals.
The scope of this inspection
This inspection will include the following systems: exterior, roof, structure, drainage, foundation, attic, interior, plumbing, electrical and heating. The evaluation will be based on limited observations that are primarily visual and non-invasive. This inspection and report are not intended to be technically exhaustive.
Your expectations
The overall goal of a home inspection is to help ensure that your expectations are appropriate with the house you are proposing to buy. To this end we assist with discovery by showing and documenting observations during the home inspection. This should not be mistaken for a technically exhaustive inspection designed to uncover every defect with a building. Such inspections are available but they are generally cost-prohibitive to most homebuyers.
Your participation is requested
Your presence is requested during this inspection. A written report will not substitute for all the possible information that can be conveyed verbally by a shared visual observation of the conditions of the property.
How to Read This Report
Getting the Information to You
This report is designed to deliver important and technical information in a way that is easy for anyone to access and understand. If you are in a hurry, you can take a quick look at our "Summary Page” and quickly get critical information for important decision making. However, we strongly recommend that you take the time to read the full Report, which includes digital photographs, captions, diagrams, descriptions, videos and hot links to additional information.
The best way to get the layers of information that are presented in this report is to read your report online, which will allow you to expand your learning about your house. You will notice some words or series of words highlighted in blue and underlined – clicking on these will provide you with a link to additional information.
This report can also be printed on paper or to a PDF document.
Chapters and Sections
This report is divided into chapters that parcel the home into logical inspection components. Each chapter is broken into sections that relate to a specific system or component of the home. You can navigate between chapters with the click of a button on the left side margin.
Most sections will contain some descriptive information done in black font. Observation narrative, done in colored boxes, will be included if a system or component is found to be significantly deficient in some way or if we wish to provide helpful additional information about the system or the scope of our inspection. If a system or component of the home was deemed to be in satisfactory or serviceable condition, there may be no narrative observation comments in that section and it may simply say “tested,” or “inspected.”
Observation Labels
All narrative observations are colored, numbered and labeled to help you find, refer to, and understand the severity of the observation. Observation colors and labels used in this report are:
- Major Concern:Repair items that may cost significant money to correct now or in the near future, or items that require immediate attention to prevent additional damage or eliminate safety hazards.
- Repair:Repair and maintenance items noted during inspection. Please note that some repair items can be expensive to correct such as re-finishing hardwood floors, but are considered simply repair items due to their cosmetic nature.
- Recommended Maintenance:These are repair items that should be considered "routine home ownership items," such as servicing the furnace, cleaning the gutters or changing the air filters in the furnace.
- Improve:Observations that are not necessarily defects, but which could be improved for safety, efficiency, or reliability reasons.
- Due Diligence:Observation such as a buried oil tank that may require further investigation to determine the severity and / or urgency of repair.
- Note:Refers to aside information and /or any comments elaborating on descriptions of systems in the home or limitations to the home inspection.
- Description:Detailed description of various aspects of the property noted during the inspection.
Summary Page
The Summary Page is designed as a bulleted overview of all the observations noted during inspection. This helpful overview is not a substitution for reading the entire inspection report. The entire report must be read to get a complete understanding of this inspection report as the Summary Page does not include photographs or photo captions.
Summary
Major Concerns
- R-1 Roof/Attic:
The roofing material on this building is a torch down or modified bitumen membrane. The service life of these roofs can vary depending on the quality of the membrane and the quality of the installation, including how well the roof is sloped to drain. Torch down roofs often have roughly 10 years of reliable service life beyond which regular repairs are often needed. With on-going maintenance these roofs can be made to last as long as 25-30 years. This roof is 35+ years old and well beyond its expected life span. Several red flags were noted during inspection that indicate vulnerable and potentially failing areas of the roof. Hire a licensed roofing contractor to replace this roof as recommended. If repairs are made and the roof is kept in service funds should be reserved for replacement at any time. Examples of observations noted during inspection include:
- Welded seam sealant is missing, losing its bond and peeling off easily.
- Some of the welded seams have the membrane beginning to peel up & separate.
- Deterioration & break down of the membrane itself is occurring due to UV sun exposure indicating this membrane needs replaced. The silver reflective coating that once protected this roof has since worn away and no longer is providing any protection.
- Seams are separating at most of the roof penetrations & flashings.
- A few active leaks are present around the NW corner chimney.
A roof replacement estimate has been provided by Top Roof Care of $85,000 and includes the installation of new 1/2" CDX plywood priced at $21,600 (which may not be needed) and roof replaced with WeatherBond TPO membrane.
Repairs
- G-1 Grounds:
The SW corner doorway to the building sits lower than the walkway and has no provisions for controlling rain water. A surface drain track should be installed or a shallow swale that can capture rain water and divert away from building entryway. Installation of a surface drain would be included in the concrete flatwork estimate.
- G-2 Grounds:
Approximately 345 sq ft of concrete driveway & sidewalk are cracked, damaged & creating trip hazards requiring replacement on the south side of building.
It is unsure whether this is part of this property or it is the responsibility of the city. If repairs fall on the responsibility of the property owner, I expect costs to be around $4,500.
- G-3 Grounds:
The south entrance stairs have one moisture damaged step runner on the west end steps that should be replaced. Additionally, the east end steps are missing a railing system and should be installed. The cost for both of these items would be around $1,200.
- G-4 Grounds:
A framed cover is present over these stairs & entryway but is missing the roof paneling that will make this weather resistant. The cost to install some corrugated material here would be minimal, around $500.
- E1-1 Exterior/Garage:
Several vertical & horizontal cracks are present on the exterior & interior of this nearly 100 year old concrete building. Cracks are common in concrete and these once appear to have been patched or sealed but have since separated and opened up again, most likely from expansion & contraction. Many other areas of cracking are present around the window openings where some have been patched and are still good patches but many other areas that have openings need to be addressed/repaired. Some areas of exposed rebar are present and need to be patched to protect the rebar from oxidation & rust. Several small spots of concrete are spalling as well, this indicates that water is being absorbed into the concrete and is causing it to peel and flake apart. If this condition continues unchecked, the damage just continues to progress further affecting a larger area.
Hire a licensed contractor who specializes in concrete to further evaluate this condition and repair. A quote from AVE Concrete & Flatwork came in at $35,000 for all exterior repairs and $25,000 for interior repairs totaling $60,000 + tax.
- E1-2 Exterior/Garage:
Plywood is being used as an exterior siding material and is not preferred as it decays quickly due to exterior exposure. The panel next to the south entrance door is rotting at the bottom end. The plywood panels on the NE & SE corners of the building above doorways are also deteriorated, bowed and no longer water-proof. These panels should be replaced with a more superior exterior material and appropriately sealed & painted. Replacement of these panels with a proper siding material would be around $1,500.
- E1-3 Exterior/Garage:
Several wall penetrations are present in the exterior building wall that are not properly sealed. See where gas line & electrical service conduits penetrate the concrete walls. Have an approved exterior sealant applied to seal these penetrations from water, rodent, bird or insect entry.
- E1-4 Exterior/Garage:
The brick window ledges on the south side of the building have some minor damage that should be repaired. The concrete window ledges at the north side of the building are deteriorated, missing and require repairs by a mason or concrete specialist.
- E1-5 Exterior/Garage:
An opening is present on the north side of building in alley where pipes pass through a window and should be sealed to prevent potential rodent entry into the basement. Costs are minimal.
- E1-6 Exterior/Garage:
MDF (Medium Density Fiberboard) has been used as exterior trim around the south entrance door and is NOT an exterior rated material as it is sensitive to moisture and has already become damaged. Have this trim replaced with an approved exterior material. Repair costs likely around $500.
- E1-7 Exterior/Garage:
The doorway framing & plywood wall paneling & framing at the SW corner of the building are moisture damaged and should be completely replaced. Openings are present allowing rodents to enter the building. Repair costs are estimated around $2,500.
- E1-8 Exterior/Garage:
The entrance door at the NE corner of the building is moisture damaged & delaminating requiring replacement. Either have this door replaced with a new door assembly or wall off this opening with proper siding materials. Door replacement would be around $1,500 and walling off this opening would be around the same.
- E1-9 Exterior/Garage:
The SE corner entrance door has a missing glass panel and has a plexiglass insert instead that can be broken into easily. I recommend having this door completely replaced or a new glass panel installed. Glass panel replacement is included in window replacement quote.
- E1-10 Exterior/Garage:
The concrete chimney on the west side of the building has been abandoned, was once used as an exhaust chase for a fossil fuel steam or water boiler and is no longer utilized. Several cracks are present in this chimney on the exterior and inside the building at all intervals. Although this chimney is not in use, these cracks are recommended to be patched and sealed. The top of the chimney is missing a rain cap and open to rain water entry into the chase. Since this is not in use, I recommend this chimney be capped/sealed and covered over with new roofing material membrane to prevent rain water entry. Sealing this chase will be important to prevent potential moisture or condensation from collecting under the roofing membrane once installed. Additionally, the base of chimney in basement where the flue exhaust pipes once entered should also be patched and sealed and the ash dump door is missing and should be re-installed.
- E1-12 Exterior/Garage:
The wood frame at the loading bay overhead door is damaged on the east side and should be replaced. Cost is very minimal.
- SB-2 Structure and Basement:
This building concrete slab has experienced some settling in the past and is very common for a structure built in the early 1900's. The concrete slab floors are not level at the north end, south end and some other various spots and pose trip hazards. No effort seems to have been made to re-level the floors. These slabs can be removed and replaced if desired or the trip hazard areas can be ground down to create a smooth transition. Consult a concrete specialist for options & costs for repairs.
- SB-5 Structure and Basement:
Water damaged & molded sheetrock is present in the basement storage room. This damaged sheetrock should be removed and replaced and during replacement, the wall framing should be checked for mold growth and/or damage and repaired, replaced or treated accordingly.
- R-2 Roof/Attic:
Only one surface drain is present for this entire roof. No secondary drain is present and is highly recommended to be installed in the event of an issue with the primary drain. When this roof is replaced, a secondary (back-up) drain should be installed. The installation of a back-up drain has been included in the roof replacement quote.
- R-3 Roof/Attic:
An exhaust fan is present at the south side of the building on the external wall for the basement storage room. This room has been created for the storage of flammable materials and this fan is only controlled by the toggle switch for the light fixture inside. The problem here is the fan/light switch appears to be defective and won't stay on and requires tape to keep the switch on. I recommend replacing this switch for the light fixture and recommend an electrician install a separate switch & timer for the exhaust fan so the fan can be operated independently. Although no flammable materials are no longer present in this room, lots of moisture is present due to seasonal water entry, water leaks, etc and the exhaust fan should be run for periodic durations throughout the day to reduce the collection of moisture in this room. Cost to install such a timer switch would be under $500.
- P-1 Plumbing:
A few minor water leaks along with rust & corrosion were noted in the basement and should be repaired by a qualified plumber. Estimated costs for repairs are probably around $1,500.
- P-2 Plumbing:
The galvanized steel supply pipe in this building looks to be at the end of its useful service life. Poor functional flow and lots of rusty water were noted operating fixtures. Roughly 90% of this building's plumbing appears to be galvanized steel pipe. Hire a licensed plumbing contractor to further evaluate and replace this supply pipe. Replacement of the remaining steel piping may be around $4,000.
- P-5 Plumbing:
The expansion tank at the water heater appears to be water logged - this did not sound hollow or empty when tapped on. This expansion tank should be repaired or replaced as recommended by a plumber to insure it is performing as intended.
- P-6 Plumbing:
Install listed seismic straps to support the water heater in the event of an earthquake; none were noted during inspection. Two straps should be located on the water heater: one on upper 1/3rd of tank and one at the lower 1/3rd.
- P-8 Plumbing:
The hose bib on the south side of the building has been completely disconnected and is no longer functional. This should either be replaced & hooked up or removed and wall opening patched.
- HCRS-2 Heating, Cooling and Refrigeration Systems:
This unit was not operational during inspection. The pilot gas line was disconnected and a sensor was disconnected from the gas valve assembly. An HVAC technician is needed to evaluate and repair this unit.
- HCRS-3 Heating, Cooling and Refrigeration Systems:
This heater unit was not operational during inspection as the pilot wouldn't light after the thermostat was tuned up. An HVAC technician is needed to evaluate and repair this unit.
- HCRS-5 Heating, Cooling and Refrigeration Systems:
This heater unit was not operational during inspection as the gas was shut off to the unit. An HVAC technician is needed to evaluate and repair this unit.
- HCRS-6 Heating, Cooling and Refrigeration Systems:
This heater unit was not operational during inspection as the pilot wouldn't light after the thermostat was tuned up. An HVAC technician is needed to evaluate and repair this unit.
- HCRS-7 Heating, Cooling and Refrigeration Systems:
This heater unit won't respond to thermostat at all, not even the fan. The gas is shut off to it as well. An HVAC technician is needed to evaluate and repair this unit.
- HCRS-11 Heating, Cooling and Refrigeration Systems:
Some of the exhaust flue vent dimensions are larger than the new output vents off some of the newer gas units and should be replaced with the proper sized flue pipe. These pipes that pass through the roof will be replaced by the roofing company during roof replacement and should be included in the estimate.
- E-2 Electrical:
Old and fraying insulation was noted on the electric service conductors on the north end of building. Additionally, one conductor is rubbing against the building mounted tension bracket and can eventually rub through the insulation. This is a safety hazard that should be further evaluated and repaired by a licensed electrician.
- E-15 Electrical:
One opening was noted in the panel. This can allow unintended access to the wiring inside this panel and can be a safety hazard. Cover all openings in the dead front cover.
- E-18 Electrical:
The electrical conduit is disconnected at the NW corner of the main floor against one of the inner support posts. Additionally, a missing junction box cover and damaged/bent conduit is present at the upstairs level next to the south wall. These defects should be repaired by an electrician.
- E-19 Electrical:
Reverse polarity was noted at one electrical receptacle in the upstairs center office, one receptacle in the first floor SW office, one receptacle in the first floor NW corner storage room & one at the first floor east wall. This is when the hot and the neutral have been wired backwards. This is a safety issue that should be corrected by a licensed electrician.
- E-20 Electrical:
One receptacle is not functional and does not appear to have power at the SW corner office on first floor and another outlet in this room is missing the cover plate.
- E-23 Electrical:
3 additional extinguishers are present on the main floor at the west wall and are quite old. These are no longer reliable and should be completely removed.
- I-3 Interior:
The fir hardwood floors on the second floor are moisture damaged in a few places. See at the south east area and at the SW area near stairwell. Have a hardwood flooring contractor replace the damaged flooring here. Costs are expected to be around $1,500.
- I-4 Interior:
Some sections of the ceiling tiles in the main floor offices are loose and hanging down. These should be re-secured to the ceiling to prevent them from completely falling off. Costs for repair are minimal.
- I-6 Interior:
No hand railing is present for the basement stairwells. A graspable handrail is needed at the stairs for safety. All hand rails should extend the length of the stairs and have returns that terminate into the wall. Hire a qualified general contractor to install hand railings.
- I-7 Interior:
The guardrail for the basement & interior stairs does not meet modern safety standards. Guardrails should have openings no larger than 4 inches, should be 36 inches tall and be adequately stiff to withstand a falling adult. Hire a contractor to repair and bring guardrail up to modern standards for improved safety. Cost for installation of guard rails & hand rails should be around $3000.
- I-9 Interior:
Four (4) cracked/broken panes of glass were noted on the first level east side of building. Another 14 were located on the north side. This requires glazing/window replacement to repair. Additionally, several of the glazing strips are damaged, loose or missing and need repaired or replaced.
- I-10 Interior:
Most of the window seals were noted to have failed in the double pane glazing. This has resulted in fogging between the panes of glass that cannot be cleaned without glazing replacement. Hire a glass replacement company to further evaluate and replace all windows with lost seals.
- I-12 Interior:
The window at the south side above the south entrance door has deteriorated and missing glazing along with several windows on the north side of the building. Glazing material is what holds the panes of glass in the window frame. Have a contractor make repairs here. Costs for miscellaneous glazing repairs might be around $1,500.
- I-13 Interior:
Some of the interior window sills on the east side of main floor are comprised of MDF (medium density fiber) board and are water damaged. This is never a good material to use for window sills, especially ones that are single pane metal frame as they will condensate. This condensation gets absorbed into the material and causes quick deterioration as MDF is sensitive to moisture. Have these sills replaced with a real wood product. Costs for repairs should be minimal.
- I-14 Interior:
No sealant is present at the bottom of the window frames to sill connections on the exterior and allows wind-driven rain to enter the structure. A proper sealant is needed at the window frames to prevent this. Additionally, the mullion (vertical portion between windows) are loose in many areas and need to be re-secured. Estimated repair costs should be around $2,000.
- WMFB-1 Women's Main Floor Bathroom:
An operable window or bath fan is recommended to provide ventilation to this bathroom - no fan or operable window was noted and one is required. Hire a qualified contractor make this window functional.
- WUB-1 Women's Upstairs Bathroom:
The single sink & faucets in this bathroom are very rusted & corroded. Water is currently shut off to this fixture as it should be replaced.
- WUB-3 Women's Upstairs Bathroom:
One toilet in this bathroom has a broken flush handle and the water supply is turned off to it. I suspect the tank water ran continuously. I recommend replacing this toilet.
- MMFB-1 Men's Main Floor Bathroom:
An operable window or bath fan is recommended to provide ventilation to this bathroom - no fan or operable window was noted and one is required. Hire a qualified contractor make this window functional.
- MUB-2 Men's Upstairs Bathroom:
A broken flush handle and cracked tank lid was noted on the bathroom toilet indicating this needs to be replaced for reliable performance.
Recommended Maintenance Items
- P-7 Plumbing:
Periodic maintenance is recommended for your water heater.
In general, most home owners never do any preventative maintenance to their hot water heaters.... that is why they have such short average service lives between 8-12 years. Generally, the most important maintenance is regular draining of the tank to eliminate sludge build-up at the bottom of the tank. There is also a sacrificial anode that needs to be periodically replaced to reduce corrosion inside the tank, although some brands state they never need to be replaced and are maintenance free.
Tank was operating at time of inspection. Cost to have maintenance done on this tank would be around $300.
- HCRS-4 Heating, Cooling and Refrigeration Systems:
This Reznor gas furnace works great but hasn't been serviced since 2017. Recommend a cleaning & service.
- HCRS-8 Heating, Cooling and Refrigeration Systems:
This Reznor gas furnace works great but hasn't been serviced since 2017. Recommend a cleaning & service.
- HCRS-9 Heating, Cooling and Refrigeration Systems:
This Reznor gas furnace works great but hasn't been serviced since 2017. Recommend a cleaning & service.
- HCRS-12 Heating, Cooling and Refrigeration Systems:
Some of the gas heater flue exhaust vents are rusted at the roof but are not damaged yet. Have these vents cleaned up and painted for protection against future damage. New flashing collars will be needed at these vent pipes when the roof is replaced and the roofing company will likely take care of painting these vents and should be included in the roof replacement estimate.
Improves
- SB-3 Structure and Basement:
A recessed debris pit is present on the main floor in the slab and is currently covered with a plywood cover. This plywood cover will not bear the weight of a fork lift and a metal grate is recommended to be installed instead.
- SB-4 Structure and Basement:
The 7x13 & 6x7 inner beams are supported by metal hangers but no bolts were used to positively connect the beam ends to the hangers and are recommended to be installed for improved seismic proofing. Additionally, these beams are sitting atop the poured concrete exterior walls on both the east & west sides and have no brackets for positive connections. The main support beams also do not have positive connections to the building. I recommend having a contractor who specializes in seismic retro-fitting to evaluate this building and improve its seismic stability. A cost estimate from Seismic Northwest came in at $17,500.
- I-15 Interior:
The metal-frames of the windows on the first floor of the north side of building are rusted out & deteriorated. It would be recommended to eventually have these entire window & frame assemblies replaced. Replacement costs for these windows would be around $3,000 per window.
Due Diligences
- P-3 Plumbing:
Due to the age of the building and type of the waste lines, a sewer scope is recommended to further evaluate the sewer line. Repairs can be very costly if problems exist.
A few recommendations are:
Seattle Sewer Inspections 206-335-2315
Hydro Physics 866-775-8445
Sound Sewer Inspection 206-619-9990
- HCRS-13 Heating, Cooling and Refrigeration Systems:
An old, abandoned boiler piping system is present in the basement of this building and the insulation on these pipes may contain asbestos. Cohesive asbestos identification and all asbestos testing is beyond the scope of this inspection. If removal of this material is desired, I recommend testing this material prior to removing. Once asbestos becomes friable or air borne it becomes a safety hazard. As long as this material is not disturbed or is encapsulated, it should not pose a health risk, but it could pose a future disposal liability. Prior to any remodeling, it is recommended that you have a thorough lead and asbestos evaluation by a certified specialist and remediate all contaminates as recommended. Old buildings often contain lead and asbestos in an assortment of building materials.
- I-2 Interior:
The old vinyl flooring in this building may contain asbestos. Cohesive asbestos identification and all asbestos testing is beyond the scope of this inspection. If removal of this flooring is desired, I recommend testing this material prior to removing. Once asbestos becomes friable or air borne it becomes a safety hazard. As long as these tiles are not disturbed or are encapsulated, they should not pose a health risk, but they could pose a future disposal liability. Prior to any remodeling, it is recommended that you have a thorough lead and asbestos evaluation by a certified specialist and remediate all contaminates as recommended. Old buildings often contain lead and asbestos in an assortment of building materials.
Notes
- E1-11 Exterior/Garage:
The overhead loading bay door is dented and appears to be just cosmetic as it doesn't affect the function of the door at this time.
- SB-1 Structure and Basement:
Typical cracks were noted in the foundation of this building, especially for being nearly 100 years old. No repair appears needed at this time. Minor settlement and shrinkage cracks are common in poured concrete and do not require repair as long as they do not continue to grow. The best way to prevent on-going settlement is by controlling roof runoff and site drainage to promote dry soils around the foundation; wet soils do not bear weight well.
- SB-6 Structure and Basement:
Small active leaks were noted in the basement - see water staining and water seepage at cracks & foundation penetrations. This is an unfinished basement so this is not a significant issue and is typical for an old building. Today's basements are sealed on the outside with concrete sealer over the foundation or a water-proofing fabric applied which will divert water into a footing drain system at the base of the foundation; old basements usually have none of these water-proofing systems installed. Some old basements do stay dry - typically the result of a good site and good soil drainage around the building. An attempt can be made to patch & seal these areas where water is entering depending on your need for this space. Consult a water-proofing specialist.
- R-4 Roof/Attic:
A dual directional fan is present at the upper floor. This fan can be used to bring in fresh air or be reversed to exhaust air from the building. This fan is operational but runs very slow and doesn't move much air.
- P-4 Plumbing:
This water heater is nearing the end of its useful service life at 11 years old.
The average life of these water heaters is 8-12 years. Budget to replace this water heater at any time. Cost to replace this water heater, expansion tank and installation of seismic straps would be around $1,700.
- P-9 Plumbing:
A surface drain is present at the basement and is covered with a very heavy gage metal plate. It is unsure where this surface drain is routed to and any blueprints for the building should be obtained and researched. The main roof drain appears to be connected to this surface drain as well and the drain pit likely needs cleaned out periodically free from debris.
- HCRS-1 Heating, Cooling and Refrigeration Systems:
Electric heater was tested and operational at the time of inspection. It was relatively clean.
- HCRS-10 Heating, Cooling and Refrigeration Systems:
Heaters 2 thru 9 repairs & maintenance costs can not be determined and can vary greatly depending on what needs repaired & what needs replaced. Consult an HVAC company on initial evaluation costs ($1,500) and get quotes for units that need repairs and ones that need replaced. Replacement units cost around $2,200 each + labor.
- HCRS-14 Heating, Cooling and Refrigeration Systems:
Old, boiler fed heaters are present on the main floor & upstairs and should be removed as desired along with its piping.
- HCRS-15 Heating, Cooling and Refrigeration Systems:
An old window air conditioner is present at the main floor office and was not tested.
- E-3 Electrical:
Two of the three 200 amp main breakers were found switched off at the south end service entrance disconnect. No defects or thermal anomalies were observed but two of the disconnected were not on.
- E-7 Electrical:
Not all of the electrical panels were inspected in this building. Some of them have power completely turned off as they are no longer feeding equipment that was once present.
- E-8 Electrical:
No significant deficiencies were observed inside the main panel and all breaker wiring appeared neat & professional.
- E-9 Electrical:
No significant deficiencies were observed inside panel AA and all breaker wiring appeared neat & professional.
- E-10 Electrical:
No significant deficiencies were observed inside panel A3 and all breaker wiring appeared neat & professional.
- E-11 Electrical:
No significant deficiencies were observed inside panel B and all breaker wiring appeared neat & professional.
- E-12 Electrical:
No significant deficiencies were observed inside panel C and all breaker wiring appeared neat & professional.
- E-13 Electrical:
No significant deficiencies were observed inside panel E and all breaker wiring appeared neat & professional.
- E-14 Electrical:
No significant deficiencies were observed inside unlabeled panel and all breaker wiring appeared neat & professional.
- E-16 Electrical:
This panel cover was locked at time of inspection and could not be entered for inspection.
- E-17 Electrical:
No significant deficiencies were observed inside panel G and all breaker wiring appeared neat & professional.
- E-21 Electrical:
E-2 to E-20 miscellaneous electrical repairs estimated around $2,500.
- E-22 Electrical:
Fire extinguishers are present throughout the building and are still in calibration.
- I-1 Interior:
Carpets appear to be in rough condition (wrinkled & damaged) and should be replaced as desired. Costs to replace would likely be around $2,000.
- I-5 Interior:
The interior side of the formed concrete walls have lots of efflorescence (white powder, salts from the cement) and lots of peeling paint due to water intrusion. These walls should be scraped, primed & repainted as desired after exterior wall cracks & openings have been sealed and sealant applied around windows. Consult with an interior painting company for associated costs.
- I-11 Interior:
The window replacements have been estimated by Four Seasons and cost estimate came in at $16,000.
- WUB-2 Women's Upstairs Bathroom:
The trough sink is also very corroded but still functional. The faucets are old, some dripping but are still functional as well. Heavy rusted water came out of these faucets when tested which is common with steel piping. I recommend updating this sink & faucets as desired.
- MUB-1 Men's Upstairs Bathroom:
No sink is located inside the bathroom, sink is located outside instead and presents a sanitary issue. Sinks should be located inside the confines of the bathroom.
- MUB-3 Men's Upstairs Bathroom:
The two other stalls are missing toilets altogether.
Commercial Report
Grounds
Drainage and Lot Location
Driveways/Walkways/Flatwork/Parking
Exterior Stairs
Fences
Landscape Irrigation
Roof/Attic
Building Roof Materials
Skylights
Gutters, Downspouts & Roof Drainage
Attic Access
Roof Framing and Sheathing
Attic Insulation
Building Ventilation
Plumbing
Water Service Supply
Distribution Pipe
Waste Pipe and Discharge
Water Heater
Exterior Hose Bibs
Sump Pumps and Drains
Plumbing Fixtures
Heating, Cooling and Refrigeration Systems
Building Heat Source 1
Building Heat Source 2
Building Heat Source 3
Building Heat Source 4
Building Heat Source 5
Building Heat Source 6
Building Heat Source 7
Building Heat Source 8
Building Heat Source 9
Air Curtain
Exhaust Flue Systems
Additional Heat Sources
Miscellaneous
General Comments
Building Characteristics / Conditions
Style of Building(s): Concrete formed
Type of Building : Commercial
Approximate Square Footage: 19,376
Approximate Year of Original Construction: 1927
Attending the Inspection: Buyer and Seller
Occupancy: Unoccupied- long term
Weather during the inspection: Clear on 6/14, Cloudy on 6/15
Approximate temperature during the inspection: Below 65[F]
Ground/Soil surface conditions: Damp
Building Faces: East
Grounds
Drainage and Lot Location
Clearance to Grade: Standard
Downspout Discharge: Within the confines of the building interior
Lot Description: Minor Slope
Surface Drains: Not present
Surface Drain Locations: None noted
The SW corner doorway to the building sits lower than the walkway and has no provisions for controlling rain water. A surface drain track should be installed or a shallow swale that can capture rain water and divert away from building entryway. Installation of a surface drain would be included in the concrete flatwork estimate.
Driveways/Walkways/Flatwork/Parking
Driveway: N/A
Curb: N/A
Walkways: Concrete
Tire Stops: N/A
Parking Stalls: N/A
Approximately 345 sq ft of concrete driveway & sidewalk are cracked, damaged & creating trip hazards requiring replacement on the south side of building.
It is unsure whether this is part of this property or it is the responsibility of the city. If repairs fall on the responsibility of the property owner, I expect costs to be around $4,500.
Exterior Stairs
Standard
A framed cover is present over these stairs & entryway but is missing the roof paneling that will make this weather resistant. The cost to install some corrugated material here would be minimal, around $500.
Fences
Fencing Material: Chain-link
Approximate Length: 14 Linear feet
Landscape Irrigation
Not Present
Exterior/Garage
Siding and Trim
Trim Material: Metal, Brick
Siding Material: Poured Concrete Walls, Fiber-cement panels, Plywood
Several vertical & horizontal cracks are present on the exterior & interior of this nearly 100 year old concrete building. Cracks are common in concrete and these once appear to have been patched or sealed but have since separated and opened up again, most likely from expansion & contraction. Many other areas of cracking are present around the window openings where some have been patched and are still good patches but many other areas that have openings need to be addressed/repaired. Some areas of exposed rebar are present and need to be patched to protect the rebar from oxidation & rust. Several small spots of concrete are spalling as well, this indicates that water is being absorbed into the concrete and is causing it to peel and flake apart. If this condition continues unchecked, the damage just continues to progress further affecting a larger area.
Hire a licensed contractor who specializes in concrete to further evaluate this condition and repair. A quote from AVE Concrete & Flatwork came in at $35,000 for all exterior repairs and $25,000 for interior repairs totaling $60,000 + tax.
Plywood is being used as an exterior siding material and is not preferred as it decays quickly due to exterior exposure. The panel next to the south entrance door is rotting at the bottom end. The plywood panels on the NE & SE corners of the building above doorways are also deteriorated, bowed and no longer water-proof. These panels should be replaced with a more superior exterior material and appropriately sealed & painted. Replacement of these panels with a proper siding material would be around $1,500.
Several wall penetrations are present in the exterior building wall that are not properly sealed. See where gas line & electrical service conduits penetrate the concrete walls. Have an approved exterior sealant applied to seal these penetrations from water, rodent, bird or insect entry.
Eaves
None
Exterior Doors
Metal, Solid core
MDF (Medium Density Fiberboard) has been used as exterior trim around the south entrance door and is NOT an exterior rated material as it is sensitive to moisture and has already become damaged. Have this trim replaced with an approved exterior material. Repair costs likely around $500.
The entrance door at the NE corner of the building is moisture damaged & delaminating requiring replacement. Either have this door replaced with a new door assembly or wall off this opening with proper siding materials. Door replacement would be around $1,500 and walling off this opening would be around the same.
Awnings
None noted
Chimneys
Present
Chimney Material: Concrete
Chimney Flue Liners: Not visible, Likely no liner present
The concrete chimney on the west side of the building has been abandoned, was once used as an exhaust chase for a fossil fuel steam or water boiler and is no longer utilized. Several cracks are present in this chimney on the exterior and inside the building at all intervals. Although this chimney is not in use, these cracks are recommended to be patched and sealed. The top of the chimney is missing a rain cap and open to rain water entry into the chase. Since this is not in use, I recommend this chimney be capped/sealed and covered over with new roofing material membrane to prevent rain water entry. Sealing this chase will be important to prevent potential moisture or condensation from collecting under the roofing membrane once installed. Additionally, the base of chimney in basement where the flue exhaust pipes once entered should also be patched and sealed and the ash dump door is missing and should be re-installed.
Loading Bay
Automatic Garage Opener: Present
Garage Door Type: Metal, Roll-up
The overhead loading bay door is dented and appears to be just cosmetic as it doesn't affect the function of the door at this time.
Structure and Basement
Building Foundation
% of Foundation Not Visible: 20%
Evidence of Seismic Protection: None visible
Building Configuration: Basement, Slab on grade
Foundation Description: Poured concrete
Typical cracks were noted in the foundation of this building, especially for being nearly 100 years old. No repair appears needed at this time. Minor settlement and shrinkage cracks are common in poured concrete and do not require repair as long as they do not continue to grow. The best way to prevent on-going settlement is by controlling roof runoff and site drainage to promote dry soils around the foundation; wet soils do not bear weight well.
This building concrete slab has experienced some settling in the past and is very common for a structure built in the early 1900's. The concrete slab floors are not level at the north end, south end and some other various spots and pose trip hazards. No effort seems to have been made to re-level the floors. These slabs can be removed and replaced if desired or the trip hazard areas can be ground down to create a smooth transition. Consult a concrete specialist for options & costs for repairs.
Floor, Wall and Ceiling Framing
Exterior Wall Framing: 16x26 concrete support columns, 8" poured concrete
Wall Insulation: None present
Wall Sheathing: Not applicable
2nd Story Floor Framing: (2) 7x26 main center support beams, 7x13 inner beams 4' on center, 9x9 Interior Wood Columns at 28' spans
2nd Story Sub-Floor Material: 2x6 Shiplap
Roof Framing: 9x19 main center support beams, 6x7 inner beams 4' on center, 2x6 Shiplap
The 7x13 & 6x7 inner beams are supported by metal hangers but no bolts were used to positively connect the beam ends to the hangers and are recommended to be installed for improved seismic proofing. Additionally, these beams are sitting atop the poured concrete exterior walls on both the east & west sides and have no brackets for positive connections. The main support beams also do not have positive connections to the building. I recommend having a contractor who specializes in seismic retro-fitting to evaluate this building and improve its seismic stability. A cost estimate from Seismic Northwest came in at $17,500.
Basement
Full
Basement Moisture
Some signs
Small active leaks were noted in the basement - see water staining and water seepage at cracks & foundation penetrations. This is an unfinished basement so this is not a significant issue and is typical for an old building. Today's basements are sealed on the outside with concrete sealer over the foundation or a water-proofing fabric applied which will divert water into a footing drain system at the base of the foundation; old basements usually have none of these water-proofing systems installed. Some old basements do stay dry - typically the result of a good site and good soil drainage around the building. An attempt can be made to patch & seal these areas where water is entering depending on your need for this space. Consult a water-proofing specialist.
Roof/Attic
Building Roof Materials
Method of Roof Inspection: Walked on roof
Roof Style: Low slope
Roof Materials: Torch-down
Layers: Unknown
Approximate SF of Roof Surface: 8,436 Sq Ft
Parapet Wall: Present, 3' high
Roof Access Method: Scuttle on north end of building
The roofing material on this building is a torch down or modified bitumen membrane. The service life of these roofs can vary depending on the quality of the membrane and the quality of the installation, including how well the roof is sloped to drain. Torch down roofs often have roughly 10 years of reliable service life beyond which regular repairs are often needed. With on-going maintenance these roofs can be made to last as long as 25-30 years. This roof is 35+ years old and well beyond its expected life span. Several red flags were noted during inspection that indicate vulnerable and potentially failing areas of the roof. Hire a licensed roofing contractor to replace this roof as recommended. If repairs are made and the roof is kept in service funds should be reserved for replacement at any time. Examples of observations noted during inspection include:
- Welded seam sealant is missing, losing its bond and peeling off easily.
- Some of the welded seams have the membrane beginning to peel up & separate.
- Deterioration & break down of the membrane itself is occurring due to UV sun exposure indicating this membrane needs replaced. The silver reflective coating that once protected this roof has since worn away and no longer is providing any protection.
- Seams are separating at most of the roof penetrations & flashings.
- A few active leaks are present around the NW corner chimney.
A roof replacement estimate has been provided by Top Roof Care of $85,000 and includes the installation of new 1/2" CDX plywood priced at $21,600 (which may not be needed) and roof replaced with WeatherBond TPO membrane.
Skylights
None noted
Gutters, Downspouts & Roof Drainage
Internal surface drain, Cast iron
Only one surface drain is present for this entire roof. No secondary drain is present and is highly recommended to be installed in the event of an issue with the primary drain. When this roof is replaced, a secondary (back-up) drain should be installed. The installation of a back-up drain has been included in the roof replacement quote.
Attic Access
No attic present
Roof Framing and Sheathing
Rafters: Plank and beam
Attic Insulation
Insulation Type: N/A
Building Ventilation
Number of Power Ventilators: 2
Ventilator Manufacturer: Nutone, Unknown
Attic Ventilation Method: N/A
An exhaust fan is present at the south side of the building on the external wall for the basement storage room. This room has been created for the storage of flammable materials and this fan is only controlled by the toggle switch for the light fixture inside. The problem here is the fan/light switch appears to be defective and won't stay on and requires tape to keep the switch on. I recommend replacing this switch for the light fixture and recommend an electrician install a separate switch & timer for the exhaust fan so the fan can be operated independently. Although no flammable materials are no longer present in this room, lots of moisture is present due to seasonal water entry, water leaks, etc and the exhaust fan should be run for periodic durations throughout the day to reduce the collection of moisture in this room. Cost to install such a timer switch would be under $500.
Plumbing
Water Service Supply
Pipe Material: Galvanized
Well or Public Supply: Public
Water Pressure: Unable to test water pressure
Pressure Reducing Valve: None noted
Main Water Shut-off Location: Basement
Distribution Pipe
Supply Pipe Materials: Galvanized steel, PEX
Functional Flow: Poor
The galvanized steel supply pipe in this building looks to be at the end of its useful service life. Poor functional flow and lots of rusty water were noted operating fixtures. Roughly 90% of this building's plumbing appears to be galvanized steel pipe. Hire a licensed plumbing contractor to further evaluate and replace this supply pipe. Replacement of the remaining steel piping may be around $4,000.
Waste Pipe and Discharge
Discharge Type: Public sewer
Waste and Vent Pipe Materials: Cast Iron, Galvanized steel
Due to the age of the building and type of the waste lines, a sewer scope is recommended to further evaluate the sewer line. Repairs can be very costly if problems exist.
A few recommendations are:
Seattle Sewer Inspections 206-335-2315
Hydro Physics 866-775-8445
Sound Sewer Inspection 206-619-9990
Water Heater
System Type: Tank
Located in: Main floor
Manufacturer: Bradford-White
Size: 50 gal
Age: Built in May 2012
Energy Source: Electricity
Last Service Date: None noted
Temperature Pressure Relief Value: Present - Not Tested
This water heater is nearing the end of its useful service life at 11 years old.
The average life of these water heaters is 8-12 years. Budget to replace this water heater at any time. Cost to replace this water heater, expansion tank and installation of seismic straps would be around $1,700.
Install listed seismic straps to support the water heater in the event of an earthquake; none were noted during inspection. Two straps should be located on the water heater: one on upper 1/3rd of tank and one at the lower 1/3rd.
Periodic maintenance is recommended for your water heater.
In general, most home owners never do any preventative maintenance to their hot water heaters.... that is why they have such short average service lives between 8-12 years. Generally, the most important maintenance is regular draining of the tank to eliminate sludge build-up at the bottom of the tank. There is also a sacrificial anode that needs to be periodically replaced to reduce corrosion inside the tank, although some brands state they never need to be replaced and are maintenance free.
Tank was operating at time of inspection. Cost to have maintenance done on this tank would be around $300.
Exterior Hose Bibs
Not operating
Sump Pumps and Drains
Floor Drain: Present
Location(s): Basement
Sump Pump: Not Present
A surface drain is present at the basement and is covered with a very heavy gage metal plate. It is unsure where this surface drain is routed to and any blueprints for the building should be obtained and researched. The main roof drain appears to be connected to this surface drain as well and the drain pit likely needs cleaned out periodically free from debris.
Plumbing Fixtures
Tested
Heating, Cooling and Refrigeration Systems
Building Heat Source 1
Energy Source: Electricity
Heating Method: Ceiling mounted electric heater
Location: Basement
Manufacturer: Dimplex
Capacity: 5000 watts
Age: Unable to determine
Last Service Record: None
Building Heat Source 2
Energy Source: Natural gas
Heating Method: Ceiling mounted gas heater
Location: Upstairs NE corner
Manufacturer: Hastings
Capacity: 200k BTU
Age: Unable to determine, Built sometime in the 70's or early 80's
Last Service Record: None
Building Heat Source 3
Energy Source: Natural gas
Heating Method: Ceiling mounted gas heater
Location: Upstairs SE corner
Manufacturer: Hastings
Capacity: 200k BTU
Age: Unable to determine, Built sometime in the 70's or early 80's
Last Service Record: None
Building Heat Source 4
Energy Source: Natural gas
Heating Method: Ceiling mounted gas heater
Location: Upstairs SW corner
Manufacturer: Reznor
Capacity: 200k BTU
Age: Built in Feb. 2013
Last Service Record: 2017
Building Heat Source 5
Energy Source: Natural gas
Heating Method: Ceiling mounted gas heater
Location: Upstairs NW corner
Manufacturer: Hastings
Capacity: 200k BTU
Age: Unable to determine, Built sometime in the 70's or early 80's
Last Service Record: None
Building Heat Source 6
Energy Source: Natural gas
Heating Method: Ceiling mounted gas heater
Location: Main floor NE corner
Manufacturer: Hastings
Capacity: 200k BTU
Age: Unable to determine, Built sometime in the 70's or early 80's
Last Service Record: None
Building Heat Source 7
Energy Source: Natural gas
Heating Method: Ceiling mounted gas heater
Location: Main floor SE corner
Manufacturer: Hastings
Capacity: 200k BTU
Age: Unable to determine, Built sometime in the 70's or early 80's
Last Service Record: None
Building Heat Source 8
Energy Source: Natural gas
Heating Method: Ceiling mounted gas heater
Location: Main floor SW corner
Manufacturer: Reznor
Capacity: 150k BTU
Age: Built in July 2014
Last Service Record: 2017
Building Heat Source 9
Energy Source: Natural gas
Heating Method: Ceiling mounted gas heater
Location: Main floor NW corner
Manufacturer: Reznor
Capacity: 150k BTU
Age: Built in July 2014
Last Service Record: 2017
Heaters 2 thru 9 repairs & maintenance costs can not be determined and can vary greatly depending on what needs repaired & what needs replaced. Consult an HVAC company on initial evaluation costs ($1,500) and get quotes for units that need repairs and ones that need replaced. Replacement units cost around $2,200 each + labor.
Air Curtain
None present
Exhaust Flue Systems
System Materials: Type B Vent
Some of the exhaust flue vent dimensions are larger than the new output vents off some of the newer gas units and should be replaced with the proper sized flue pipe. These pipes that pass through the roof will be replaced by the roofing company during roof replacement and should be included in the estimate.
Some of the gas heater flue exhaust vents are rusted at the roof but are not damaged yet. Have these vents cleaned up and painted for protection against future damage. New flashing collars will be needed at these vent pipes when the roof is replaced and the roofing company will likely take care of painting these vents and should be included in the roof replacement estimate.
Additional Heat Sources
None noted
Miscellaneous
An old, abandoned boiler piping system is present in the basement of this building and the insulation on these pipes may contain asbestos. Cohesive asbestos identification and all asbestos testing is beyond the scope of this inspection. If removal of this material is desired, I recommend testing this material prior to removing. Once asbestos becomes friable or air borne it becomes a safety hazard. As long as this material is not disturbed or is encapsulated, it should not pose a health risk, but it could pose a future disposal liability. Prior to any remodeling, it is recommended that you have a thorough lead and asbestos evaluation by a certified specialist and remediate all contaminates as recommended. Old buildings often contain lead and asbestos in an assortment of building materials.
Electrical
Service Entrance
Volts: 3 Phase, 240 volt
Service Drop: Overhead
Transformer Location: Power pole on S Weller St for first floor, Power pole on 12th Ave S for second floor
Meter Base Amperage: 400
Service Entrance (SE) conductor Size: Unable to determine
Electric Service Amperage: 800 amps at south end
Old and fraying insulation was noted on the electric service conductors on the north end of building. Additionally, one conductor is rubbing against the building mounted tension bracket and can eventually rub through the insulation. This is a safety hazard that should be further evaluated and repaired by a licensed electrician.
Not all of the electrical panels were inspected in this building. Some of them have power completely turned off as they are no longer feeding equipment that was once present.
Panel A
Panel location:
Single Phase Main Panel
Volts: 120/240
Panel location: Upstairs north end near stairwell
Main Conductor: Copper, 2/0, 200 amps
Panel Amperage: 200
Panel Brand: Square D
Panel AA
Volts: 120/240
Panel location: Main floor north wall
Main Conductor: Copper, 1/0, 175 amps
Panel Amperage: 150
Panel Brand: Square D
Panel A3
Volts: 3 Phase
Panel location: Main floor center post
Main Conductor: Copper, 3/0, 225 amps
Panel Amperage: 225
Panel Brand: Square D
Panel B
Volts: 120/240
Panel location: Main floor north wall
Main Conductor: Copper, #2, 125 amps
Panel Amperage: 100
Panel Brand: Square D
Panel C
Volts: 120/240
Panel location: Upstairs north end near stairwell
Main Conductor: Copper, #4, 100 amps
Panel Amperage: 100
Panel Brand: Square D
Panel E
Volts: 120/240
Panel location: Upstairs north end near stairwell
Main Conductor: Copper, #4, 100 amps
Panel Amperage: 100
Panel Brand: Square D
Unlabeled Panel 1
Volts: 3 phase
Panel location: Upstairs north end around corner from stairwell
Main Conductor: Copper, 3/0, 225 amps
Panel Amperage: 225
Panel Brand: Square D
Unlabeled Panel 2
Volts: Unknown, Likely 3 phase
Panel location: West side of main level
Panel G
Volts: 3 phase
Panel location: Main floor west wall
Main Conductor: Copper, #2, 125 amps
Panel Amperage: 125
Panel Brand: Square D
240 volt Sub Panel 1
Panel location:
240 volt Sub-Panel 2
Panel location:
Branch Wiring
Wire Material: Copper
Wiring Method: Metal Conduit, Armored BX cable
The electrical conduit is disconnected at the NW corner of the main floor against one of the inner support posts. Additionally, a missing junction box cover and damaged/bent conduit is present at the upstairs level next to the south wall. These defects should be repaired by an electrician.
Receptacles and Fixtures
Inspection Method: Random Testing
Outlets: Three wire outlets
Reverse polarity was noted at one electrical receptacle in the upstairs center office, one receptacle in the first floor SW office, one receptacle in the first floor NW corner storage room & one at the first floor east wall. This is when the hot and the neutral have been wired backwards. This is a safety issue that should be corrected by a licensed electrician.
E-2 to E-20 miscellaneous electrical repairs estimated around $2,500.
Smoke Alarms and Fire Extinguishers
Present
Extinguisher Qty: 8
Extinguisher Expiration Date: Jan. 2024
Grounding Electrode / Conductor
Present
Grounding Method: Service conduit, Water pipes
Fuel Storage and Distribution
Oil Storage
None noted
Propane Storage
None noted
Interior
Floors
Floor Materials: Concrete, Fir wood floors, Carpet, Vinly asbestos tiles
The old vinyl flooring in this building may contain asbestos. Cohesive asbestos identification and all asbestos testing is beyond the scope of this inspection. If removal of this flooring is desired, I recommend testing this material prior to removing. Once asbestos becomes friable or air borne it becomes a safety hazard. As long as these tiles are not disturbed or are encapsulated, they should not pose a health risk, but they could pose a future disposal liability. Prior to any remodeling, it is recommended that you have a thorough lead and asbestos evaluation by a certified specialist and remediate all contaminates as recommended. Old buildings often contain lead and asbestos in an assortment of building materials.
The fir hardwood floors on the second floor are moisture damaged in a few places. See at the south east area and at the SW area near stairwell. Have a hardwood flooring contractor replace the damaged flooring here. Costs are expected to be around $1,500.
Walls, Ceilings and Closets
Wall and Ceiling Materials: Drywall, Plywood, Wood paneling, Ceiling tiles
The interior side of the formed concrete walls have lots of efflorescence (white powder, salts from the cement) and lots of peeling paint due to water intrusion. These walls should be scraped, primed & repainted as desired after exterior wall cracks & openings have been sealed and sealant applied around windows. Consult with an interior painting company for associated costs.
Stairs and Railings
Non-standard
The guardrail for the basement & interior stairs does not meet modern safety standards. Guardrails should have openings no larger than 4 inches, should be 36 inches tall and be adequately stiff to withstand a falling adult. Hire a contractor to repair and bring guardrail up to modern standards for improved safety. Cost for installation of guard rails & hand rails should be around $3000.
Interior Doors
Solid Core
Windows
Window Glazing: Single pane, Double pane
Interior Window Frame: Metal
Window Styles: Casement, Fixed pane
First floor of the building has single pane non-insulated windows. The second floor has double pane insulated windows.
Four (4) cracked/broken panes of glass were noted on the first level east side of building. Another 14 were located on the north side. This requires glazing/window replacement to repair. Additionally, several of the glazing strips are damaged, loose or missing and need repaired or replaced.
The window replacements have been estimated by Four Seasons and cost estimate came in at $16,000.
The window at the south side above the south entrance door has deteriorated and missing glazing along with several windows on the north side of the building. Glazing material is what holds the panes of glass in the window frame. Have a contractor make repairs here. Costs for miscellaneous glazing repairs might be around $1,500.
Some of the interior window sills on the east side of main floor are comprised of MDF (medium density fiber) board and are water damaged. This is never a good material to use for window sills, especially ones that are single pane metal frame as they will condensate. This condensation gets absorbed into the material and causes quick deterioration as MDF is sensitive to moisture. Have these sills replaced with a real wood product. Costs for repairs should be minimal.
No sealant is present at the bottom of the window frames to sill connections on the exterior and allows wind-driven rain to enter the structure. A proper sealant is needed at the window frames to prevent this. Additionally, the mullion (vertical portion between windows) are loose in many areas and need to be re-secured. Estimated repair costs should be around $2,000.
Women's Main Floor Bathroom
Sinks and Counters
None noted
Toilet
Tested
Bathroom Ventilation
Type: None noted
An operable window or bath fan is recommended to provide ventilation to this bathroom - no fan or operable window was noted and one is required. Hire a qualified contractor make this window functional.
Women's Upstairs Bathroom
Sinks and Counters
Tested, Not tested
Toilet
Tested
Bathroom Ventilation
Type: Operable window
Men's Main Floor Bathroom
Sinks and Counters
Not noted
Toilet
Tested
Bathroom Ventilation
Type: None noted
An operable window or bath fan is recommended to provide ventilation to this bathroom - no fan or operable window was noted and one is required. Hire a qualified contractor make this window functional.
Men's Upstairs Bathroom
Sinks and Counters
None noted
No sink is located inside the bathroom, sink is located outside instead and presents a sanitary issue. Sinks should be located inside the confines of the bathroom.
Toilet
Tested
The two other stalls are missing toilets altogether.
Bathroom Ventilation
Type: Operable window
Receipt -- Commercial Report
4500 15th Ave S, Tacoma, WA 98402
Commercial Inspection | $2595.00 |
$2595.00 | |
PAID |
Livin Good Inspections
C/O Todd Livingood
12330 NE 92nd Lane, J404
Kirkland, WA 98033
(206) 251-3009
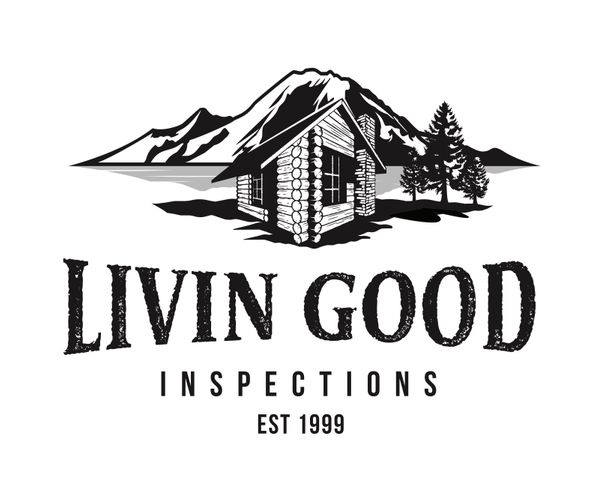