The Scope and Purpose of a Home Inspection
Purchasing property involves risk
The purpose of a home inspection is to help reduce the risk associated with the purchase of a structure by providing a professional opinion about the overall condition of the structure. A home inspection is a limited visual inspection and it cannot eliminate this risk. Some homes present more risks than others. We cannot control this, but we try to help educate you about what we don’t know during the inspection process. This is more difficult to convey in a report and one of many reasons why we recommend that you attend the inspection.
A home inspection is not an insurance policy
This report does not substitute for or serve as a warranty or guarantee of any kind. Home warranties can be purchased separately from insuring firms that provide this service.
A home inspection is visual and not destructive
The descriptions and observations in this report are based on a visual inspection of the structure. We inspect the aspects of the structure that can be viewed without dismantling, damaging or disfiguring the structure and without moving furniture and interior furnishings. Areas that are concealed, hidden or inaccessible to view are not covered by this inspection. Some systems cannot be tested during this inspection as testing risks damaging the building. For example, overflow drains on bathtubs are generally not tested because if they were found to be leaking they could damage the finishes below. Our procedures involve non-invasive investigation and non-destructive testing which will limit the scope of the inspection.
This is not an inspection for code compliance
This inspection and report are not intended for city / local code compliance. During the construction process structures are inspected for code compliance by municipal inspectors. Framing is open at this time and conditions can be fully viewed. Framing is not open during inspections of finished homes, and this limits the inspection. All houses fall out of code compliance shortly after they are built, as the codes continually change. National codes are augmented at least every three years for all of the varying disciplines. Municipalities can choose to adopt and phase in sections of the codes on their own timetables. There are generally no requirements to bring older homes into compliance unless substantial renovation is being done.
This is just our opinion
Construction techniques and standards vary. There is no one way to build a house or install a system in a house. The observations in this report are the opinions of the home inspector. Other inspectors and contractors are likely to have some differing opinions. You are welcome to seek opinions from other professionals.
The scope of this inspection
This inspection will include the following systems: exterior, roof, structure, drainage, foundation, attic, interior, plumbing, electrical and heating. The evaluation will be based on limited observations that are primarily visual and non-invasive. This inspection and report are not intended to be technically exhaustive.
Your expectations
The overall goal of a home inspection is to help ensure that your expectations are appropriate with the house you are proposing to buy. To this end we assist with discovery by showing and documenting observations during the home inspection. This should not be mistaken for a technically exhaustive inspection designed to uncover every defect with a building. Such inspections are available but they are generally cost-prohibitive to most homebuyers.
Your participation is requested
Your presence is requested during this inspection. A written report will not substitute for all the possible information that can be conveyed verbally by a shared visual observation of the conditions of the property.
How to Read This Report
Getting the Information to You
This report is designed to deliver important and technical information in a way that is easy for anyone to access and understand. If you are in a hurry, you can take a quick look at our "Summary Page” and quickly get critical information for important decision making. However, we strongly recommend that you take the time to read the full Report, which includes digital photographs, captions, diagrams, descriptions, videos and hot links to additional information.
The best way to get the layers of information that are presented in this report is to read your report online, which will allow you to expand your learning about your house. You will notice some words or series of words highlighted in blue and underlined – clicking on these will provide you with a link to additional information.
This report can also be printed on paper or to a PDF document.
Chapters and Sections
This report is divided into chapters that parcel the home into logical inspection components. Each chapter is broken into sections that relate to a specific system or component of the home. You can navigate between chapters with the click of a button on the left side margin.
Most sections will contain some descriptive information done in black font. Observation narrative, done in colored boxes, will be included if a system or component is found to be significantly deficient in some way or if we wish to provide helpful additional information about the system or the scope of our inspection. If a system or component of the home was deemed to be in satisfactory or serviceable condition, there may be no narrative observation comments in that section and it may simply say “tested,” or “inspected.”
Observation Labels
All narrative observations are colored, numbered and labeled to help you find, refer to, and understand the severity of the observation. Observation colors and labels used in this report are:
- Repair:Repair and maintenance items noted during inspection. Please note that some repair items can be expensive to correct such as re-finishing hardwood floors, but are considered simply repair items due to their cosmetic nature.
- Recommended Maintenance:These are repair items that should be considered "routine home ownership items," such as servicing the furnace, cleaning the gutters or changing the air filters in the furnace.
- Improve:Observations that are not necessarily defects, but which could be improved for safety, efficiency, or reliability reasons.
- Monitor:Items that should be watched to see if correction may be needed in the future.
- Due Diligence:Observation such as a buried oil tank that may require further investigation to determine the severity and / or urgency of repair.
- Future Project:A repair that may be deferred for some time but should be on the radar for repair or replacement in the near future.
- Efficiency:Denotes observations that are needed to make the home more energy efficient as well as to bring the home up to modern insulation standards. This category typically includes windows and insulation. Other items, such as lighting and appliances, are not inspected for their energy status.
- Note:Refers to aside information and /or any comments elaborating on descriptions of systems in the home or limitations to the home inspection.
- Description:Detailed description of various aspects of the property noted during the inspection.
Summary Page
The Summary Page is designed as a bulleted overview of all the observations noted during inspection. This helpful overview is not a substitution for reading the entire inspection report. The entire report must be read to get a complete understanding of this inspection report as the Summary Page does not include photographs or photo captions.
Summary
Repairs
- E1-9 Exterior/Garage:
The wood trim at both of the front porch pillars is moisture damaged and has been puttied, caulked & painted instead of being replaced. The wood is already damaged to point where it should be replaced.
- E1-10 Exterior/Garage:
No guardrail system has been provided for the front porch/deck. A guardrail system is required for all decks and porches more than 30" off the ground. Railings should be installed where height of porch/deck surface is 30" or greater from the surface of yard or soil.
- CS-2 Crawl Space:
Some minor ponding water is present in the center of the crawlspace collecting above & below the plastic and some muddy areas were also observed. Improvements to the crawlspace drainage system appear to be needed to prevent this. Recommend installing additional drains in key spots to capture this water and route to the sump pump reservoir.
- R-1 Roof/Attic:
The roofing material on this building is done in a three-tab presidential grade architectural composition shingle. These are often rated as 50 year roofs. In practice these roofs have not been installed that long so difficult to know how long they will last. The installation appears neat and professional but a few repair items are in need of attention right away. Inquire with the seller about any warranty information for this roof. Many professional roofing companies will offer limited workmanship warranties. Repairs needed are:
- A few ridge shingles are torn/damaged that should be replaced.
- Lifted roofing nails are present in some places pushing through top layer and should be re-sealed.
- One section of the roof decking on the east side has lifted away from the trusses and is causing raised shingles and needs to be repaired.
Have a roofing contractor or a general contractor familiar with roof repairs make these corrections.
- R-6 Roof/Attic:
Organic substances were noted in the attic on the roof framing mostly on the north facing sections of roof and some spots on the east side as well. This appears to be due to lack of ventilation at the lower roof cavity areas. The substances looked localized to these areas and not chronic to the attic. Rusty nails were also observed along with rust drip marks in the batten insulation. Mold testing and molds in general are beyond the scope of this inspection. Use sealants as desired to seal any mold-like substances and monitor this area. I recommend having a qualified contractor evaluate & install additional ventilation to remedy this issue.
- P-7 Plumbing:
The laundry room deep sink has a small leak on the drain trap line and should be repaired. Have a qualified plumber or handyman make repairs here.
- HCF-3 Heating, Cooling and Fireplaces:
The heat pump was not tested during inspection as the 240 breaker inside the sub-panel is turned off for some reason. I recommend having this heat pump evaluated and serviced to be sure it is functioning correctly.
- E-4 Electrical:
The open electrical junction boxes should be covered for improved safety at the crawlspace.
- I-1 Interior:
Some minor carpet damage is present where the upstairs hallway meets west guest bedroom as the carpet is frayed and could be from pet damage. Have this repaired as desired.
- I-3 Interior:
The upstairs laundry room door rubs and sticks at the frame and the door will not latch closed. Have this door adjusted and/or repaired to function properly.
- I-4 Interior:
The upstairs hall closet & hall bathroom closet sliding door hardware is missing at the bottom to keep doors in line and is recommended to be installed.
- I-5 Interior:
The door stop system for the home is incomplete. Some door stops are missing and I recommend systematically installing door stops to protect doors and wall finishes.
- I-6 Interior:
The two single hung windows at the kitchen garden window will not stay open and the sash springs are not functioning correctly. Repair these springs for proper operation of the windows. Please note that these windows are designed to be able to disengage the springs so that the window frames can be removed for cleaning.
- K-2 Kitchen:
A faint gas smell is present around the gas stove and could indicate a very small leak. I recommend further evaluation to be sure no leak is present. If an actual leak is discovered, have it repaired.
- UB-1 Upstairs Bathroom:
One drawer on each of the hallway bathroom sink cabinets is not operating as designed and needs adjustments or repairs.
Recommended Maintenance Items
- E1-3 Exterior/Garage:
Additional caulking is needed at wood trim, wall penetrations, windows, etc in some places on the exterior to fully seal against moisture penetration and possible damage. This is typical periodic maintenance that should be done every few years.
- E1-6 Exterior/Garage:
The exterior paint requires some localized touch up in one area of the siding above the front porch. Have the exterior paint job touched up and completed by a painter.
- E1-7 Exterior/Garage:
One of the rake board ends is splitting/cracking and should have caulking & more paint applied to protect this wood from future moisture damage.
- R-2 Roof/Attic:
Minor moss growth was noted on the roof. This is bad for the roof covering and decking as it can trap moisture on the roof and can inhibit drainage off the roof. Moss removal and prevention is recommended. Products such as Tide are not recommended as the bleach in these products can deteriorate the shingles. Pressure washers should not be used to clean the moss as they can damage the shingles unless the moss has been killed prior to washing. Only very low pressure should be used to clean the roof of moss and chemicals should be used to kill the moss prior to removal. Hire a professional roof cleaning service to clean and service this roof to insure proper drainage off the roof and help the roofing material last its full expected life.
- R-4 Roof/Attic:
The gutter system has some debris collection that is causing water to build-up inside the gutter and require cleaning. Clean the entire gutter system including downspouts and insure they are leak free, properly sloped to drain and are securely connected to the roof line. This is periodic maintenance that should be done a few times per year.
- P-5 Plumbing:
Periodic maintenance is recommended for your water heater.
In general, most home owners never do any preventative maintenance to their hot water heaters.... that is why they have such short average service lives between 8-12 years. Generally, the most important maintenance is regular draining of the tank to eliminate sludge build-up at the bottom of the tank. There is also a sacrificial anode that needs to be periodically replaced to reduce corrosion inside the tank, although some brands state they never need to be replaced and are maintenance free.
Tank was operating at time of inspection with no defects observed.
- HCF-1 Heating, Cooling and Fireplaces:
Annual servicing of the heating system is recommended for safe and reliable heat. Records indicate that this furnace has not been serviced in the last year. The furnace was tested during inspection and was operational. Recommend the furnace be serviced & cleaned.
- HCF-6 Heating, Cooling and Fireplaces:
Annual servicing of the gas fireplace is recommended to insure safe and reliable performance. Have this appliance serviced by a qualified gas appliance specialist annually. Unit was tested during inspection and was operational but a little dirty in the lower & upper cabinets and should be cleaned.
Improves
- E1-8 Exterior/Garage:
It is always a very good idea to have all your entrance door locks re-keyed after taking possession of the house. If any doors have a code for keyless entry, be sure to obtain the code and re-program for improved security.
- E1-12 Exterior/Garage:
For improved security, it is always a good idea to re-program the key code for the overhead garage door opener.
- P-6 Plumbing:
An expansion tank is recommended for the water heater. This helps reduce pressure on the plumbing system when the pipes and water expand from heating. Installation of expansion or pressure tanks is modern installation practice and should have been installed since a pressure reducing valve is present. Consult with a qualified plumber to install.
- P-10 Plumbing:
A drip pan is recommended to be installed under the laundry washer to protect the finished floor system in case of leaks. For improved protection from accidental water heater leaks consider a flood-safe device such as this - http://www.watts.com/floodsafe/popup.asp or a battery-operated water alarm.
- E-5 Electrical:
The existing smoke detectors in this home are original and older than 10 years - updating is recommended every ten years to insure reliable performance. I randomly tested the existing detector units during inspection today and they appeared to be operating correctly.
- MFB-1 Main Floor Bathroom:
The wall base trim (MDF) is recommended to have additional caulking around the tub & shower areas in all bathrooms to prevent water from being absorbed into the trim and causing swelling and water damage.
Monitors
- E1-11 Exterior/Garage:
Note: The elastomeric deck coating should be kept free from sharp edges such as metal patio furniture and such that can potentially damage the coating. Use pads or protectors to ensure coating is not damaged from chairs or other exterior furniture. Monitor this deck water-proof coating and maintain appropriately to ensure water does not access wood materials below and cause damage.
- R-3 Roof/Attic:
The plumbing vent flashings are a black rubber style that can become damaged / split on the roof and need to be monitored and replaced accordingly. These can lead to possible water intrusion around plumbing vent pipes and into the attic. These plumbing vent flashings typically do not last as long as the roof material itself and usually need replaced or re-sealed before the roof needs replaced.
Due Diligences
- P-2 Plumbing:
This home's sewage appears to employ a private septic system. Please note that an evaluation of this system is beyond the scope of this inspection. I recommend having this system further evaluated by a septic specialist.
Future Projects
- HCF-4 Heating, Cooling and Fireplaces:
The duct system typically is recommended to be professionally vacuum cleaned every 5-7 years. Avoid hiring a duct cleaning company that does NOT use a vacuum truck to clean the duct system. A vacuum truck is the best method for cleaning ductwork.
Efficiencies
- CS-1 Crawl Space:
One small section of floor insulation is missing under the kitchen area and should be re-installed.
- R-5 Roof/Attic:
The attic access hatch requires weather stripping to prevent heat loss and heat migration into the attic. Have a qualified contractor or handyman install weather stripping.
- R-7 Roof/Attic:
Fiberglass batten insulation has been used on the floor of the attic. This type of insulation allows for small gaps between the insulation and the wood framing/trusses and can allow thermal bridging, which easily allows heat loss around the wood framing. A better way is to use a blown-in loose fill insulation on the floors to allow a more even blanket of insulation to prevent thermal bridging.
Notes
- E1-1 Exterior/Garage:
The siding details at the fiber-cement siding are done using an older detail where the siding butts end joints are not flashed and are caulked instead. Today, the detail is to provide a flashing at these butt ends to prevent water from potentially running down behind the siding. Consider flashing these areas in the future prior to a whole house repaint or caulk these joints at a minimum.
Please see link to best practices guide for one of the most commonly installed brands of fiber cement siding:
- E1-2 Exterior/Garage:
The fiber-cement siding is missing metal horizontal flashing at many wall penetrations and are caulked instead. Today, the detail is to have a metal flashing and blocking installed at every wall penetration greater than 1 1/2" as the siding manufacturer requires. The problem here is caulking can dry out and shrink over time and eventually allow water penetration. Additionally, the siding manufacturer may void the product warranty for these particular areas due to improper installation and not following manufacturers installation instructions.
Please see link to best practices guide for one of the most commonly installed brands of fiber cement siding:
- E1-4 Exterior/Garage:
A few small nail or screw holes are present in various areas of the exterior and should be properly sealed with exterior-rated caulking.
- E1-5 Exterior/Garage:
The fiber-cement siding has cracked in a few places but only appear to be a cosmetic issue at this point. Recommend replacing these cracked siding boards prior to next whole house re-paint.
Please see link to best practices guide for one of the most commonly installed brands of fiber cement siding:
- SB-1 Structure and Basement:
Typical small cracks were noted in the foundation. No repair appears needed at this time. Minor settlement and shrinkage cracks are common in poured concrete and do not require repair as long as they do not continue to grow. The best way to prevent on-going settlement is by controlling roof runoff and site drainage to promote dry soils around the foundation; wet soils do not bear weight well. This will also help to prevent basement or crawl space moisture problems.
- P-1 Plumbing:
The supply pipe insulation is missing in the crawl space in a few places. Be sure all supply lines in unheated spaces have been adequately insulated to protect from freezing conditions that could damage the pipes and to prevent heat loss.
- P-3 Plumbing:
For more information about septic systems and how they work, please see this web site - a homeowner's guide to on-site septic systems: https://www3.epa.gov/npdes/pubs/homeowner_guide_long.pdf
- P-4 Plumbing:
This water heater is nearing the end of its useful service life at 15 years old.
The average life of these water heaters is 8-12 years. Budget to replace this water heater at any time.
- P-8 Plumbing:
A sump pump system was noted for this building in the crawlspace - it was tested during inspection and it was operating, including the battery-operated water alarm. The sump pit was full of water at the time of inspection meaning it is required to help keep this space dry. Please note that a sump pump can require maintenance and you may want to install some back up power systems so the pump will work when the power is out or be sure to have the generator provide power for this equipment.
- P-9 Plumbing:
There is no washer and dryer installed at the downstairs laundry room. You will need to buy these appliances and install.
- P-11 Plumbing:
The dryer vent duct should be routinely cleaned out professionally about every 2 years. This is important regular maintenance as lint build-up can be a potential fire hazard. The dryer vent appeared relatively clean at time of inspection.
- HCF-2 Heating, Cooling and Fireplaces:
The air filter was clean at the time of inspection and does not require replacement at this time. Furnace filters should be cleaned or replaced every 2-3 months.
- HCF-5 Heating, Cooling and Fireplaces:
During inspection today, I manipulated the thermostat for the radiant floor heat. There was a temperature rise on the floors confirmed by my thermal camera. For ideal comfort and efficiency with these heated floors, I recommend programming the thermostats to come on at desired times of the day. Leaving these on all day can be a waste of energy and it can be hard to remember to turn them on and off.
- E-1 Electrical:
No significant deficiencies were observed inside the main panel and all breaker wiring appeared neat & professional.
- E-2 Electrical:
This home has a manual transformer station for a generator. Inspection of generator systems is beyond the scope of this inspection. No generator was observed. Consider installing an automatic natural gas generator as an upgrade.
- E-3 Electrical:
No significant deficiencies were observed inside the sub-panel and all breaker wiring appeared neat & professional.
- I-2 Interior:
The drywall / sheetrock finishes require some touch up repair: See localized cracking & nail pops. This is typical. No red flags were found to indicate structural movement. Repair sheetrock blemishes as desired.
- K-1 Kitchen:
The Insta-Hot hot water fixture in the kitchen was tested during inspection and was operational.
- UB-2 Upstairs Bathroom:
The stopper in the upstairs hall bathtub is missing and requires replacement - or a rubber stopper can be used.
Inspection Report
Grounds
Drainage and Lot Location
Driveways/Walkways/Flatwork
Grounds, Trees and Vegetation
Retaining Walls
Exterior Stairs
Fences
Carport, Outbuildings and Other
Exterior/Garage
Siding and Trim
Eaves
Exterior Doors
Exterior Window Frames
Wrap Around Porch/Deck
Back Deck & Steps
2nd Floor Deck/Balcony
Chimneys
Garage
Crawl Space
Crawl Space Access
Vapor Barrier
Crawl Space Ventilation
Posts, Stem Walls and Footings
Insulation
Moisture Conditions
Rodents
Roof/Attic
Roof Materials
Skylights
Gutters / Downspouts
Attic Access
Attic Rodent/Bird Activity
Roof Framing and Sheathing
Attic Insulation
Attic and House Ventilation
Plumbing
Water Service Supply
Distribution Pipe
Waste Pipe and Discharge
Water Heater
Exterior Hose Bibs
Additional Sinks
Sewage Ejector Pumps
Sump Pumps and Drains
Washer
Dryer
Heating, Cooling and Fireplaces
Heating System
Air Conditioning/Heat Pump
Heating / Cooling Distribution Systems
Additional Heat Sources
Gas Fireplaces
Electrical
Service Equipment
Sub Panel
Branch Wiring
Receptacles and Fixtures
Smoke and CO Alarm Systems
Grounding Electrode / Conductor
Interior
Floors
Walls, Ceilings and Closets
Stairs and Railings
Interior Doors
Windows
Central Vacuum System
Kitchen
Sinks and Faucets
Cabinets and Countertops
Ventilation Method
Appliances
General Kitchen Condition
General Comments
Building Characteristics / Conditions
Style of Home: Contemporary
Type of Building : Single Family (2-story)
Approximate Square Footage: 2,100
Approximate Year of Original Construction: 2007
Attending the Inspection: Buyer and Buyer's Agent
Occupancy: The home was occupied
Animals Present: Dog present- no problem
Weather during the inspection: Clear, Recent Rain
Approximate temperature during the inspection: Below 40[F]
Ground/Soil surface conditions: Damp
Direction house faces: Mostly south
Grounds
Drainage and Lot Location
Clearance to Grade: Standard
Downspout Discharge: Below grade
Lot Description: Minor Slope
Driveways/Walkways/Flatwork
Driveway: Asphalt, Concrete, Gravel
Walkways: Concrete, Pavers, Gravel
Grounds, Trees and Vegetation
Trees/Vegetation too near building: No
Retaining Walls
None noted
Exterior Stairs
Standard
Fences
None noted
Carport, Outbuildings and Other
Cabana
Exterior/Garage
Siding and Trim
Trim Material: Wood
Siding Material: Fiber-cement, Board and batten, Masonry veneer
The siding details at the fiber-cement siding are done using an older detail where the siding butts end joints are not flashed and are caulked instead. Today, the detail is to provide a flashing at these butt ends to prevent water from potentially running down behind the siding. Consider flashing these areas in the future prior to a whole house repaint or caulk these joints at a minimum.
Please see link to best practices guide for one of the most commonly installed brands of fiber cement siding:
The fiber-cement siding is missing metal horizontal flashing at many wall penetrations and are caulked instead. Today, the detail is to have a metal flashing and blocking installed at every wall penetration greater than 1 1/2" as the siding manufacturer requires. The problem here is caulking can dry out and shrink over time and eventually allow water penetration. Additionally, the siding manufacturer may void the product warranty for these particular areas due to improper installation and not following manufacturers installation instructions.
Please see link to best practices guide for one of the most commonly installed brands of fiber cement siding:
A few small nail or screw holes are present in various areas of the exterior and should be properly sealed with exterior-rated caulking.
The fiber-cement siding has cracked in a few places but only appear to be a cosmetic issue at this point. Recommend replacing these cracked siding boards prior to next whole house re-paint.
Please see link to best practices guide for one of the most commonly installed brands of fiber cement siding:
Eaves
Open rafters
Exterior Doors
Solid core, Sliding glass
It is always a very good idea to have all your entrance door locks re-keyed after taking possession of the house. If any doors have a code for keyless entry, be sure to obtain the code and re-program for improved security.
Exterior Window Frames
Wood
Wrap Around Porch/Deck
Present
Structure: Ground contact treated lumber
Deck Ledger Board: Standard
Guardrail: Non-standard
Decking Material: Plastic/synthetic material
Back Deck & Steps
Present
Deck Structure: Ground contact treated lumber
Deck Ledger Board: Standard
Guardrail: None needed
Decking Material: Plastic/synthetic material
2nd Floor Deck/Balcony
Present
Deck Structure: Not visible
Deck Ledger Board: Not applicable
Guardrail: Standard
Decking Material: Elastomeric over plywood
Note: The elastomeric deck coating should be kept free from sharp edges such as metal patio furniture and such that can potentially damage the coating. Use pads or protectors to ensure coating is not damaged from chairs or other exterior furniture. Monitor this deck water-proof coating and maintain appropriately to ensure water does not access wood materials below and cause damage.
Chimneys
None noted
Garage
Attached
Automatic Garage Opener: Present
Garage Door Type: Metal w/ glass panel
For improved security, it is always a good idea to re-program the key code for the overhead garage door opener.
Structure and Basement
Foundation
% of Foundation Not Visible: 60%
Evidence of Seismic Protection: Present
Building Configuration: Crawl space
Foundation Description: Poured concrete
Typical small cracks were noted in the foundation. No repair appears needed at this time. Minor settlement and shrinkage cracks are common in poured concrete and do not require repair as long as they do not continue to grow. The best way to prevent on-going settlement is by controlling roof runoff and site drainage to promote dry soils around the foundation; wet soils do not bear weight well. This will also help to prevent basement or crawl space moisture problems.
Floor, Wall and Ceiling Framing
Wall Framing: Not visible
Wall Insulation: Not visible
Wall Sheathing: Not visible
Floor Framing: TGI Joists
Sub-Floor Material: OSB
Ceiling Framing: Bottom cord of truss
Crawl Space
Crawl Space Access
Located in: Garage
Method of Inspection: Crawled, but visibility was limited by insulation
Vapor Barrier
Vapor Barrier Material: Plastic
Crawl Space Ventilation
Ventilation Method: Exterior wall vents
Posts, Stem Walls and Footings
Standard
Insulation
Insulation Type: Fiberglass
Approximate R-Value: R-30
Moisture Conditions
Some signs
Some minor ponding water is present in the center of the crawlspace collecting above & below the plastic and some muddy areas were also observed. Improvements to the crawlspace drainage system appear to be needed to prevent this. Recommend installing additional drains in key spots to capture this water and route to the sump pump reservoir.
Rodents
None noted
Roof/Attic
Roof Materials
Method of Roof Inspection: Walked on roof
Roof Style: Hip and Gable
Roof Materials: Architectural grade composition shingle
Layers: 1
Approximate Age of Roof: Original, 15 years old
The roofing material on this building is done in a three-tab presidential grade architectural composition shingle. These are often rated as 50 year roofs. In practice these roofs have not been installed that long so difficult to know how long they will last. The installation appears neat and professional but a few repair items are in need of attention right away. Inquire with the seller about any warranty information for this roof. Many professional roofing companies will offer limited workmanship warranties. Repairs needed are:
- A few ridge shingles are torn/damaged that should be replaced.
- Lifted roofing nails are present in some places pushing through top layer and should be re-sealed.
- One section of the roof decking on the east side has lifted away from the trusses and is causing raised shingles and needs to be repaired.
Have a roofing contractor or a general contractor familiar with roof repairs make these corrections.
Minor moss growth was noted on the roof. This is bad for the roof covering and decking as it can trap moisture on the roof and can inhibit drainage off the roof. Moss removal and prevention is recommended. Products such as Tide are not recommended as the bleach in these products can deteriorate the shingles. Pressure washers should not be used to clean the moss as they can damage the shingles unless the moss has been killed prior to washing. Only very low pressure should be used to clean the roof of moss and chemicals should be used to kill the moss prior to removal. Hire a professional roof cleaning service to clean and service this roof to insure proper drainage off the roof and help the roofing material last its full expected life.
The plumbing vent flashings are a black rubber style that can become damaged / split on the roof and need to be monitored and replaced accordingly. These can lead to possible water intrusion around plumbing vent pipes and into the attic. These plumbing vent flashings typically do not last as long as the roof material itself and usually need replaced or re-sealed before the roof needs replaced.
Skylights
Insulated curb style
Gutters / Downspouts
Gutter / Downspout Materials: Aluminum
The gutter system has some debris collection that is causing water to build-up inside the gutter and require cleaning. Clean the entire gutter system including downspouts and insure they are leak free, properly sloped to drain and are securely connected to the roof line. This is periodic maintenance that should be done a few times per year.
Attic Access
Crawled partial
Located in: Upstairs Hall Closet
The attic access hatch requires weather stripping to prevent heat loss and heat migration into the attic. Have a qualified contractor or handyman install weather stripping.
Attic Rodent/Bird Activity
None noted
Roof Framing and Sheathing
Rafters: Truss
Sheathing: Plywood
Organic substances were noted in the attic on the roof framing mostly on the north facing sections of roof and some spots on the east side as well. This appears to be due to lack of ventilation at the lower roof cavity areas. The substances looked localized to these areas and not chronic to the attic. Rusty nails were also observed along with rust drip marks in the batten insulation. Mold testing and molds in general are beyond the scope of this inspection. Use sealants as desired to seal any mold-like substances and monitor this area. I recommend having a qualified contractor evaluate & install additional ventilation to remedy this issue.
Attic Insulation
Insulation Type: Batten Fiberglass
Approximate Insulation R-Value on Attic Floor: 49
Approximate Insulation R-Value on Attic Walls: 30
Fiberglass batten insulation has been used on the floor of the attic. This type of insulation allows for small gaps between the insulation and the wood framing/trusses and can allow thermal bridging, which easily allows heat loss around the wood framing. A better way is to use a blown-in loose fill insulation on the floors to allow a more even blanket of insulation to prevent thermal bridging.
The attic insulation appears to be installed to modern standards of R-49, reference: 2021 International Energy Conservation Code (IECC).
Attic and House Ventilation
Bath Fan Ducting: Ducted to exterior
Kitchen Fan Ducting: Ducted to exterior
Attic Ventilation Method: Soffit vents, Continuous ridge vents, Roof jack vents
Plumbing
Water Service Supply
Pipe Material: Copper
Well or Public Supply: Public
Water Pressure: 65 PSI
Pressure Reducing Valve: Present
Main Water Shut-off Location: Garage
Distribution Pipe
Pipe Insulation: Present
Supply Pipe Materials: Copper, PEX
Functional Flow: Average
Waste Pipe and Discharge
Discharge Type: Septic system
Waste and Vent Pipe Materials: ABS plastic
For more information about septic systems and how they work, please see this web site - a homeowner's guide to on-site septic systems: https://www3.epa.gov/npdes/pubs/homeowner_guide_long.pdf
Water Heater
System Type: Tank
Located in: Upstairs Laundry Room Closet
Manufacturer: Bradford-White
Size: 75 gal
Age: Built in Feb. 2007
Energy Source: Gas
Last Service Record: None noted
Temperature Pressure Relief Value: Present - Not Tested
Temperature: 110F +
Periodic maintenance is recommended for your water heater.
In general, most home owners never do any preventative maintenance to their hot water heaters.... that is why they have such short average service lives between 8-12 years. Generally, the most important maintenance is regular draining of the tank to eliminate sludge build-up at the bottom of the tank. There is also a sacrificial anode that needs to be periodically replaced to reduce corrosion inside the tank, although some brands state they never need to be replaced and are maintenance free.
Tank was operating at time of inspection with no defects observed.
An expansion tank is recommended for the water heater. This helps reduce pressure on the plumbing system when the pipes and water expand from heating. Installation of expansion or pressure tanks is modern installation practice and should have been installed since a pressure reducing valve is present. Consult with a qualified plumber to install.
Exterior Hose Bibs
Operating
Additional Sinks
Tested
Sewage Ejector Pumps
None noted
Sump Pumps and Drains
Sump Pumps: Present
A sump pump system was noted for this building in the crawlspace - it was tested during inspection and it was operating, including the battery-operated water alarm. The sump pit was full of water at the time of inspection meaning it is required to help keep this space dry. Please note that a sump pump can require maintenance and you may want to install some back up power systems so the pump will work when the power is out or be sure to have the generator provide power for this equipment.
Washer
Not tested
There is no washer and dryer installed at the downstairs laundry room. You will need to buy these appliances and install.
A drip pan is recommended to be installed under the laundry washer to protect the finished floor system in case of leaks. For improved protection from accidental water heater leaks consider a flood-safe device such as this - http://www.watts.com/floodsafe/popup.asp or a battery-operated water alarm.
Dryer
Tested
Power Source: Electric, Gas present but not in use
Duct to Exterior: Ducted
Dryer Vent Termination: Back of house
The dryer vent duct should be routinely cleaned out professionally about every 2 years. This is important regular maintenance as lint build-up can be a potential fire hazard. The dryer vent appeared relatively clean at time of inspection.
Heating, Cooling and Fireplaces
Heating System
Energy Source: Natural gas
Heating Method: Forced air furnace
Located in: Garage
Manufacturer: York
Capacity: 120k BTU
Age: Built in March 2005
Last Service Record: 2018
Filtration System: Disposable
The air filter was clean at the time of inspection and does not require replacement at this time. Furnace filters should be cleaned or replaced every 2-3 months.
Air Conditioning/Heat Pump
Heat Pump
Manufacturer: York
Energy Source: Electric
Age: Built in 2007
Capacity: 5 Ton
Location: North side of house
Heating / Cooling Distribution Systems
Heat Source in Each Room: Present
Distribution Method: Ductwork
The duct system typically is recommended to be professionally vacuum cleaned every 5-7 years. Avoid hiring a duct cleaning company that does NOT use a vacuum truck to clean the duct system. A vacuum truck is the best method for cleaning ductwork.
Additional Heat Sources
Present
Description: Radiant floor
Manufacturer: NuHeat
Location: Upstairs Bathrooms
During inspection today, I manipulated the thermostat for the radiant floor heat. There was a temperature rise on the floors confirmed by my thermal camera. For ideal comfort and efficiency with these heated floors, I recommend programming the thermostats to come on at desired times of the day. Leaving these on all day can be a waste of energy and it can be hard to remember to turn them on and off.
Gas Fireplaces
Present
Fireplace Types: Sealed gas decorative fireplace
Annual servicing of the gas fireplace is recommended to insure safe and reliable performance. Have this appliance serviced by a qualified gas appliance specialist annually. Unit was tested during inspection and was operational but a little dirty in the lower & upper cabinets and should be cleaned.
Recommended procedure for cleaning gas fireplace glass.
1) Make sure your glass is cool to the touch. It is also recommended that your pilot is turned off before you begin to clean the glass.
2) Remove the front face or louvers of your fireplace.
3) Follow the instructions in your manual to carefully remove the glass assembly. Lay it on a soft surface.
4) Using a soft cloth, clean both sides of the glass with a household glass cleaner. Do not use a product with ammonia or any abrasive cloth or cleaner to clean your glass. The glass can shatter if it is scratched. For heavy deposits, use a hard water deposit glass cleaner, such as Stove Bright Glass Cleaner.
5) Follow the instructions in your manual to carefully replace the glass on the front of the fireplace. Make sure you re-latch the glass so it is securely fastened on your fireplace and the door gasket is making good contact all the way around.
Electrical
Service Equipment
Volts: 120/240
Service Drop: Underground
Meter Base Amperage: 200
Service Entrance (SE) conductor Size: Aluminum, 4/0, 200 amps
Main Panel Amperage: 200 amps
Electric Service Amperage: 200 amps
Main Electric Panel Location: Garage
Panel Brand: Siemens
This home has a manual transformer station for a generator. Inspection of generator systems is beyond the scope of this inspection. No generator was observed. Consider installing an automatic natural gas generator as an upgrade.
Sub Panel
Sub-panel
Sub-panel Main Conductor: Aluminum, #2, 100 amps
Sub--Panel Amperage: 100
Sub-Panel Location: Garage
Panel Brand: Siemens
Branch Wiring
Wire Material: Copper and Multi-strand Aluminum
Wiring Method: Non-metallic sheathed cable, Armored BX cable
Receptacles and Fixtures
Inspection Method: Random Testing
Outlets: Three wire outlets
Smoke and CO Alarm Systems
Smoke Detectors: Present
Carbon Monoxide Alarms: Present
The existing smoke detectors in this home are original and older than 10 years - updating is recommended every ten years to insure reliable performance. I randomly tested the existing detector units during inspection today and they appeared to be operating correctly.
Grounding Electrode / Conductor
Present
Grounding Means: Driven grounding rods, Main water line, Gas line, Water pipes at water heater
Fuel Storage and Distribution
Oil Storage
None noted
Propane Storage
None noted
Gas Meter and Gas Plumbing
Present
Gas Shutoff Location: East side of structure
Gas Pipe Materials: Steel and flex pipe
For improved safety, this house is equipped with a Northridge valve. These are seismic protection that can automatically shut off the gas in the event of an earthquake. Testing these valves is beyond the scope of a home inspection.
Interior
Floors
Floor Materials: Carpet, Pre-finished Hardwood, Tile, Vinyl
Walls, Ceilings and Closets
Wall and Ceiling Materials: Drywall
The drywall / sheetrock finishes require some touch up repair: See localized cracking & nail pops. This is typical. No red flags were found to indicate structural movement. Repair sheetrock blemishes as desired.
Stairs and Railings
Standard
Interior Doors
Solid Core
The upstairs laundry room door rubs and sticks at the frame and the door will not latch closed. Have this door adjusted and/or repaired to function properly.
The upstairs hall closet & hall bathroom closet sliding door hardware is missing at the bottom to keep doors in line and is recommended to be installed.
The door stop system for the home is incomplete. Some door stops are missing and I recommend systematically installing door stops to protect doors and wall finishes.
Windows
Window Glazing: Double pane
Interior Window Frame: Vinyl
Window Styles: Casement, Sliding, Fixed pane, Single hung
The two single hung windows at the kitchen garden window will not stay open and the sash springs are not functioning correctly. Repair these springs for proper operation of the windows. Please note that these windows are designed to be able to disengage the springs so that the window frames can be removed for cleaning.
Central Vacuum System
None Noted
Kitchen
Sinks and Faucets
Tested
Cabinets and Countertops
Countertop Material: Granite
Cabinet Material: Wood, Plastic laminate
Ventilation Method
Fan ducted to exterior
Appliances
Refrigerator: Operating
Dishwasher: Operated
Dishwasher Air Gap: Present
Range/ Oven /Cook-tops: Gas and electric
Disposer: None noted
The Insta-Hot hot water fixture in the kitchen was tested during inspection and was operational.
A faint gas smell is present around the gas stove and could indicate a very small leak. I recommend further evaluation to be sure no leak is present. If an actual leak is discovered, have it repaired.
General Kitchen Condition
Standard
Main Floor Bathroom
Sinks and Cabinets
Tested
Toilet
Tested
Bathtub / Shower
Tested
Bathroom Ventilation
Type: Bath fan
General Bath Condition
Standard
The wall base trim (MDF) is recommended to have additional caulking around the tub & shower areas in all bathrooms to prevent water from being absorbed into the trim and causing swelling and water damage.
Upstairs Bathroom
Sinks and Cabinets
Tested
One drawer on each of the hallway bathroom sink cabinets is not operating as designed and needs adjustments or repairs.
Toilet
Tested
Bathtub / Shower
Tested
The stopper in the upstairs hall bathtub is missing and requires replacement - or a rubber stopper can be used.
Bathroom Ventilation
Type: Bath fan
General Bath Condition
Standard
Master Bathroom
Sinks and Cabinets
Tested
Toilet
Tested
Bathtub / Shower
Tested
Bathroom Ventilation
Type: Fan and window
General Bath Condition
Standard
Receipt -- Inspection Report
12345 NE 9th Ct, Bellevue, WA 98000
Home inspection | $595.00 |
$595.00 | |
PAID |
Livin Good Inspections
C/O Todd Livingood
12330 NE 92nd Lane, J404
Kirkland, WA 98033
(206) 251-3009
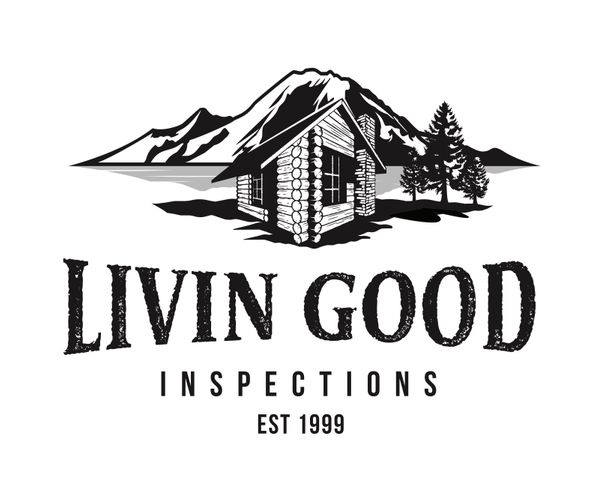