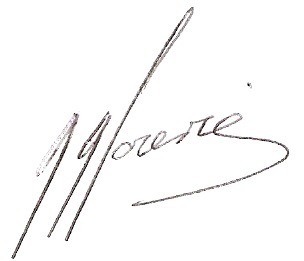
Jurie Fourie, License #NACHI14102004
The Scope and Purpose of this Home Inspection
Purchasing or selling property involves risk
The purpose of this Critical Inspection and Report is to help reduce the risk associated with the purchase, sale or maintenance of a structure by providing professional observations about the critical components of the structure which are the structure, roof, windows and doors, plumbing installation and electrical installation of the structure and damp issues. A home inspection is a limited visual inspection and cannot eliminate all the risk. Some homes present more risk than others. If you attended the inspection, I would have tried to inform you of my concerns during the inspection process. This is more difficult to convey in a report and one of the many reasons why I recommend attendance during the inspection.
A home inspection is not an insurance policy
This report does not substitute for or serve as a warranty or guarantee of any kind. Home warranties can be purchased separately from insurance firms that provide this service.
A home inspection is visual and not destructive
The descriptions and observations in this report are based on a visual inspection of the structure. I inspect the aspects of the structure that can be viewed without dismantling, damaging or disfiguring the structure and without moving furniture and interior furnishings. Areas that are concealed, hidden, inaccessible or unsafe to view are not covered in this inspection. Some systems cannot be tested during this inspection as testing risks damage to the building. For example, overflow drains on baths are generally not tested because if they were found to be leaking they could damage the finishes below. My procedures involve non-invasive investigation and non-destructive testing which limit the scope of the inspection.
This is not an inspection for NHBRC/Building Regulation/Municipal Compliance
Although this inspection report may refer to SANS (South African National Standards) and municipal by-laws, this report is not intended to be an NHBRC (National Home Builders Registration Council), NBR (National Building Regulation) or a local Municipal By-law Compliance inspection. Although some safety issues may be addressed in this report, this inspection is not a safety inspection and I am not required to identify all potential hazards.
This is not an inspection for Mould or Wood Destroying Organisms
The Standards of Practice of the International Association of Certified Home Inspectors (InterNACHI) do not require me to determine the presence of mould, mildew or fungus! Nor do they require me to determine the presence of wood-destroying organisms (WDO) or pests. Observations of mould-like substances, WDO and pests may be included in this report as a courtesy. These observations are identified by WDO at the beginning of the narratives. However, this report is not a mould or WDO report. Mould and WDO inspection are separate inspections that are performed on request and quoted for and reported separately!
My observations are based on my tertiary qualifications, InterNACHI's Continuing Education requirements, research and workplace experience
Construction techniques and standards vary. There are different ways to build a house or install a system in a house. The observations in this report are based on my tertiary qualifications, research and workplace experience. Other inspectors and contractors may have some differing opinions. You are welcome to seek opinions from other professionals.
The scope of this inspection
This inspection will include the following systems depending on the type of inspection required: exterior, roof, structure, drainage, foundation, roof space, interior, plumbing, electrical and heating. The evaluation will be based on limited observations that are primarily visual and non-invasive. This inspection and report is not intended to be technically exhaustive.
Your expectations
The overall goal of a home inspection is to help ensure your expectations are appropriate with the house you have bought or are proposing to buy. To this end, I assist with the discovery by showing and documenting observations made during the home inspection. This should not be mistaken for a technically exhaustive inspection designed to uncover every defect with the building. Such inspections are available but they are generally cost-prohibitive to most homebuyers and home owners.
Your participation was requested
Your presence was requested during this inspection. A written report will not substitute for all the possible information that can be conveyed verbally by a shared visual observation of the conditions of the property.
How to Read This Report
Getting the Information to You
This report is designed to deliver important and technical information in a way that is easy to access and understand. This report may include a summary page. If you are in a hurry, you can take a quick look at my "Summary Page” and quickly get critical information for important decision making. However, I strongly recommend that you take the time to read the full Report, which includes digital photographs, captions, diagrams, descriptions, videos and hot links to additional information.
The best way to get the layers of information that are presented in this report is to read your report online, which will allow you to expand your knowledge about your house. You will notice some words or series of words highlighted in blue and underlined – clicking on these will provide you with a link to additional information.
This report can also be printed on paper or to a PDF document.
Chapters and Sections
This report is divided into chapters that parcel the home into logical inspection components. Each chapter is broken into sections that relate to a specific system or component of the home. You can navigate between chapters with the click of a button on the left side margin.
Most sections will contain some descriptive information done in black font. Observation narratives, done in colored boxes, will be included if a system or component is found to be significantly deficient in some way or if I wish to provide helpful additional information about the system or the scope of my inspection. If a system or component of the home was deemed to be in satisfactory or serviceable condition, there may be no narrative observation comments in that section and it may simply say “tested,” or “inspected.”
Unless defective or maintenance items are specifically allocated to rooms or areas they should be regarded as generally defective items that can be found throughout the residence and/or property.
Photographs
Photographs take up a lot of space, therefore, the photographs pertaining to a particular defect do not necessarily include all the photographs or defects of the particular defect identified.
Note: For a better view of the photographs included in the report, click on the photographs to enlarge them.
Observation Labels
All narrative observations are colored, numbered and labeled to help you find, refer to, and understand the severity of the observation. Observation colors and labels that may be used in this report are:
- NOTE:Refers to aside information and /or any comments elaborating on descriptions of systems in the home or limitations to the home inspection.
- COMMENT:A comment of the general condition of various aspects of the property noted during the inspection.
- MAJOR CONCERN:Repair items that may cost a significant amount of money to correct now or in the near future, or items that require immediate attention to prevent additional damage or eliminate safety hazards.
- DEFICIENT:Repair and maintenance items noted during inspection. Please note that some repair items can be expensive to correct such as re-finishing hardwood floors, but are considered simply repair items due to their cosmetic nature.
- DEFERRED:An observation or item that could not be inspected or which may require further investigation such as a buried oil tank to determine the severity and / or urgency of repair.
- MAINTENANCE REQUIRED:A system or component requiring maintenance appears to be functioning as intended, but would benefit from minor repair, maintenance or improvement at this time. General deficiencies include patching, painting, cleaning, cleaning the gutters or changing the filters.
- MONITOR:An area, condition, system or component that is in need of monitoring appears to be functioning as intended and capable of safe usage in its present condition; however, the inspector's concern stated in the report should be monitored or further evaluated by an appropriate person.
Summary Page
The summary page is intended to provide you and interested other parties directly involved with this home a convenient and cursory preview of some of the conditions and components that I have identified within my report as being in need of further evaluation or service by an appropriately qualified specialist or that pose a potential health and safety risk. It is not intended to be comprehensive, and should not be used as a substitute for reading the entire home inspection report or be viewed as a tacit endorsement of the condition of components or features that do not appear in this summary report. The entire report must be read to get a complete understanding of this report as the Summary Page does not include photographs or photo captions.
Summary
Major Concerns
- E1-3 Electrical:
There was an uncovered opening in the cover of the main electrical panel that exposes those who have access to the panel to shock hazards. This opening will need to be covered with approved panel block-out covers. Have a suitably qualified electrician check and repair the installation. This is a safety issue.
Deficients
- E-4 Exterior:
Waterproofing of the balcony floors under the tiling appeared not to have been done. There was signs of plaster or paint damage on the underside of the balcony structure at the time of the inspection.
- E-7 Exterior:
The balcony door frame was loose at the opening side. The aluminium frame should be properly repaired by an qualified carpenter or handyman.
- E-8 Exterior:
The exterior doors at the southeast side of the house had cracks and gaps running along the external thresholds at the bottom rail of the door frames and on the threshold finish. The cracks and gaps in threshold should be sealed to prevent further moisture intrusion into the thresholds and reveals (sides). No rising damp was noticeable on the sides of the door openings externally.
- E-9 Exterior:
The aluminium doors and frames appeared to have been leaking past the thresholds. Note the moisture damage to the skirtings inside these doors. Have these doors, frames, side lights and thresholds further investigated and sealed. The skirtings should also be repaired and sealed as recommended by a qualified carpenter or handyman.
- E-10 Exterior:
The front entrance door was binding onto the door frame on the lock side, making the door difficult to close. In time, this will cause the hinges and door frame to loosen. The door will need adjustment to function properly.
- The striker plate on front entrance's door required adjustment
- I-3 Interior:
There was moisture damage and signs of bubbling paintwork, flaking paintwork and moisture damage on the upper and middle portion of the walls internally in the living room, loft and bathroom which appeared to be a result of falling damp and penetrating damp caused by roof leaks and moisture intrusion from windblown rainwater against the outside of the windows and walls. I recommend an inspection and repair by a suitably qualified painter. The walls can be repaired and painted once the source of the moisture is found and repaired.
- Bubbling paintwork and staining on the wall below the ceiling on the east wall of the living room.
- Bubbling, flaking paintwork and efflorescence on the wall as a result of bubbling paintwork, falling damp and penetrating damp.
- Bubbling paintwork and flaking paintwork on the upper section of the wall in the living room.
- Bubbling paintwork and moisture staining on the wall in the corner of the loft.
- Staining and mould like substances on the bathroom wall above the shower. This appeared to be from roof leaks and not from condensation!
- Staining and mould like substances on the bathroom wall above the toilet.
- I-4 Interior:
There was evidence of moisture damage to most of the ceilings and cornices in the flat. There was some cornice cracks, cracking between cornices and walls, cracking between ceiling boards, deviations and moisture damage on the ceilings and cornices. The ceiling damage appeared to have been caused by leaks in the roof. Expect concealed water damage here based on the current visual condition.
Some examples are shown below:
- Cracking between ceiling boards in the living room ceiling from a roof leak.
- Staining and mould like substances on the living room wall at the cornice.
- Moisture intrusion between ceiling boards at the H-section joiner and a paint patch!
- Crack between ceiling boards and cornice in the loft was a sign of moisture intrusion.
- Moisture staining on the loft ceiling and the cracked cornice.
- Paint damage and moisture staining on the cornice in the loft. The opening section of the window appeared to be corroded or stained.
- Moisture damage and cornice cracks on the cornice and wall in the loft.
- I-7 Interior:
No doorstops on the interior and exterior doors of the unit were provided. The stops should be installed to prevent the exterior and interior doors from banging against the walls.
- I-9 Interior:
Flaking paintwork, moisture damage and staining was noted at the sills in the unit's windows indicating that the windows were leaking. There is always a chance of hidden moisture intrusion and corrosion with this condition. Seal around the exterior of the frames at the sill, reveals and head of the windows with a suitable exterior silicone.
Examples are shown below:
- I-10 Interior:
A cracked pane of glass was noted in the kitchen window. This requires glazing replacement.
- I-11 Interior:
Moisture staining and leaking was noted at and above the operable roof light in the loft. This may be from the roof windows being left open during rain. However, from the damage noted on the window and ceiling in the loft and living room area, the roof appeared to be leaking. Repair will be required to prevent further moisture damage to the finishes. Have the roof and roof light evaluated by an appropriately qualified roofing contractor for further remarks and recommendations.
- I-13 Interior:
One of the timber steps was damaged on the leading edge. Care must be taken when descending the stairs for possible slipping.
- The edge of one of the steps was damaged.
- B2-5 Bathroom:
The shower trap grid in the shower was missing at the time of the inspection. The grid should be replaced and fixed to prevent objects from entering the trap and blocking it. The edges of the trap itself should be sealed.
- B2-6 Bathroom:
The glass shower door in the bathroom shower required adjustment - it was not latching closed and could leak during operation.
- E1-6 Electrical:
Two ceiling lights in the living room and kitchen did not respond to switching. The globes should be replaced to check if the fittings are in working order.
- According to the tenant, this light stopped working during a rainstorm as a result of water leaking through the ceiling.
- Lights circuits are not always fed through earth leakage circuit breakers (ELCBs)! If there is a fault on a light fitting that requires replacement, the main switch, ELCB and the dedicated circuit breaker will need to be switched off to be on the safe side!
- E1-7 Electrical:
The ceiling fan in the loft was not tested. The light worked with the longer pull switch but the pull switch operating the fan was not accessible. Repair was required!
- P-8 Plumbing:
There was a hole in the waste pipe from the kitchen sink that should be repaired.
- A hole on this wastepipe! The hole should be sealed!
Maintenance Requireds
- R-2 Roof:
The roof valley appeared to be leaking. During hail or heavy rainstorms rain may leak over the sides of the valley flashing. The roof sheeting and valley flashing on the valley can also collect leaves, other wind blown objects, loose objects or other obstructions. If this occurs rainwater may leak past the valley flashing. Have the valley flashing and roof sheeting properly checked and repaired as necessary.
- E-12 Exterior:
The window putty at the all of the steel windows at all sides of the house was cracked. Badly cracked putty and corrosion should be removed, the putty redone and repainted to prevent leakage and corrosion of the frames. Where the window putty has been replaced the putty should be painted within 2 weeks to prevent the premature drying out and cracking of the putty.
An example is shown below:
- K-6 Kitchen:
The stove plates were rusty and required cleaning and restoring.
- B2-2 Bathroom:
A tap on the basin was loose. The water supply pipes could be vulnerable to physical damage. Have this further evaluated and repaired as needed by a licensed plumber.
Monitors
- S-1 Structure:
The visible cracks on the exterior walls of the unit appeared to have been the result of differential moisture movement, thermal movement between different building materials or slight settlement in the structure. At this stage, the cracks did not appear to be structurally significant. Once the cracks are patched, the cracks probably won't appear at a later stage. However, this area requires monitoring to see if the wall cracks reappear. If the cracks reappear and lengthen and widen, or more cracks appear, a structural engineer should be consulted for further remarks and recommendations.
- A crack between the concrete column and the brickwork was caused by differential movement between different building elements.
- It appeared that there had been a crack at the corner of the window that had been repaired.
- This crack was not unusual and is normally the result of differential thermal movement between different building materials, in this case, the steel lintel and brickwork.
- This slight diagonal crack at the living area and loft was indicative of settlement. It did not appear to be structurally significant.
- The minor crack in the corner of the structure ran up all the way to the ceiling.
- The peeling paint appeared to indicate that the crack was as a result of a moisture movement between building elements. This was not structurally significant!
- Moisture intrusion and slight cracks through the paint on the wall in the loft on the south side.
- Moisture damage and slight cracks at the wall and window in the loft. This is from either or both penetrating damp and falling damp at the wall and window.
Critical Inspection Report
Exterior
General
Exterior Walls
Decks, Patios, Balconies and Verandahs
Exterior Doors
Window Exteriors and Sills
Interior
General
Floors and Floor Materials
Walls and Ceilings
BICs (Built In Cupboards) and Cabinetry
Interior Doors
Windows
Interior Stairs and Landings
Kitchen
Sinks, Vegetable Bowls, Wash Troughs, Taps and Mixers
Cabinets and Counters
Appliances
Ventilation
General Condition
Bathroom
Basins
Cabinets and Counters
Toilet and Bidet
Bath and Shower
Bathroom Ventilation
General Bathroom Condition
General Comments
Building Characteristics, Conditions and Limitations
Type of Building : Apartment
Approximate Area (m²): Less than 60
Approximate Year of Original Construction: 2013
Attending the Inspection: Inspector only
Occupancy: Occupied
Animals Present: No
Weather during the inspection: Warm, Scattered clouds
Approximate temperature during the inspection: Over 15 ˚C
For the purposes of this report, the flat is on: Southeast corner, top floor
This building was occupied at the time of the inspection. Inspection of occupied buildings presents some challenges as goods, fittings, fixtures and furniture can obstruct visual inspection of and access to parts of the house. I do my best during inspection to work around these to discover as much as possible about the building without moving or damaging goods, fittings, fixtures and furniture, however, the presence of these items may limit the inspection.
The Occupational Safety Act requires that all residential electrical installations must be installed and repaired under the control of a registered electrician. The act also requires that the property owner must be in possession of a Certificate of Compliance (CoC) at all times for any new installations and changes to the wiring of the building. An updated document is required every time a property is sold (transferred) and every time an electrical installation is altered. Make sure you have a copy!
It is always wise to get plans from the seller and to do a visual due diligence to ensure that the approved plans correspond with the “as built” structures on the property! By law, property owners in South Africa have to ensure that all the buildings on their properties are on the plan and that the plans have been approved by the relevant local authorities and comply with Building Regulations. It is important to have the approved plans for the property and any extensions and renovations. Final approval of the building is in the form of an Occupation Certificate which is issued by the building control element of the municipality to certify that the construction, extension or renovation work have been executed in accordance with the approved drawings. The Building Regulations apply to all buildings within the borders of South Africa.
This unit has a very exposed design that will result in higher exterior maintenance costs and shorter life cycles from exterior protective systems. Buildings with this exposure to the elements in this climate should have maintenance and repairs done more regularly in a professional and detailed way to prevent premature failure of the exterior systems.
It is imperative for the seller to disclose all known defects to their agent before placing their property on the market. Agents are obliged to disclose these defects to buyers. However, a seller cannot be expected to know about latent defects, and therefore, you need to be aware of the risks associated with purchasing a secondhand property particularly given that the voetstoots clause is designed to protect the seller. The Consumer Protection Act is not a protective shield for you in these circumstances. The law requires that the seller's disclosure forms part of the sales contract or be attached as an addendum to the sales contract, signed by the seller. Not disclosing all the defects the seller may know of, risks expensive litigation and damages claims.
Structure
Floor, Wall and Roof Structure
Floor Structure: 3rd Floor (Concrete/screed)
Wall/Support Structure: Load-bearing (Masonry, 230 mm Brickwork), Non-load-bearing (Masonry, 110 mm Brickwork)
Roof and Ceiling Framing: Roof structure (Roof trusses/beams, Factory manufactured roof trusses, Ceiling brandering nailed or screwed to the bottom cord of the roof trusses)
The visible cracks on the exterior walls of the unit appeared to have been the result of differential moisture movement, thermal movement between different building materials or slight settlement in the structure. At this stage, the cracks did not appear to be structurally significant. Once the cracks are patched, the cracks probably won't appear at a later stage. However, this area requires monitoring to see if the wall cracks reappear. If the cracks reappear and lengthen and widen, or more cracks appear, a structural engineer should be consulted for further remarks and recommendations.
- A crack between the concrete column and the brickwork was caused by differential movement between different building elements.
- It appeared that there had been a crack at the corner of the window that had been repaired.
- This crack was not unusual and is normally the result of differential thermal movement between different building materials, in this case, the steel lintel and brickwork.
- This slight diagonal crack at the living area and loft was indicative of settlement. It did not appear to be structurally significant.
- The minor crack in the corner of the structure ran up all the way to the ceiling.
- The peeling paint appeared to indicate that the crack was as a result of a moisture movement between building elements. This was not structurally significant!
- Moisture intrusion and slight cracks through the paint on the wall in the loft on the south side.
- Moisture damage and slight cracks at the wall and window in the loft. This is from either or both penetrating damp and falling damp at the wall and window.
Roof
General
Roof Style: Gambrel, Shed
Roofing and Flashings
Roof Covering Materials: Sheeted roofs (Metal with exposed fasteners)
Approximate Age of Roof Covering: 10-12 Years
The roof material on the building and flat's roof appeared to consist of IBR profile sheeting which was fixed with pierced fixings. Pierced roof sheeting material can last between 40 to 70 years. However, much depend on the installation of the roofing. Items like roof screws, washers and rubber gaskets do not last as long! They typically last about 20 years, but roof sheet and screw movement can shorten this time! A pierced fixing roof system is installed by securing the sheets down by screwing through the metal. This method doesn’t allow the metal to expand and contract naturally causing the screws to enlarge the holes in the roof sheeting they are fixed through. In addition, heat and movement may cause the gaskets that come with the roof screws to deteriorate and fail. This leads to leaks and the need for regular maintenance.
The roof valley appeared to be leaking. During hail or heavy rainstorms rain may leak over the sides of the valley flashing. The roof sheeting and valley flashing on the valley can also collect leaves, other wind blown objects, loose objects or other obstructions. If this occurs rainwater may leak past the valley flashing. Have the valley flashing and roof sheeting properly checked and repaired as necessary.
Exterior
General
My inspection of the exterior included the visually accessible areas of windows, walls and doors. The exterior windows, walls, doors and eaves were inspected from the ground only. My inspection was performed in accordance with the International Association of Certified Home Inspectors' Standards of Practice.
Exterior Walls
External Superstructure Finish: Facebrick
The facebrick superstructure finish of the unit was generally in a reasonable condition.
Decks, Patios, Balconies and Verandahs
Balconies: 3rd-floor balcony, Covered balcony
Guardrail: Standard
The rails and the posts in the balustrades were functional and secure.
Exterior Doors
Door Types: Sliding doors
Door Finishes: Factory finished
Door Fame Material: Aluminium
All external doors and frames were tested for correctly opening and closing. Where keys were available, the locking of the doors were tested for locking.
The exterior doors and frames were generally in a reasonable condition except where additional items are specifically listed.
The exterior doors at the southeast side of the house had cracks and gaps running along the external thresholds at the bottom rail of the door frames and on the threshold finish. The cracks and gaps in threshold should be sealed to prevent further moisture intrusion into the thresholds and reveals (sides). No rising damp was noticeable on the sides of the door openings externally.
The aluminium doors and frames appeared to have been leaking past the thresholds. Note the moisture damage to the skirtings inside these doors. Have these doors, frames, side lights and thresholds further investigated and sealed. The skirtings should also be repaired and sealed as recommended by a qualified carpenter or handyman.
The front entrance door was binding onto the door frame on the lock side, making the door difficult to close. In time, this will cause the hinges and door frame to loosen. The door will need adjustment to function properly.
- The striker plate on front entrance's door required adjustment
Window Exteriors and Sills
Window Types: Casement
Window Material: Steel
Window Finishes: Painted
Sills: Precast Concrete
The window exteriors and sills appeared to be in a average condition except where additional items are specifically listed.
The window putty at the all of the steel windows at all sides of the house was cracked. Badly cracked putty and corrosion should be removed, the putty redone and repainted to prevent leakage and corrosion of the frames. Where the window putty has been replaced the putty should be painted within 2 weeks to prevent the premature drying out and cracking of the putty.
An example is shown below:
Interior
General
My inspection of the interior of the house included the visually accessible areas of floors, walls and ceilings. The interior areas were inspected from floor level only and without the use of a ladder. No furniture, equipment, floor coverings, appliances or stored goods were moved during my inspection to prevent accidental damage. My inspection was performed in accordance with the International Association of Certified Home Inspectors' Standards of Practice.
Floors and Floor Materials
Floor Materials: Ceramic tile
Floor Settlement: None noted
Generally, where visible, the tile flooring throughout the unit appeared in reasonable decorative order.
Walls and Ceilings
Wall and Ceiling Materials: Walls (Plaster), Ceilings (Gypsum ceilings with H section trim, Gypsum cornices)
There was moisture damage and signs of bubbling paintwork, flaking paintwork and moisture damage on the upper and middle portion of the walls internally in the living room, loft and bathroom which appeared to be a result of falling damp and penetrating damp caused by roof leaks and moisture intrusion from windblown rainwater against the outside of the windows and walls. I recommend an inspection and repair by a suitably qualified painter. The walls can be repaired and painted once the source of the moisture is found and repaired.
- Bubbling paintwork and staining on the wall below the ceiling on the east wall of the living room.
- Bubbling, flaking paintwork and efflorescence on the wall as a result of bubbling paintwork, falling damp and penetrating damp.
- Bubbling paintwork and flaking paintwork on the upper section of the wall in the living room.
- Bubbling paintwork and moisture staining on the wall in the corner of the loft.
- Staining and mould like substances on the bathroom wall above the shower. This appeared to be from roof leaks and not from condensation!
- Staining and mould like substances on the bathroom wall above the toilet.
There was evidence of moisture damage to most of the ceilings and cornices in the flat. There was some cornice cracks, cracking between cornices and walls, cracking between ceiling boards, deviations and moisture damage on the ceilings and cornices. The ceiling damage appeared to have been caused by leaks in the roof. Expect concealed water damage here based on the current visual condition.
Some examples are shown below:
- Cracking between ceiling boards in the living room ceiling from a roof leak.
- Staining and mould like substances on the living room wall at the cornice.
- Moisture intrusion between ceiling boards at the H-section joiner and a paint patch!
- Crack between ceiling boards and cornice in the loft was a sign of moisture intrusion.
- Moisture staining on the loft ceiling and the cracked cornice.
- Paint damage and moisture staining on the cornice in the loft. The opening section of the window appeared to be corroded or stained.
- Moisture damage and cornice cracks on the cornice and wall in the loft.
BICs (Built In Cupboards) and Cabinetry
The BIC's exterior appeared to be in a reasonable condition at the time of the inspection.
Interior Doors
Door Types: Hollow Core Doors
No doorstops on the interior and exterior doors of the unit were provided. The stops should be installed to prevent the exterior and interior doors from banging against the walls.
The interior door and frame were generally in a reasonable condition except where additional items are specifically listed.
Windows
Window Glazing: Single pane
Window Material: Steel
Window Styles: Casement
Window Finish: Painted
Window Decoration: Curtain rails
Internal Sills: Asbestos/Fibre Cement
Flaking paintwork, moisture damage and staining was noted at the sills in the unit's windows indicating that the windows were leaking. There is always a chance of hidden moisture intrusion and corrosion with this condition. Seal around the exterior of the frames at the sill, reveals and head of the windows with a suitable exterior silicone.
Examples are shown below:
Moisture staining and leaking was noted at and above the operable roof light in the loft. This may be from the roof windows being left open during rain. However, from the damage noted on the window and ceiling in the loft and living room area, the roof appeared to be leaking. Repair will be required to prevent further moisture damage to the finishes. Have the roof and roof light evaluated by an appropriately qualified roofing contractor for further remarks and recommendations.
Interior Stairs and Landings
Standard
The stairs, treads and risers leading up to the loft of the unit conformed to the Building Regulations and were functional. Exceptions are specifically listed below..
One of the timber steps was damaged on the leading edge. Care must be taken when descending the stairs for possible slipping.
- The edge of one of the steps was damaged.
Kitchen
Sinks, Vegetable Bowls, Wash Troughs, Taps and Mixers
Sinks, Vegetable Bowls and Wash Troughs: Single bowl sink, Tested
The sink was functional. The sink was filled and allowed to drain. The mixer tap, drain and trap were functional at the time of the inspection.
Cabinets and Counters
Cabinets: Checked
The kitchen cabinets and counters were in a reasonable condition with some wear and cosmetic damage that is commensurate with their age.
Appliances
Stove/Oven/Hobs: Electric
If an electrical appliance was being used before the start of load shedding, make sure that the electricity to the electrical appliance is turned off in case the electricity is restored during the time that nobody is in the vicinity of the electrical appliance. I suggest switching off all appliances, turning off all stove isolators and plug points feeding all appliances, and the stove and plug circuits in the main board! Switch some lights on so that a light fitting comes on when the electricity is restored.
The electric stove responded to normal user controls. Stoves are only tested for basic function. Ovens are tested in bake mode only.
Ventilation
Type: Operable window
General Condition
Except for the maintenance issue listed above, the kitchen was in a reasonable condition.
Bathroom
Basins
Basins: Tested
The basin was functional. The basin was filled and allowed to drain. The taps, trap, drainplug and draining were functional at the time of the inspection. Additional items are specifically listed below.
Cabinets and Counters
Cabinets: None (the basin was mounted on a pedestal)
Toilet and Bidet
Toilet: Tested
Toilet Seat: Checked
Cistern/Flushing System: Checked
The toilet was functional and responded properly when flushed. No leaks were observed at the toilet, wastepipe or water supply at the time of the inspection.
Bath and Shower
Shower: Tested
The showerhead, arm and mixer taps were in satisfactory condition. The shower was allowed to run and allowed to drain. No leaks were observed at the shower enclosure at the time of the inspection. Additional issues are specifically listed below.
Bathroom Ventilation
Type: Operable window
Bathroom ventilation is important to prevent moulds from forming. Moisture and condensation collect on the ceilings and walls from the lack of sufficient ventilation in bathrooms, creating an ideal situation for the formation of mould. I suggest that the window and door be left open to provide ventilation to disperse the steam and condensation resulting after showering or bathing.
General Bathroom Condition
Except for the deficient and maintenance issues listed above, the bathroom were in a reasonable condition.
Electrical
General
What a COC does not include
Appliances and fixtures such as lights, geysers, stoves, air-conditioning units, etc. are not covered by the CoC. A non-working appliance doesn’t mean that the CoC is invalid! The CoC and test report covers the whole installation from the point of control (main switch in the distribution board) to the point of consumption anywhere on the premises (ie. socket outlets and terminals of light fittings, geysers, stoves, etc.). It is also possible that an electrical installation might not be fully functional (for example, some lights or plugs don’t work), but the installation is safe and the therefore the CoC and test report is valid. This is the reason your report includes appliance and fixture defects.
Service Equipment
Main Panel Amperage: 60 amps
Electric Service Amperage: 60 amps
Main Electric Panel Location: kitchen
The main panel and its components in the apartment had no visible defects or deficiencies. Additional issues are specifically listed below..
There was an uncovered opening in the cover of the main electrical panel that exposes those who have access to the panel to shock hazards. This opening will need to be covered with approved panel block-out covers. Have a suitably qualified electrician check and repair the installation. This is a safety issue.
Branch Wiring
Wire Material: Not visible
Lights, Switches, Plug points and Fixtures
Inspection Method: All accessible points tested
Electric Plug Points: Three wire receptacles
The earth leakage circuit breaker at the electrical panel responded to its test button. An earth leakage circuit breaker (ELCB) socket tester was used to trip the earth leakage circuit breakers. The breakers tripped at 30 mA as required.
All tested interior and exterior light fixtures and switches were in working order except where additional items are reported.
Two ceiling lights in the living room and kitchen did not respond to switching. The globes should be replaced to check if the fittings are in working order.
- According to the tenant, this light stopped working during a rainstorm as a result of water leaking through the ceiling.
- Lights circuits are not always fed through earth leakage circuit breakers (ELCBs)! If there is a fault on a light fitting that requires replacement, the main switch, ELCB and the dedicated circuit breaker will need to be switched off to be on the safe side!
Plumbing
General
Plumbing Notes: Limit of inspection
I test every tap, fixture, the drain, waste and vent (DWV) system by running water through every fixture and waste and watching for blockages or slow drains. Fixture blockages become quickly evident and can usually be cured by clearing out the traps. However, if the drain line is blocked or damaged, there is a very strong chance that it will not become apparent during the course of my inspection.
Water Meter
Location of Main Water Shut Off
Main Water Supply Shut-off: Shut-off in duct
Water Service Supply
Pipe Material: Copper
Water Supply: Public water
Distribution Pipe
Supply Pipe Materials: Copper, Angle valve note
Functional Flow: Average
The water pipes, where visible, were copper and flexible braided connectors and appeared to be in a reasonable condition.
Angle stops are the shut offs located below plumbing fixtures such as sinks, basins and toilets. These are designed so that water can be shut off locally to a fixture without shutting off the water to the entire house so that localised fixtures can be serviced and repaired or replaced. Home inspectors do NOT test or adjust angle stops during inspection as there is a risk of leakage.
As water flow is a matter of personal desirability, and as temperature and flow fluctuations will often occur when other fixtures are operated simultaneously, I tested the flow at the basin while operating other fixtures in order to determine whether or not it meets with requirements. The water flow at the cold and hot water side of the fixtures was generally good.
Waste Pipe and Discharge
Discharge Type: Public sewer
Waste and Vent Pipe Materials: PVC
Where visible, the drain and vent pipes inside the duct and inside the unit appeared to be functional at the time of the inspection. No leaks were observe.
There was a hole in the waste pipe from the kitchen sink that should be repaired.
- A hole on this wastepipe! The hole should be sealed!
Water Heaters/Geysers
System Type: not found
Size: Could not ascertain size
Energy Source: Electricity
Inspection Observations
Check Out List
Stove: off
Lights: Off
Property Comments
Usually your body corporate is responsible for all the safety and defective problems on the external side of the unit and for the repairs to them. This also applies to damages inside the unit and property caused by external factors such as leaking roofs and geysers etc.. Body Corporates are inclined to drag their feet or site lack of funds when it comes to their responsibilities. All body corporates are required to have insurance against most of the defects which appear under "Structure". I would suggest you contact your managing agent who is obliged to provide you with a copy of the complex insurance policy. Also make sure you receive a copy of the body corporate rules. Check the body corporate financial statements and inquire as to their 10 year maintenance program before you buy into the complex.